By Geoff VanLeeuwen, P.E.
Introduction
Facility managers who rely on industrial pumps for the various liquid-transfer duties in their manufacturing processes can be excused if they occasionally think that once the pump has been purchased the majority of the heavy lifting has been completed. It is easy to see why this mindset might become prevalent. After all, identifying the right pump for the right process requires a lot of time and due diligence, from performance reviews to cost estimates, to even soliciting opinions from other manufacturers.
In reality, studies of different types of manufacturing operations have indicated that, when all is said and done, the purchase price of a pump will only be 10% to 15% of its total life-cycle cost, with “life-cycle cost” defined by The Hydraulic Institute as the “total lifetime cost to purchase, install, operate, maintain and dispose of the pump.”
Based on that definition, the reality is that cutting a check for the purchase price of the pump is only the first of many potential expenses that will be incurred over the pump’s operational lifetime, which – if the operator is fortunate – can be as long as 20 years or more. Hand in hand with that, pumps are said to account for between 20% and 25% of the energy usage in a manufacturing operation. Therefore, it is imperative that facility operators analyze their pre-buy research not only from an initial-cost perspective, but also from a total life-cycle cost viewpoint.
To do that, there are five cost factors to consider when attempting to arrive at a trustworthy figure for what a pump’s total life-cycle cost may be. Let’s take a closer look at all five:
1. Capital Cost
As mentioned, capital expenditure – or CAPEX – in the amount of money paid to actually purchase the pump is the first and most obvious life-cycle cost. But identifying and optimizing that CAPEX cost involves much more than comparing and contrasting price tags.
The first consideration should be identifying the pumping technology that best suits the needs of your liquid-transfer processes. Usually, this comes down to a choice between positive displacement (PD) and centrifugal-style pumps, with the type of technology that is ultimately chosen having huge implications regarding the total life-cycle cost of the pump.
In many instances, final pump selection can come down to an either/or choice:
- If a PD pump is chosen, will its operation require the use of a gear reducer or speed-reduction device? If it will, that is an added upfront cost that must be considered since centrifugal pumps do not need speed reducers.
- There have been a number of significant advances recently in the development of leak-free or seal-less pumps. These types of pumps, however, are generally more expensive than sealed pumps, but on the other hand, an inventory of replacement seals will not need to be purchased, stocked and tracked.
- Within the PD realm, air-operated double-diaphragm (AODD) pumps are a unique technology in that they do not need a traditional electric or fuel-powered motor to operate and have no couplings or seals that need to be maintained or replaced. The only daily operational cost is paying for a supply of air, but this means that the facility must be able to accommodate that capability. AODD pumps also do have a number of wear parts that will need to be monitored, including their diaphragms, balls and valve seats.
Particular to the chemical-manufacturing industry, over the years centrifugal pumps have become the default liquid-transfer technology in many of the world’s chemical-processing systems. Because of this, many chemical processors will always choose a centrifugal pump because they know how they operate, are familiar with their benefits and are confident they will get the job done, no questions asked.
The problem with this mindset is that it means that many chemical-processing systems have been designed around the needs of the pump, rather than the needs of the system. For example, design engineers will design their systems so that raw materials can be blended or heated in a way that their viscosity is brought to a level that enables them to be handled by a centrifugal pump. In this case, they are reconditioning the material to fit the need of the pump, regardless of any potential life-cycle cost impact.
The operator, in addition to getting the viscosity to a centrifugal-friendly level, must also ensure that the pump continues to operate at its Best Efficiency Point (BEP), generally believed to be a window in which the pump operates at 80% to 110% efficiency levels. Any time spent operating outside the BEP can result in shaft deflection that will place higher loads on the pump’s bearings and mechanical seal, which can damage the pump’s casing, impeller and back plate. This domino effect will lead to higher maintenance and part-replacement costs that – teamed with the costs required to actually keep the pump operating at its BEP – will increase total life-cycle costs.
