Many refineries rely on outdated maintenance practices that expose workers to unnecessary risks. Scheduled maintenance, where equipment is serviced at regular intervals regardless of condition, often leads to wasted resources and unnecessary downtime. Conversely, running equipment to failure invites breakdowns and costly repairs.
The Imperative for Digital Transformation
Fortunately, advancements in digital technology offer a superior solution: real-time condition monitoring for process valves. By embracing digital transformation, refineries can:
- Minimize Downtime: Proactive maintenance, guided by real-time data, allows for early detection and correction of potential valve issues, preventing costly shutdowns.
- Enhance Worker Safety: when valves are monitored remotely, fewer physical maintenance rounds are required. This reduces worker exposure to hazardous environments.
- Make Data-Driven Decisions: Real-time data on valve health empowers operators to make informed decisions about maintenance, process optimization, and resource allocation.
Why the Hesitation?
Despite the clear benefits, some refineries hesitate to adopt digital transformation. Misconceptions about complexity can lead to a reluctance to embrace new technologies. However, digital transformation doesn’t have to be intimidating. All it requires are simple, practical steps to gain process visibility and a clearer understanding of operations.
From Manual to Digital: A Paradigm Shift
Traditional methods involve manual data collection on valve cycles and positions, a risky process exposing workers to hazardous environments. Digital transformation replaces this with real-time data accessible from a device or control room. Adding a sensor to a valve creates a digital record of its health. This data is then translated into actionable insights that enable automation and optimization, ultimately leading to improved reliability, cost savings, and safety.
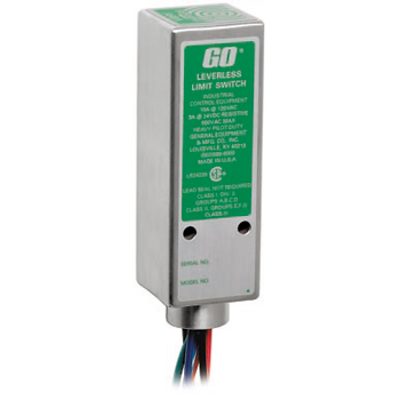
The magnetically driven TopWorxTM GOTM Switch from Emerson provides reliable proximity sensing in demanding and extreme conditions.
The See-Decide-Act Cycle – A Continuous Improvement Loop
Digital transformation sets in motion a continuous cycle of improvement:
- See: Sensors collect vital data about valves, including cycles, temperature, and position.
- Decide: Control devices, like distributed control systems (DCS) or safety instrumented systems (SIS), analyze the data and present it in user-friendly dashboards.
- Act: Personnel receive alerts and take appropriate actions, such as repair or replacement of valves.

Integrated Solutions: Simplifying Valve Management
Integrated switchboxes combine sensing, communication, and control functionalities in a single unit, simplifying valve management. Real-time performance monitoring provides constant valve visibility, and the system can send proactive maintenance alerts. Predictive analytics, enabled by this data, optimize device replacement, minimizing downtime and associated costs. If we consider the staggering cost of a single valve shutdown at $1.3 million per day, with an average of 27 unplanned shutdowns annually, these costs can quickly become exorbitant. Monitoring data-driven condition can significantly reduce the financial impact of downtime, with estimates suggesting a 60% decrease.
Enhanced Worker Safety Through Remote Monitoring
Proactive maintenance and preset safety alerts significantly reduce the frequency of maintenance rounds. Remote monitoring of valve health eliminates the need for workers to be physically present near the asset, minimizing exposure to hazardous environments. Fewer trips for maintenance and troubleshooting decrease the risk of injuries. Additionally, improved valve health insights empower personnel to make safer operational decisions.
Future-Proofing Technology: Investing in Compatibility
Standards like HART 7 ensure compatibility and accessibility of data across systems. Integrated switchboxes equipped with a HART 7 module can capture “stranded data” from legacy systems, further enhancing uptime and safety. Stranded data refers to valuable information that’s inaccessible due to compatibility issues or outdated control systems.
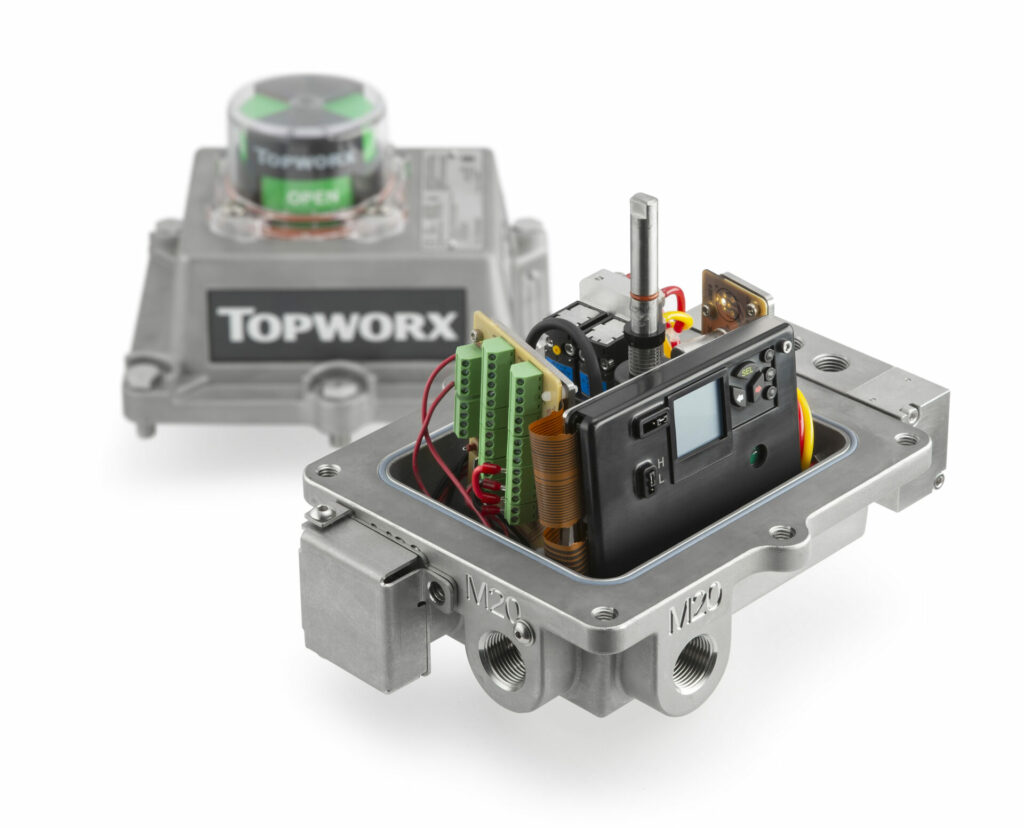
Emerson’s TopWorxTM DXP discrete valve controller contains sensing and feedback in a single housing. Suitable for use in SIL-3 applications, it’s certified for use in hazardous areas. It tracks a wider variety of variables and is easier to set up and integrate into processes than other HART 7 technologies.
Navigating the Transformation Journey
Refineries don’t have to go through the digital transformation process alone. Partnering with an expert partner who understands both the technologies and the unique needs of the hydrocarbon industry can significantly smooth the way. The ideal partner offers a comprehensive package of solutions from valves, to control systems, software, and services – tailored to each facility’s specific requirements.
By embracing digital transformation, it is possible to leverage existing data to automate and optimize processes, gaining a deeper understanding of valves – the true heart of productivity – and make data-driven decisions that maximize uptime and ensure smooth and efficient operations.