They were looking for three new ATEX-rated pumps that would be used for the transfer and export of diesel within the new oil facility.
What’s the best pump for this type of application?
It’s important when handling fuels, chemicals or other volatile liquids that the right pump design is chosen to meet the requirements of the type of fluid and performance levels. When contractors are looking to transfer and export a fluid like diesel there’s a wide selection of pump technologies available.
Selecting the right pump is critical
If the fluid needs to be transferred at medium to high pressure, a positive displacement pump would be a good option. These pumps ensure that siphoning of fluid doesn’t take place and also provide a guarantee of duty point.
A pump’s operating point or duty point is where the pump’s capabilities and the pipework’s capabilities meet. This means that the pump will always operate at the point where the system and pump curves intersect. At this point, there’s a perfect balance between what the system needs and what the pump can deliver.
Another pump option is a long-coupled type of design. This gives a number of advantages including easy access so that the pump can be serviced in situ without disconnecting it from the pipework.
In this specific application for our Pacific region client, the required flow was high, but the pressure would be low at just 10m head. For this customer, a long-coupled centrifugal transfer pump would be a smart choice. It would deliver the high flow at the pressure required very cost-effectively, as the viscosity of diesel is very close to water.
The key design features of a long-coupled centrifugal transfer pump
Overall, a long-coupled pump design is very easy to maintain as the pump head can be accessed and worked on without having to remove the motor.
In addition, the centrifugal pump format has additional bearings installed in the pump head to share the operational workload. This makes it more robust and able to operate continuously as the extra bearings take a great deal of strain away from the motor during operation.
So, to summarise the key features of the design chosen were:
- Separate motor
As a separate standalone component, this can be replaced easily. In addition, the motor is available worldwide and almost certainly locally if there is an emergency
- Easy component replacement
If just the pump shaft needs replacing, this can be done simply without disconnection of the pump from the system, with the motor remaining in situ.
- Reduced motor strain
Separate bearings located on the pump head take on a large part of the workload, reducing stress and strain on the motor
- Longer lifespan
As well as the additional bearings in the pump head, separate shafts also help to spread the workload more evenly, extending the pump’s lifespan
- Better protection against fluid leaks
In a long-coupled design, the space between the pump and motor drastically reduces the chance of fluid getting in the motor if the seal fails
- Easy maintenance
The simple design gives quick access to the pump head for repairs or replacements without having to disconnect the motor first
Where are long-coupled centrifugal transfer pumps used?
They’re ideal for use in a vast range of applications in the industrial and marine markets. They are usually chosen for heavy duty industrial applications.
Typical applications include fuel export and transfer, agricultural irrigation, water treatment and supply, wastewater pumping with low solid content, energy plants, mining, firefighting, dewatering, building systems including high-rise building water supply, marine and cooling/heating conditioning (HVAC).
A tailor-made pump design
For this client in the Pacific, we selected three of our XHLE horizontal diesel transfer pumps. These are large heavy-duty units offering high flow and high-pressure capabilities.
They’re specifically designed to pump low viscosity clean or slightly contaminated fluids including fuels like diesel, petrol and kerosene, as well as sea water and fresh water. They also offer ATEX-rated versions which are modified for handling flammable fluids or operating in a hazardous environment.
The pumps were long-coupled and mounted on a baseplate fitted with a 7.5Kw IP56 1,200rpm ABB ATEX motor operating at 60Hz. Normally pumps can operate as high as 3,600rpm. However, these pumps will usually be working at one third speed, so they’re configured to give many years of service and need little to no maintenance.
In addition, the diesel transfer pumps were manufactured with a casing made from strong and durable ductile iron, with impellers and shafts formed from stainless steel AISI 316. The pump was painted in anti-static paint, with an anti-sparking brass coupling guard for additional safety.
Fully tested performance
The units were designed to deliver 2500L/min at 10m head. In accordance with ISO 9906:2012 Gr2B certification, we supplied the pumps after carrying out rigorous pump performance tests.
During the test, the pumps were rated for a maximum of five duty points which include the rated point, shut-off and three more points.
As the table below shows, an acceptance grade of 2B shows the variation in flow and pressure that would be required to confirm that the diesel transfer pumps would be acceptable. For grade 2B as shown this equates to + – 8% for flow and +- 5% for pressure.
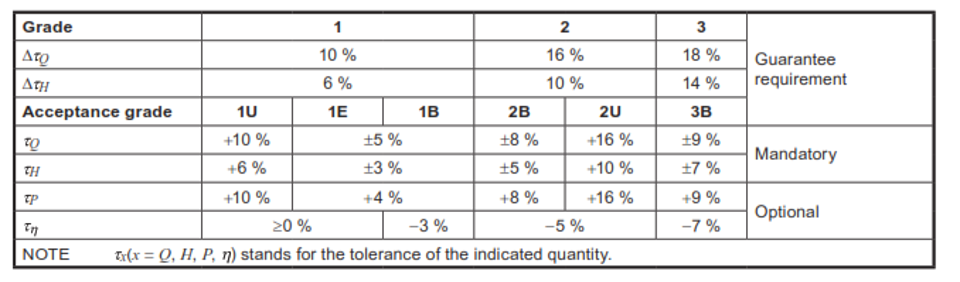
If you have a transfer application handling any kind of fluid and are unsure which pump is right for you, contact North Ridge Pumps now to see how we can help you.