Pharmaceutical water is one of the most important raw materials in pharmaceutical production. It is used directly as feed for the production process with highest quality requirements, as well as for cleaning the plant units. Therefore, production and distribution of pharmaceutical water is considered to be one of the critical and sensitive elements of the pharmaceutical industry. Variations in water quality, or even of water delivery failures, can cause pharmaceutical production to stop immediately.
Pharmaceutical water is purified water, and in principle just desalinated drinking water with a high degree of microbiological purity. It must be manufactured in compliance with the specifications of the pharmaceutical production industry. A pharmaceutical water supply system is typically subdivided into generation, storing and distributing units.
With a capacity of 79,252 gal/h (300 m³/h) the central pharmaceutical water system at the Hoechst Industrial Park Frankfurt (fig. 1) is the largest of its kind worldwide. The distribution system went in operation in 2000 and supplies purified water to approximately 20 connected pharmaceutical operations through a distribution system 8.5 miles (14 km) of sterile pipes around the clock.
Increasing validation requirements instigated the decision to replace the existing production system with a new one using state-of-the-art process and automation technologies. Siemens was responsible for planning, engineering, installation and qualification of the instrumentation and control part of the project including the complete field instrumentation package.
Pharmaceutical Water Production Plant
Pharmaceutical Water is an essential raw material for pharmaceutical production. It must comply with very stringent quality specifications and be available for use by the production plants 24 hours a day. Therefore, modern pharmaceutical water production and distribution facilities feature a high degree of automation and process instrumentation technologies.
Siemens is a leading supplier of process instrumentation with a broad range of products that comply with the requirements and specifications of the pharmaceutical industry.
Purified water production plants, with many different process devices working together, are a particularly challenging application.
From drinking water to pharmaceutical water Source material for the pharmaceutical water production is drinking water. It is extracted in the Mönchhof area and transported via underground pipes to the Hoechst Industrial Park, where it is processed to drinking water. Then the water is further purified by passing through several treatment steps.
Typical specification data are:
- Specific conductivity < 0.3 μS/cm
- TOC value < 50 ppb
- Temperature 50 °F – 72 °F (10 °C – 22 °C)
- Heavy metals (DAB) < 0.1 mg/l
- Nitrate (DAB) < 0.2 mg/l
This water quality is achieved by the following treatment steps (fig. 1):
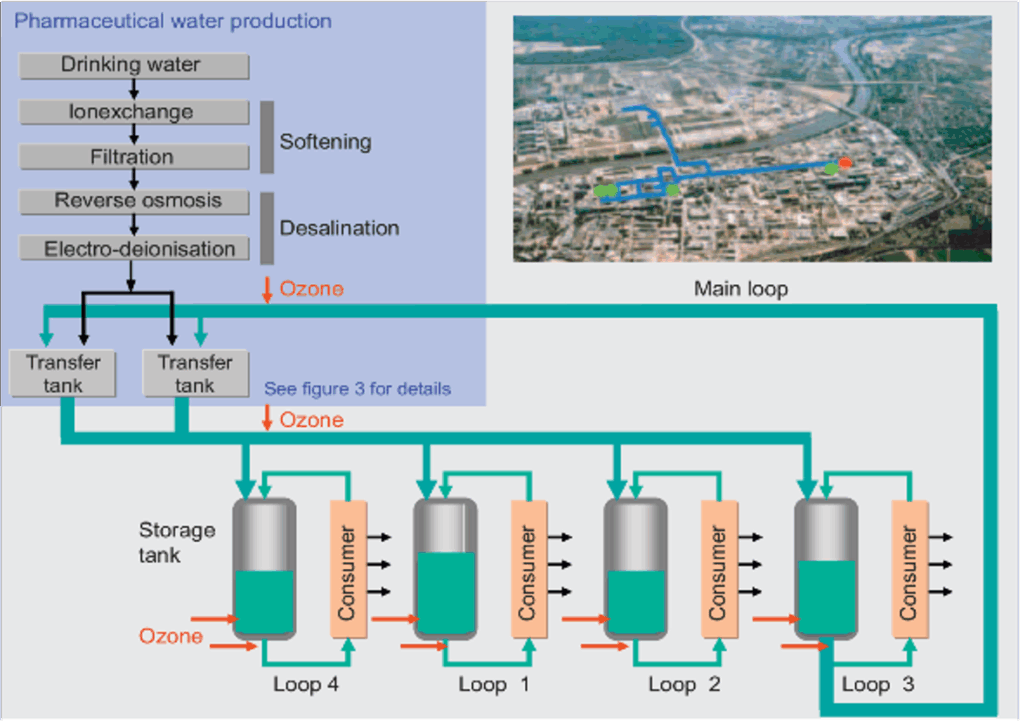
Softening through ion exchange
Calcium and magnesium ions of the “hard “water are replaced by sodium ions in vessels that are filled with special ion exchange resin. By passing through the vessels the water is softened.