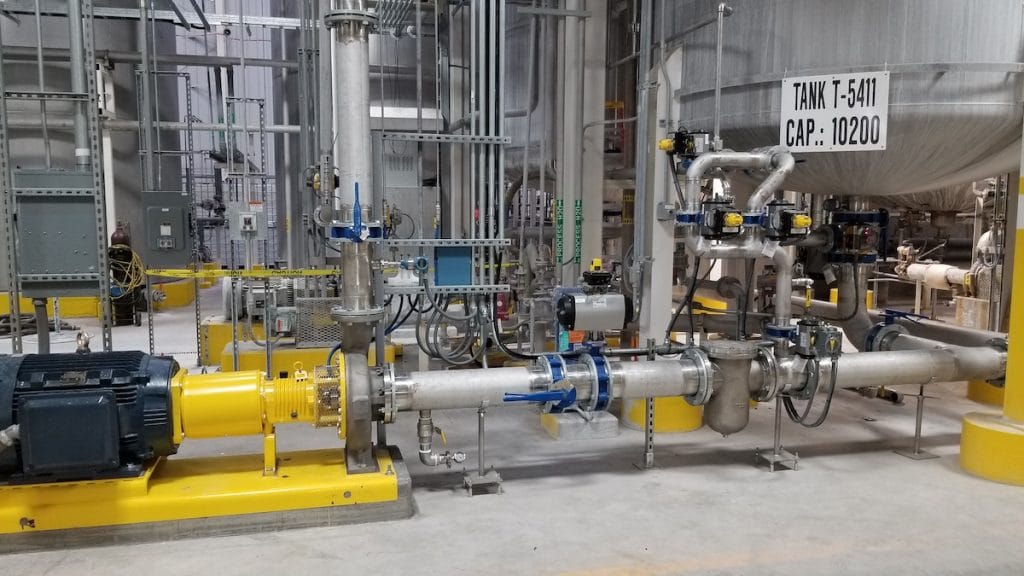
2. Installation Costs
Determining installation costs and their eventual effect on total life-cycle expenses requires a total overview of the pumping operation. Some questions to consider include:
- Will any modification to the pumping system be needed when the new pump is introduced or can it just be plugged into the existing infrastructure?
- Will new or modified connections to the process piping, electrical wiring and instrumentation, and auxiliary systems and utilities be needed?
- Are there any special weight considerations that could lead to the need for a special foundational platform, i.e. a baseplate?
- Will any boring into the existing foundation, or the pouring of a new foundation, be required?
This last question is the one that can have the biggest effect on total life-cycle costs. Some pump technologies are easy to install; for instance, AODD pumps that need only an air and discharge hose to be hooked to them before they are asked to do their jobs, even if that job demands that the pump operate underwater.
Vertical pumps, on the other hand, are typically less expensive than some other styles, but they sometimes need extensive foundation work that could require boring as much as 30 feet (10 meters) into the ground just to install the pump. Again, this can prompt the facility operator to employ some comparative if/then thinking: “If I want to use a more economical vertical pump, then it will cost quite a bit in installation costs.” By taking that into consideration and reviewing all of the possible alternatives, that if/then statement can be turned into: “If I use a more expensive multi-phase pump, then I will have lower installation costs.”
Another area of consideration during pump installation is alignment. Simply put, pumps that are not aligned properly with the motor – and many often aren’t – can lead to quicker part wear that can result in inefficient operation and pump failure. There are now some pump technologies that can be pre-aligned as they are manufactured through the use of an adapter, which eliminates the need to align the pump on-site, along with any costs associated with that alignment process.
A final expense within the installation-cost realm is commissioning costs. These are the fees that must be paid to have the installation reviewed to ensure that it satisfies all of the parameters for proper installation and safe operation. Only after this review has been performed and sign-off received will the facility manager be able to flip the switch and begin operating the pump.
In the end, it all comes down to each individual facility’s needs, wants and economic considerations, with all of the spokes in the installation-cost wheel playing a part in determining total life-cycle costs.
