Summary
Sanwei New Materials Co., Ltd in China produces butanediol (BDO), a raw material used for producing biodegradable plastics. The production of BDO by the Reppe process involves two steps:
- Formaldehyde and acetylene react in the presence of a copper-based catalyst to produce 2-butyne-1,4-diol (BYD).
- BYD is further hydrogenated to BDO.
Controlling the hydrogen gas flow rate is critical throughout the entire reaction process, as it determines the efficiency of the reaction as well as ensuring BDO stays within its specifications.
There are several high-pressure hydrogen gas lines at the site with the following specifications.
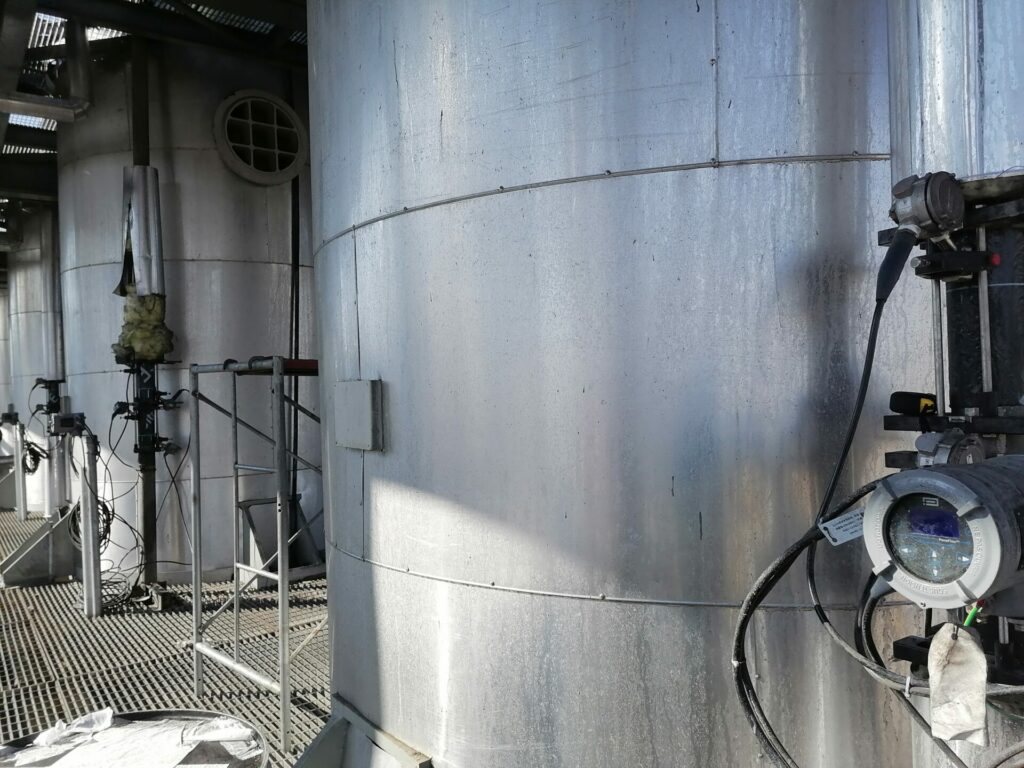
Specifications
- Fluid: Hydrogen gas
- Pipe sizes: DN80 and DN100 (3” and 4”) with wall thickness of 20mm (0.79”)
- Pipe material: carbon steel
- Process temperature: 60°C (140°F)
- Pressure: 30 MPa (4351 psig)
- Density: ~ 19 kg/m³ (1.186 lb/ft³)
- Sound speed: 1430 to 1500 m/s (4691 to 4921 ft/s)
- Flow velocity: 4.5 to 6.5 m/s (14.7 to 21.3 ft/s)
Challenges
Traditionally, the customer used orifice plate type flow meters for measuring hydrogen gas. To maintain an accurate measurement, the differential pressure cells had to be calibrated regularly requiring process interruptions, which affected production yield and generated serious safety risks given the high process pressure and the low inflammability limit of hydrogen. The measurement of high-pressure hydrogen gas had always been a major challenge for the customer and so the team wanted to look at safer, more reliable and drift-free alternatives.
