The milk flow never stops. Every day, up to 1.3 million liters rush through the steel pipes of the Hochwald Foods GmbH dairy company in the small community of Thalfang in the Hunsrück region of Germany. The precious raw material from the member dairy farmers is processed into condensed milk and canned all around the clock. Every minute, 600 cans of the non-perishable, thickened milk come off the company’s four canning lines, among them well-known German brands such as Bärenmarke and Glücksklee. “In Thalfang, we turn raw milk into condensed milk for the global market with all in-house processes of canning, sterilizing, labeling, packaging, storing and loading into sea freight containers,” describes Holger Kuhn, Manager Electrical Engineering, the high level of vertical integration in the Thalfang factory. Hochwald Foods even has an own production of tin cans and lids.
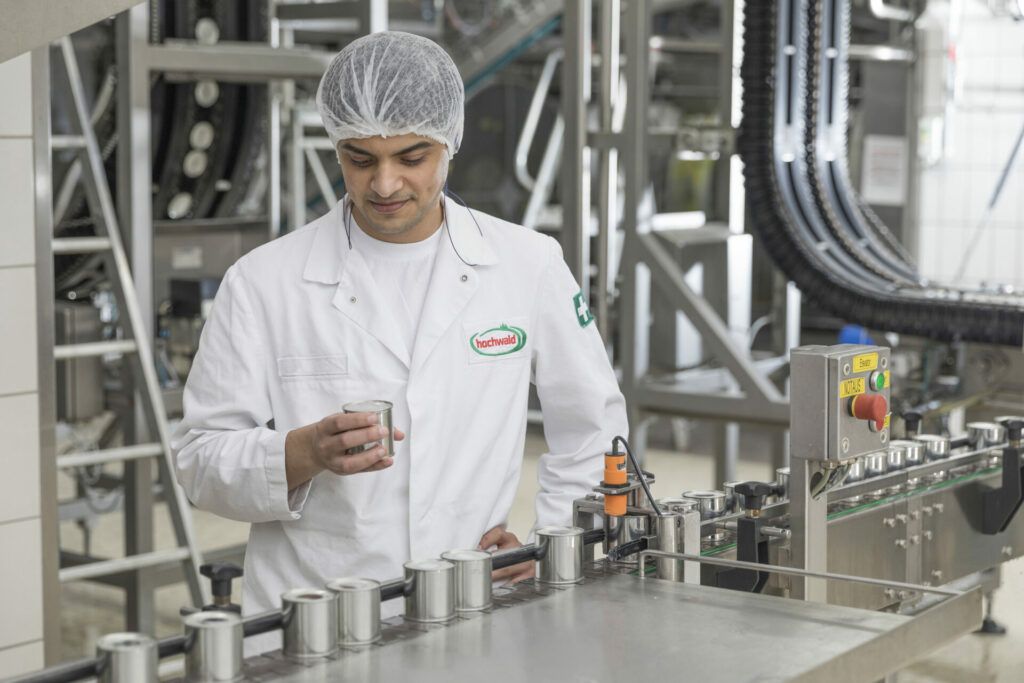
A major challenge in milk processing is the large number of deliveries and production batches due to increasing product diversity. “We process different qualities of milk and attach greatest importance to purity in origin and sorting ,” says Mr. Kuhn. The final stage in every delivery of raw milk by the company’s own milk tankers is cleaning. This means 30-40 CIP objects every day. The great number of production batches entails numerous cleaning cycles, since prior to processing any new batch, lines and tanks must be clean and hygienic. Right on the shop floor, Mr. Kuhn’s team runs 30-40 CIP cleaning cycles every day in order to prevent any standstill in milk processing. “No CIP cleaning means no canning,” he says, describing the central role of cleaning-in-place. This must not happen, he says, since constantly milk tankers are arriving at the yard, filling the raw milk silos which are as high as a house
Reliable conductivity measurement is required to make sure CIP cleaning does not block production. Conductivity measurements monitor the concentration of acids and alkalis for the maximum cleaning effect and will also detect when the pipe is flooded with pure again at the end of a CIP cycle. Conductivity sensors play a crucial role also in phase separation. They identify different media and allow for collecting used fluids to re-enter another cycle and this way play an important role in saving resources.
