When Tapflo’s founder, Börje Johansson, began developing diaphragm pumps, his vision was to create products defined by quality, reliability, and simplicity. To this day, Tapflo takes pride in the fact that its diaphragm pumps contain up to 70% fewer components than competitors’ models, a simplification that enhances their efficiency and performance in specialized applications. Key benefits of Tapflo diaphragm pumps include the absence of rotary seals, self-priming capability, ability to operate dry or under “dead head” conditions, and excellent handling of solids. A crucial part of these pumps is the diaphragm itself, which, due to its composite construction, is engineered for long service life and high-performance durability.
Each model offers virtually unlimited connection configurations and can be constructed from various materials to meet the specific requirements of each application. Tapflo’s product range includes plastic, metal, sanitary, powder, pharmaceutical, low-energy, and aseptic EHEDG pumps, available in both air-powered and electric versions. The company also offers a wide selection of valve ball materials and types designed for different applications, as well as energy-efficient air valves produced in its Polish facility. These valves, which require no lubrication, are available in materials such as brass, stainless steel (AISI 316L), or PET. Tapflo’s engineers continually face new challenges and create innovative solutions. Here are a few examples.
Need a Special Pump? Challenge Accepted!
Each year, Tapflo’s engineers develop around a thousand new pump configurations, including custom-designed diaphragm pumps. Among these projects was a request from a company in the automotive components sector, which needed a pump that could withstand extreme conditions, including abrasive liquids, particle-laden environments, and continuous 24/7 operation. Additionally, the pump had to be easy to service, particularly in terms of seats and valve balls—a challenge in standard metal pumps where valve seats are often irreplaceable. This need led to the development of the TF225 SEE-5FP6A7MN8E model.
This innovative pump is an industrial, 2” glass-blasted filter press pump, designed to handle a discharge pressure of up to 12 bar. Equipped with DIN flanges, heavy-duty PE1000 valve seats, a valve ball guiding system, EPDM gaskets, a reinforced stand, and high-pressure clamps, the pump is optimized for high durability. Featuring a pressure booster and Eco-boost system, it is engineered for optimal performance and extended operational life.
Rigorous Testing for Reliability
The TF225 pump is used to circulate liquid through a filter press and back into the system in 24/7 operations. For reliability at elevated pressures, all fittings were modified to handle 12 bar, and the pump underwent extensive in-house testing, including an 18-bar hydrostatic test and a long-term, 12-bar endurance test. A sanitary model was chosen over an industrial version to accommodate ball cup valves, making the valve seat easily replaceable. Thanks to the valve ball guiding system, this pump effectively handles large particles and minimizes wear on valve balls and seats, which are replaceable without requiring complete disassembly—a valuable feature when dealing with abrasive liquids.
Sludge with Limescale? Tapflo Has the Solution
Another project involved a TE100 PEP/154D model, an electrically driven diaphragm pump with an EPDM diaphragm, PE1000 valve balls, and a built-on frequency inverter. This pump was installed in a wastewater treatment plant to pump sludge with limescale—a challenging substance with a pH of 6 to 9, high FeCl3 content, and high abrasiveness. Particle sizes vary from 1 to 5 mm, and the pump operates at 50 Hz, delivering a flow rate of 90 l/min at 1-1.5 bar on a 24/7 schedule.
Tapflo places great importance on customer feedback, advising on proper usage and evaluating pump performance onsite. After six months of operation, an initial maintenance inspection found all parts in perfect condition. Tapflo pumps, of which the client now has two, replaced hose and progressive cavity pumps that required frequent component replacement. Previously, hose pumps experienced ruptures every 3-6 months, and progressive cavity pumps required stator replacements every 2-3 months. Since maintenance is conducted only once per year at this facility, the longevity of Tapflo’s pumps presents a significant advantage to the customer.
Handling Aggressive Vapors
Certain applications involve chemicals that make metal components unsuitable due to their susceptibility to corrosive vapors. In response, Tapflo developed the T100 PTT-5CP5NM7PV9T11SP14RF, a pump designed without external metal components. Featuring a plastic nameplate and air intake adapter, a fully plastic stroke sensor, PET/FKM air valve, titanium-coated fasteners, and reinforced plastic plates, this pump is built for extreme conditions, where standard steel parts would degrade. This model is ideal for handling hot sodium hydroxide and similar chemicals; the fasteners can also be coated with PTFE or Xylan® if needed.
