Heat pumps work by capturing heat from a source, in this case, waste heat from an industrial process, and amplifying and transferring this energy to supply heat for other industrial applications such as boilers, dryers, or preheating process streams. MVR heat pumps work by mechanically compressing low-pressure vapor, increasing the temperature and pressure of the vapor so that it can be repurposed as a heat source.
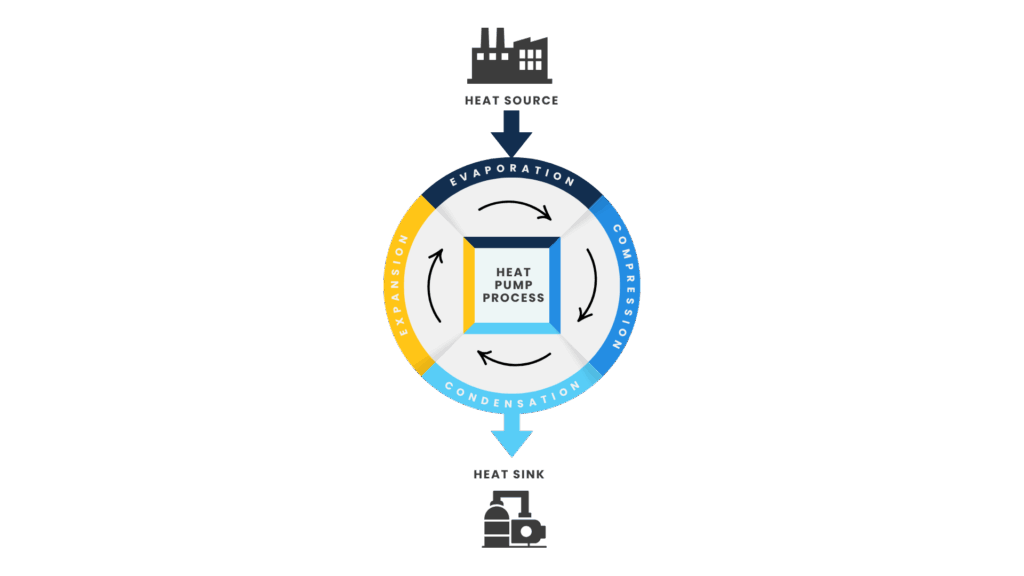
Because the mechanical compressor works with electricity, MVR heat pumps present an opportunity not only to recover and reuse waste heat from thermal processes, but also to reduce dependency on traditional natural gas boilers. Electrically-driven compression can help move a process closer to net-zero targets when the electricity for heat pumps comes from renewable, low-emissions energy sources.
In chemical manufacturing, MVR heat pumps can be integrated with separation processes such as distillation. This is because the hot vapor available at the top of a distillation column offers a waste heat source while, the bottom of the column requires heat input for the column reboiler. An MVR system can recover the waste heat from top-end vapor and deliver it as a heat source to the bottom reboiler. This can be designed as a closed-loop cycle to minimize external energy requirements.
Integrating MVR systems into chemical processes presents several challenges. Changes in temperature and pressure affect not only utility systems, but also vapor-liquid equilibrium, separation performance, and control strategies. Pressure, flow, and heat transfer must be carefully evaluated in both the heat pump process and the distillation process to avoid mismatches in operational performance.
One recent project by a Norwegian-based process consultant and equipment manufacturer successfully applied this concept. Using CHEMCAD process simulation software, the team simulated a solvent-recovery process to evaluate separation performance, reboiler energy demands, and utility-side integration.
