It would be fair to assume plants now have flow control down to a fine art. After all, the LNG industry is well over 50 years old and has grown exponentially in the last two decades. This has emphasised the need for best practice when processing feed gas for liquefaction. But despite clear areas of progress, this has yet to emerge and many organisations still rely on older valve designs that introduce their own set of challenges.
This wouldn’t be a problem were it not for the wide range of different conditions found as gas enters transmission networks. Feed gas is often supplied from several sources, held by owners that use their own pressures and flow rates. This puts pressure on valves close to the inlet, limiting rangeability and stable control. However, there have been considerable breakthroughs in this area, which now make it easier for LNG plants to process more efficiently and without the issues resulting from flow instabilities, shifting temperatures and changes to flow velocity.
The Noise Problem
LNG trains often exceed accepted noise tolerances of 85dB, with several sources contributing to the problem. Compressors, for example, increase the pressure of natural gas before it enters a liquefaction unit. These machines are working at high rotational speeds and, as the name suggests, make use of gas that’s highly compressed. This on its own is loud enough, yet there are also pumps, heat exchangers, turbines and vents that add to the overall noise levels on site. Some of this equipment can be housed to mitigate noise levels, though this is not always practical.
Valves present a more complex challenge for managing noise at LNG plants – mainly due to the complex physical changes taking place inside pipework when natural gas is transferred from one area to another. When a control valve opens or closes, gas rapidly changes its flow rate and direction, causing turbulence and fluctuations in pressure. These changes can cause major tremors and vibrations inside the valve and downstream through the pipework.
