- Product loss in dairy processing is becoming a pressing concern as companies in the EU are required to report for the EU CSR Directive for the first time in 2025
- Product loss in push-out processes can be prevented by more accurate detection of the contents in the pipeline. This can be achieved using dielectric detection
- More stringent regulatory requirements and changing consumer preferences are powerful incentives for dairy companies to reduce product loss
From 2025, listed companies in the EU with more than 500 employees will be required to report sustainability information according to the new mandatory European Sustainability Reporting Standards (ESRS). This requirement will be expanded over the coming years to cover further categories of companies.
Product loss is a significant problem at many dairies and can have a large impact on the carbon footprint. Hundreds of liters of product is often lost to the drains when liquid product is displaced with water by pushing it from one processing step to another. Frequently, as much as 1% of dairy production can be wasted in the push-out between product batches. For an average dairy plant processing 250,000 tons of raw milk annually, this means a loss of 2,500 tons of raw milk, as well as unnecessary CO2 emissions upstream in the supply chain.
However, inaccurate measuring technologies frequently prevent operators from addressing this issue in an effective way, as it can be difficult to correctly identify the product that moves through the pipeline. But with appropriate measuring technology, the end of one batch and the beginning of the next can be accurately located. If it is not, the small losses at each push-out point, of which there can be hundreds, accumulate and become significant by the end of the process.
Pipeline contents are commonly measured by one of the three technologies – flow meter, turbidity sensor or conductivity sensor. Flow meters estimate the arrival of the product at the push-out point based on the system flow rate; turbidity sensors monitor the interaction between a light beam and the liquid; and conductivity sensors operate by measuring the electrical conductivity of the liquid.
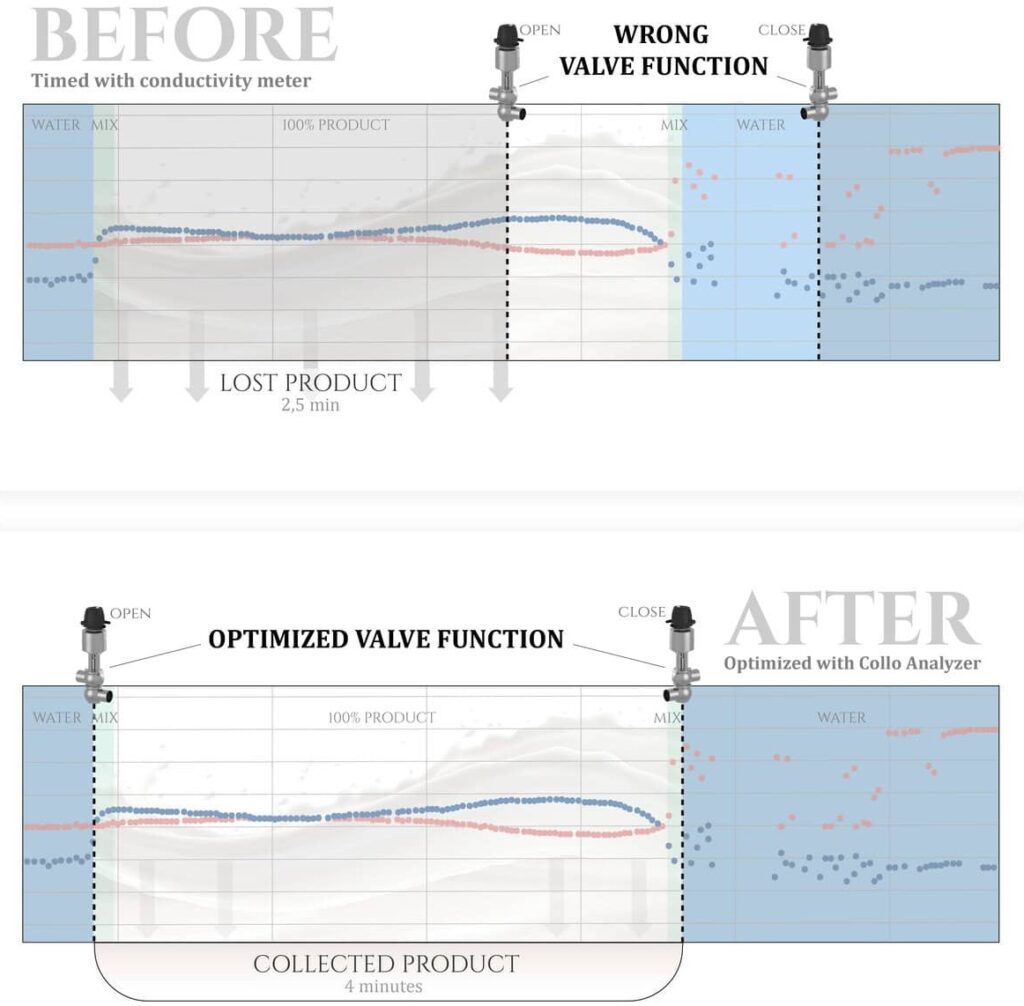
A fourth method is based on monitoring the dielectricity of the liquid, i.e. its ability to hold electric charge. This is achieved by using a sensor that accurately identifies the substance moving through the pipeline as a radiofrequency electromagnetic field is induced into the liquid. Different liquids have different dielectricity, making them distinguishable from each other, giving each liquid a unique fingerprint.
“Measuring the dielectric properties of the liquid provides significant advantages over traditional approaches. Flow meters have very low accuracy and turbidity sensors cannot distinguish transparent liquids, such as whey concentrate, from water, and become clogged by thick liquids, like cream. The electrical conductivity of milk-based products is close to that of water, which translates into low sensitivity for conductivity sensors when detecting product interfaces,” says Matti Järveläinen, CEO of Collo, a leading manufacturer of dielectric liquid analyzing systems.
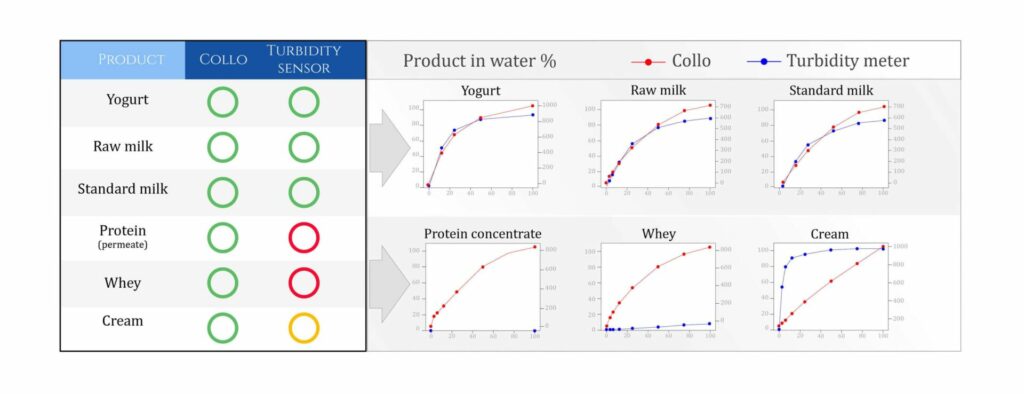
The dielectric sensor can detect any liquid, whether it is thin, thick, colored, colorless, opaque or transparent. This means that the same measuring technology can be applied across the dairy plant, while in the past the plant needed to select the sensor based on the type of liquids processed in each particular location,” adds Järveläinen.