What are the key things to consider when choosing a flowmeter?
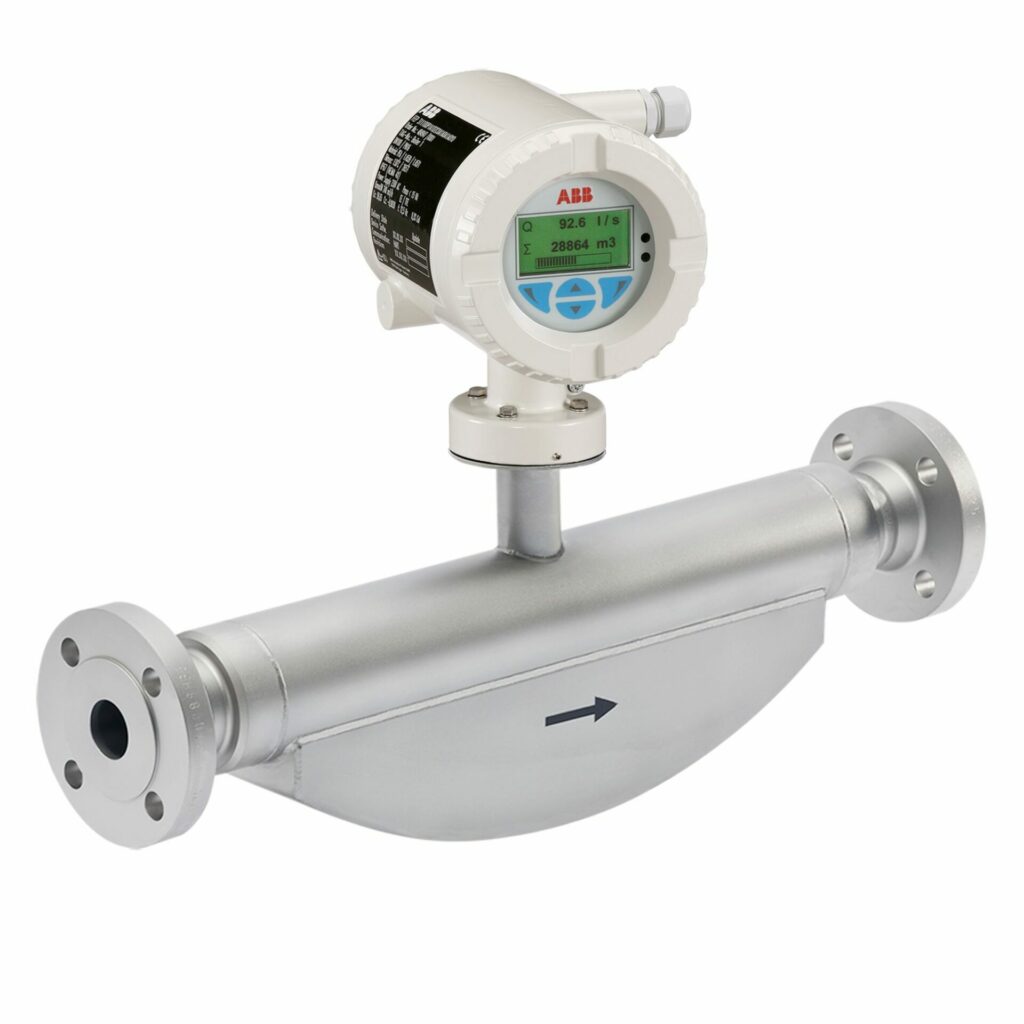
The key things to consider are what is the fluid type and does the flow vary widely. Be mindful of whether the flow is turbulent or prone to “pulses” and what accuracy is required of the meter. It is also a good idea to check what technical support and advice is available for selection, installation and maintenance.
Do not be tempted to choose on cost alone. When it comes to selecting a flowmeter, in many cases cheapest is by no means best. Ultimately, the most cost-effective installation will be the one where the supplier can offer good technical back-up, independently traceable test facilities and a long and established track record for reliable products based on sound research and development.
Why does it matter what fluid flow I am measuring?
Every liquid or gas behaves differently when flowing through the pipeline. By profiling the flow of a liquid or gas through the pipeline, it is possible to narrow down the choice of flowmeters to those best able to cope with the conditions of the application.
