What are the main challenges and how to optimize the flow control in your process by using real-time pressure and temperature compensation?
Temperature fluctuations and variations in line-pressure are two major external factors that can influence accurate, repeatable and stable gas flow in a process. Pressure variations may for instance be caused by the reduction of pressure in a gas cylinder or by cross talk between multiple flow controllers.
Cross talk typically occurs when multiple mass flow controllers are positioned in close proximity using the same source of gas supply, or when they are installed upon the same rail or frame. The line-pressure from a gas regulator is affected by the flow demand of the flow controllers. When the flow instrument is changing its setpoint, it will affect the line-pressure. Due to this pressure change, the flow measuring section in a conventional mass flow controller (MFC) is affected, indicating an incorrect flow measuring signal that does not correspond with the actual flow through the MFC. The smaller the nominal flow of a flow controller, the bigger the effect will be to a setpoint change of a larger, parallel installed MFC.
Static pressure compensation is the compensation for slow pressure changes, for example the gradual reduction of pressure from a gas cylinder. By integrating a pressure transmitter to the mass flow controller, together with an on-board conversion algorithm, real-time calculation of the actual fluid properties can be performed. For semi-caloric measurement, the density, viscosity, thermal conductivity and heat capacity are used in the calculation. Under influence of pressure and temperature, these properties change. Thus, actual temperature and pressure are measured and processed, resulting in accurate flow measurement and control stability.
Dynamic pressure compensation is the compensation for rapid pressure changes. This can occur when an MFC for a higher flow at the same gas supply line changes setpoint. This may cause the ‘cross talk’ effect as described above. The moment that these rapid pressure changes are identified by the pressure sensor, the valve control will be adjusted accordingly so that the flow remains stable.
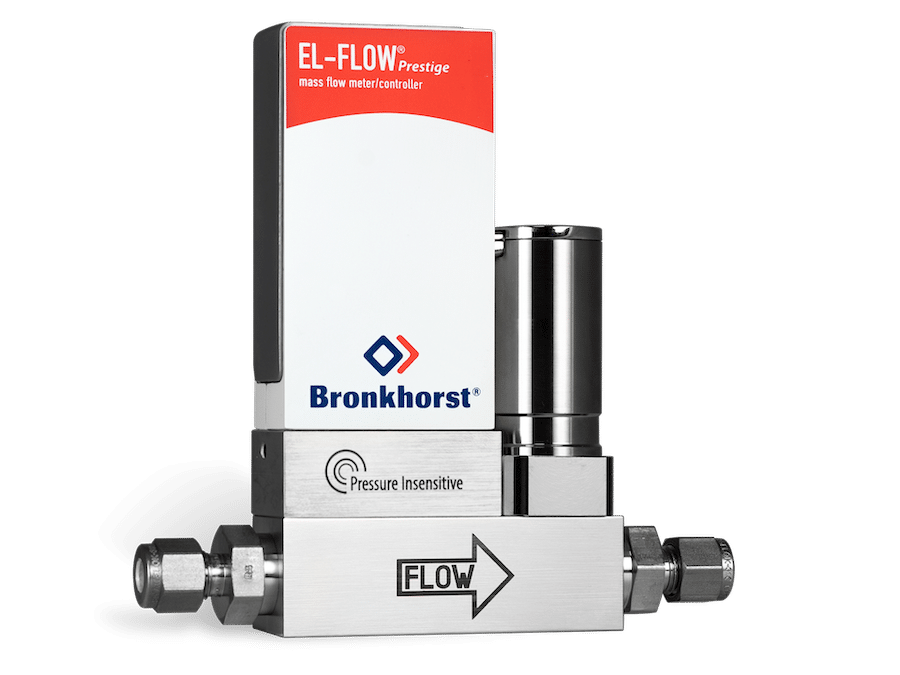
The solution for variations in process conditions lies in real-time pressure and temperature compensation. Bronkhorst® EL-FLOW Prestige thermal mass flow controllers offer standard temperature compensation and can optionally be supplied with on-board pressure compensation. The actual measured temperature and pressure are used in the on-board conversion model, compensating for changes in the process conditions. This leads to a more reliable and more accurate conversion and also to an improved control stability.