In the hydrocarbon industry, production processes are complex, and safety is paramount. Plant owners operate with a sharp focus on the bottom line, so finding a way to reduce costs and increase yields in a safe, cost-efficient framework is a very valuable find indeed. An often-overlooked method to improve the process is by updating the plant’s flow meters since they are paramount to increasing the accuracy and recording all measurements connected to the process. This type of upgrade can improve both the yield and the plant’s bottom line at the same time.
New flow sensors offer enhanced digital features for easier setup and troubleshooting as well as predicative maintenance, in addition to higher accuracies and reliability. Each new feature and improved specification helps to save time, man-hours and costs.
Challenges in the hydrocarbon industry
One of the most challenging opportunities within the oil and gas industry is achieving repeatable, highly accurate flow measurements that can minimize losses and optimize the process.
Many installations in rugged applications and harsh environments can push flow meters to the very edge. Durable and precise flow meters are critical to ensure proper measurement of the media and assure an efficient, profitable operation.
A shift in technology
Turbine meters are a traditional and cost-effective tool for flow rate measurement in natural gas production, but their low price comes at a cost, as they are not without challenges in practice: turbine meters’ moving parts never mix well with grit or sand. Meter internals can show wear, reducing measurement accuracy in relatively short order. The result is costly maintenance time, soon followed by inevitable replacement.
New and improved technologies have allowed a significant shift to take place, resulting in reduced use of turbine meters in natural gas applications. Turbine meters are being replaced by electronic flow meters, leaving their problematic consequences behind. Siemens Process Instrumentation has been an innovative supplier of electronic flow meters to the hydrocarbon industry for many years.
The vortex flow meter
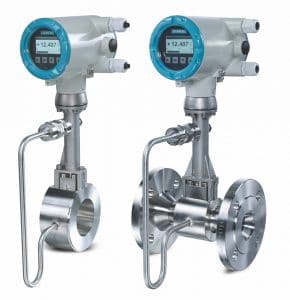
pressure correction all in one device.
Siemens has recently improved its offering with a new vortex flow meter, the Sitrans FX330. The vortex meter offers flexibility as it enables both the mass and volume measurement of steam and gases as well as liquid fluids, with onboard temperature and pressure compensation. When compared to the conventional turbine and differential pressure flow sensing technology, vortex offers a significant improvement with the ability to measure a greater variety of fluids and to do so with a much higher degree of accuracy and durability.
The vortex meter is perfectly designed for reliable gas flow measurement independent of changes in conductivity, temperature, density and pressure.
Excellence in performance
The hydrocarbon industry works under adverse and changing conditions, such as varying temperatures and pressures. This demands that the products applied in the processing industry be constructed of robust materials and designs. The Sitrans FX330 is designed to be rugged and durable and is resistant to pipeline hammer effects.
Impacts from external vibrations are also limited with the use of Intelligent Signal Processing (ISP), further improving the vortex flow meter’s reliability and performance in noisy applications.
The vortex sensor offers a fully welded bluff body that improves safety and robustness, making it perfect for harsh conditions. The vortex flow meters carry Class 1, 2 and 3 Division 1 and 2 approvals, which secure safe installations in a multitude of hazardous zones.
Ultrasonic flow measurement
Another technology growing in popularity in the oil and gas industries is ultrasonic flow, where Siemens has one of the most diverse offerings of clamp-on ultrasonic flow sensors available. Having this type of technology in the product portfolio enables Siemens to offer solutions to a wide array of installations within the industry. Choosing which one of the ultrasonic tranducers is the best fit for an application is not always a simple task. In each case, factors such as installation type, accuracy, pressure, approvals, and pipe size and material requirements must be evaluated thoroughly.
