Refineries need to recover sample liquids from online analyzers; there’s no room for guesswork. Reliability matters. Maintenance resources are stretched thin. And failure isn’t an option because if the recovery system goes down, so does everything else.
That’s the problem Xenon set out to solve with its unique Liquid Recovery System (LRS). It’s a inert gas-driven, pump-free solution that recovers and returns process liquids from atmospheric drains back into the system with minimal, if any, intervention.
Typical applications include:
- Atmospheric drain and sample recovery for online analyzer effluents
- Rotating equipment lube oil collection and recovery
- Condensate recovery
Designed for high reliability and simplicity, Xenon’s LRS replaces traditional pump-based approaches with an innovative two-tank configuration, using Siemens instrumentation and local support from Siemens partner Ponton Industries.
Decades of refinery engineering experience
Based in Irvine, California, Xenon is a full-service engineering inte¬gration firm with deep roots in the refining industry. The company provides instruments, controls, and electrical integration services in-house. It can design, build, and commission complete turnkey systems without needing to outsource expertise. This allows for tighter integration and a “one-stop shop” for customers.
Many on the team, including Managing Partner Michael Andraos, spent years working inside refineries of major oil companies be¬fore founding Xenon in 2007. That frontline experience gives the company a unique advantage when it comes to understanding customer needs.
“I’ve sat in the maintenance seat, I’ve sat in the reliability seat, and I’ve managed analyzer systems for an entire refinery,” says Andraos. “So, when we design systems, we don’t just think about how they’ll work on paper. We think about how they’ll be installed, how they’ll be maintained, and what happens when something goes wrong.”
Today, Xenon’s LRS is being adopted by major fuel producers for its simplicity, reliability, and ability to support real-time process optimization. With Siemens technology playing a supporting role in the background, and Ponton’s guidance helping ensure proper component selection and delivery, Xenon is helping customers. Andraos notes: “Our LRS design can be customized for different process liquids and deployed beyond refineries in other process in¬dustries that need to recover and reuse sample streams, providing cost savings and environmental benefits.”
Challenge: Engineering for performance, simplicity, and reliability in a resource-constrained world
In process industries, production disruptions can be extremely expensive. And when a support system like an LRS goes down, it can compromise entire optimization systems, costing six figures or more. That’s why Xenon designed its pump-free LRS around a simple but essential goal: it had to work reliably in demanding industrial environments.
“Reliability is paramount,” says Andraos. “It’s more important than any one analyzer, because if the recovery system fails, the entire analyzer system fails. We designed our LRS to be bulletproof.”
Traditional LRSs rely on rotating pumps to move sample effluent from atmospheric pressure into pressurized process headers. But pumps require maintenance and are significantly less reliable. The Xenon engineering team’s experience in refinery operations told them there had to be a better way.
Ditch the pump. Their solution was to eliminate the pump entirely. Xenon’s system uses ball valves with any inert gas, such nitrogen, as the motive force, cycling between fill and discharge modes to move recovered liquids with minimal moving parts. But designing around this concept presented its own set of challenges —tight control logic, precise level sensing, and a need for seam¬less integration across components.
Adding to the complexity, many customers operate in hazardous environments with minimal staffing. Analyzer technicians are scarce. Maintenance resources are pulled in multiple directions, often tasked more with compliance monitoring than process optimization.
“Our customers don’t have time to babysit these systems,” says Andraos. “We knew we had to make our LRS not only perform precisely with dependable data readings in real-world applications but also reduce complexity and constant maintenance.”
Designing a solution that met those standards—while remaining cost-effective and customizable—required careful engineering with every component working as hard as the system itself.
Solution: Use advanced, ultra-reliable Siemens instru¬mentation
When Xenon set out to design its pump-free LRS, instrumen¬tation was core to its operation. The entire system depends on continuous and precise level monitoring and a failsafe interlock to keep its pressurized cycles running safely and smoothly. For those capabilities, Xenon turned to Siemens.
“We knew Siemens as a strong, reliable brand,” says Andraos. “We’d used their instrumentation in other applications and had good experiences. For this system, we needed technologies we could trust completely, and Siemens has given us that.”
Xenon’s LRS solution relies on two key Siemens devices: the SITRANS LC300, a continuous capacitance level transmitter; and the SITRANS LVL200, a point level switch that serves as a high-level safety interlock.
The LC300 continuously monitors fluid levels in the discharge tank, feeding data to the PLC that controls fill, pressurize, and discharge cycles.
The LVL200 adds a protective layer, putting the system into a “safe park” mode if levels rise too high. “We can’t operate without those two SITRANS devices,” says Andraos. “They’re absolutely critical to our LRS design and operation.”
