Behind the scenes of complex production systems, mechanical seals play an indispensable role. Without them, manufacturing processes come to a standstill, as uncontrolled leakage can put the entire plant safety at risk. The requirements for seals are diverse and demanding; they must not only withstand extreme temperatures, but also aggressive chemicals, high pressure, and mechanical stress. And as if that wasn‘t enough, the seals are often located in hard-to- that wasn‘t enough, the seals are often located in hard-to- reach places or hundreds of miles away from the nearest reach places or hundreds of miles away from the nearest service team.
Operators of modern production facilities therefore rely on highly developed sealing systems that reliably fulfil their function. Thanks to intelligent design technology and innovative materials, seals can do even more today: they optimise energy consumption and therefore conserve resources. Research and development are not only aimed at making seals even more economical and resistant in the future. It is also about extending the life cycle of sealing solution, especially in process-critical areas.
Intervening in time to increase service life
Digitisation provides development teams with the tools to do just that. For example, the seal manufacturer EagleBurgmann (EB), which is part of the Freudenberg Group, has launched „EB Smart Product®“, a digital monitoring solution that helps customers to continuously monitor their sealing systems and ensure optimal operating conditions. “The idea behind this is to detect changes in the mechanical seal, the supply system, or the entire machine at an early stage to prevent consequential damage and increase the service life of these systems,“ explains Dr. Max Botz, Development Engineer IoT Sensors at EagleBurgmann. „In many cases, EB Smart Product® can help customers to avoid costly and time-consuming repairs associated with valuable resources and production losses by making minor adjustments or performing targeted maintenance work.“
Condition monitoring is the technical term that describes permanently monitoring parameters of a machine to assess its condition. The basis for this is in our case the battery-powered EB Smart Seal® sensors, which collect measurement data such as pressure, temperature or vibrations remotely. In con- trast to conventional measurement technology, these sensors are attached directly to the barrier system at the seal inlet and outlet and therefore deliver accurate results – without any cables, because the measurement data is transmitted wirelessly to the cloud. The low installation and operating effort compared to wired systems are also reflected in lower costs. Even more informative measurement data can be collected by sensors that are installed directly inside the seal, such as in the EB Smart Seal®. This sealing solution already has integrated sensors, that enable monitoring of the sliding parts temperatures. Many EB Smart Seal® applications are already in use with customers around the World, sending data wirelessly via a protected communication protocol to a gateway, and from there to the secure „myEagleBurgmann“ cloud. Here, the data is continuously monitored and analysed not only by the customer, but also by EagleBurgmann. If a parameter exceeds a predefined limit, an alarm is triggered, and the customer is immediately notified. For example, temperature or pressure get too high or too low. As a result, consequential damage, or expensive repairs with the associated use of materials and resources can be avoided. In the worst-case scenario, devastating effects on the environment and safety are prevented.
Solution pays off
The value of using this smart solution is demonstrated by the case of long-time EagleBurgmann customer, Leuna Carboxylation Plant GmbH (LCP). Since September 2022, this was the first German pilot project to have several EB Smart Seal Sensors in operation on a paddle dryer. „Our goal was to protect the high-quality assembly of this process-critical system and to guarantee safe operation for as long as possible,“ explains Robert Tulaszewski, Operations Engineer at LCP. „The EagleBurgmann solution was perfectly suited for our variable batch processes, as the regular basic fluctuations such as temperature and vibration can be taken into account.“ About a year later, the company would learn that this investment would pay off. Within just a few hours, the temperature in the dryer‘s supply system rose to unusually high levels. The heat gene- rated by the friction in the seal could not be dissipated as planned, and quickly spread to all parts of the system and threatened to overheat the entire system – with potentially serious consequen- ces. „When the alarm came in, it quickly became clear to us that immediate action had to be taken,“ says Christian Ihrke, Head of Service Center Halle/Leipzig at EagleBurgmann and long-time service contact for LCP. In addition to the automatically generated e-mail alert in such situations, the experts at EagleBurgmann picked up the phone to inform the customer personally. „This allowed us to intervene immediately, quickly fix the problem with our cooling system even without a hard shutdown, and start the next batch without interruption,“ Tulaszewski continues. In this way, EB Smart Product® prevented damage that would have quickly added up to a six-figure loss with repairs and production downtime.