Easy-to-install clamp-on meters
Siemens offers two clamp-on ultrasonic product families:
- Sitrans FS230 for hydrocarbon installations
- Sitrans FUG1010 for gas applications
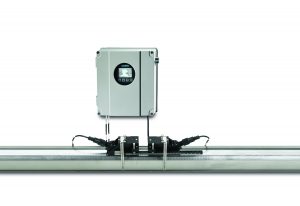
The hydrocarbon version of the Siemens Sitrans FS230 clamp-on ultrasonic flow meter is designed for applications such as ship offloading, pipeline transportation, process control metering, leak and interface detection, etc. For flow measurement, all Siemens clamp-on meters use a patented method of dynamically compensating for variations in the liquid properties and viscosity by continuously adjusting the Reynolds number. In addition to providing users with valuable diagnostic data, they allow an analog output of inferred viscosity values. The standard volume/mass meter has additional features, as the volume is compensated to a standard temperature as defined by the user. The clamp-on ultrasonic sensors are capable of accurately inferring the mass flow through a patented method of determining viscosity and density using the measured sonic velocity combined with the clamp-on temperature measurement. For even more precise density compensation, an analog input from a densitometer can be utilized.
The FS230 clamp-on ultrasonic flow meter is also a perfect fit for liquid mass leak detection. Mass flow leak detection is preferred over conventional leak monitoring. The reasoning is that the amount of liquid entering the pipeline is compared to the amount of liquid leaving the pipeline, providing a direct approach to line balance leak detection. In this type of installation one would employ a complete or partial system using the meter in combination with third-party software.
The Sitrans FUG1010 flow meter is ideal for natural gas and specialty gas industry applications, including check metering, lost and unaccounted for analysis, allocation, flow survey verification, production, storage, and gas-fired power stations. The Sitrans FUG1010 includes easy-to-use “data view” software that provides application and operational diagnostics, assuring calibration and operational integrity. Speed of sound calculations that comply with the AGA-10 standard are incorporated in the software for verification purposes. An internal AGA-8 compliant table for fixed gas composition is available for standard volume computation. As a special feature, the FUG1010 can be mounted on the wellhead of a gas well where it measures the amounts of gas coming directly from the well. No separator is needed, making it a very cost-effective solution.
The standard industrial FS230 is usually employed in non-critical, low-end applications where dynamic compensation for viscosity and density are not required. These include flush lines, sampler pacing, corrosion inhibitor injection, drag reducer injection, etc.
High accuracy multiparameter Coriolis measurement
Flow meters based on the Coriolis measurement principles offer the highest standards in accuracy and reliability. Traditional volume flow measurement technologies require compensation of temperature, pressure or density in order to calculate the mass flow rate accurately. The Coriolis meter measures mass flow directly and is not affected by changes in process variables, such as fluid density, pressure, viscosity, temperature, and flow profile. Furthermore, the Coriolis flow meter is compatible with just about any fluid, liquid or gas.
The Coriolis meters provide access to process temperature, density, mass and volume flow data, as well as fraction values for a mixture of two substances, such as oil and water. As the oil and gas industry faces the challenge of measuring a dynamically changing medium consisting of oil, water and gas under high pressure, the Coriolis mass flow meter is a perfect choice.
The fraction flow value output can be measured in mass units such as pounds or barrels as well as in percentage, and the obtained data can be used directly as input to a control loop, monitoring the mix ratio. This means that an in-line/real-time analysis of crude oil can detect high water content, reducing the need for sampling to a minimum. The results can be presented on a computer screen, immediately showing whether the media meets the required standards.
The density of the fluid is measured with an accuracy better than 0.06 lb./ft3 or ±0.001 g/cm3. For crude and hydrocarbon measurement this means that product quality monitoring as well as process control are made easier. The density value can indicate sudden shifts in media composition, for instance in the case of degassing or if the pipe runs empty.
These situations can lead to application hazards. By fully utilizing the multiple capacities of Coriolis flow meters, dangerous situations can be avoided, and an absolute minimum of instrumentation can be applied, e.g. as previously used densitometers are rendered superfluous.
In the oil and gas industry, where the costs of losses or downtime are prohibitive, it is additionally important that the Coriolis flow meter is available as a low-maintenance, high-accuracy and flexible measurement instrument.
