Making white liquor
The process starts when the smelt from the recovery boiler is dissolved in weak wash in the dissolving tank to produce green liquor. The raw green liquor, which consists mostly of sodium carbonate and sodium sulfide, is then pumped into a stabilization tank to even out fluctuations in density and temperature, and to ensure a more constant liquor composition to the causticizing process.
The clarifier aims to obtain a well-clarified green liquor for the slaker. It also reduces dregs carryover, which causes problems in downstream equipment. In the slaker, the clarified green liquor is brought into contact with reburned lime. This slaking reaction converts the green liquor into white liquor by converting sodium carbonate into sodium hydroxide, an active pulping chemical. Impurities, known as grits, are also separated at this stage.
White liquor is produced in slaker where sodium carbonate (Na2CO3) reacts with reburned lime (CaO) forming white liquor (NaOH) and calsium carbonate CaCO3, which is separated in lime mud washers and burned in lime kiln back to CaO.
Maximizing mill productivity
Green liquor density or TTA must be measured accurately to achieve high-quality white liquor. Real-time measurement and control of density/TTA during the causticizing process has several notable benefits:
- Increased causticizing efficiency
- Improved white liquor quality
- Safe operation of the green liquor dissolving tank and slaker
- Consistent and high green-liquor TTA levels for slaking
- Possibility to quickly trim green liquor automatically to counter disturbances
- Reduced risk of overliming
How to measure and control effectively
To carry out the causticizing process efficiently, controls are needed to achieve three main objectives:
- Stabilize green liquor TTA – this can be done by controlling dissolved green liquor density/TTA.
- Control the ratio of lime to green liquor – this can be done by using green liquor TTA trim control on the slaker.
- Stabilize white liquor effective alkali (EA) to the digester – this can be achieved by controlling the previous two objectives well, as well as controlling slaker causticizing efficiency and temperature.
The controls are needed in two places:
In the dissolving tank – inline measurement of density/TTA in the dissolving tank helps to maintain the target value of the green liquor and avoid deviations. This is a hugely important control for the stability of the entire line – sometimes said to be the point at which pulp making really starts. Measurements in the transfer lines are paired with a control loop to the weak wash liquor, giving automatic control based on density/TTA. The measurement device reads target values, avoids deviations, and is completely automatic, enabling stable TTA levels and safe operation of the dissolving tank.
In the slaker feed – the second control is placed inline for active slaker control, ensuring that the green liquor for slaking has a consistent TTA. The real-time density/TTA measurement is in the slaker feed and then a control loop ensures the automatic and quick trimming of green liquor to counter disturbances. This increases causticizing efficiency while also avoiding overliming, improving the quality of white liquor and lime mud. It also ensures the safe operation of the slaker.
Choose a reliable, real-time measurement method
There are several different methods to measure and control green liquor density/TTA in the causticizing process, but the most effective are inline, real time, and can be used for automatic control. Process refractometers offer several important several benefits:
- Real-time TTA or density measurement
- Measurement is not affected by particles, bubbles, fibers, color, or dregs
- High accuracy and repeatability
- No drift over time
- Out-of-the-box installation
- No regular maintenance
- Efficient scale prevention
- Reliable operation
Density measurement technologies, on the other hand, raise several challenges, including continuous scaling, drifting and measurement insensitivity, unreliable control requiring manual input, and an unstable process that leads to efficiency and production losses.
The Vaisala Polaris™ PR53SD Process Refractometer can be used to measure the density or TTA concentration of green liquor at both stages where control is needed: after the green liquor dissolving tank, and after the green liquor clarifier at the slaker feed.
The refractometer’s sensor is mounted directly in the pipelines for inline measurement, allowing real-time and active control to achieve the target TTA. The digital measurement is unaffected by bubbles, suspended particles, or color changes to the green liquor. The refractometer provides highly accurate measurement with no drift, and with an additional prism wash system it also supports scaling conditions.
Effective causticizing control improves the quality and stability of white liquor, decreases operating costs, and increases pulping efficiency. Effective lime dosage control reduces the recirculation flow of lime in the process, leading to less lime reburning in the lime kiln and decreased energy consumption. Real-time, accurate, and reliable inline measurement with a process refractometer is the easiest way to achieve these goals.
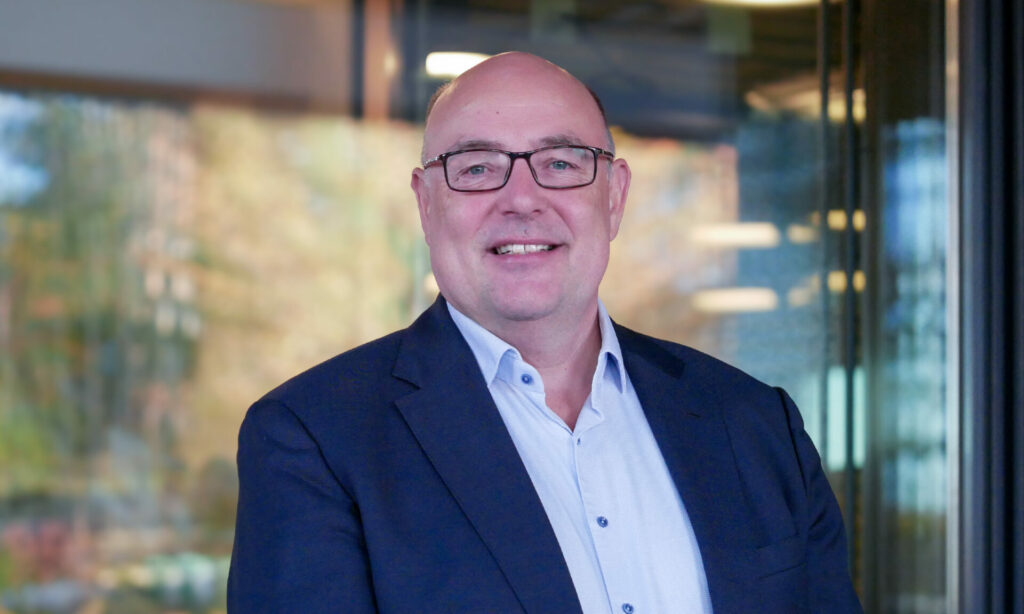