But what happens when traditional sealing materials fail? And what can be done to ensure the reliability of sealing materials for critical valves – such as those used in chemical processing and heavy duty industrial applications – where seal failure has a clear impact on consumer and operator safety?
In the development of an innovative sealing material which can handle the demands of high temperature process and control valves, the team at Precision Polymer Engineering (PPE) have had to consider not only the thermal properties of the material, but also its chemical compatibility, mechanical strength, and the legal compliances required to be specified into certain industries – such as food and pharmaceutical production and processing.
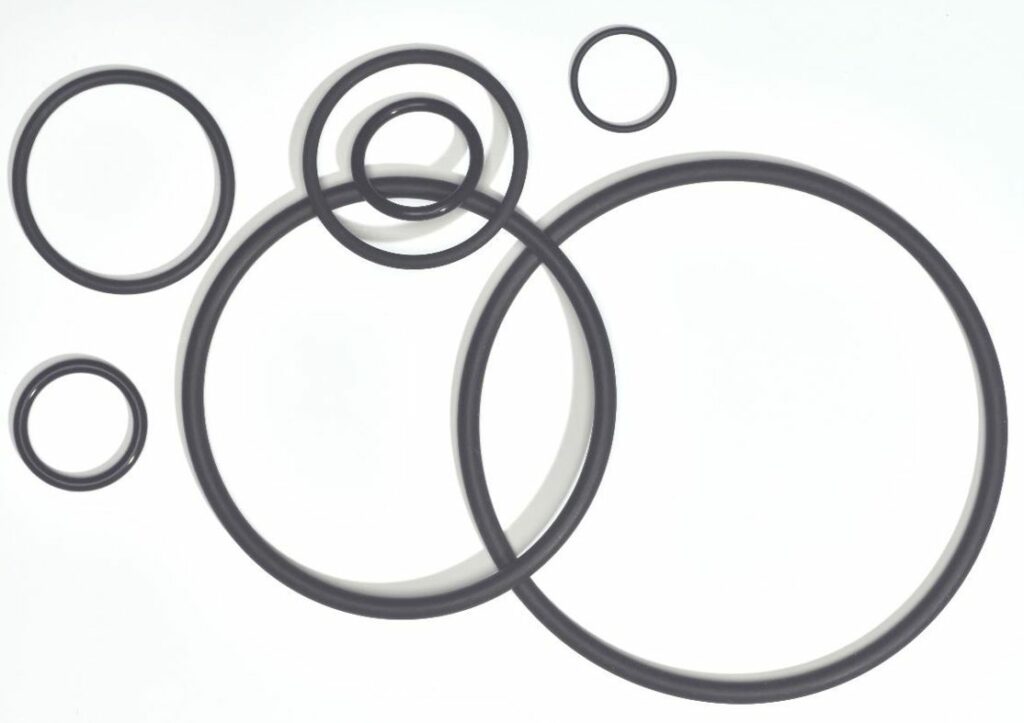
In the development of an innovative sealing material which can handle the demands of high temperature process and control valves, the team at Precision Polymer Engineering (PPE) have had to consider not only the thermal properties of the material, but also its chemical compatibility, mechanical strength, and the legal compliances required to be specified into certain industries – such as food and pharmaceutical production and processing.
The result was Perlast® G77X – a class-leading high temperature FFKM sealing material engineered specifically for long term performance and durability when failure is not an option.
The challenges of sealing for process control valves
One of the key considerations when designing sealing solutions for valves in high temperature applications or aggressive chemistries is an appreciation that there is never a one size fits all solution. For every valve type and material construction, and every temperature and pressure variable, there may be a different material type with the properties to provide an optimal sealing solution.
A central concern is the nature of the media to be transferred through the valve. Hydrocarbons, acids, and amines all place their own demands on elastomer seals, and a seal which works well for one fluid may result in critical seal failure for another. A specialist sealing engineer can advise on the suitability of a range of nitriles, silicones or fluorinated compounds, and give accurate assessments on performance and reliability expectations under a range of operating temperatures – from cryogenics to steam, and beyond. However, for peak sealing performance and long-term reliability, perfluoroelastomer (FFKM) materials are second to none.