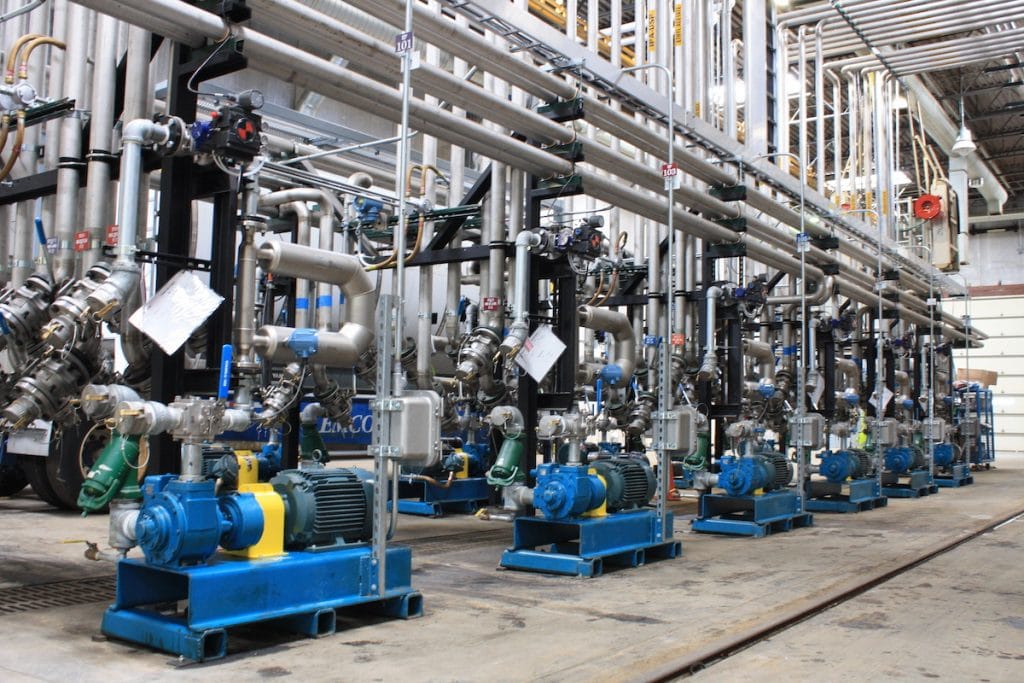
3. Operating Costs
The most obvious cost here is acquiring the energy – generally electricity, fuel or air – that is needed to power the pump. Here again, the style and operational capabilities of the pump technology play a notable role. For example, when contemplating a pump that operates via a motor that is 50 horsepower or lower, energy efficiency should not be a top-of-mind consideration for the operator. However, energy efficiency becomes a critical concern when the motor is 100 horsepower or larger, especially when those heavy-duty motors are featured on pumps that perform continuous-duty pumping operations.
Again, a comparison between PD and centrifugal-style pumps is in order:
- Typically, a PD pump motor is sized according to the bypass valve set point. This optimizes the motor sizing so that it is close to the actual operating points and limits the energy consumed while still enabling it to achieve desired flow rates regardless of temperature, pressure or viscosity changes during the pumping process.
- Centrifugal pumps, on the other hand, are often not protected with bypass valves. Instead, centrifugal pump motors are sized according to the runout power. This essentially oversizes the motor “just in case” the pump operates at runout. In reality, most centrifugal pumps don’t operate at runout, meaning that the cost for a larger motor is often a needless expense.
Another cost to focus on when considering life-cycle operating expenses is the cost of any ancillary liquids needed to heat, cool or lubricate the pump during its operation. For instance, sealed pumps can require a water “quench,” a process in which tap water is injected into the seal gland as a way to cool and clean the seal faces. This water is usually introduced into the pump at very low volumes, sometimes even lower than a dripping water faucet, but if 10 pumps require this treatment and they operate for 8,000 hours a year each, the costs for that water can quickly escalate. This expense is not needed with seal-less pumps.
Operating costs also contain a human element in the form of labor costs. These costs can fluctuate widely depending on the complexity of the pumping system itself. A system that regularly handles hazardous or explosive materials requires closer monitoring than one that only transfers benign materials. Though there has been growth in next-generation remote Cloud-based pump-monitoring systems and equipment in recent years, most manufacturing facilities still rely on first-hand on-site observation of the pumps to determine if they are meeting the parameters of any and all required performance indicators.