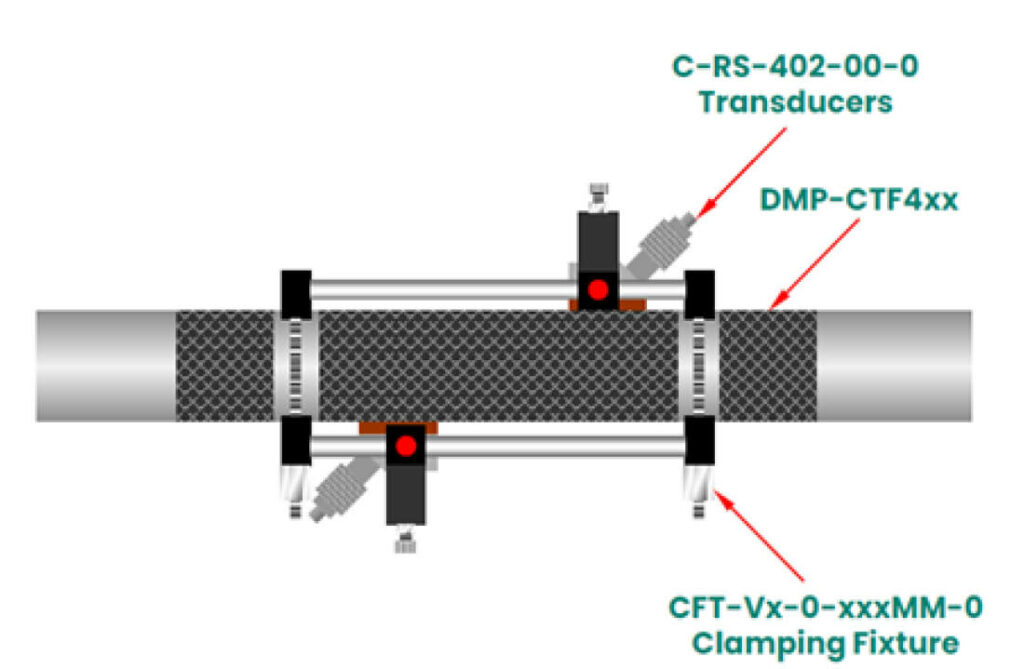
Triple-traverse installation
Solution
Ultrasonic flow meters have been used to provide hydrogen gas measurement for close to 30 years. However, clamp on solutions are not typically adopted for this type of application, especially at extreme pressures. Why? The sound speed of hydrogen gas is close to that of water with a low density. At a pressure of 30 MPa, the density of hydrogen at 60°C is about 19 kg/m3. Therefore, typical clamp-on gas transducers are not suitable when using such thick pipe walls.
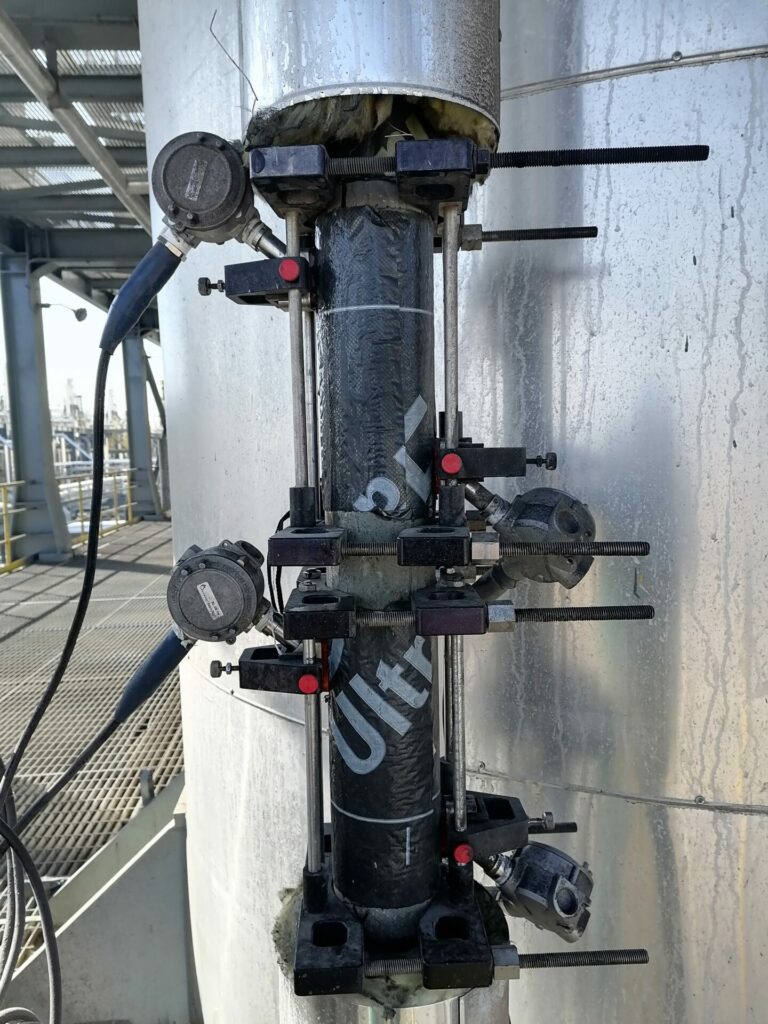
Clamp on Benefits
- Safe as it is contactless
- Low maintenance
- Easy installation with no process interruption
- No pressure drop
- Long term stability and drift free performance
However, the Panametrics team tested 200 kHz, 500 kHz, and 1 MHz transducers, and concluded that the C-RS-402 at 1 MHz frequency was an