Easy integration and configuration
The instruments were also easy to integrate. Both the LC300 and LVL200 connected seamlessly with Xenon’s PLC and HMI architec¬ture, Andraos reports.
“Configuration was straightforward with no complex program¬ming, or calibration needed,” he says. “That mattered for our systems, which we designed and built to operate in remote or hazardous locations where simple operation and ultra reliability are critical requirements.”
Support from Ponton Industries, Siemens’ channel partner, helped accelerate component selection and deployment. “Ponton’s been great,” said Andraos. “They’ve always got us the answers we need, even on short notice. Every company needs a highly capable sup¬port partner like what we have that with Ponton.”
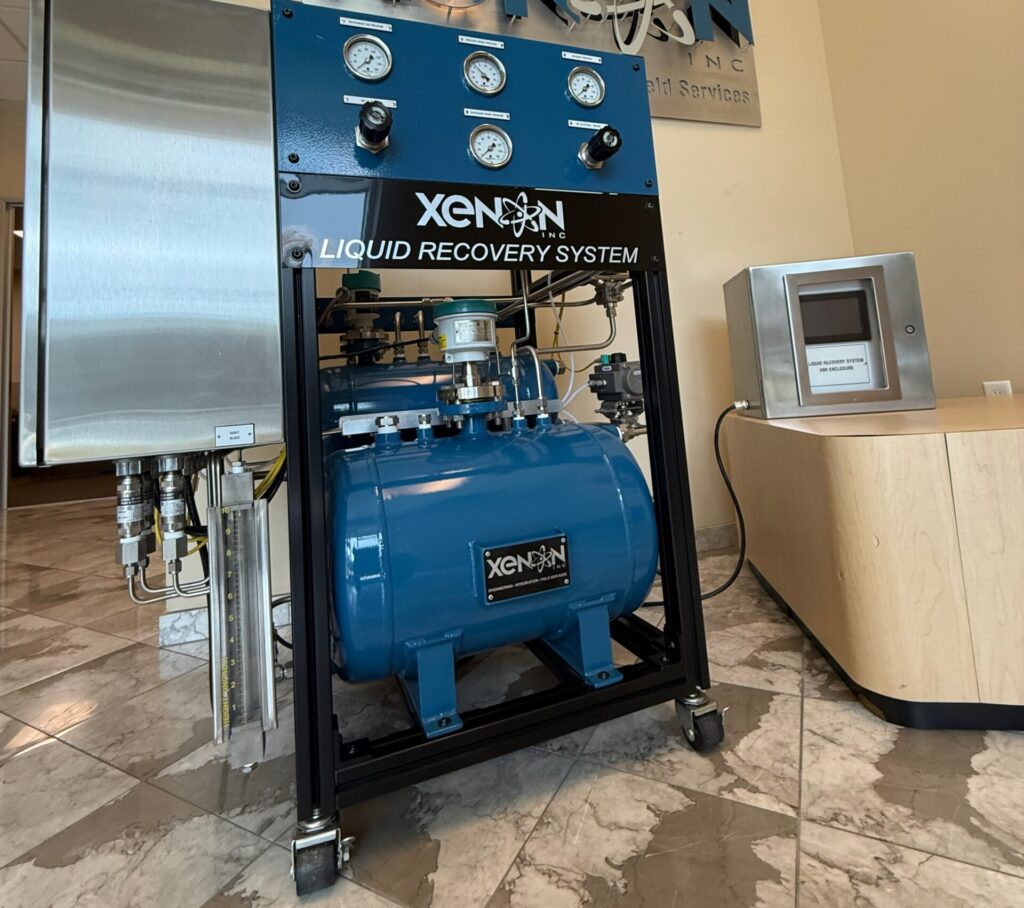

Results: A trusted solution that’s gaining ground with top-tier customers
Since launching its LRS, Xenon has earned the trust of some of the most respected names in U.S. refining. Plants that once strug¬gled with unreliable mechanical pump-based recovery setups are now seeing fewer maintenance calls, better analyzer uptime, and greater peace of mind.
“Every site that’s tried the LRS has come back for more,” says Andraos. “And the reason is simple: it works. It does exactly what it’s supposed to do—quietly, reliably, and without creating new problems.”
The LRS’s simplicity has proven to be a major advantage. Analyzer technicians can operate the system without needing significant training or oversight. In addition, maintenance technicians appre¬ciate that there are no pumps to rebuild, no oil to change, and no moving parts to troubleshoot.
“The Siemens instrumentation has been flawless,” Andraos adds. “We’ve had next to zero failures in the field. That kind of reliability is what our customers count on.”
Demand for Xenon LRS solutions has grown, especially in critical refining environments like Fluid Catalytic Cracking Unit (FCCU) gasoline blending processing and alkylation areas, where reliability is non-negotiable. Each LRS unit is built to order, and Xenon continues to refine the design based on real-world feedback from plant operators and technicians.
