Knowing which pump technology to use to ensure a safe, efficient process, but provide the flexibility for small scale batches, whilst undertaking refinements prior to commercialization can prove challenging.
Not only are you trying to ensure accurate, repeatable traceable results and avoid transferring fluids manually, but also ensure any technology selected will stand the test of time and make certain cross contamination does not skew results.
One of the ways North Ridge Pumps recently helped a client looking to scale production and perform trials was an innovator within the supplement industry.
They were looking to transfer one of several blends of chemicals which were highly viscous, would not flow under gravity and they wanted to consistently batch set amounts.
The Problem with High Viscosity Liquids
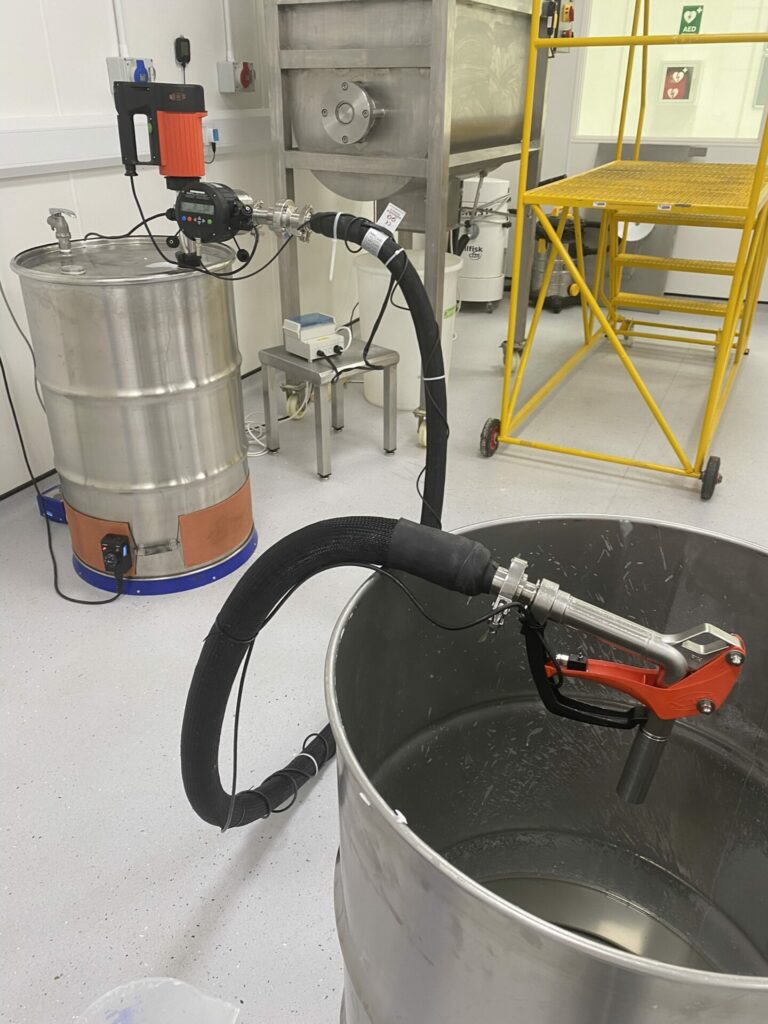
High Viscosity liquids often cause difficulty in transfer applications. They do not flow under gravity, require a specialist pump technology which if used can also pose issues if ran without fluid and be easily damaged.
Such fluids are sometimes so thick that when delivered in barrels or containers, if the incorrect pump technology is chosen, fluid is not pumped – holes are made with the pump within the container of fluid, rather than it being completely emptied, with large amounts of product remaining.
Not only is product within the centre of containers a cause for concern but also fluids which may remain stuck to the side of the container and the amount of wastage this can generate, in particular with more expensive fluids, or those which must be disposed of via waste collection. So when looking to scale production or conduct trials what factors should be considered?
5 Considerations When Scaling Production
- Sensitivity to Shear – Some fluids may be shear sensitive meaning they must be handled gently to avoid them being changed during transfer, or can become thicker when pumped.
- Solid Handling – When solids are transferred careful consideration needs to be given to the way they are handled. They can be transferred with technologies preserving their shape and consistency, or with designs which can assist with the next stage of production with solids broken down, or partially blended.
- Volatile & Corrosive liquids – Volatile and corrosive liquid handling is another consideration such as whether an ATEX design is required or seal less construction to ensure the full containment of fluids.
