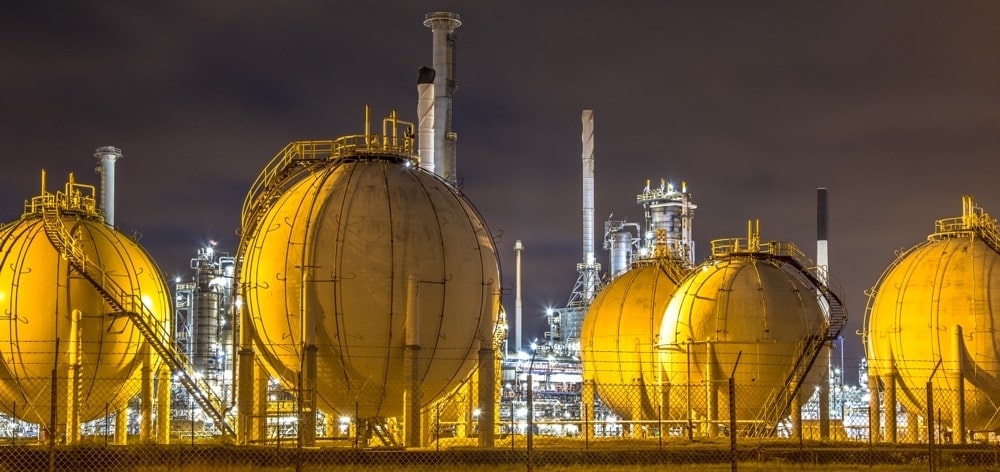
Gas processing is a sophisticated industrial method for refining raw natural gas from wells. This involves precise fluid handling, measurement, control, and dispensing to remove impurities such as methane, ethane, propane, and butane. The purified gases are then used for heating, electricity, industry, and transportation, making gas processing essential in the energy supply chain.