Partial desalination through Reverse Osmosis In the reverse osmosis stage the water is partially desalinated. The water is pressed through a semi-permeable membrane by high pressure pumps against the osmotic concentration gradient.
This process is called reverse osmosis and removes minerals and other impurities. The product is called permeate.
Final desalination through Electro-Deionization (EDI) systems are used as a post-treatment for reverse osmosis to finally purify the permeate.
EDI is a combination of ion exchange and electrodialysis. The ions picked up by the ion exchange resin are discharged from the cell through an electric field.
Preventing microbial growth through Ozonation A further treatment step is the ozonation of the water with electrolysis cells at several locations of the distribution network. It prevents microbial growth and secures the water quality along the extended distribution distances.
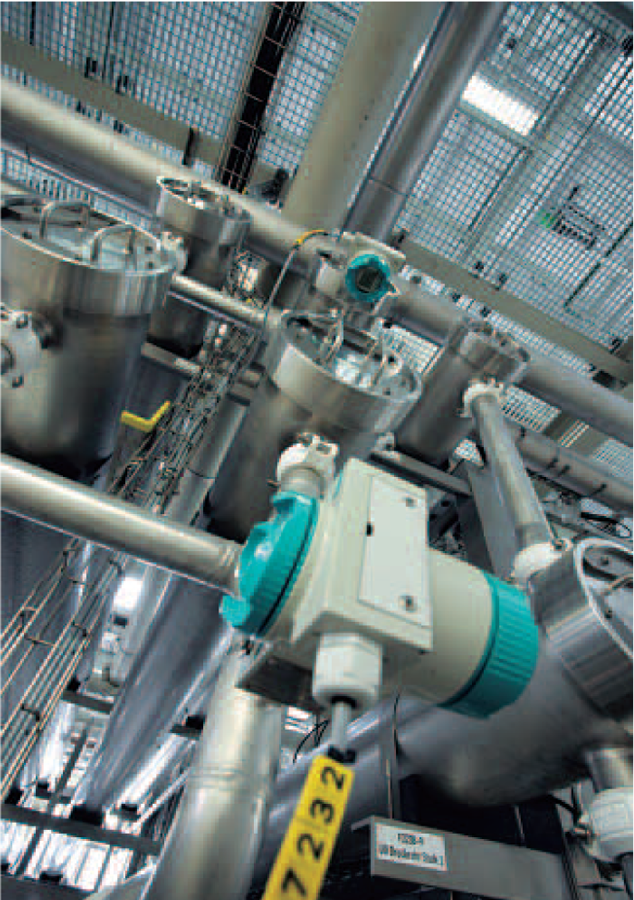
Purified water
In contrast to common water with a certain content of minerals, such as magnesium and other substances, purified water contains almost no contaminants. Purified water is produced typically by processes like ion exchange, reverse osmosis, ultrafiltration, photooxidation, de-gassing, UV-treatment and sterile filtration, which are used in defined combinations. The pharmaceutical industry distinguishes between Compendial Waters and Non-compendial Waters. The first is based on fixed specifications contained in Pharmacopoeias.
The most important compendial waters are Purified Water (PW) and Water suitable for Injections (WFI). At the industrial park in Hoechst, as described here, the water refers to purified water in pharmaceutical quality.
