Dynamic reactors are those with moving elements. The improved mixing provided by moving parts in the reactor can be advantageous for highly reactive processes, mixing limited processes and heat transfer limited processes.

The benefits of mixing are useful for both batch vessels where stirrers and agitators are used, and for flow chemistry reactors with a whole spectrum of mixing elements. In general, mixing reduces reaction times, which in flow leads to smaller footprint reactors. Moreover, a high degree of mixing results in efficient processes.
The rate of chemical processes depends on two main factors that influence the rate of chemical reactions, mass transfer and kinetics. A reactor may have sufficient mixing, but if its contents are not chemically reactive, no reaction will occur (this is often called rate-limited or kinetically limited). Similarly, a chemical reaction may be innately fast, but if the reagents fail to meet, the reaction cannot proceed (mass transport limited).
These two factors governing chemical productivity each pose limits on process efficiency. While chemical rates are inherent properties to a reaction based on the molecules alone, mass transfer is something that can be controlled with selecting the right technology. Indeed, reactive chemical conversions can benefit substantially from the right choice of technology, for productivity but also selectivity and safety.
Why heat transfer is an important consideration
Generally, reactions that are fast release a substantial amount of heat. Heat release in a chemical plant is an important consideration, as increases in temperature can negatively impact the process. Excessive generation of heat can lead to severe safety risks, which needs to be addressed. The difficulty of addressing heat scales to the thrid power with volume, as do problems caused by thermal runaway scenarios. In batch reactors, the volume restriction may force choices for parallel reactors in scaleup. Performing the process in flow can be an alternative.
In flow reactors, the active reaction volume is relatively smaller compared to batch reactors. A smaller reactor is easier to cool, but also concentrates the generated heat. As such, the increased chemical reactivity in flow needs to be accompanied by a comparable increase in heat transfer capacity. An added benefit of flow for highly reactive species is safety aspect of a smaller volume.
How SpinPro reactors tackle heat & mass transfer
Mass transfer
The intense turbulence and high sheer produced by the rotating parts in the reactor ensures a high degree of mixing. The fast rotating rotors are close (within millimetres) to the stators. This proximity provides high shear and high (>1.000.000) Reynolds numbers. As such, the resulting mixing capabilities are high: most mass transfer-limited reactions can in this fashion be completed almost instantaneously, limited only by the extraction rate of generated heat. For example, some processes that can take hours in batch (due to dosing limitations, to prevent thermal runaway) can be reduced to seconds.
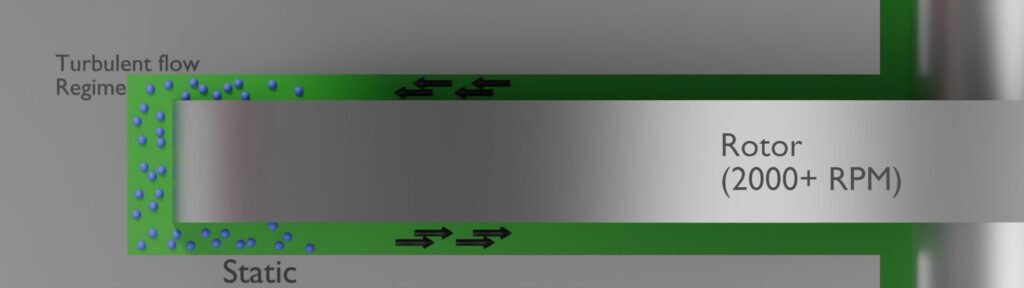
Heat transfer
The intensified productivity enabled by the high mass transfer rates also leads to an increased release rate of reaction heat. Therefore, any process intensified reactor needs to have a highly effective cooling strategy. In SpinPro this is achieved first of all by the aforementioned highly intense turbulence, so that reaction heat in the process side between the rotor and the stator is rapidly transported to the thin wall separating the process liquid from the utility or thermal control fluid. Secondly, the thickness and thermal conductivity of this stator wall is chosen so that this heat is subsequently conducted very quickly into the heat transfer liquid. And third, the specific design of the utility zones of the SpinPro enables the rapid refreshment of utility liquid to carry away the heat of the reaction.