For Ponton Industries, Xenon’s success is no surprise. “Given the company’s experience in the refining industry, which extends to many other process industries, their engineers really understand what their customers need,” said Karen Mansilla, OEM Account Manager at Ponton. “Xenon is solving a specific pain point for pro¬cess industries with a well-thought-out design, and our role is to help them keep their system simple and reliable.”
How the Xenon Liquid Recovery System works
- Pressurized Operation: The LRS uses inert gas to pressurize the system and push the liquid effluent back into the process header, rather than using a pump. This makes the system more reliable with fewer moving parts.
- Two-Tank Design: The system has two tanks – a receiver tank that is continuously vented to atmosphere, and a discharge tank that is pressurized to push the liquid back into the process.
- Level Monitoring: A Siemens capacitance level transmitter (LC 300) monitors the level in the discharge tank. A Siemens level switch provides a high-level interlock to shut down the system if levels get too high.
- Automated Cycling: The PLC controls the opening and closing of the ball valves to automate the fill, pressurize, discharge, and vent cycles based on the tank levels. This is all monitored and controlled through a user-friendly HMI.
- Safety Features: The system has numerous interlocks and safeties, including pressure monitoring, valve position feedback, and timeouts, to ensure the system operates safely and does not over-pressurize or discharge liquid improperly.
- Reliability Focus: The lack of rotating equipment like pumps, and the use of highly reliable ball valves makes the LRS a very low-maintenance system compared to traditional liquid recovery approaches using pumps.
Siemens SITRANS LVL200 Point Level Switch Overview
The SITRANS LVL200 is a standard vibrating point level switch de¬signed for industrial use in all areas of process technology. These include liquid and slurry use cases such as overflow, high- and low-point level detection, and dry run protection.
It is deployed worldwide in chemical, oil and gas, pharmaceutical, food and beverage, and general industries.
Rated for SIL-2 uses, it can be used in such challenging conditions as flow turbulence, air bubbles, foam generation, buildup, or external vibration.
With a tuning fork insertion length of just 40 mm (1.57 inch), the SITRANS LVL200 can be mounted in small pipes and applications with confined space.
Siemens SITRANS LC300 Level Transmitter Overview
The SITRANS LC300 is an inverse frequency shift capacitance continuous level transmitter for liquids and solids applications. It is ideal for industrial applications in chemical, hydrocarbon pro¬cessing, food and beverage and mining, aggregate and cement industries.
The 2-wire level measurement instrument combines a sophisticat¬ed yet easy-to-adjust microprocessor with field-proven probes. It is available in four versions:
- Rod only
- Rod with stilling well
- Cable with PFA insulation
- Cable without PFA insulation

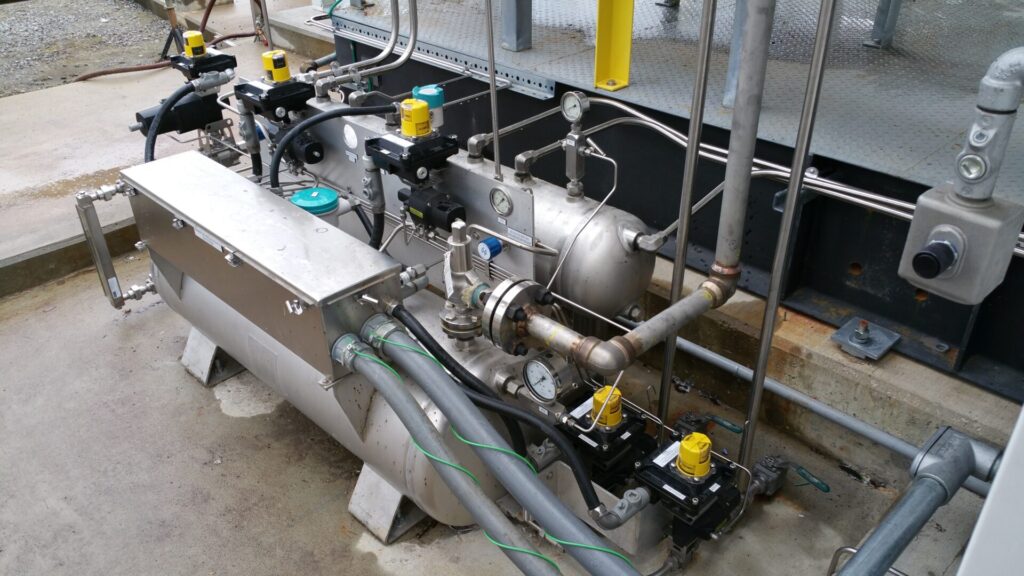