EtherNet/IP™ and PROFINET® are the fastest growing digital communication protocols in industrial automation, continuing to gain wider acceptance as companies look to transition from fieldbus to ethernet networks. They represent the largest number of new nodes of industrial ethernet networks shipped, at approximately 64% share of the total market[i]. EtherNet/IP™ and PROFINET® deliver the speed, precision, and reliability needed to manage and control information in real-time by connecting devices to a single network, allowing users to collect meaningful data that helps keep critical systems on track. In addition to basic process control, information transmitted via the EtherNet/IP™ and PROFINET® networks can be used for enhanced diagnostics, deviation alarms or predictive maintenance – all of which maximize system uptime and save costs.
Recognizing this trend, Brooks Instrument has worked closely with process and automation engineers to bring the EtherNet/IP™ and PROFINET protocols to its industry-leading SLA Series mass flow controllers (MFCs). The SLA5800 and SLAMf mass flow controllers are available with either EtherNet/IP™ or PROFINET protocols and come embedded with value-added alarm and diagnostic features.
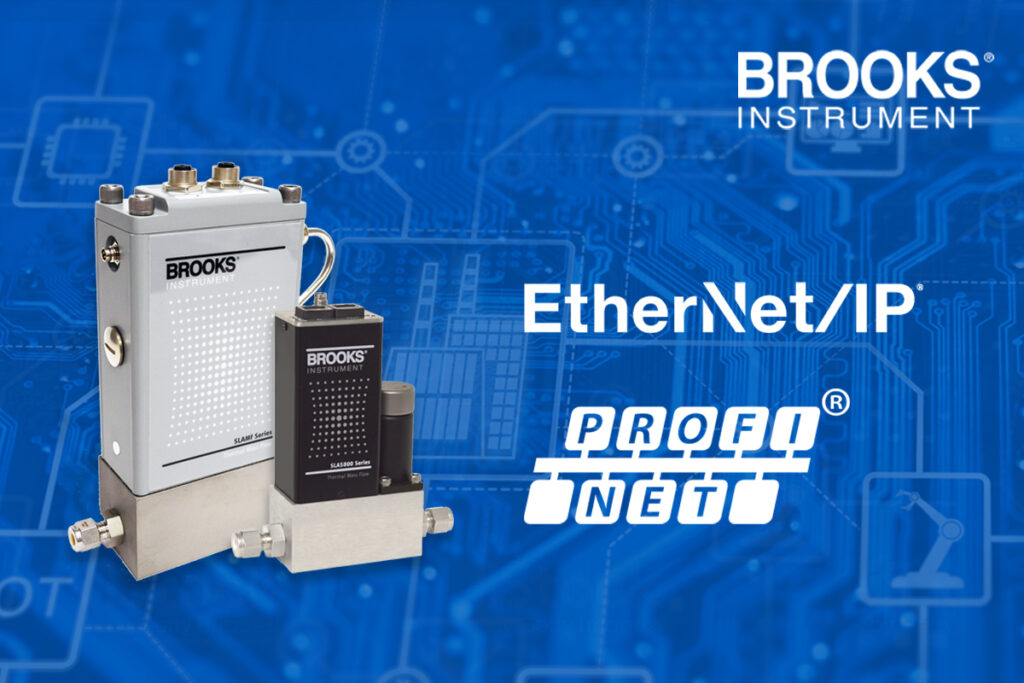
Why EtherNet/IP™ and PROFINET are Leading Adoptions of Industrial Ethernet Protocols
Relying on common internet and ethernet standards, key components of the value proposition for EtherNet/IP™ and PROFINET include:
- Various topology options, including conventional star, ring or daisy chain.
- Compliance with IEEE Ethernet standards provides a variety of network speeds to choose from – e.g., 10, 100 Mbps and 1 Gbps – operators can monitor real-time performance and network data.
- A flexible network architecture that is compatible with standard Cat 5 cabling and routers simplifies network setup and ensures all devices on the network communicate and exchange data with each other.
- Broad range of rich data for process control, monitoring, diagnostics and predictive maintenance can be made available from EtherNet\IP™ and PROFINET enabled devices.