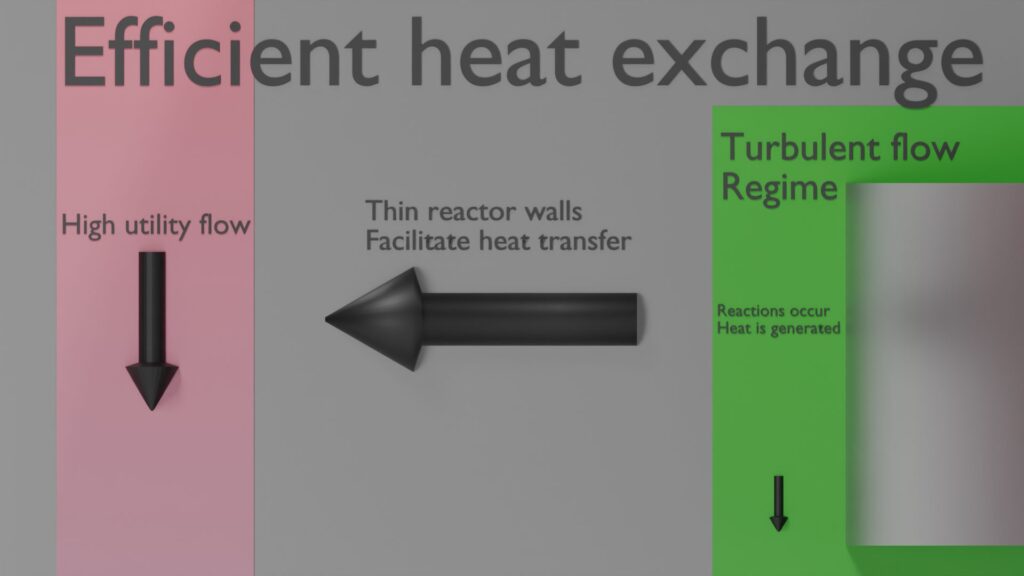
Major applications
Highly exothermic reactions
Generating heat can be a complex factor in the design of technology for a chemical process. Excessive heat can increase the temperature when not controlled, which reduces selectivity at best and can become a major safety hazard at worst. High heat transfer capabilities minimize these risks. As a result of effective heat extraction, these type of conversions can be carried out in a highly controlled manner, often at a higher temperature without losses in selectivity. The reason for reactions remaining selective is the lack of hotspots that would otherwise be generated due to locally increasing temperatures. Hotspots are not an issue in this dynamic reactor, because the distance to a cooling surface is always less than a few millimetres. Some specific examples of relevant reactions in this category are nitrations, organometallics, diazotizations, chlorinations, polymerisations and sulfonations.
Multiphase systems
Processes that involve more than one phase (gas, aqueous, organic) are inherently more difficult to design than a single phase one. Generally, the two phases in the process are to interact with one another, which happens on the interface (surface) rather than within the entire volume. Interfacial areas tend to minimize themselves without external forces, which reduces reactivity between the two volumes. More surface area thus needs to be actively generated for increased reactivity. As such, multiphase reactivity is inherently a mass transport limited system. Generation of more surface is done efficiently within a SpinPro reactor. The high velocity difference obtained between the rotor and the stator generates a large amount of shear which effectively rips apart larger bubbles and droplets into many smaller ones. Moreover, with Reynolds numbers of over 1.000.000, many small eddies are formed, which further accelerate the mass transfer between the two phases. Examples of reactive gasses used: Cl2, CO, CO2, H2, H2S, HCl, O2, SO2, freon, acetylene and many more.
Conclusion
The use of dynamic reactors can be beneficial for many processes. Major advantages lie in the applications for mass transfer limited processes, heat transfer limited processes and highly reactive processes. Flow reactors can be of particular benefit, due to the intrinsic smaller volumes which are safer and easier to cool. The flow reactor used as example here, the SpinPro, utilizes fast rotation, small volumes and high utility flow rates to optimize for mixing limited processes.
