The Stendal pulp work is a key project by the Canadian Mercer Group and is considered one of the largest and most modern pulp works in Europe. Established in 2004 as a Greenfield project, the location has continued to develop and is home to the largest biomass power plant in Europe. Due to to several extensive expansion projects, the plant today has a production capacity of 740,000 tons of NBSK pulp (Northern European long-fiber pulp) as well as a modern extraction system for biochemicals such as turpentine and resin oil.
In addition to pulp production, the work pursues ambitious goals for decarbonizing and promoting sustainability. In the sense of a sustainable circular economy, Mercer uses the trees that are needed for pulp production, as complete as possible and can thus reduce the CO2 footprint of production at the same time. All organic residues, including bark and the biomass contained in the pulp, are used as fuel in the power plant. Like all of Mercer, the Stendal plant produces enough green energy to cover its internal needs and at the same time feed energy into the public power grid.
Independent energy and steam generation
Steam plays a central role in the production processes in the plant. From wood shredding through to the heating process, cellulose drying and energy generation in the biomass power plant – it is the primary energy source in almost all the processes. Steam is generated in an onsite biomass power plant, which has two boilers: a large boiler for the burning of lignin solution and a smaller boiler for the burning of residue after processing. These boilers produce 164 kilograms of steam per second at 85 bar and 485 ° C, which enabled an impressive energy production of over 1 terawatt hour last year.
For the optimum utilisation of this steam, as little as possible should be allowed to escape into the atmosphere. These steam losses are synonymous with energy wastage. Steam traps play a key role here. They drain the condensate from the steam lines, which would otherwise have a negative impact on the efficiency of the system. “In the entire plant there are over 300 steam traps installed at various points. For example on the main steam lines as trace heating or on heat exchangers in the production process and on other pieces of equipment. In the past, however, we have repeatedly had problems with the traditional mechanical steam traps, ”says Frank Wegener, Energy Manager from Mercer in Stendal.
Challenges with mechanical steam traps
The Stendal plant was originally equipped with a variety of different steam traps, including thermodynamic traps, float traps and bimetallic traps. According to Wegener, this variety of different types not only led to a considerable effort to manage spare parts parts but also made it difficult to supervise maintenance. “In the event of failure, the type of defective trap had to be determined, the appropriate spare parts were sought and often laboriously reordered. This resulted in longer downtime and high repair costs, ”says Wegener.
In search of a more efficient and more robust solution, the plant finally came across venturi orifice steam traps. “In critical places where the mechanical steam traps regularly failed, we tried this technology. The results were impressive: with the new venturi orifice steam traps there are no more problematic vibrations that otherwise led to regularly damage, ”reports Wegener.
In view of these results, the plant decided to replace a total of 80 old mechanical steam traps for ECOFLOW™ venturi orifice steam traps from the Essen based company EBE Engineering. The installation was cassied out during a regular shutdown in which extensive maintenance work was carried out. According to Wegener, the advantage of this technology was evident immediately after startup: “In the past on startup, we expected many failures with the mechanical steam traps – but this was not the case with the venturi orifice steam traps we had no problem with the starting loads. ” Since the installation of the EBE Engineering traps, no failures have occurred in the affected areas, and the problematic water hammer problems in the registers have become a thing of the past.
Easy maintenance and better energy efficiency
A central advantage of the ECOFLOW™ venturi orifice steam traps from EBE Engineering is its modular design. This allows the trap to cover a variety of capacities- from minimal condensate flow in trace heating and line drainage applications up to high flow condensate rates and variable loads in process heating applications. This also makes maintenance easier, for example in the event of blockages caused by particles in the steam system. This can lead to an efficiency loss in the system, since the steam is not properly condensed and drained. In order to avoid this problem, the ECOFLOW™ venturi orifice steam trap is equipped with a filter. “The cleaning of the filters in our regular maintenance plan takes only a few minutes and is done in just a few simple steps,” reports Wegener.