Plant design
The central pharmaceutical water system at the Hoechst Industrial Park is the largest of its kind worldwide and somewhat challenging: with a capacity of approximately 79,252 gal/h (300m³/h) it is small compared to a full-size desalination plant. On the other hand, it is big compared to normal pharmaceutical water production systems with a capacity of e. g. 220 gallon/minute (50 m³/h). Consequently, it was a remarkable challenge to all partners to design and build a system of that size according to the qualification and validation rules of the pharmaceutical industry and, at the same time, meet the requirement of continuous availability.
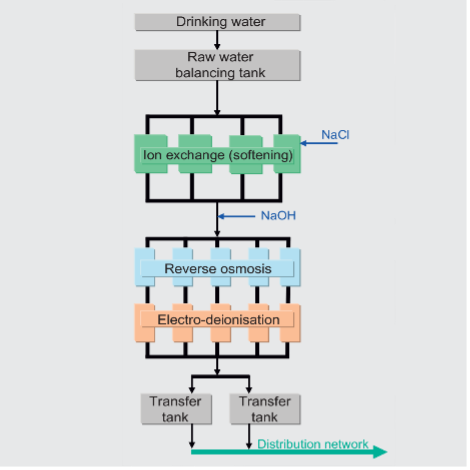
Considering the large number (19) of operations connected to the system, a plant shutdown would have a tremendous impact on production. The plant basically comprises a fourfold constructed softening unit (three lines in operation, one in regeneration) using the ion exchange principle, followed by five independently controlled production lines, each consisting of a three-stage reversed osmosis and an electro-deionization unit. The feed of NaCl provides the regeneration of the ion exchanger and the NaOH is used to control the pH value upstream of the reverse osmosis.
Additionally, the plant is equipped with a CIP- sanitization and cleaning system. It uses only hot water to avoid any infiltration of chemicals into the purified water system.
Use of more than 100 process devices
More than 100 Siemens process devices have been installed at the plant and are connected to a SIMATIC PCS 7 control system (Fig. 4) to solve the versatile and challenging application tasks.
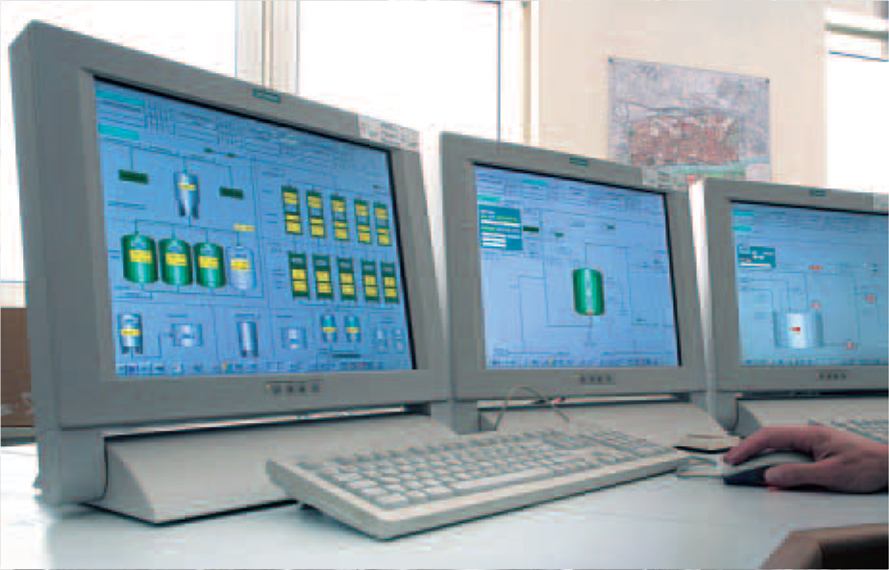
Some devices and their applications
The SITRANS F product line offers numerous flow sensors and transmitters. In the purified water plant, they are used mainly for balancing functions and to support commissioning and to report device status messages.
SITRANS F Electromagnetic
An electromagnetic flow meter measures volume flow rates of electrically conductive liquids (fig. 5). It is used for balancing the amount of water processed by the plant. This technology is very effective in this case, because the water is still conductive at the place of installation.
SITRANS F Clamp-on Ultrasonic
A non-intrusive externally mounted transit time flow meter perfect for flow measurement of low or zero conductivity water. Since clamp-on ultrasonic flow meters do not encounter the fluid inside the pipes, they eliminate the risk of contamination. This is critical when dealing with sensitive flows ensuring that the final product remains safe.