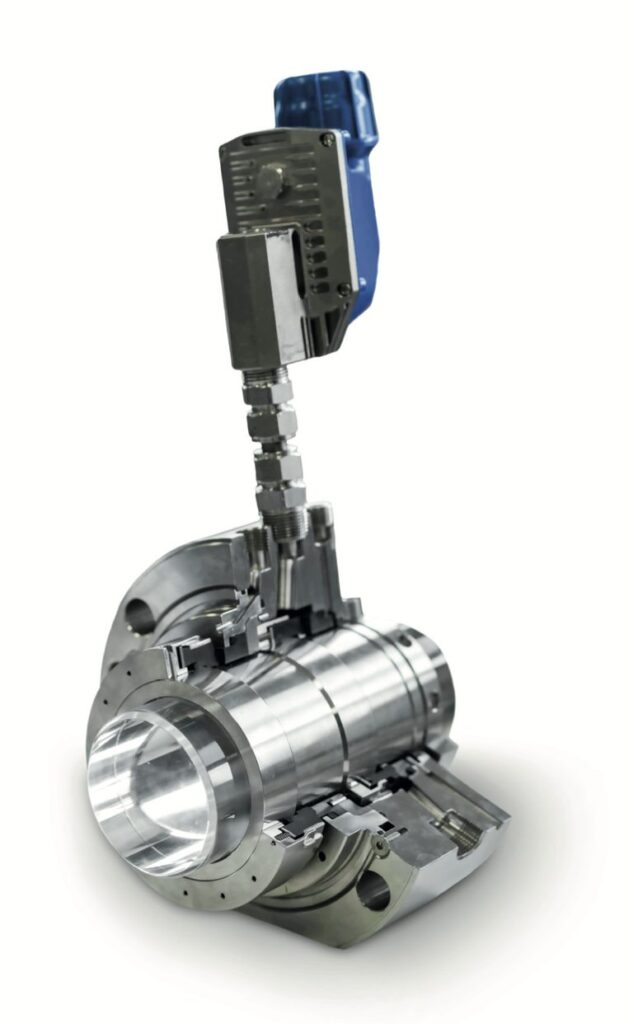
Predictive Maintenance Reduces Footprint
For the Wolfratshausen-based sealing spe- cialist, the cloud-based product is another important contribution to improving the ecological footprint of its customers. „Of course, we are continuously working to save resources and reduce our own environmental impact as a company. At the same time, we want to use innovative materials, technologies and digital solutions to help our customers reduce emissions and the use of resources,“ says Daniel Goebel, Sales Director Aftermarket for Compressor Solutions EMEA at Eagle- Burgmann, making it clear that even with such inconspicuous components as seals, there is still a lot that can be done. „Our vision is pre- dictive maintenance,“ Goebel continues. „We want to further expand our EB Smart Product® service and evaluate the collected data in an even more targeted manner. In the future, we would not only be able to intervene in the event of problems, but would be able to take action beforehand and, for example, make preventive maintenance recommendations. This would increase the service life of seals even further.“
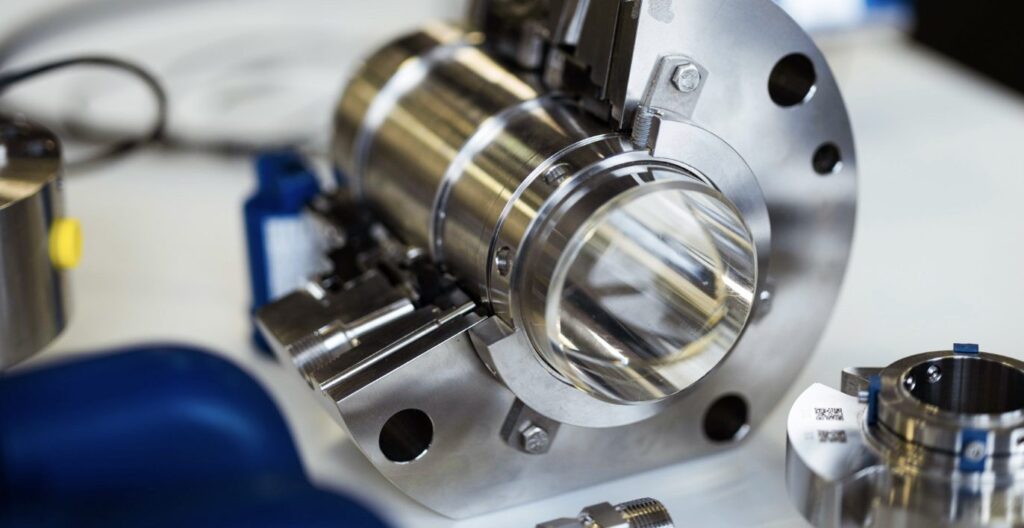