Why is compressed air monitoring important?
After electricity, natural gas, and water, compressed air is frequently regarded as the fourth utility in the industry due to its extensive use. However, in terms of per unit of energy delivered, compressed air is more expensive than the other three utilities. Compressed air production accounts for about 10% of all industrial electricity consumption. The high cost of energy has made reducing energy consumption a top priority for many businesses.
Compressed air is often taken for granted, but it is a crucial part of many industrial operations. If compressed air is not measured and maintained properly, it can lead to serious performance issues and to significant energy losses. So, it is important to measure and monitor compressed air flow and optimize your system.
What are the benefits of permanent compressed air monitoring?
You gain immediate insight of your energy flows by using permanent energy monitoring. You can use it as a guide to set energy-saving goals for your production level. Permanent monitoring allows you to:
- Obtain clear understanding of your factory baseline (such as energy, flow and pressure).
- Keep track of and optimize the control system.
- Implement optimization and maintenance management, thereby preventing exorbitant maintenance fees and device breakdowns.
- Size the machinery (compressors, pipework, and downstream consumers) and detecting capacity.
- Allocation of costs especially energy expenses.
- Abide energy-related regulations (EED, ISO 50001).
- Collect (huge) data, which is essential to be ready for the immediate future.
- Setting benchmarks for production facilities and machines.
- Leakage management.
- Impact human behavior by assessing energy costs (compressed air is not free).
Example of how permanent monitoring keeps your energy consumption at a low level
There are several advantages to permanent monitoring, as shown above. Let us take a closer look at one of the points: leakages. Leaks in any system are unavoidable, but unwanted: they are a waste of money. Any day new leaks occur, and multiple leaks together can affect system performance, for e.g., impacting system pressure. A permanent monitoring system provides insight into the baseline of your compressed air system. When consumption goes up, this can mean that more leakages occur. You can determine when it is worthwhile the manpower and investment, to organize a leak survey. Your leakage management can be further optimized by placing flow meters strategically in your factory, for you to allocate the leakage level.
And when you are fixing leaks, you will see your consumption level drop, showing the savings immediately. Permanent monitoring provides fact-based improvement. No longer annual leak surveys but execute them when you know that it makes sense.
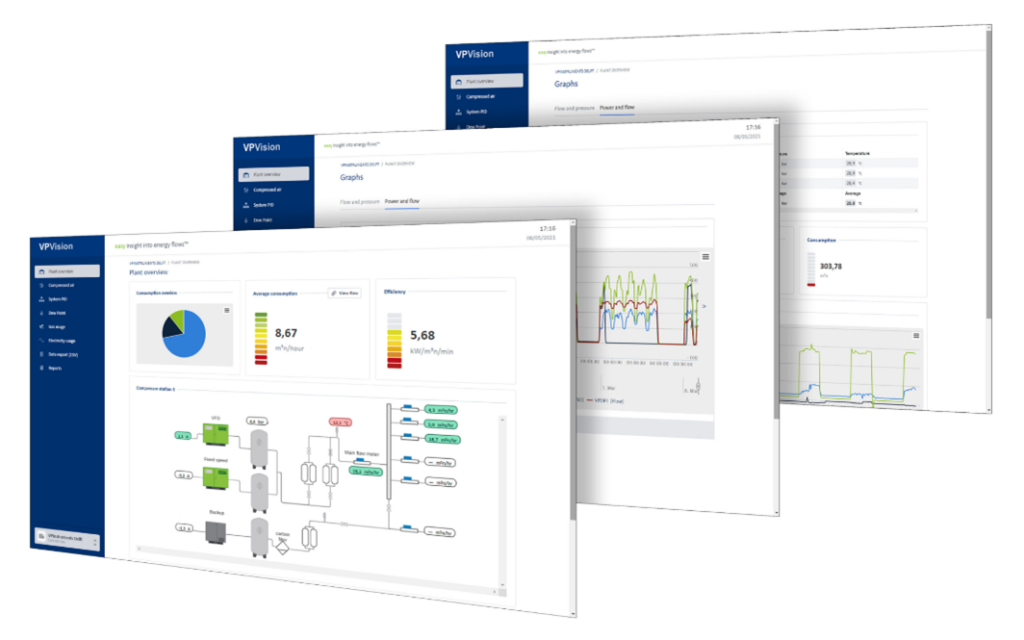
Why should I install a permanent monitoring system when I can hire an expert for an air audit?