Other options include the swaging of hose fittings for the safety and security of leak free connections, nozzles for ease of fluid dispensing and speed control to alter dispensing rate and prevent splashing.
- Accuracy & Repeatability of Results – The ability to repeatedly batch preset amounts with ease, or record the amounts dispensed with high accuracy ensuring consistency.
- Accreditation – Material choice can be puzzling. Whether to adopt an accredited hygienic design, or simply a stainless steel design which can be easily disassembled and cleaned providing peace of mind during testing to simply what is chemically resistant.
High Viscosity Fluid Dispensing
In this project North Ridge were tasked with assisting a client dispensing a product being developed which had the consistency of molten fat.
When cold, the product would solidify making it unpumpable, and near on impossible to remove from the container.
The equipment needed to be hygienic, easily cleanable and handle a wide temperature range, yet consistently transfer differing volumes of liquid as accurately as possible.
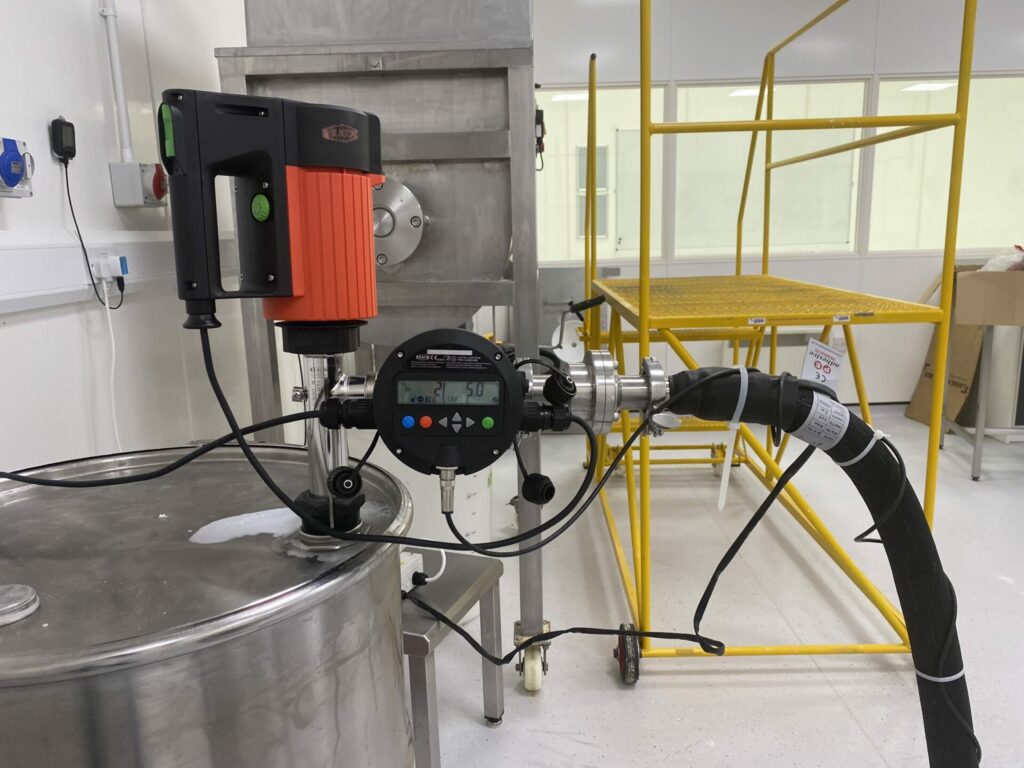
North Ridge supplied, commissioned and installed a complete automatic batching system to dispense the liquid accurately and repeatedly.
The unit was supplied complete with heat traced hose to ensure the liquid did not solidify in the hose, with the barrel also heat traced to ensure the contents remained liquid and pumpable. As the fluid was heated, it became easily pumpable enabling the client to trial new processes, test small scale batches and trial methods of packing.
Their results are accurate, repeatable & fully traceable enabling them to accelerate production and scaling.
One of the ways avoiding many of the pitfalls during commercialization of fluid process or fluid handling products is to work with a partner who can specify the right pump technology for your process.
With over 100 application case studies, we know how to get it right.
If you have a new process, method or application you are looking to undertake, contact us on 01773 302 600, email at sales@northridgepumps.com or visit www.northridgepumps.com to see how we can deliver the results you need.