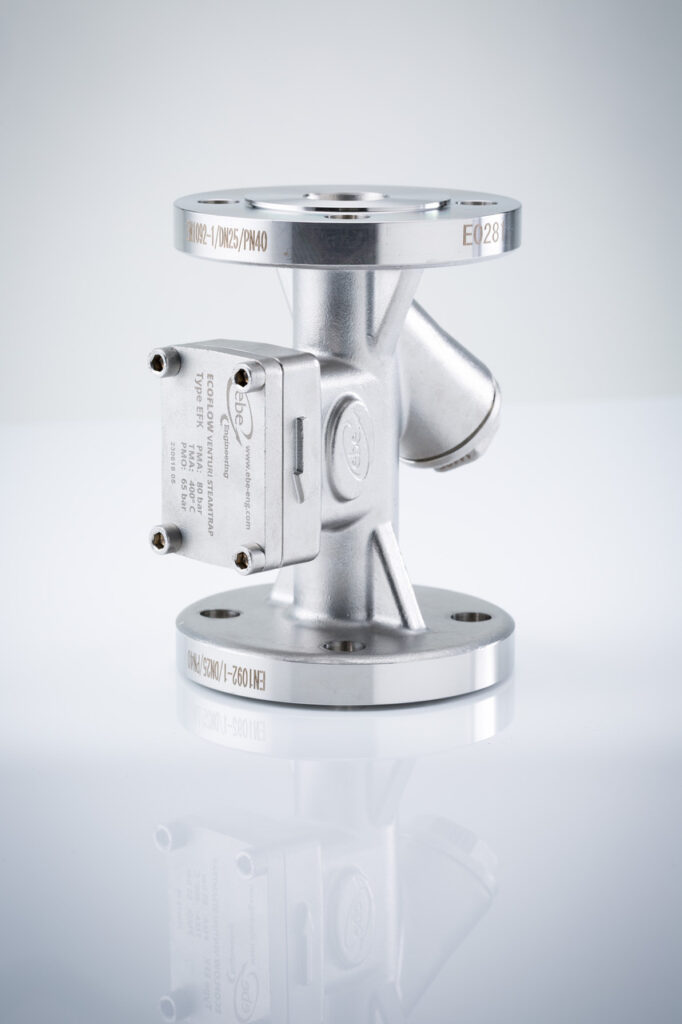
However, energy efficiency is the most important aspect for Frank Wegener. And this is where the ECOFLOW™ venturi orifice steam trap from EBE Engineering excels. “Before switching to the new technology, because of failed mechanical steam traps, large amounts of steam were lost unused in the atmosphere. With the new traps, these losses could be eliminated almost completely, ”says Wegener.
The physical operating principle of the venturi orifice steam trap removes condensate from the steam system without live steam being able to escape. This means that the steam is used more effectively in the entire system and energy losses are thus reduced. The steam losses in Stendal could be reduced by up to 30 percent thanks to the new traps. “The savings are so large that the return on investment with the new steam traps was less than one year,” summarizes Wegener.
The spare parts stock was also drastically simplified by the introduction of the new trap. While a variety of different spare parts in the past had to be kept for the different types of mechanical steam traps, the plant now only requires a few standard components that can be stored in a small box.
Significant cost savings
Overall, the plant was not only able to reduce energy consumption by introducing the ECOFLOW™ venturi orifice steam traps but also significantly reduce the maintenance costs and downtimes. “Until now, we had to budget every year with costs in the six -figure area because of failed mechanical traps. This cost has been removed with the ECOFLOW™ venturi orifice steam trap, ”says Wegener.
According to Wegener, the cooperation with EBE Engineering went smoothly and the entire company is now convinced of the advantages of the new technology. “At the next major shutdown, we want to replace almost all remaining old mechanical steam traps. Reducing steam losses and improved energy use are a crucial step towards sustainability. With the innovative solutions of EBE Engineering, the Stendal plant is well equipped for the future and sets new standards in pulp production and energy generation.