An air audit is a great way to uncover your savings potential and based upon its results, great improvements can be made to your compressed air system. However, it’s important to note that your system is subject to change and maintenance, so your savings results will only be temporary. To keep your energy consumption low, permanent monitoring and continuous improvements are required.
By using a permanent monitoring system, like VPVision, you will learn your consumption baseline. Any occurrences that are out of the ordinary will be noticed quickly. Moreover, a monitoring system that provides proper alarms, dashboarding and reports, will provide the right insight to track the performance of your compressed air system and other utilities.
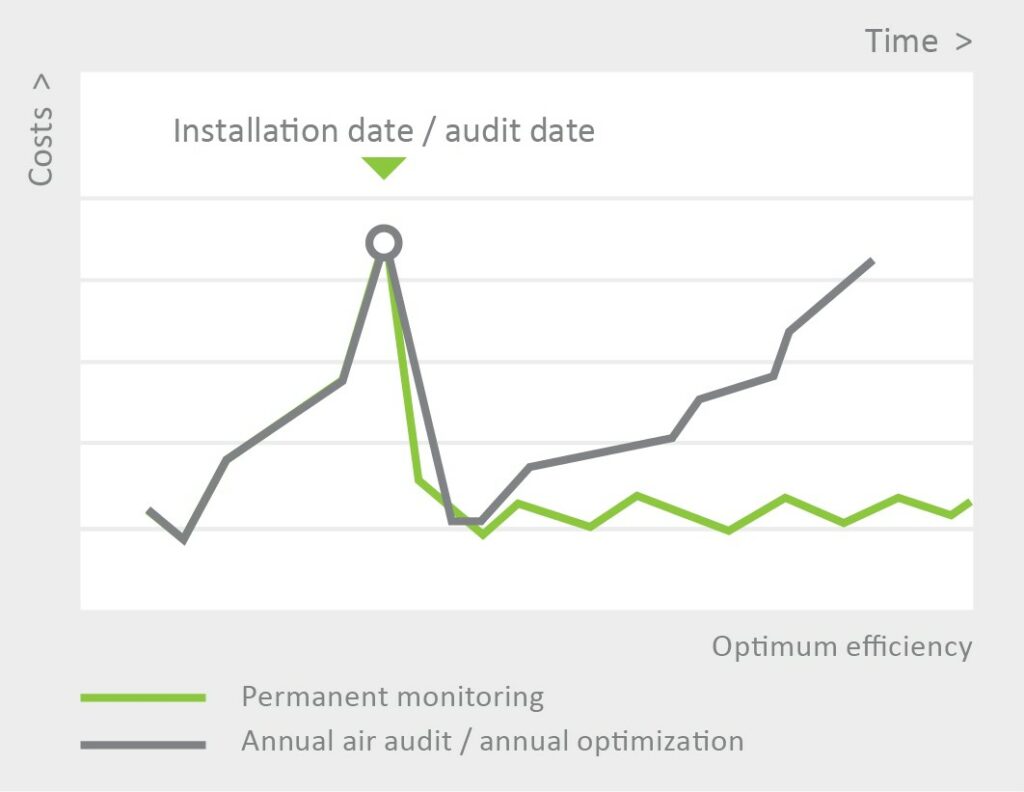
Improving your system one step at a time
Insight into unnecessary energy consumption makes waste concrete. Determine the right KPIs and keep checking in during the improvement process. Make changes step by step, so that it remains realistic and manageable. Energy management is a continuous process that initially costs money and time. Using a step-by-step approach keeps initial investment limited. With the energy and cost savings achieved, new investments can be funded for further improvements. A permanent monitoring system helps to provide the necessary data to valid your investments to higher management.
In the long run, however, your investment will be more than worth it. The potential is enormous: a reduction of 10 to 50% can be achieved for just your compressed air system. With the knowledge you have now, start cutting costs today with compressed air monitoring.