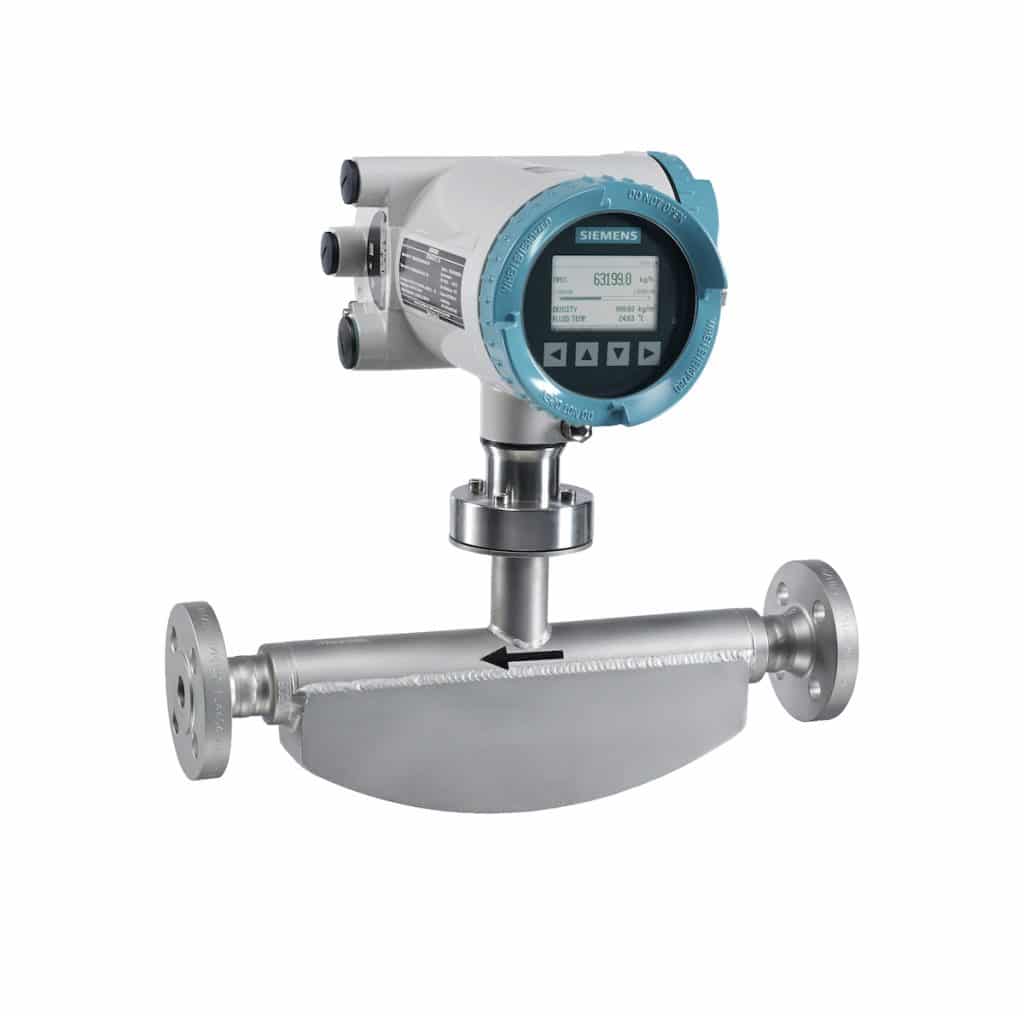
Experience you can trust
Siemens flow meters are designed to provide long-term reliability and sustained quality of measurement values. This is further enhanced by the fact that Siemens is well known in the oil and liquid petroleum gas industry, with many years of experience and successful completion of a broad range of projects. Choosing Siemens instrumentation guarantees safer, more profitable operations for the business of hydrocarbon delivery.
Eric Heilveil is the Flow Marketing Manager for Siemens Industry, Inc. Based in Harleysville, PA, Eric is responsible for business development and marketing of Coriolis, Vortex and in-line ultrasonic products. He has 25 years of experience in flow measurement, working for several companies as an
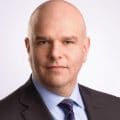
Account Manager, Salesperson, Product Manager, and Application Engineer. Phone: +1 (267) 470-3474; Email: eric.heilveil@siemens.com.