Airports, such as Sea-Tac, across the United States are today required to protect the environment, especially from the run-off of glycol de-icing fluids mixed with rainwater or snow melt that can adversely affect water quality, plant life and sea creatures. In 2012 the United States Environmental Protection Agency (US EPA) issued 40 CFR Part 449, which requires the treatment of de-icing fluid wastewater flows prior to their discharge as effluent. As a result, airport storm water run-off treatment systems must pass a permit review under the National Pollutant Discharge Elimination System (NPDES).
The Challenge
The facility engineers responsible for Sea-Tac recently undertook an upgrade project involving its wastewater system to maintain compliance with the EPA’s storm water requirements and also reduce the volume of wastewater flowing to a local wastewater treatment plant (WWTP). The purpose of the airport’s new Industrial Wastewater System Segregation Meter MC-0319775/WP# U00299 Project was to improve the storm surface water catchment system for the airport’s runways that contained de-icing fluids during frigid cold weather as opposed to normal rainfall run-off.
This expansion project was necessary in order to provide an additional point of water chemical analysis measurement across the process line for decreasing the amount of process water needing treatment. The engineers required a more accurate measurement of the de-icing fluid glycol present during freezing cold or snow storm incidents while also optimizing the airport treatment system’s efficiency and effectiveness.
The engineering, procurement and construction (EPC) engineer assigned to the project contacted the applications group at Electro-Chemical Devices, Inc., in Anaheim, California, to discuss the requirements of their project. The airport engineers were concerned first about the type and accuracy of the needed analytical water sensors, the initial cost of the analyzer and then how the ongoing cost of maintenance would affect the instrument’s lifecycle costs. In short, they were looking for the most cost-effective measurement solution with the lowest life-cycle cost.
The Solution
The ECD applications engineers, after reviewing all the requirements, then recommended the company’s Total Organic Carbon (TOC) Analyzer. It relies on UV persulfate oxidization sensing (per EPA Method 415.2) analysis. The TOC Analyzer was then chosen by the airport engineers as the new system to replace the existing equipment on site.
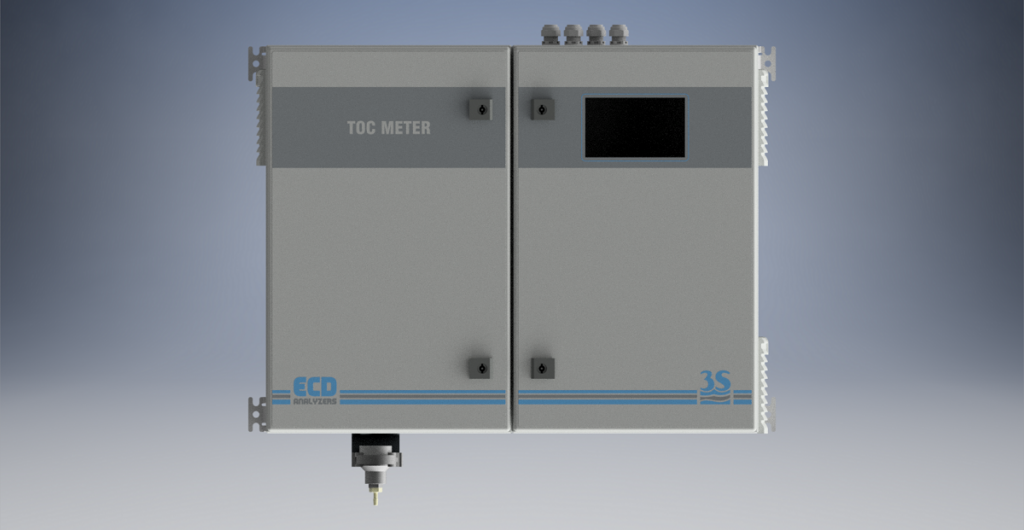
The added features and benefits of ECD’s new TOC Analyzer, such as no band filters to clean, no need for external CO2 carrier gas and a self-cleaning filtration system were recognized by the airport engineers as key advantages for keeping the overall cost and the maintenance cost of the instrument down to a minimum.
Organic compounds are found in almost all types of water – from natural and treated drinking water to process water, cooling water, and water used in pharmaceuticals and food production which is a challenge in many industrial processes. Wastewater, storm or municipal, of course also contain organic compounds—sometimes in very high amounts.
Too much organic contamination in process water or wastewater interferes with many industrial and water quality processes. For example, an excess of organic matter can foster microbiological growth or, when disinfecting drinking water, encourage the presence of undesirable byproducts. In storm water or municipal wastewater, the same holds true when treating effluent prior to release back into the ecosystem where left untreated it can harm sensitive plants, animals, fish and sea life.
On the other hand, there are numerous processes in the chemical and galvanic industries in which water is mixed with organic additives. In order to control and monitor these processes, it is important to measure the amount of organic substances in the water, and TOC is an important sum parameter.