Until recently, noise has only been a significant problem for staff working at plants. However, urban sprawl and an increased demand for LNG has brought residences much closer to the source of potentially hazardous noise. In 2020, for instance, locals in the Welsh town of Milford Haven complained of a constant low droning, likened to a helicopter hovering nearby. The source of the noise was traced back to an LNG tanker berthed at a nearby terminal, which was preparing to offload its cargo. Cases like this are becoming increasingly common, particularly in coastal areas where LNG plants are located, restating the need for better mitigation techniques at source.
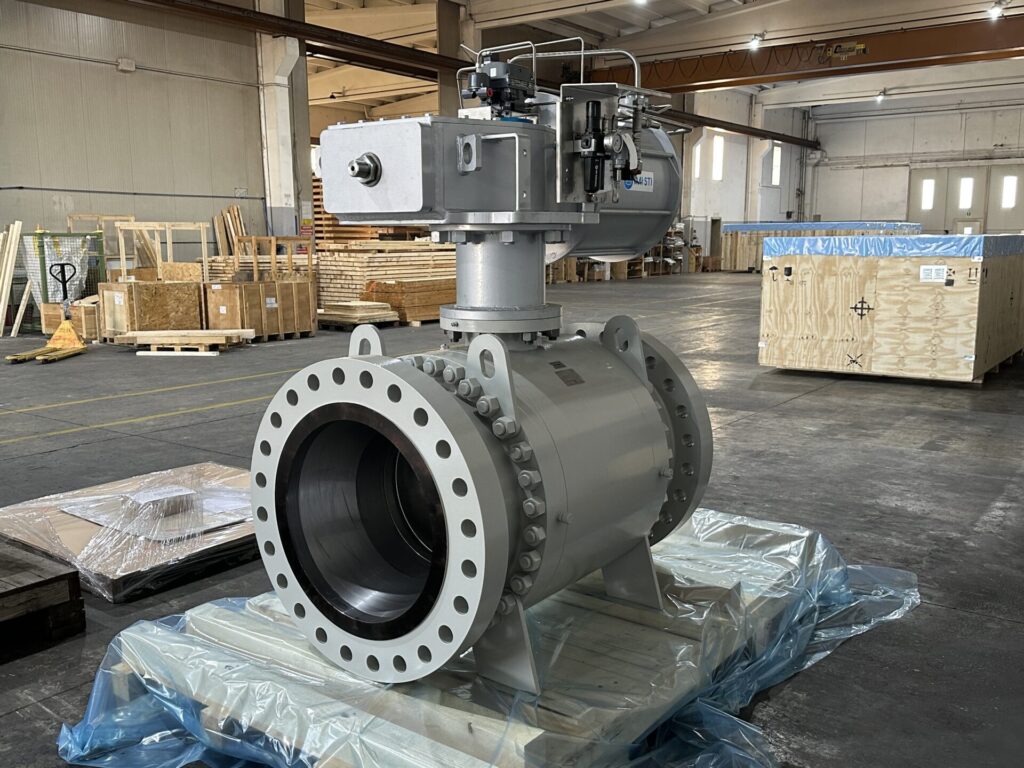
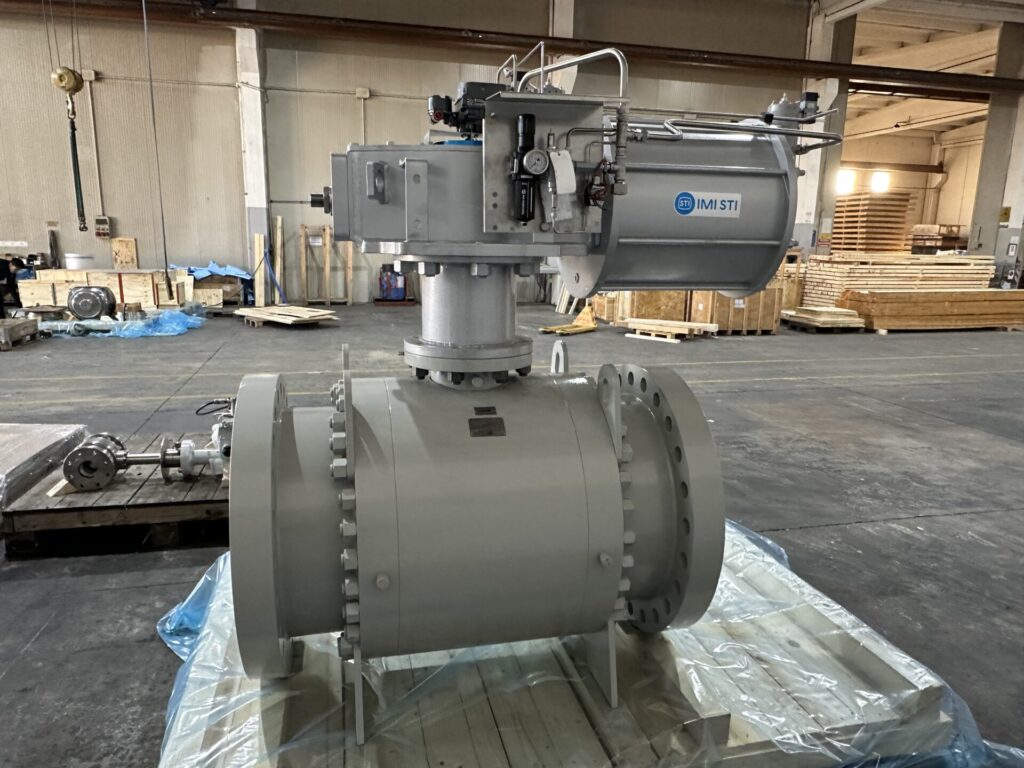
Reimaging Flow Control
Such techniques can be seen through IMI’s recent work with a major LNG producer in the Caribbean. The company operates four liquefaction trains, with a total capacity of approximately 115 million tonnes of LNG per year, making it among the largest in the world.
In the early 2000s, the customer approached IMI to address the criticality of its feed gas flow control valves. The feed gas line size was already sized at 24 inches, while the flow control valve on the data sheet, specified as a linear motion globe valve, should have been 36 inches to accommodate Cv requirements.
In response, the IMI team worked on a new valve design to improve safety and total gas output. To maximise the valve’s Cv, a quarter-turn ball valve was proposed with an inherently higher flow capacity and the addition of a customised multi-stage trim design based on the company’s patented DRAG™ technology – a revolutionary solution first developed by the company in 1960s to control high pressure drops. IMI called this valve dBX Shield, owing to its ability to manage and minimise flow control issues
Modulating valves for feed gas applications foresee multi-stage trim, making them an ideal application for the introduction of DRAG™. Adding it to a quarter-turn trunnion mounted ball valve was considered a new approach at the time of development, allowing for a consistent space and weight reduction compared to traditional solutions, as well as better sealing performance when closed.