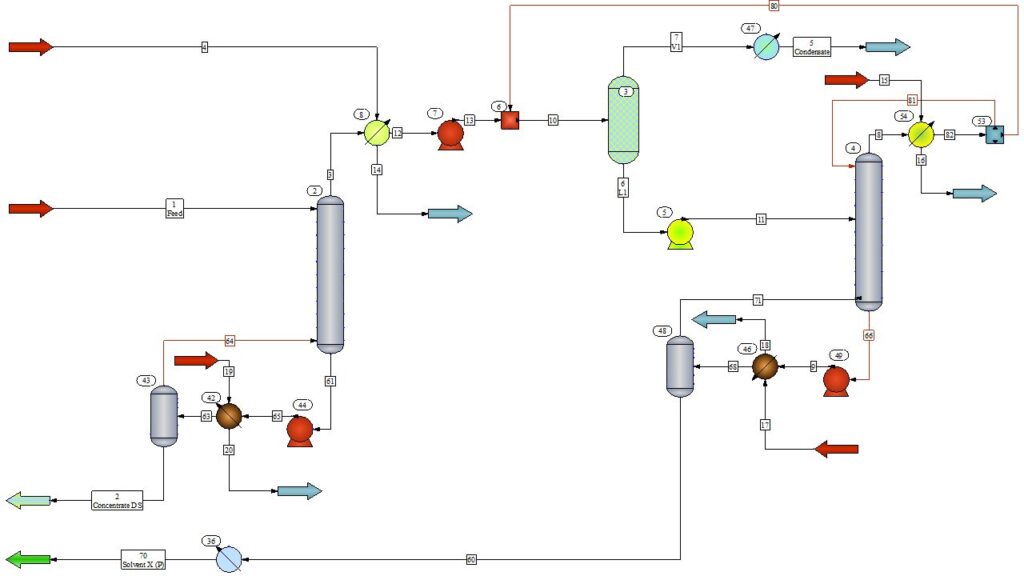
The goal of the simulation was to determine the energy demands and process conditions, and integrate an indirect MVR heat pump system with the solvent recovery process. The system utilized water as the working medium, enabling the entire process to operate without the need for boiler steam. This approach was expected to significantly reduce production and operating costs, as well as carbon footprint. Beyond finding the heating and pressure requirements of the MVR heat pump side, the team sought to optimize distillation variables such as number of stages, reflux ratio, and feed point location to minimize the required reboiler energy.
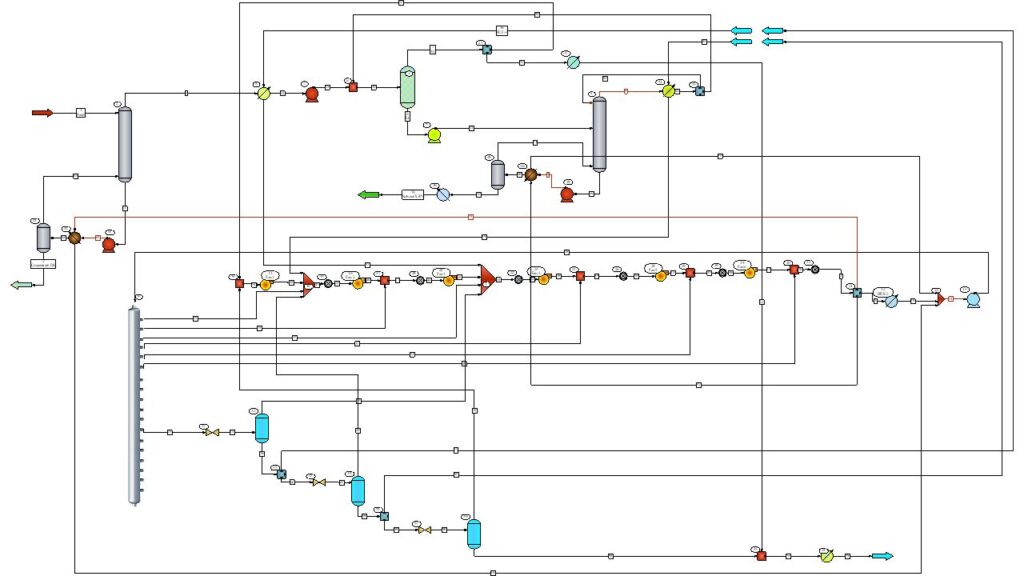
As industries from specialty chemicals to food processing confront growing pressure to reduce energy use and achieve net-zero emissions, the appeal of thermal system electrification is on the rise. MVR heat pumps offer clear efficiency and safety benefits, but the complexity of heat integration calls for detailed analysis in process design. Process simulation tools are needed to not only calculate system requirements but to optimize system configuration and control strategy to ensure that supply meets demand and maintain stable plant performance.