4. Maintenance Costs
Unanticipated downtime and lost production play a huge role in the pump’s total life-cycle cost. In other words, a pump that is down for maintenance is not moving liquid, which means the line is not producing product. While all maintenance is bound to take the pump out of service for some period of time, there are some pump technologies, such as sliding vane, that allow simple maintenance duties to be performed without having to remove the pump from the line. This will shorten the amount of time that the pump needs to be out of service. All of these things make it imperative to understand a pump’s anticipated maintenance needs before it is purchased.
The ultimate impact of maintenance costs is usually tied to the number of wear parts that the pump possesses. Pump technologies like centrifugal, sliding vane and AODD have relatively few wear parts – things like seals, vanes, O-rings and diaphragms – that are easy to replace at low cost. These part-replacement costs usually total less than 20% of the cost of a new pump over its lifetime.
On the other hand, technologies like progressive cavity, screw and internal gear pumps can feature maintenance, repair and replacement costs that can approach or exceed 80% to 90% of the pump’s CAPEX cost. These types of pumps operate via highly precisioned machined metallic components that are expensive to produce. That’s why these types of pumps are often called “throwaway” pumps; they are used until they break down and then replaced because replacement is more economical than repair.
Another component of maintenance costs is preventative maintenance. This is critical if the operator hopes to reduce or eliminate unanticipated downtime in any pumping processes. Because each pump application is unique, pumps can seem fickle at times. While the operator can determine a desired target life for the pump, the reality is that, if left unchecked, unexpected failures will cause costly pump downtime.
A preventative-maintenance plan can combat this – if the plan is properly considered and makes use of the past operational history of similar pumps used in similar applications. Making well-considered assumptions regarding pump maintenance based on past history can go a long way in building a maintenance plan that can anticipate and mitigate any problems before they occur. This is another area where the recent advances in remote monitoring and data storage of a pump’s operational history can help ease the burden on preventative maintenance. Some manufacturers are now offering phone apps to help track, monitor, operate and keep notes on the maintenance needs of their installed assets.
One final maintenance-related consideration for the operator is to determine whether or not it would be economically wise to purchase a spare pump that can be inserted into the pumping system on an as-needed basis. Determining the necessity of this CAPEX expense will also play into the calculations for total life-cycle-costs.
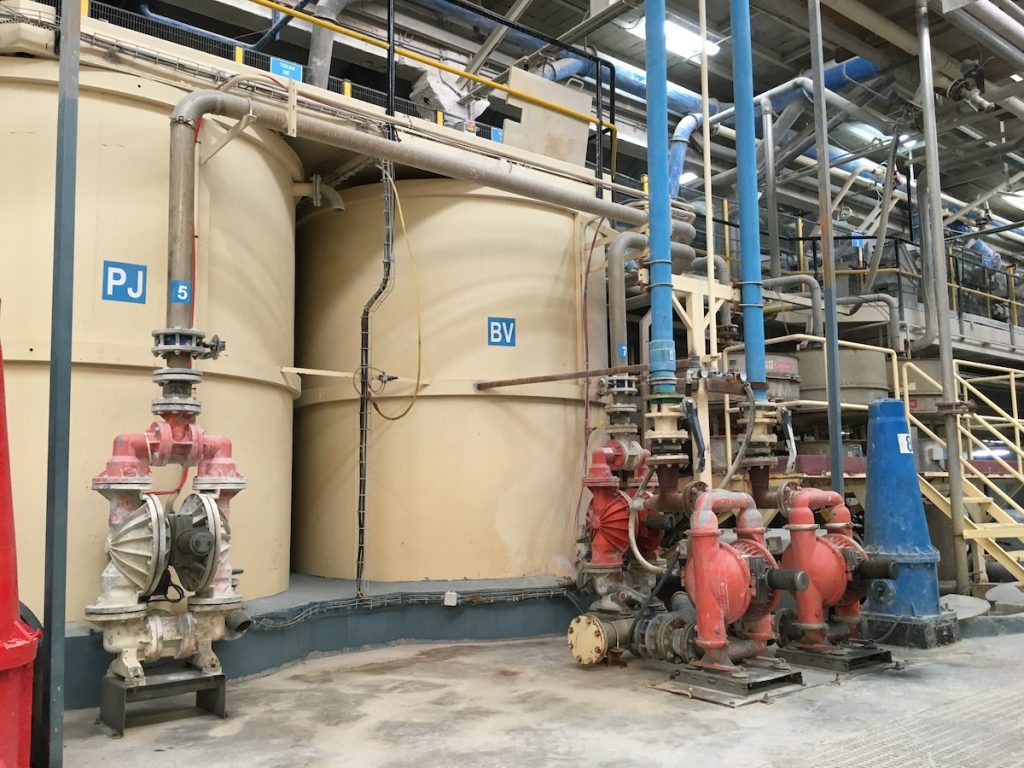
5. Decommissioning Costs
The final cost in a pump’s lifetime is its decommissioning cost, or the cost to remove it from operation and dispose of it. While these costs are typically not prohibitive, if the pump has been used in the handling of hazardous, toxic, radioactive or any other materials that require environmental sensitivity the costs to decommission them will be higher. When disposing of pumps that have handled hazardous materials, the number and type of regulatory requirements that must be satisfied will also play a role in determining the decommissioning costs and their ultimate effect on total life-cycle costs.