ECD’s TOC Analyzer is particularly effective at measuring the total carbon content of the mixed wastewater flows such as those present in the airport’s de-icing/rainwater catchment system. The TOC values are converted by the airport’s control system into biochemical oxygen demand (BOD) values. If the BOD value is less than 45 ppm, the process flow could be safely released as effluent and sent directly to Puget Sound (Pacific Ocean). If the BOD value is greater than 45 ppm, the process water would be sent to the sewer system where it would be treated at a nearby local wastewater treatment plant (WWTP).
The ECD TOC Analyzer relies on the UV persulfate oxidation method for the detection of generated carbon dioxide (CO2) using a non-dispersive infrared (NDIR) detector, which conforms to EPA, DIN, CE, ASTM, NAMUR regulations. This analyzer can measure TOC in liquid samples ranging from 0 to 5 mg/L to 20,000 mg/L.
In analyzing water for the presence de-icing fluid, the water sample is first acidified and then sparged to remove inorganic carbon. The remaining liquid is mixed with sodium persulfate and digested by two high-performance (UV) reactors. CO2 free carrier gas is sparged through the UV reactors. The CO2 is stripped from the sample. CO2 is mixed with the carrier gas and is sent to the dryer to remove any moisture, and it also passes through a Copper filter to prevent any moisture or corrosive gas coming into contact with the NDIR detector. The TOC level is then determined based on the CO2 concentration as measured by the NDIR detector.
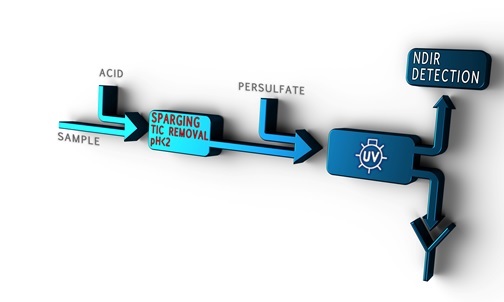
The ECD TOC Analyzer offers safe operation even if there is a sample loss. The analyzer’s fast loop reservoir has a built-in floating level sensor, which indicates a “sample” or “no sample” condition. If no sample reaches the reservoir for more than a preset time, the analyzer switches automatically to standby mode. When in standby mode, the analyzer doesn’t consume any reagent fluid and puts the 4-20mA output signal on hold. Also when the loss of a sample occurs, the analyzer can be setup to issue a “loss of sample” alarm on one of its relays. As soon as the sample flow restarts, the analyzer goes back into the conditioning mode then switches back to the analysis cycle automatically.
ECD Analyzer TOC Analyzer was ordered for a pre-mixed catchment basin where the majority of the process water is captured from de-icing events. This new installation helps the Port of Seattle decrease the amount of process water being sent to the WWTP by reducing the amount of rainwater transferred from the other catchment basin.
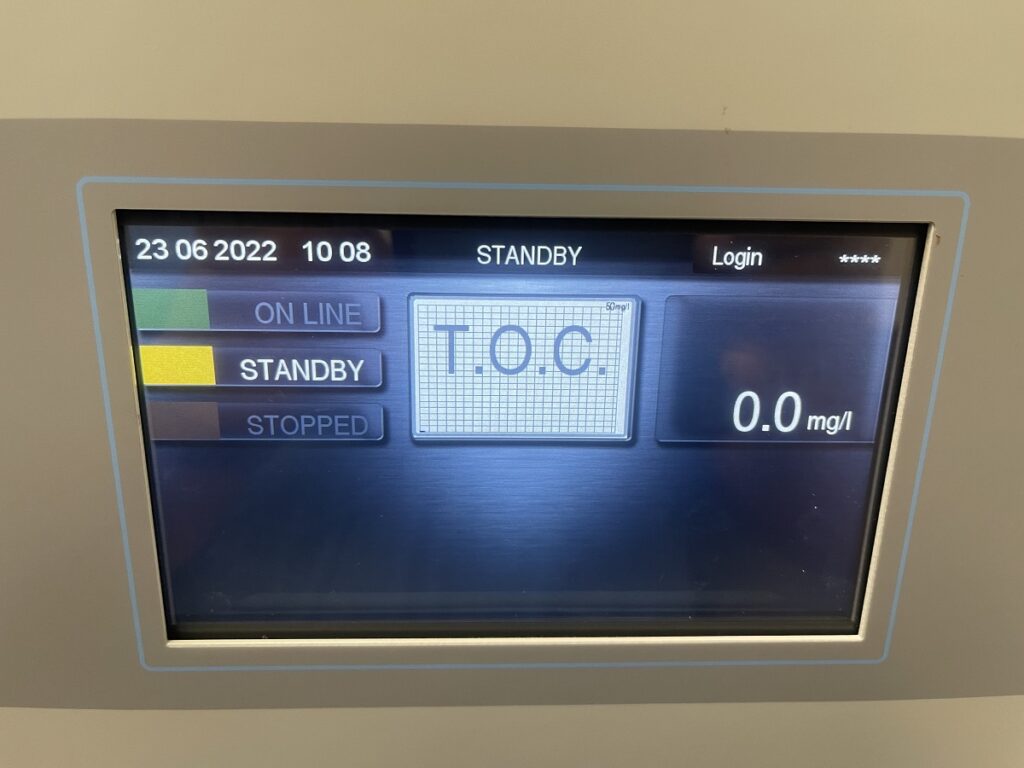
The Results
The key advantages the SeaTac team saw in the ECD TOC analyzer was that it has a built in gas system, so no external gas supply was required. The analyzer also has a touch screen display human machine interface (HMI) (Figure 4) with built in software, so no external computer is required. Using an external self-cleaning metal filter eliminated the need for paper filters. The unit’s pre-mounted dilutor and reservoir made for easier installation too.
