GF first introduced SYGEF to meet the growing demand for Flow Solutions in applications requiring high purity and resistance to aggressive chemicals. While the brand encompasses a variety of materials and technologies, the SYGEF PVDF range has seen particular success in industries such as pharmaceuticals, microelectronics, and chemical processing.
SYGEF Standard is specifically designed for corrosive environments. It combines high mechanical strength at temperatures between -20°C and 140°C with high chemical resistance against aggressive substances, including oxidizing and non-oxidizing or organic acids. In addition, PVDF is highly weather-resistant and can withstand prolonged exposure to sunlight, wind, or rain. Tailor-made welding solutions include IR fusion, characterized by a contact-free melting process that eliminates the risk of contamination.
SYGEF Plus is a high-purity PVDF piping system specifically engineered for applications demanding exceptional purity and stringent particle control. All components follow the SYGEF High Purity Chain, from raw material selection to the installation, and are manufactured and double bagged under ISO Class 5 (100) conditions in one of the largest cleanroom factories for fluoropolymer products in Ettenheim, Germany. Continuous improvements, regular leach-out tests that exceed SEMI F57 standards, and seamless quality assurance contribute to maximum reliability. Enhanced by specifically developed jointing technologies, SYGEF Plus is suited for the most demanding high-purity applications.
Looking back at the history of SYGEF PVDF, Sebastian Ehrlinspiel, Product Manager for SYGEF at GF, comments “In highly demanding industries such as microelectronics or chemical processing, companies are pushing the boundaries of technology. SYGEF Standard and Plus not only meet the requirements of today’s harsh or high-purity applications but have done so for the past 50 years. Combined with a complete solution approach that includes extensive services, our profound experience empowers customers to maximize the potential of their piping systems. Here’s to the next 50 years!”
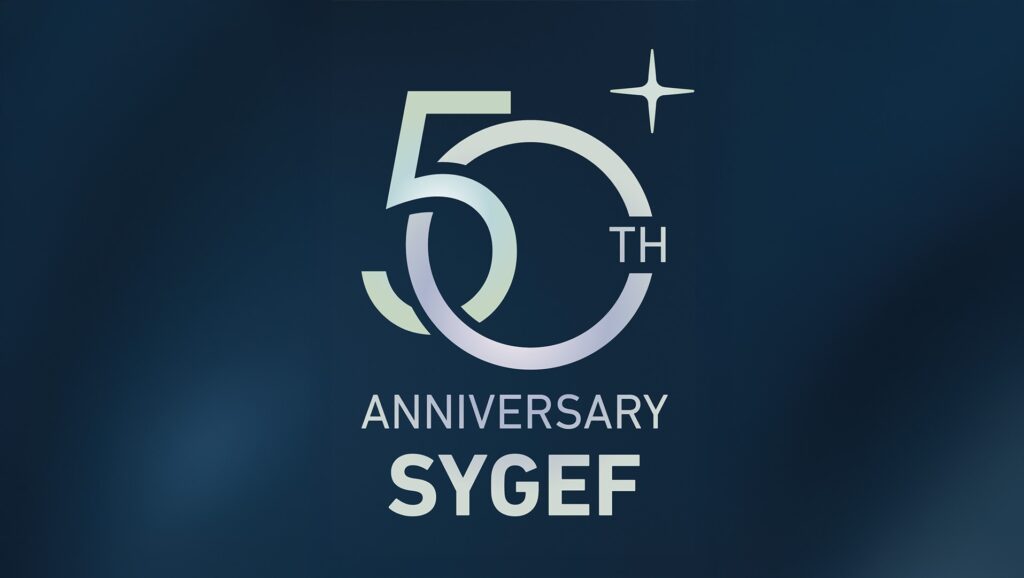