1. EtherNet/IP™ and PROFINET are Open, Non-Proprietary and Future-Proof
Because EtherNet/IP™ and PROFINET utilizes the Common Industrial Protocol (CIP™), it is media-independent and therefore supported by a large ecosystem of solution providers for the automation of industrial processes. EtherNet/IP™ and PROFINET easily ties into a wide range of Distributed Control Systems (DCSs) and Programmable Logic Controllers (PLCs) including:
- Allen-Bradley
- Emerson
- Rockwell Automation
- Siemens
2. EtherNet/IP™ and PROFINET Seamlessly Communicate with Industry-Leading Control Systems
Original equipment manufacturers (OEMs) are rapidly adopting EtherNet/IP™ and PROFINET protocols because contract manufacturing organizations (CMOs) and end users recognize the opportunity to:
- Reduce operational costs
- Improve process performance, quality, yield and throughput.
3. SLA5800 and SLAMf MFCs Feature Plug & Play Integration with Rockwell Automation (Allen-Bradley) PLCs
To further simplify integration of the SLA5800 and SLAMf MFCs with EtherNet/IP™ into a network, Brooks Instrument engineers worked with Rockwell Automation to create an enhanced device profile that facilitates setup and integration of the MFC into the Rockwell Automation (Allen-Bradley) PLC. This allows for plug and play functionality of the SLA5800 and SLAMf with EtherNet/IP™ with leading automation suppliers.
While normal setup of a mass flow controller with a user’s automation network can take a significant amount of time to setup and program – especially when dozens of MFCs are involved – the enhanced device/add-on profile:
- Ensures all attribute tabs and parameters are visible and available for setup or adjustment – the user merely decides which attributes make sense for their process.
- Eliminates the need for programing expertise to get the MFC connected and communicating with the network.
4. EtherNet/IP™ and PROFINET are Fully Integrated into SLA5800 and SLAMf
By adding functionality, performance and value without sacrificing equipment space is fully realized in SLA5800 and SLAMf with EtherNet/IP™ or PROFINET. To address applications where gas cabinet space is at a premium, Brooks Instrument engineered EtherNet/IP™ and PROFINET directly inside the mass flow controller – no add-on adapters or modules needed. With EtherNet/IP™ and PROFINET fully integrated into SLA5800 and SLAMf MFCs, there is no change to the fit, form or function of the device. Whether you’re upgrading from an analog device to a digital protocol, or designing a new gas cabinet, the EtherNet/IP™ or PROFINET enabled SLA5800 and SLAMf MFCs maintains the same footprint as the standard SLA5800 and SLAMf. Additionally, the Brooks Instrument SLA5800 and SLAMf Series MFCs seamlessly connect to your EtherNet/IP™ or PROFINET networks. This allows the MFC to communicate directly with the DCS/PLC without requiring additional hardware, such as gateways, analog I/O cards or custom cabling and wires. Standard, widely available and cost effective ethernet cabling is all that’s needed to get your device running and connected to the network.
5. Web-Based Interface Allows EtherNet/IP™ and PROFINET Network Settings to be Easily Configured into SLA5800 and SLAMf
Another time saving feature of the SLA5800 and SLAMf with EtherNet/IP™ or PROFINET are their user-friendly TCP/IP configuration. When connecting the MFC to the user’s EtherNet/IP™ or PROFINET networks, a web-based interface allows network settings to be easily configured into the MFC. Once on the network, the user can easily identify individual MFCs which saves time – especially if there are multiple MFCs in the system.
6. EtherNet/IP™ and PROFINET Protocols Enable the Latest Diagnostics and Predictive Functions, Some of Which are Unique to Brooks Instrument MFCs, to Enhance Process Quality
The SLA5800 and SLAMf mass flow controllers with EtherNet/IP™ or PROFINET are intelligent and data-rich devices that can facilitate improvement in operational efficiency in areas of equipment automation, and metrology and maintenance.
For example, if upstream gas inlet pressure becomes restricted, the overall MFC accuracy could change. Using the built-in restricted flow alarm, the alarm data could be presented to an operator to prompt action.
Preventative maintenance and process quality are also enhanced by having a broad array of thresholds and alarms that can be set and monitored by the MFC, such as a high flow/no flow alarm and MFC calibration due.
In Summary
Process and automation engineers should consider that both EtherNet/IP™ and PROFINET® communication protocols are supported by a large ecosystem of solution providers for the automation of industrial processes; seamlessly communicate with industry-leading control systems; and easily integrate into the Rockwell Automation (Allen-Bradley) PLC. This all results in maximum system uptime and cost savings.