Fluid mixing is the movement of fluids to enhance a process result, which is accomplished through an agitation source.
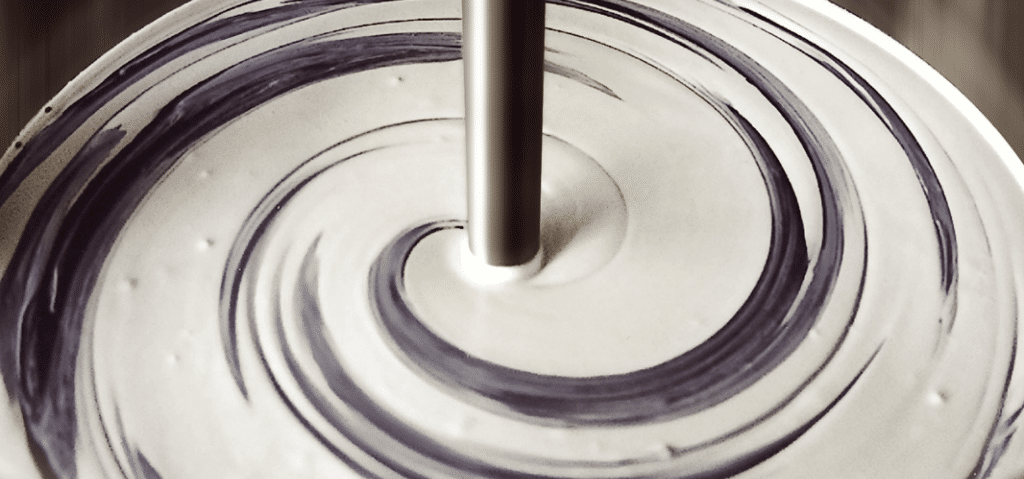
Fluid mixing is the movement of fluids to enhance a process result, which is accomplished through an agitation source.
The process of fluid mixing is concerned with all combinations of phases, which frequently include:
For more information about solid-solid mixing, liquid-solid mixing, and gas-solid mixing, click here.
Liquid-liquid mixing is essential in many industries, generally accomplished in mechanical agitation systems.
Liquid-liquid mixing in a mechanically stirred vessel is a standard industrial operation encountered in many foods, pharmaceutical, petrochemical, and chemical industries.
The particular purpose of these industrial processes is to promote good contact between the two immiscible phases and extend the interfacial area to increase the mass transfer rate.
Different parameters, such as: can evaluate Liquid-liquid mixing performance in a stirred tank
Input parameters include:
Gas-gas mixing or gas blending is the mixing of gases for a purpose where the final gas mixture is specified. A gas mixture is defined in a molar gas fraction by percentage, parts per thousand, or parts per million.
In gas mixing, many variables and factors play a role. Proper mixing and blending of gases saves money, increases repeatability of the end product, and improves quality. The applications are scientific, industrial, food production, food storage, and breathing gases.
Various methods are available for gas blending, and these may be distinguished as batch methods and continuous processes. Gas mixtures must be analyzed either in process or after blending for quality control.
Liquid-gas mixing is an essential and standard unit operation in chemical and allied industries. Many of the most important chemical reactions in the industry involve mixing liquids and gases, and Chlorination, hydrogenation, and organic oxidation are just a few examples. Liquids and gases are usually combined to allow mass transfer to occur.
The main difficulty in most gas-liquid mixing is maximizing the contact between the two phases and making sure that as many molecules as possible of the gas come into contact with molecules of the liquid. This means making the gas bubbles as tiny as possible and ensuring that the bubbles are distributed evenly throughout the liquid. However, in practice, this is a highly complex matter.
Many industrial processes rely on effective and efficient agitation fluid mixing technology.
The application of fluid mixing technology covers the areas of mining, hydrometallurgy, biology, petroleum, food, pulp and paper, pharmaceutical and chemical process industry.
In particular, in these industries, we find typical chemical reaction engineering processes like fermentation, wastewater treatment, hydrogenation, polymerization, crystallization, flue gas desulfurization, and more.
Agitation
Generally, agitation forces the fluid to flow in a vessel by mechanical means.
Mixing
Mixing usually implies taking two or more separate phases or two fluids and causing them to be randomly distributed through one another.
There are several purposes for agitating fluids, for example:
Fluid mixing may also be necessary for reactors to ensure optimal operation conditions for some chemical systems requiring uniform temperature and species concentrations within the reactor volume.
Therefore, fluid mixing and blending devices are essential units for reactive and non-reactive processes.
Industrial fluid-fluid reactors may broadly be divided into gas-liquid and liquid-liquid reactors.
Gas-liquid reactors typically may be used to manufacture pure products (such as sulfuric acid, nitric acid, nitrates, phosphates, adipic acid, and other chemicals) where all the gas and liquid react.
Types of reactors
The types of reactors used for fluid-fluid, for example, gas-liquid and liquid-liquid reactions, may be divided into two main types:
Tower or Column Reactors
Tower or column reactors, without mechanical agitation, are used primarily for gas-liquid reactions. If used for a liquid-liquid response, the arrangement involves vertically stacked compartments, each mechanically agitated. In either case, the flow is counter-current, with the less dense fluid entering at the bottom and the more viscous liquid at the top.
In the case of a gas-liquid reaction without mechanical agitation, both inter-phase contact and separation occur under the influence of gravity. In a liquid-liquid response, mechanical agitation dramatically enhances the communication of the 2 phases. The emphasis here is only gas-liquid reactions.
Tank Reactors
Tank reactors generally employ mechanical agitation to bring about more intimate contact of the phases, with one stage being dispersed in the other as the continuous phase. The gas-phase may be introduced through a sparger located at the bottom of the tank; this is a circular ring of closed-end pipe provided with several holes along its length allowing multiply entry points for the gas.
Compared with non-agitated reactors equipped only with spargers, mechanically agitated tank reactors have the advantage of providing a greater interfacial area for more efficient mass transfer.
Tank reactors are well suited for a reaction requiring a considerable liquid hold-up or a long liquid-phase residence time.
The operation may be continuous concerning both phases or semi-continuous, i.e., batch concerning the liquid. The most straightforward flow pattern for each stage is back-mix flow.
Tank reactors equipped with agitators (stirrers, impellers, turbines) are used widely for gas-liquid reactions in the traditional chemical process industries and biotechnology.
They are also used for 3-phase gas-liquid-solid reactions, in which the solid phase may be catalyst particles; in this case, they are usually referred to as “slurry” reactors.
Get the extensive coverage for fluid handling professionals who buy, maintain, manage or operate equipment, delivered to your inbox (it’s free!).
By signing up for our list, you agree to our Terms & Conditions.
Get the extensive coverage for fluid handling professionals who buy, maintain, manage or operate equipment, delivered to your inbox.
By signing up for our list, you agree to our Terms & Conditions. We deliver two e-Newsletters every week, the Weekly E-Update (delivered every Tuesday) with general updates from the industry, and one Market Focus / Technology Focus e-newsletter (delivered every Thursday) that is focused on a particular market or technology.
Panametrics, a Baker Hughes business, develops solutions for measuring and analyzing moisture, oxygen, liquid, steam, and gas flow with proven technologies. More info ➜
Bronkhorst High-Tech B.V. is a leading manufacturer of Mass Flow and Pressure Meters / Controllers for gases and liquids. More info ➜
A
website
© Fluid Handling Pro 2025
Be the first to know about the latest process technology innovations, tailored to your specific interests.
Join 29000+ readers that receive our “web exclusive” articles, white papers, new products, and other information.