ECD field engineers and technicians provided the startup and commissioning of the TOC analyzers for the Port of Seattle (Figure 5). TOC instrument introductory classroom style sessions and actual hands-on training were also both provided to the staff. The TOC Analyzer is highly intuitive with its graphical HMI interface, making the learning process simple to master for technicians and engineers alike with no special tools required for installation or operation.
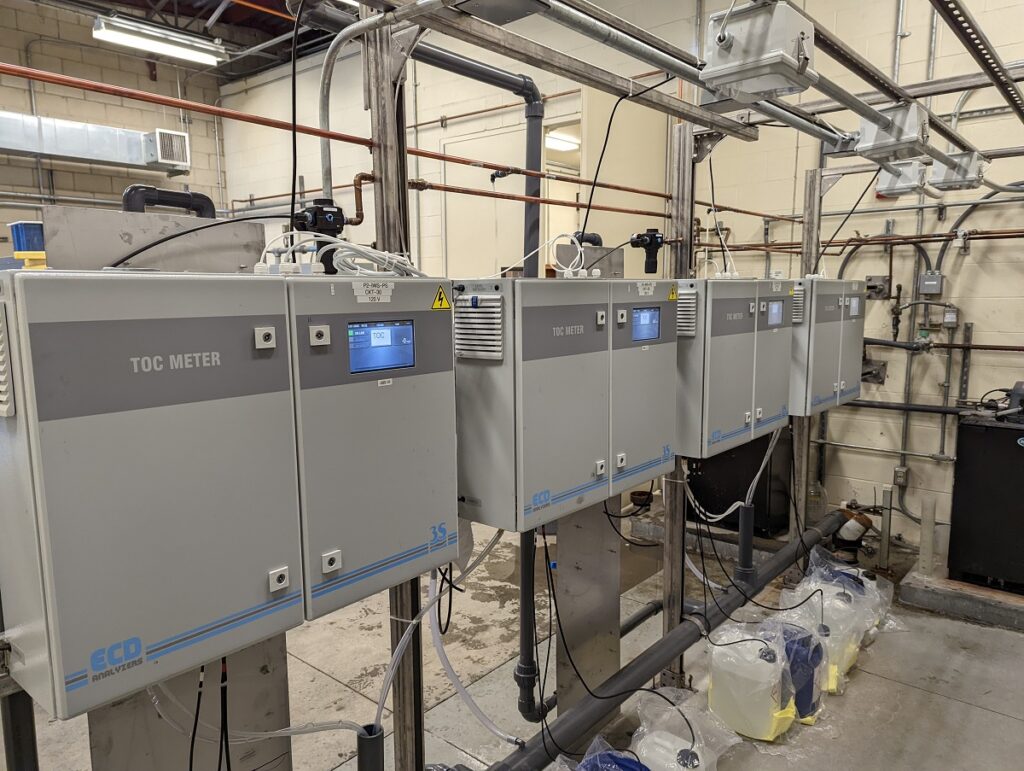
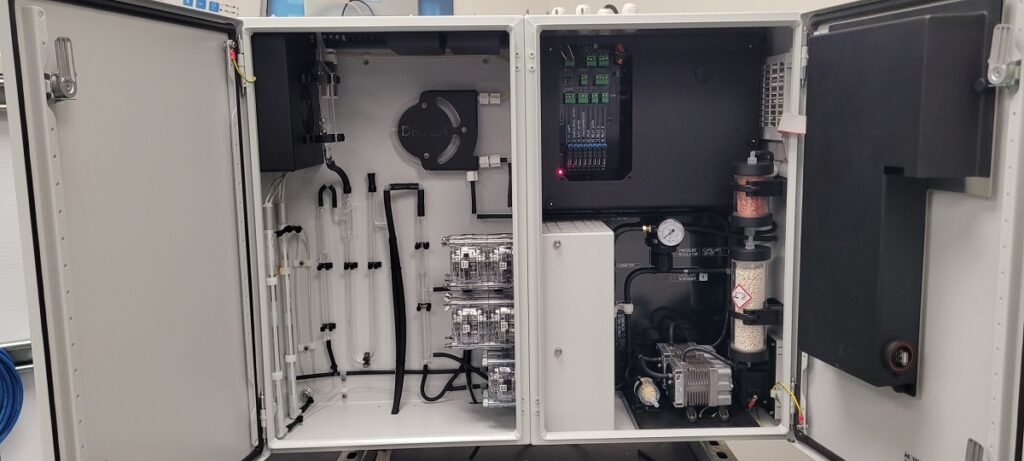