A polymer leak will halt production and is costly, time-consuming and labour-intensive to clean up, and also creates a safety risk. Wastewater treatment operators want to avoid the disruption of maintenance downtime while also abiding by strict regulations for harmful chemicals, pharmaceutical residues, and microplastics.
In Germany, these regulations mean the opportunities for reusing wastewater sludge as agricultural fertiliser are being increasingly limited and sending it to landfill is usually not permitted. This means thermal recycling is becoming more and more accepted as a highly effective way of sludge disposal, but the required sludge dewatering and polymer dosing during the sludge conditioning process can add significant cost. Therefore, identifying cost-efficiencies in the dewatering process can mean significant savings for wastewater treatment plant operations, and reduce the amount of sludge produced and polymer used.
The operator of a wastewater treatment plant in Heide, Schleswig-Holstein, Germany, changed its chemical dosing pumps after experiencing maintenance interventions and polymer leaks with progressive cavity pumps. Also, there was no leak detection system in place, so if a tube failed the entire polymer contents in the container could leak out. This meant a loss of expensive polymer, additional maintenance, and time to clean up leaked chemical. Additionally, the amount of time and effort involved in servicing the screw pumps, due to the different parts that come into contact with the polymer, was a growing problem.
Peter Dohrn, wastewater treatment manager and technical department manager at Abwasserzweckverband Region Heide (AZV Heide), said: “A slippery mess on the floor would require intensive cleaning. Every servicing run involved several hours of work [with the screw pumps]. Also, the extremely heavy progressive cavity pump was hard to move around, and its working principle meant it couldn’t achieve the dosing accuracy of other pumps due to its design.”
Spill prevention – avoiding high cleaning costs and environmental damage, while ensuring safety of workers – is a key consideration when deciding which pump solution to use for handling polymers.
Water treatment operators therefore need to consider prioritising the adoption of dosing solutions that avoid messy polymer leaks because of the following:
- Cost Wasting polymers is expensive. Major producers of specialty chemicals recently announced price increases in products like polyacrylamide (PAM). Then there is the cost of cleaning products in the event of a polymer leak.
- Sustainability To ensure a sustainable use of polymers is achieved by minimising polymer use with accurate dosing pumps; eliminating chemical waste through leaks, and avoiding the need for cleaning chemicals in the event of a spillage.
- Safety Spilled polymer is extremely slippery and difficult to clean, with the possibility of some residue left behind causing a safety risk of slipping for operators if it gets wet.
- Maintenance Water treatment operators are under increasing pressure to produce more clean water so cannot afford downtime. Some rural plants also have a small workforce where regular, unplanned maintenance is a challenge.
- Accuracy Reliability of the dosing pumps is critical to thickening the sludge in a cost-effective manner.
The Heide water treatment plant replaced its screw pumps with a Qdos 60 PU peristaltic pump, from Watson-Marlow Fluid Technology Solutions (WMFTS), which has been specially designed to dose hard-to-process polymers, and other hydrocarbons, with high-precision accuracy for its sludge conditioning process.
ReNu PU (polyurethane) pumpheads for Qdos® peristaltic pumps are designed to avoid messy situations by safely containing polymer spills in the event of tube failure.
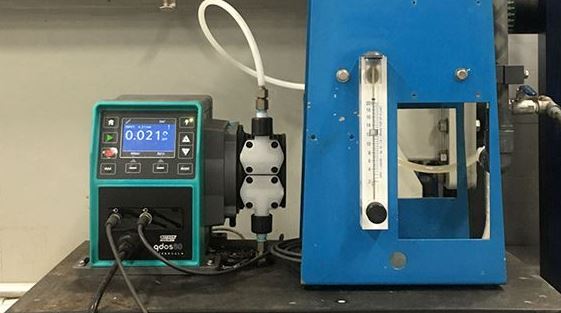
ReNu PU pumpheads are now available in two sizes: Qdos 20 PU up to 28 L/hr at pressures up to 4 bar), and the recently released Qdos 60 PU (up to 60 L/hr at pressures up to 5 bar). Specifically designed for polymers, the polyurethane (PU) tubing element is not damaged by the chemical.
The specialised tubing sits within the sealed housing of the pumphead, so if there is a leak, the pumphead contains the polymer spillage which minimises chemical waste and stops creating a safety risk which has been important for operators at Heide in Germany.
“In comparison to our previous pump, the Qdos has a much higher level of safe chemical handling and operational safety,” said Dohrn.
“Thanks to its highly effective suction capability, the self-priming Qdos pump can extract polymer from the IBC (intermediate bulk container) from above by means of a suction tube. The pump handles the suction height of just under a metre with ease. The pump can also empty the polymer almost completely reducing the risk of leakage during changeover.”