Endless Customization Options
While it’s impossible to cover all of Tapflo’s unique projects in a single article, many examples can be found on their website. Tapflo also has a specialized division, Tapflo Solutions, dedicated to developing custom projects. For those needing mobile solutions or specific setups like drum unloading, the HVS Quattro model with a Tapflo diaphragm pump is a must-see. In addition to diaphragm pumps, the Swedish company manufactures hose and centrifugal pumps, and offers complete pump systems with control panels, handles, trolleys, and dosing systems.
Tapflo’s commitment to quality and innovation has made it a trusted name in pumping solutions for industrial challenges worldwide.
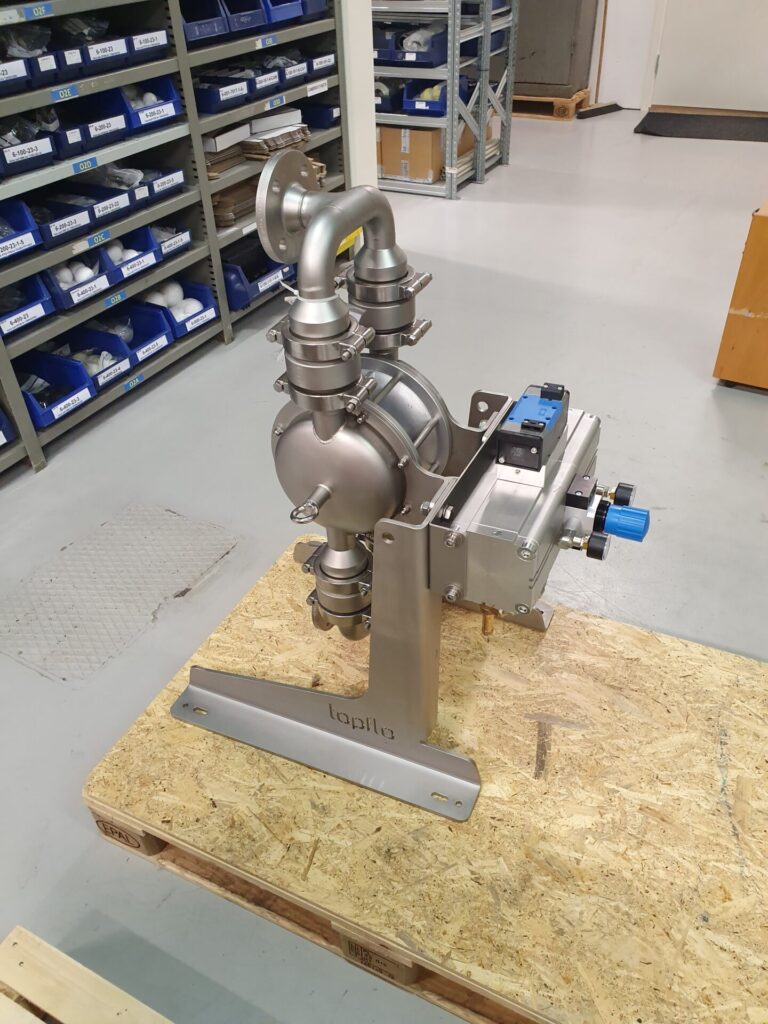
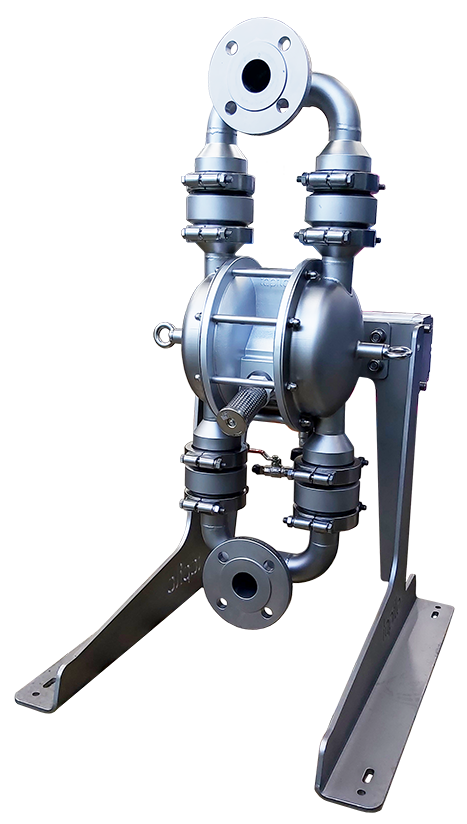