SITRANS P
A digital P320 pressure transmitter featuring integrated diagnostic functionality and HART, or PROFIBUS PA communication capability. It comes with easy-to-use pushbutton operation and high accuracy. It is used here to control and monitor the drop in pressure at the water production lines, which is a key functionality for correct plant operation.
SITRANS T
The SITRANS Temperature portfolio offers numerous sensors and temperature transmitters. They are used to control the required water quality at different locations at the plant.
Pointek CLS 200
A capacitance technology-based level switch featuring inverse frequency approach for high resolution. It is used here at two locations: to monitor and control the NaOH feed and to monitor the filling level of the two transfer tanks.

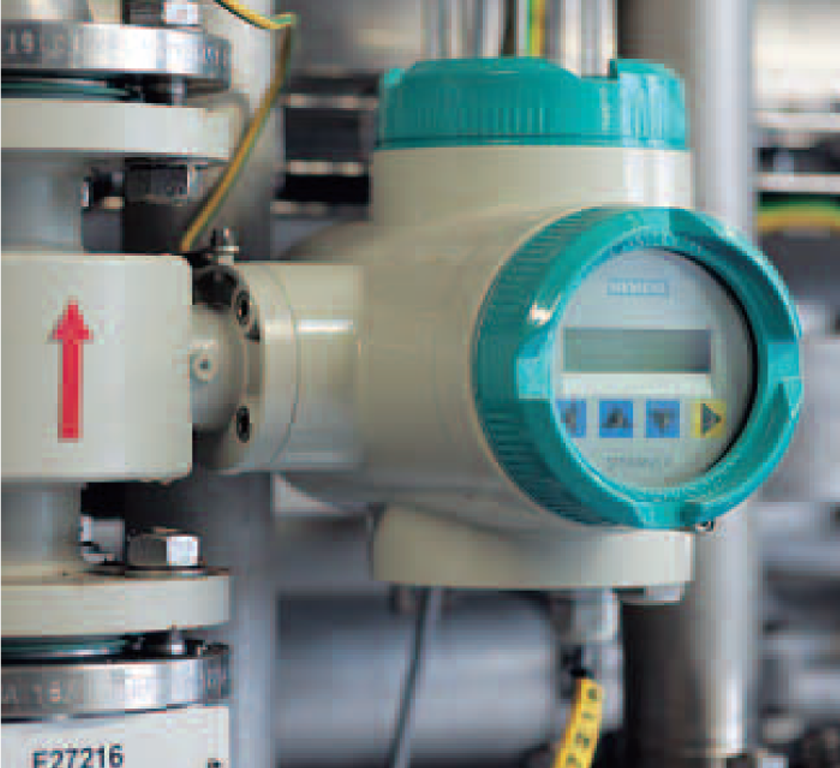
Experiences
During upgrading and rebuilding the plant (Fig. 5), the supply of pharmaceutical water could not be interrupted at any time. This challenge was successfully met by a step-by-step integration and a very close coordination between Infraserv Hoechst (plant operator), Hager+Elsässer (plant construction) and Siemens as supplier and specialist of the automation and instrumentation equipment.
The equipment qualification procedures required for a pharmaceutical plant were carried out during installation and commissioning. The plant operator recognized Siemens’ competence as an important factor in the success of this process.
After the optimization steps during the start-up phase the plant very soon provided the defined performance: a reliable, fully automatic operation and a correct quality of the pharmaceutical water.
User benefits
The main user benefits from this project include:
- The combination of a first-class process technology and the advanced measuring and control technology of Siemens ensures the user optimal functionality and a remarkable added value through technological lead.
- The close interconnection between measuring technology (process devices) and control technology (PCS 7) from one supplier increases plant operating reliability and efficiency.
- The outstanding performance of the process devices regarding accuracy, long-term-drift, operating reliability and suitability for use in pharmaceutical applications secure trouble-free operation and allow to full use of the technological potential of the processes involved. Siemens’ extensive long-time experience with the specific requirements of the pharmaceutical industry avoids time delays and shortens time-to-market.