This process is often controlled with pressure, resulting in damaged pigs and pipes. The damage occurs when the pig gets stuck. Pressure increases until the pig breaks free at a very fast and uncontrollable rate.
By controlling the flow in the pipe rather than the pressure, the velocity of the pig can be better controlled. When the pig gets stuck, the mass flow controller allows pressure to build up. As soon as the pig breaks away, the mass flow controller senses the increase in flow and immediately reduces it. This reduces the velocity of the pig and the potential for damage.
This sketch shows pig velocity control by controlling flow in the pipe. A Proportion-Air FQB3 and F-Series mass flow controller assembly controls the speed of a pig as it moves through a pipe. The FQB3 servo control valve is a smart part that closes the loop around the signal output of the F-Series flow transducer. Constant velocity can be maintained, or pig velocity can be varied.
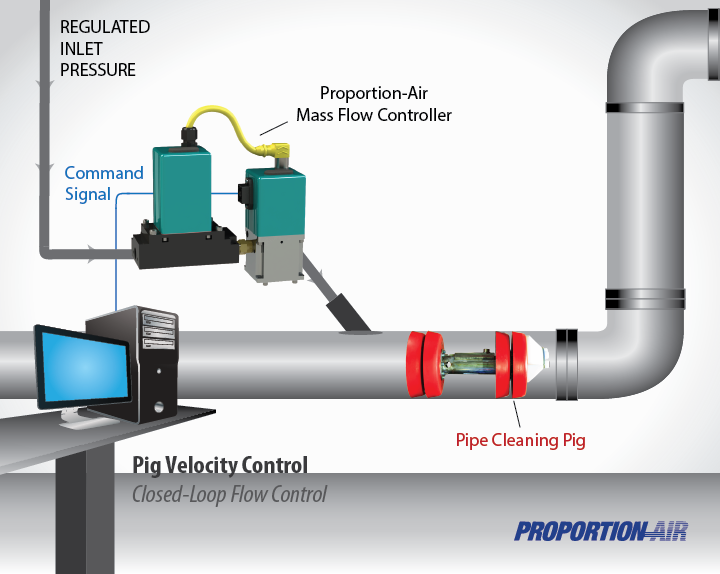
Update speed from the F-Series is less than 10 milliseconds, which ensures there is no lag in pig velocity control as conditions change in the pipe. Pig speed is adjustable based on a command signal from the controller and a signal output showing flow from the F-Series is available on pin 5 of the FQB3 electrical connector for data acquisition.
Controlling flow rather than pressure in a pipeline pigging application results in less damage to pigs and pipes, keeping systems online and efficient. Contact our team of applications experts at info@proportionair.com to learn more about how this method can work for you.