What Have We Learned?
When any type of list like this is created, an expected question might be: “So, which of these costs is most important if you want to optimize total life-cycle cost?” Let’s look at them from least to most significant.
The one category that generally has a fixed cost that is least open to fluctuation or interpretation is decommissioning costs. Many operators may not even consider those costs as part of the total life-cycle cost package.
After that, we’ve found that CAPEX and operational costs (as they relate to energy usage and pump efficiency) are not seen as a make or break proposition for the pump user. While it’s popular to market industrial operations as “green” or environmentally friendly, the truth is that no one makes a purchasing decision based on the pump’s efficiency – and there really is no compelling reason to do so because the economics of operational efficiency don’t really matter for pumps that have motors smaller than 100 horsepower, and that’s where most industrial pumps operate.
Maintenance costs are important because pump reliability is a key component in ensuring that the pumping system meets the demands of the operation. However, the costs of maintenance are usually built into operating budgets through the purchase of spare inventory or the performance of prescheduled maintenance routines, making this a life-cycle expense that can usually be predicted pretty reliably.
That leaves installation cost, which may be the least understood of all of the categories. This also means that it offers the best opportunity for improvement. Most operators ignore or care little about installation costs, viewing them as nothing more than the “cost of doing business.” However, this is an area that is ripe for improved optimization, especially in new installations. Many operators can fall into the trap of relying too heavily on what has been done previously on-site or what has been done in other company facilities, without truly realizing how unique each individual installation really is.
This can lead to a situation where it is hard to know what the true costs of the installation are and their ramifications regarding total life-cycle cost. These installation costs include not only foundation work, piping, etc., but also any auxiliary systems that will need to be made part of the pumping operation. These can include priming, liquid conditioning, heating, closed-cooling, filtration, vacuum and pigging systems, some of which can be exorbitantly expensive to install.
Conversely, rather than considering the need and cost of auxiliary systems, some operators will fall back on the mindset that all problems can be solved through the incorporation of a control valve or variable frequency drive (VFD). Control valves are useful to modulate the level of pressure that is needed to get the pump working properly – another example of building the system around the pump – but a more economical solution can be buying a pump that can inherently produce the application’s required pumping pressure.
VFDs have become more affordable over the years, so some operators have begun to think that they can be a silver-bullet solution to everything that ails pump operation. While VFDs do offer a lot of functionality and flexibility and can make the system very nimble, they can wreak havoc on motors by introducing electronic pulses that will compromise the performance and reliability of the motor and other downstream pump components. Further, speed control itself is not a fix-all solution. A VFD will not help if a system’s operating range is outside a pump’s performance envelope.