Over the years, this novel valve design has gained momentum and been further improved with the introduction of new manufacturing techniques. The DRAG™ element, for instance, was optimised with the introduction of additive manufacturing, making it easier to make incremental design improvements without having to modify the overall valve design. Today, the dBX Shield offers unprecedented possibilities for flow control, reducing noise in some settings to just 60dB.
The LNG facility in question carries out regular inspections to identify and eliminate asset integrity issues stemming from installed assets. This is what led the facility to move from its existing linear valves to a single dBX Shield, finding the move would improve plant efficiency, tackle on-site noise and secure higher yields.
There has been a marked improvement since the site upgraded its train two feed gas line valve to a dBX Shield 24-inch reduced bore. Further valve inspections have now resulted in a repeat order for the facility’s third train feed gas line.
Additive Advantages
IMI has been working with additive manufacturing since 2010, investigating and testing it for the use in the production of standard production parts, including DRAG™ trim. The technology and recognition of the process has grown considerably as it has advanced over the past decade. Improvements to additive manufacturing machines have also had a large impact on the design and manufacture of complex components for a wide number of industries including aerospace, defence, medical and automotive industries.
Within IMI, additive manufacturing is commonly used for the production of DRAG™ trim components. 3D printing offers several advantages for simplifying the manufacturing process, including reduced raw material usage, quicker delivery times and consistency of valve trim components.
The gas industry is seeing an increasing trend in the demand for fugitive emission control mandated by global standards such as ISO 15848, API 641 and API622. Fugitive emissions through any static or dynamic joints or seals within the valve are key areas of potential leakage. Quarter-turn valves by design have better sealing capabilities through their life, so as the LNG industry looks towards carbon reduction, valve selection will be crucial.
With more than 160,000 DRAG™ trims installed in severe service control applications world-wide and 14,000 isolation valves installed in applications where safety, integrity and performance are critical, the dBX Shield rotary control valve has a strong pedigree.
Additive manufacturing is still a developing technology and machines have limitations in the production of component sizes. To work around this, a method was developed by IMI to produce a DRAG™ flow control element in a shape that could accommodate the use of 3D printing. Working this way also meant the product was not limited by the machine’s capabilities.
Base material for the dBX Shield trim is Inconel 718, as this delivers optimal performance for both the printing and design requirements. This design also allows trims to be engineered specifically to meet customer process flow requirements. The ball valve retains all of its capabilities in terms of sealing, fire safe certification, and quarter-turn actuation with full modulating functionality.
The design delivers the highest rangeability in its class at 1000:1 full noise, velocity and kinetic energy that fully meets ISO/IEC control valve sizing. The use of this valve in LNG feed gas and gas pipelines significantly reduces infrastructure capital costs. As seen in the earlier example, it eliminates the need for multiple valves and offers weight savings when compared to a traditional globe control valve.