effective solution that would provide the customer with accurate and reliable results. Damping material before and after the clamping fixture was applied and the installation surface of the sensor was polished to improve signal quality.
A triple-traverse installation was implemented and the Panametrics XMT1000LC clamp-on flow meter was programmed for high voltage. Finally, the SNR increased to around 5:1, and up to 8:1. With the flow meter readings stable, the DCS carried out process controls based on the data fed by the XMT1000LC solution.
Close collaboration between the Panametrics technology team and its local Services team brought about the successful solution to the customer’s hydrogen gas application. Sanwei new materials is now benefiting from more accurate and reliable measurements which is enabling improved safety performance and better productivity.
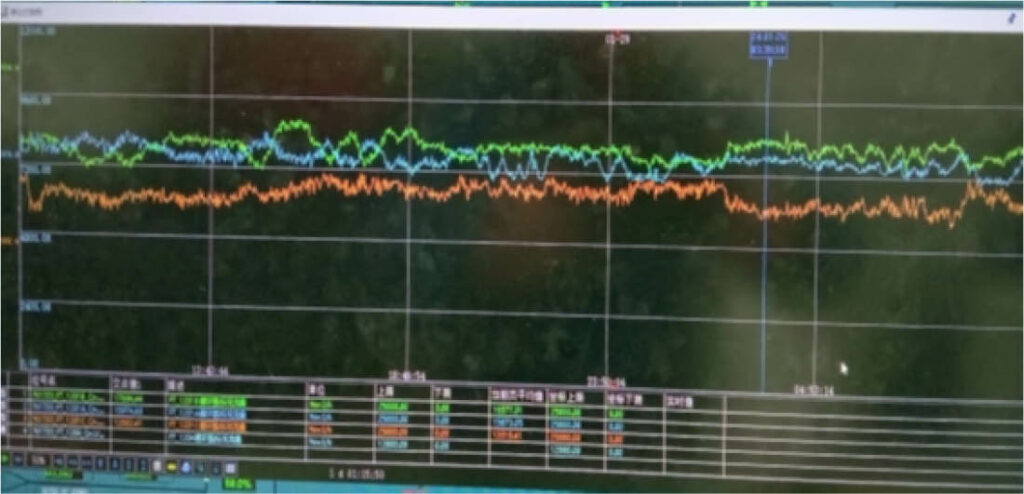