The flow profile of a fluid will vary according to whether it is Newtonian or non-Newtonian. Newtonian fluids have a tendency to ‘stick’ to the pipe walls, resulting in the liquid moving more slowly at the sides of the pipe than in the middle. They have a directly proportional relationship between the pressure of the liquid flowing through and the resistance, or shear force, caused by the fluid sticking to the pipe walls.
The behaviour of Non-Newtonian fluids is harder to predict, as there is no relationship between pressure and resistance. Instead, the flow of these fluids tends to vary as viscosity changes either with time or due to a change in resistance caused by the collision of two different velocities as the fluid sticks to the pipe walls.
To select the best flowmeter, it may be necessary to calculate the Reynolds number of the application. This figure is basically the ratio of momentum against viscosity and can be calculated by using the minimum and maximum fluid flow and viscosity figures of the application. Once the Reynolds values are known, they can then be matched against a flowmeter’s Reynolds range to help pick the one that is best able to meet the demands of the application.
Why is turndown important?
Turndown is the ratio of the maximum and minimum flow rates a flowmeter can measure within its specified accuracy range. The turndown of a flowmeter is particularly important because it is virtually impossible to know in advance the exact range of flows to be measured. Selecting a flowmeter that offers the widest possible turndown will ensure that it can cover all anticipated flow variations.
What’s the best place to install a flowmeter?
Obstructions in the pipeline such as joints, bends, or valves near the meter can all cause distortions in flow profile, affecting flowmeter accuracy and repeatability. To ensure best results, flowmeters should be installed in locations where there are several straight lengths of unobstructed pipeline both upstream and downstream of the meter.
It is therefore important to find out the manufacturer’s installation recommendations before buying a flowmeter, particularly where installation space is limited. Some flowmetering techniques require minimal or even no conditioning pipework. Use of such techniques, for example VA and Coriolis meters, can assist with accurate metering in awkward or cramped physical installations.
How can I achieve the best measurement accuracy?
Find out which types of flowmeter are most suited to the application. Electromagnetic meters provide for the widest flow range for conductive fluids; turbine meters may provide an inexpensive capital cost option for small sizes, but suffer with the problems of mechanical wear over time and possible process contamination with worn parts (e.g. bearing swarf); while DP meters including orifice plates, venturis and wedge meters are the most commonly used metering devices, and now come in compact integrated solutions. Despite their high initial cost, Coriolis mass flowmeters are ideal for measuring particularly viscous substances and their use has been steadily increasing in many applications, no longer just where the measurement of mass rather than volume is required.
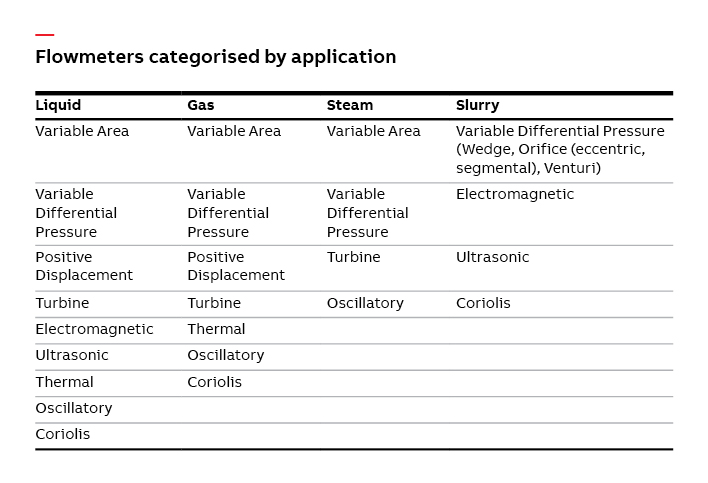
Where accuracy is concerned, it is important to remember that most flowmeters are affected to some extent by the medium they are metering and by the way they are installed. Consequently, flowmeter performance in real life conditions will often be different from the reference conditions under which the flowmeter was calibrated.
Beware also of manufacturers’ calibration accuracy claims. Even under stable reference conditions, the best accuracy that manufacturers can hope to achieve is 0.1%.
How do I keep my flowmeter in good working order?
For optimum measurement performance, it is advisable to periodically check your flowmeter’s accuracy throughout its service life. The most modern electro-magnetic flowmeters employ self checking diagnostics aimed at predicting possible meter or process failure in advance.
Where can I find out more information?
ABB has a wealth of information to help you choose the best flowmeter for your process. To find the best solution for your application, visit www.abb.com/flow.