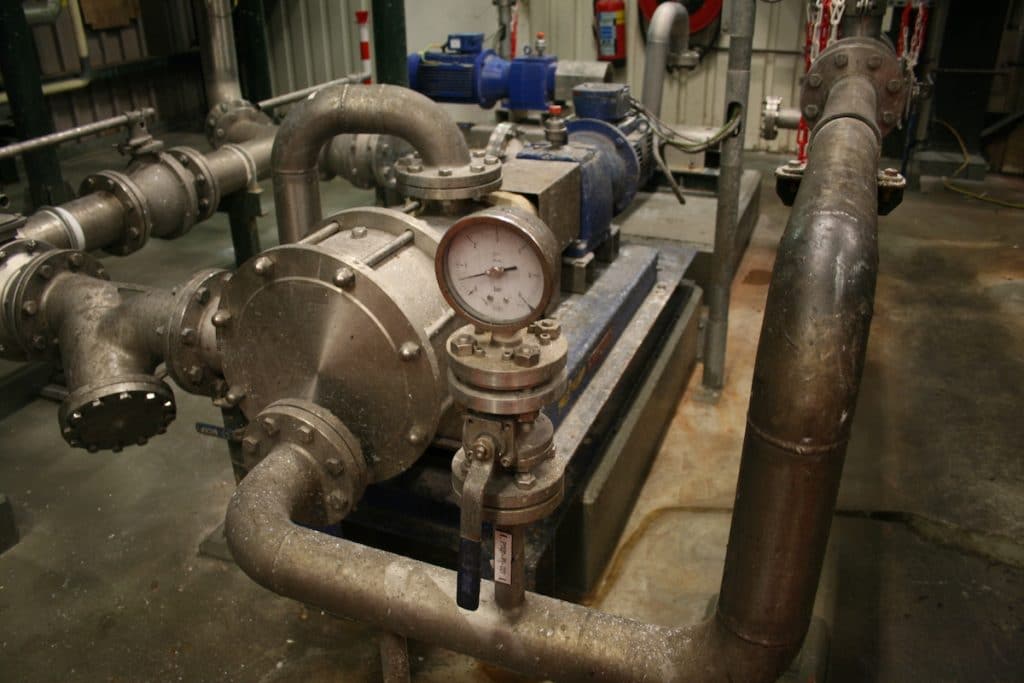
Where Do We Go From Here?
People in the process industries are knowledgeable, but because of the demands of their jobs they need a path of least resistance that accommodates the time, resource and production constraints that are placed on today’s plant operators. The simple fact is that somehow, someway today’s industry expects to achieve more output with less resources, which includes actually knowing all of the intricacies of an effectively functioning process system.
This has led more and more facility managers to turn to third-party Engineering, Procurement and Construction (EPC) contractors for assistance. EPCs are tasked with all design, procurement and construction tasks while ensuring that the entire project is completed on time and on budget. The use of EPCs has become more and more prevalent in recent years, to the point that hiring an EPC is now essentially considered an unavoidable first step when designing, outfitting and commissioning a manufacturing plant. And EPCs can be a valuable resource – if they have the knowledge and expertise to know the ins and outs of the operation they are building and are able to answer any questions their clients may have so they can truly meet their needs. However, some EPCs prioritize short-term guarantee periods and ignore long-term life-cycle costs. Additionally, EPCs don’t pursue system optimization. Instead, they are incentivized to design and construct systems that meet only the minimum requirements that are outlined in their contracts.
As mentioned earlier, the arrival of advanced remote pump-monitoring technologies promises to be a boon in optimizing pump life-cycle costs. These new monitoring systems fill a niche in what has come to be known as the Industrial Internet of Things (IIoT). IIoT is defined as a network of physical devices, systems and platforms that use embedded communication technology to share the operational intelligence of industrial machines. It combines data technology and machine learning to bring together sensor data and machine-to-machine communication technologies. This enables the identification of operational inefficiencies sooner and more reliably, creating real-time operational transparency and significant cost savings for the operator.