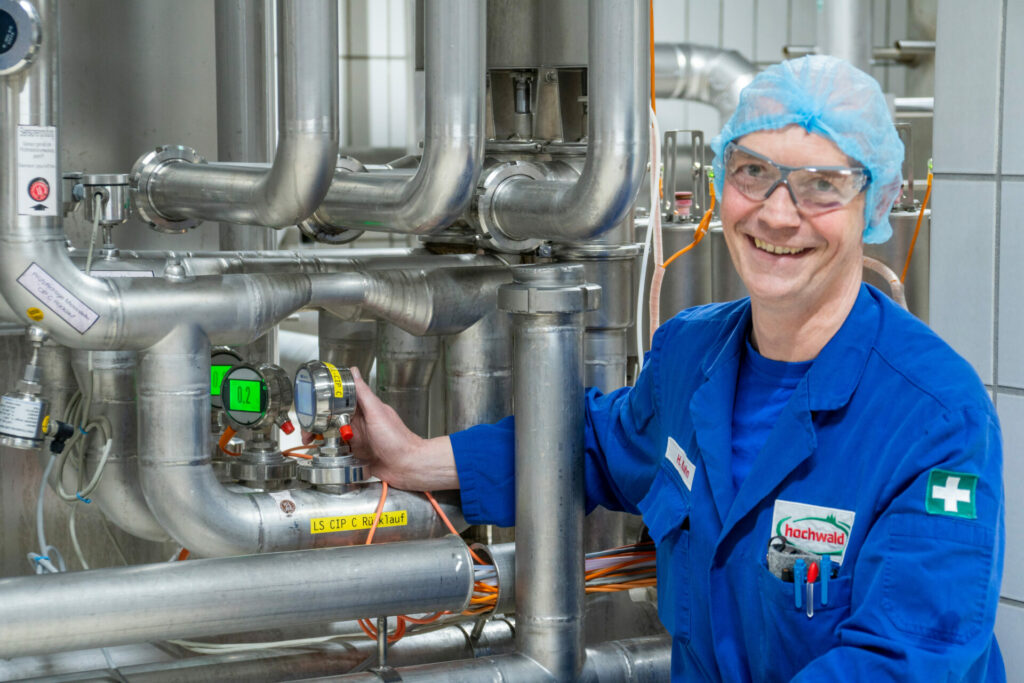
When Mr. Kuhn took over his position as Manager Electrical Engineering in the Thalfang company eight years ago, he quickly realized that the sensors used for conductivity measurement did not meet his high expectations. But even test runs with alternative sensors did not present Mr. Kuhn with the desired results. He wanted the optimum solution for conductivity measurement and kept searching.
In the end, the experienced Manager encountered the conductivity sensor he was looking for by chance. At some point, a third-party labeled CombiLyz AFI4 ended up the workbench of the electrical maintenance department. Since the dealer didn’t answer the service request, an employee made investigations to find out the manufacturer of the promising sensor – Baumer. Now the sensor partner for conductivity measurement was found. “After the successful test run we were pleased with the performance of the conductivity sensor, since AFI4 met our needs just as required,” reports Mr. Kuhn. In addition, he was well satisfied with the customer service provided.
Reliability is first among technical requirements. AFI4 proves itself every day in up to 80 CIP cleaning cycles. Since having started the cooperation with Baumer four years ago, there had not been a single failure of the AFI4s in use, neither there was a single housing damaged or leaking. “I’m satisfied by an analytical sensor working well for five years. That’s why we are on the right track with the Baumer sensors,” says Mr. Kuhn.
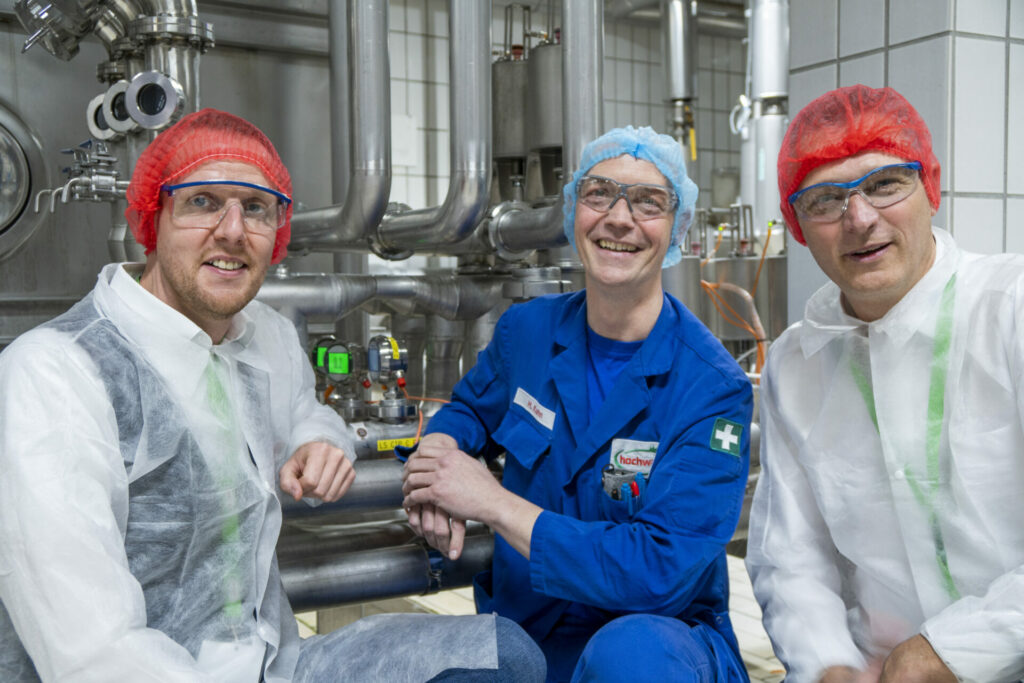
Another requirement were short response times with high precision measurements in parallel. In this point as well, AFI4 scores high by very good performance: “AFI4 is very fast and is exactly what we need since we deploy the sensor also in phase separation.” To him, this is the most important point. With flow volumes of 4-6 liters per second, fast measurement results will noticeably increase resource efficiency. Mr. Kuhn nods, “Thanks to AFI4 we minimize product rejects.” This is also to the benefit of the agricultural shareholders since besides quality, factory efficiency is decisive in raw milk processing. After all, it is the factory objective to make the most of the milk supplied by their member dairy farmers.