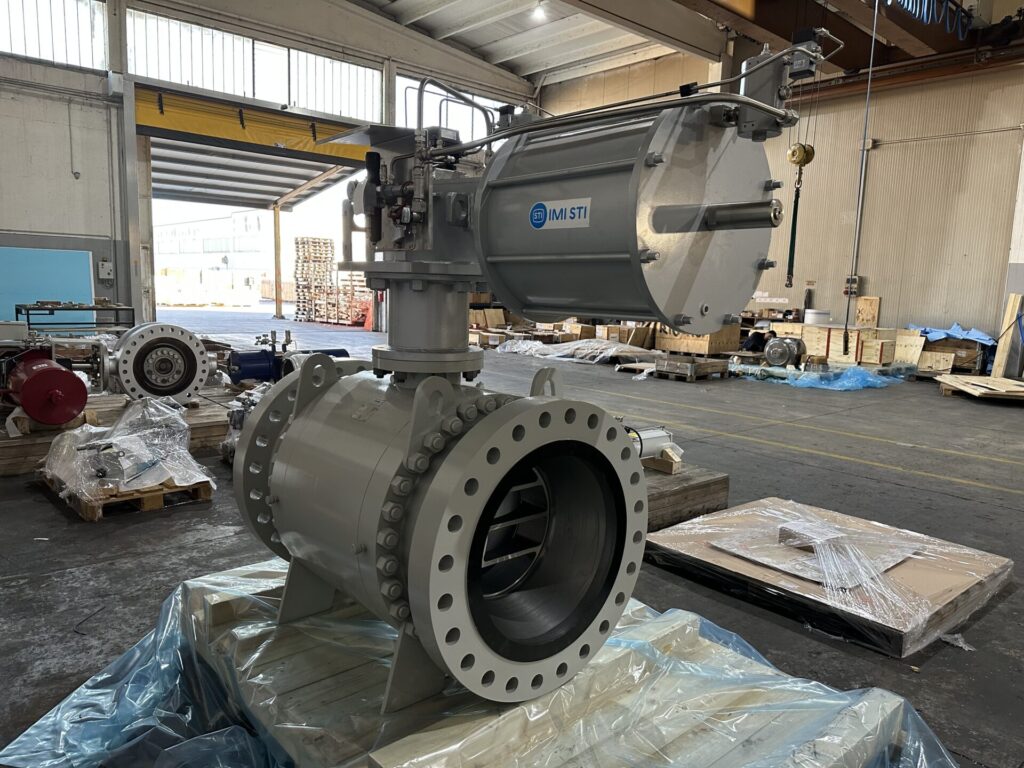
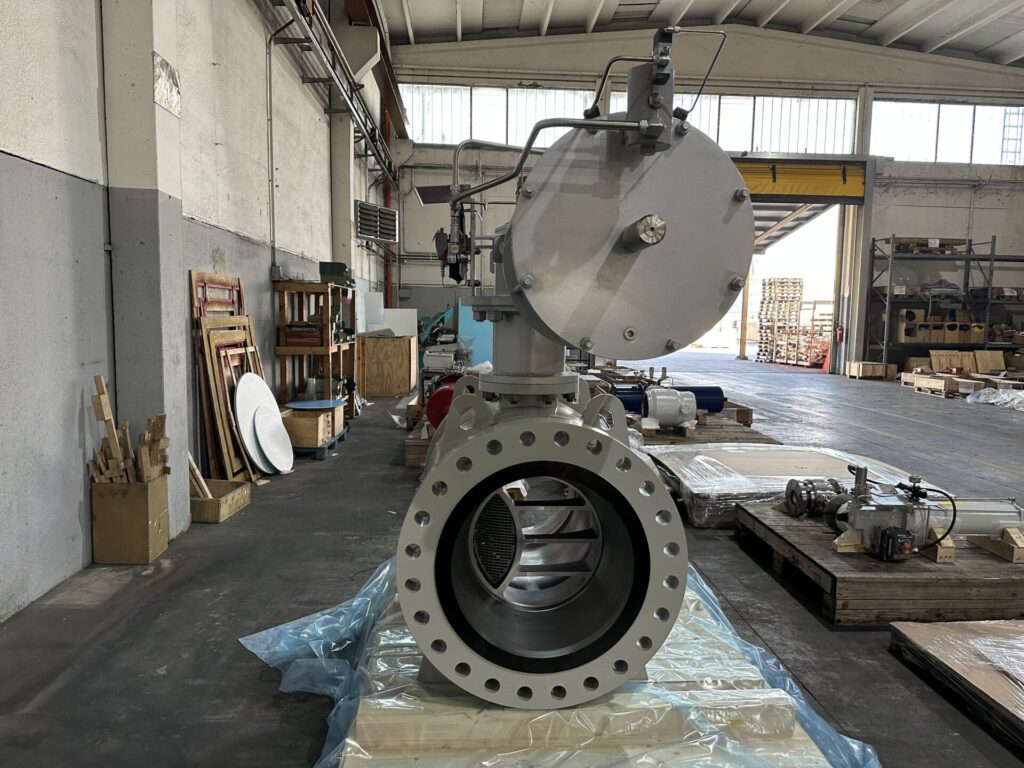