The driver behind remote Cloud-based pump-monitoring systems is creating the ability to gather pump-performance data and store it for future use. These systems are nothing more than augmented ways to aggregate data. The challenge is finding the best ways to use this data to observe and predict pump performance, with the goal of optimizing it as it pertains to total life-cycle cost.
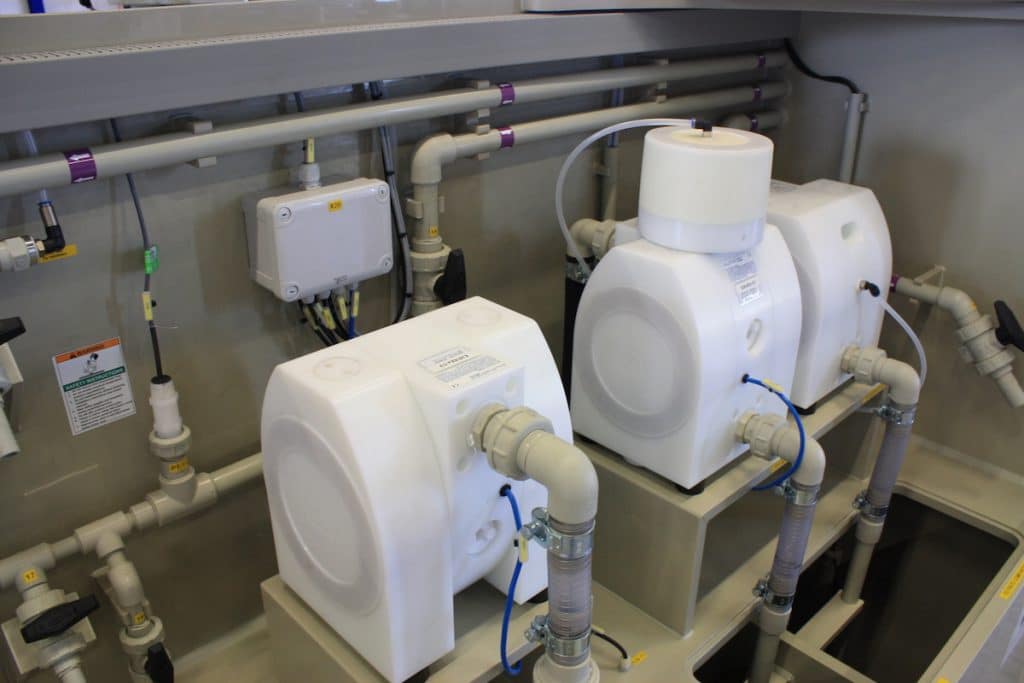
Conclusion
Many pump technologies are hundreds of years old and there really hasn’t been a new, significant way to move 10 gallons of water 10 feet in 10 seconds developed in a century. But there are still exciting ways to improve the total life-cycle costs – if the operators of manufacturing facilities will, as they say, stop “kicking the can down the road.” Granted, these time-strapped individuals do their best to create and operate manufacturing processes that meet the demands of strict and oftentimes unforgiving production schedules. That being said, by working in harmony with pump manufacturers who are constantly looking to improve the effectiveness and reliability of their products – as evidenced by the new remote monitoring tools – they can identify and incorporate pump technologies with optimized life-cycle costs that will reflect positively on the manufacturing operation’s ability to meet production demands and improve the bottom line.
About The Author
Geoff VanLeeuwen, P.E., is a Product Management Director for Blackmer® and PSG®. He can be reached at geoff.vanleeuwen@psgdover.com. For more information on the full line of Blackmer pumps and compressors, please call +1 (616) 241-1611 or visit blackmer.com. Blackmer, Grand Rapids, MI, USA, is a product brand of PSG®, a Dover company, Oakbrook Terrace, IL, USA. PSG is comprised of several leading pump brands, including Abaque™, All-Flo, Almatec®, Blackmer®, Ebsray®, em-tec, EnviroGear®, Griswold®, Hydro Systems, Mouvex®, Neptune™, Quattroflow™, RedScrew™ and Wilden®. You can find more information on PSG at psgdover.com.