Perlast® is PPE’s own brand of FFKM materials, the ultimate perfluoroelastomers where chemical resistance and high temperature performance are critical. The most advanced of these Perlast® grades for high temperature valves is Perlast® G77X – but what sets it apart from the competition?
What makes Perlast® G77X special?
Perlast® G77X is class-leading in high temperature capability, with long term performance and durability in temperatures up to a maximum of 350°C. Continuous temperature performance is also outstanding, with compression set testing at 330°C for 24h and 72h – better than many other key competitor materials in this space.

Other prominent features of Perlast® G77X are:
- Excellent response to temperature cycling effects
- Exceptionally low compression set over extended periods
- Excellent seal force retention properties
- Excellent mechanical properties
- Good chemical resistance
Upgrading to Perlast® G77X can have several advantages to a valve operator. There is marked improvement to sealing performance in high temperature applications, across a wide range of chemistries. Other benefits include:
- Extended maintenance intervals, or MTBR (Mean Time Between Repair)
- Increased safety margins
- Reduced cost of ownership
- More reliable performance in temperature cycling applications
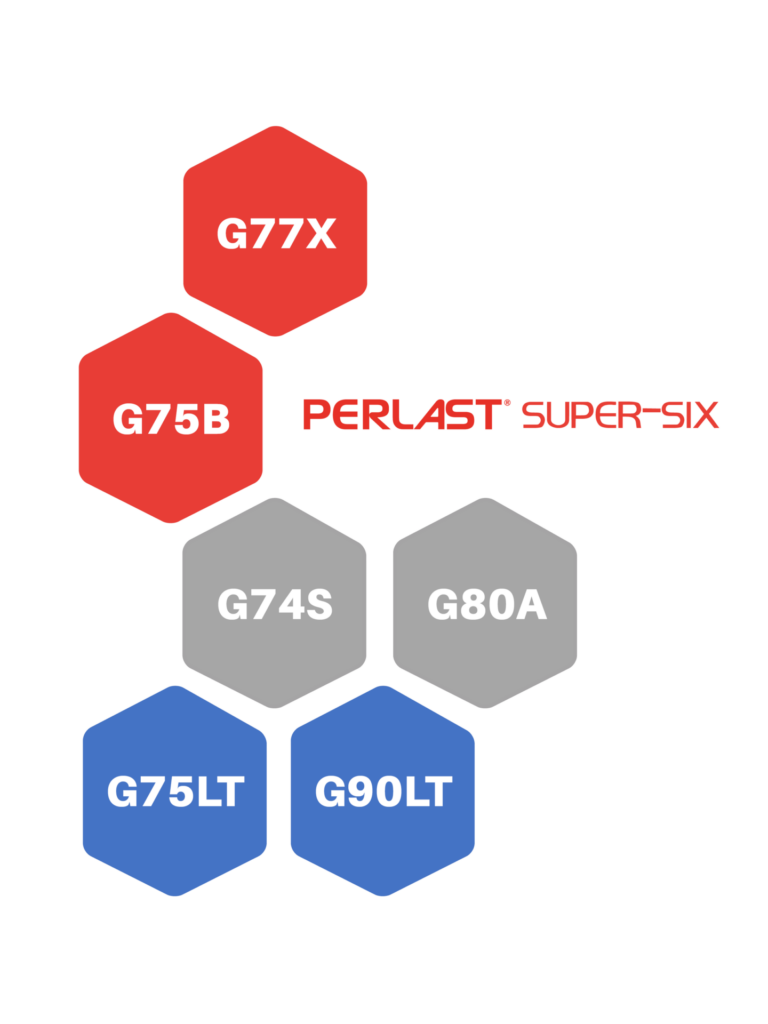
Perlast® FFKM – a material family when performance matters most
The development of Perlast® G77X brings the total number of Perlast® perfluoroelastomers for the most critical applications to six. It means that PPE can now offer a high performance sealing option for extreme high and low temperature valve applications, all kinds of chemically aggressive operating environments, as well as process valves involving food contact.
Find your nearest specialist sealing engineer at www.prepol.com, to discuss which of PPE’s full range of elastomer sealing materials represent the best fit for your network of process control valves, or to discuss optimising performance, reducing lifetime cost of ownership, or improving safety at your operations.