Can AFI4 guarantee such high long-year performance despite the high requirements? At Hochwald Foods, there are no signs at all of any performance loss. The technical team checks each sensor once a year. Out of the 47 currently deployed AFI4 sensors, a mere two presented drift but even within the tolerances. “The long-term stability is very good,” says Mr. Kuhn. According to him, further AFI4 benefits are the rotatable touch color display, easy handling, compact design, switchable measuring ranges and adaptive connection system. “In addition, this Baumer sensor is freely configurable and hence allows for universal use in every application. This also simplifies and reduces spare part inventory,” adds Mr. Kuhn who is a strong supporter of standardized solutions.
As a result of the good experience made with AFI4, the Manager of Electrotechnical Engineering has declared the robust Baumer sensor as a factory standard. For the upcoming factory overhaul with 6 new CIP circulations, this means: The long-term stable Baumer analysis sensor will continue to make an important contribution towards smoothly running milk processing. For optimal process monitoring, AFI4 will get company and backup by the proven Baumer PF20 flow sensor measuring flow velocity in CIP returns. This will further assure product quality and prevent time-consuming troubleshooting in the pipe system. Since after all, non-stop milk processing must be ensured in the future.
INFO Box
Hochwald
Hochwald Foods GmbH is a subsidiary of Hochwald Milch eG (both locations in Thalfang/Hunsrück) with 3082 member dairy farmers, an annual milk volume of 2.17 billion kg and 1.59 billion Euros annual turnover. The cooperative dairy company employs 2065 people at eight plants for dairy products such as cheese, yogurt, cream, and mixed milk drinks. The Thalfang factory founded in 1932 has specialized in condensed milk. Every day, 800,000 to 1.3 million kg of raw milk are processed into condensed milk and canned by 190 employees. The best-known brands rolling off the line include Bärenmarke and Glücksklee, together with other brands intended for the international market. 98 percent of the cans produced in Thalfang are exported, mainly to North Africa, the Middle East and South America. “In hot countries, non-perishable condensed milk is very popular. Less for coffee, though, but as consumer milk or in tea,” says Mr. Kuhn, Manager Electrical Engineering at the Thalfang factory.
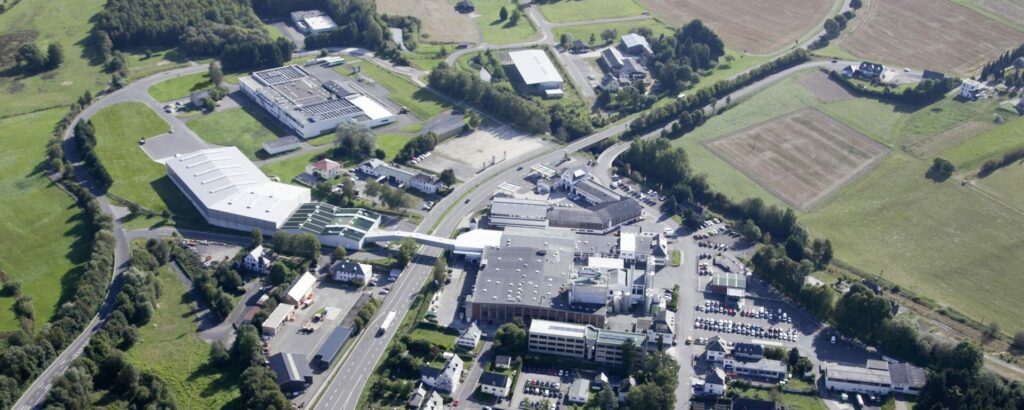
Why is AFI4 that robust and fast?
The Baumer CombiLyz AFI4 conductivity sensor is popular in food & beverage applications thanks to its durability and speed. One of the reasons for such high robustness is the one-piece design: unlike conventional conductivity sensors, sensor tip and temperature element are entirely in PEEK. Omitting a metal component with different thermal expansion, the sensor tip will endure frequent temperature jumps. Furthermore, thanks to the one-piece design Baumer was in a position to realize outstanding fast 15 seconds as temperature compensation time t 90. This design has been created by the Baumer experience in hygienic ultrasonic welding which is applied in the manufacture of the AFI4 sensing tip. The dark thin line around the opening in the sensing tip gives evidence of such excellence in welding. All welded products undergo helium leak tests. Like many other Baumer sensors, the AFI4 comes with EHEDG certification.