Authors
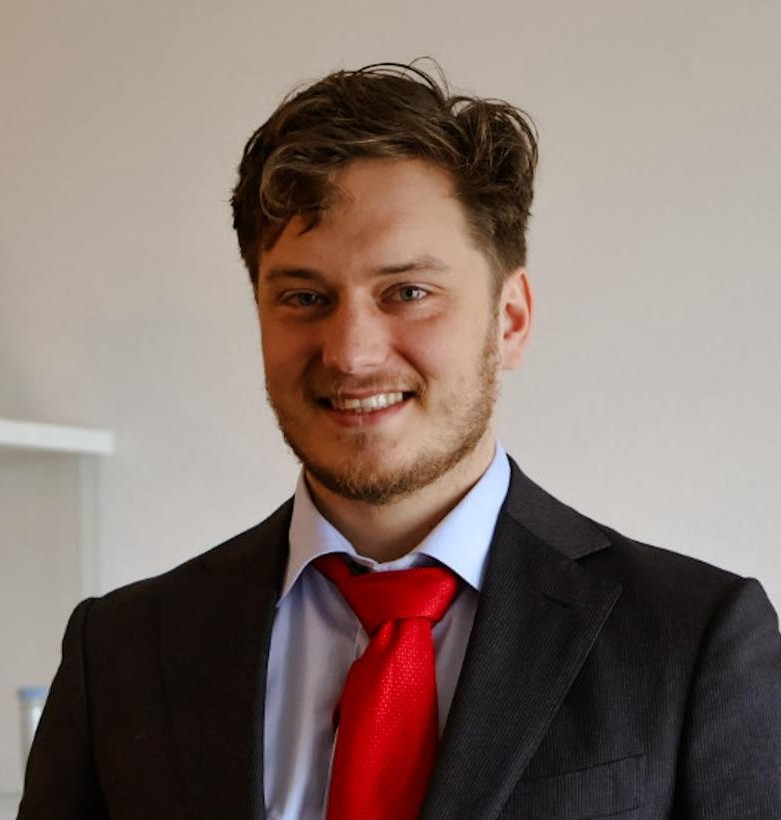
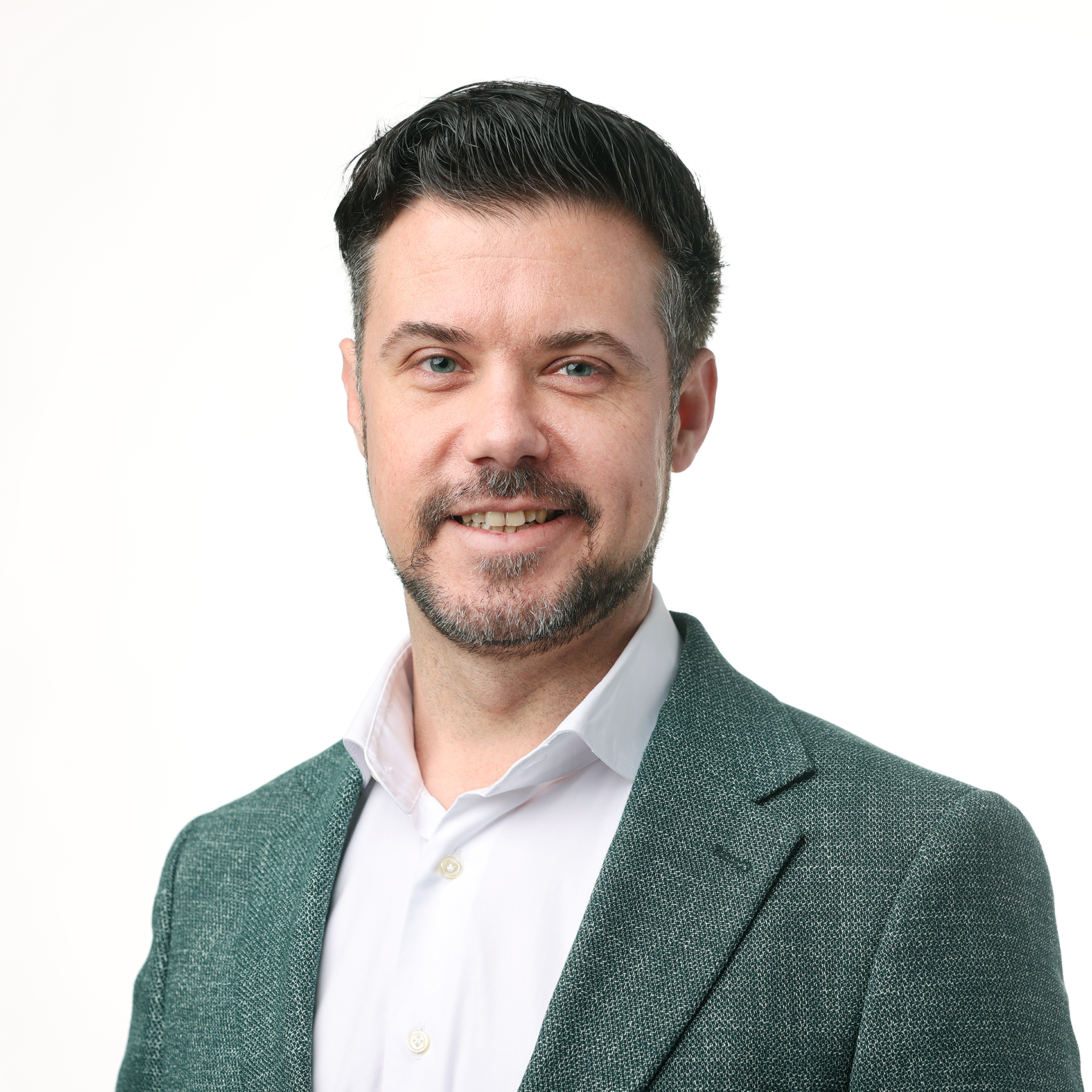