Why intelligent mechanical seals?
Mechanical seals are mounted on rotating shafts, and seal the process side to the atmospheric side and therefore work directly inside the machine. Regardless of whether they are pumps, agitators or compressors, mechanical seals are an integral part of the process sequences in machines. Due to their function and design even the smallest anomalies and deviations affect the seal. If the mechanical seal is equipped with intelligent sensor technology and connected to associated services, a sealing solution can be quickly and easily turned into an effective remote condition monitoring solution.
What does intelligent sealing technology mean and what does it have to do with condition monitoring?
An intelligent sealing solution is a combination of hardware, software and expertise. In return, this results in valuable 24/7 process insights, a significant increase in safety and an improvement in process stability.
Mechanical seals with sensor technology and data transmission equipment provide the initial input. The actual values of temperature, pressure and vibration are provided as standard. However, other measured variables such as flow rate, axial displacement, speed, torque and vibration can also be recorded.
The special feature of the EagleBurgmann technology for condition monitoring with intelligent sealing solutions is the enormous range of measured values of heat up to 150 °C, sealing pressure of up to 100 bar and 3-axis vibration of up to 1 kHz, 6 g.
The data can be conveniently viewed online at any time. Maximum and minimum parameters for application monitoring can also be defined as standard, which send alarm signals if they are exceeded or not reached.
However, it only gets really interesting with the data analysis and the findings and recommendations for action derived from it. The most exciting analyses are the data packages over a longer period of time which identify trends and patterns that may not be visible in snapshots. Correlations, causalities and risks can also be better recognized and understood. EagleBurgmann regularly provides its customers with this information in the form of carefully prepared performance reports. In addition to the processed data over an individually defined observation period, the reports also include the interpretation of events and the resulting recommendations for action.
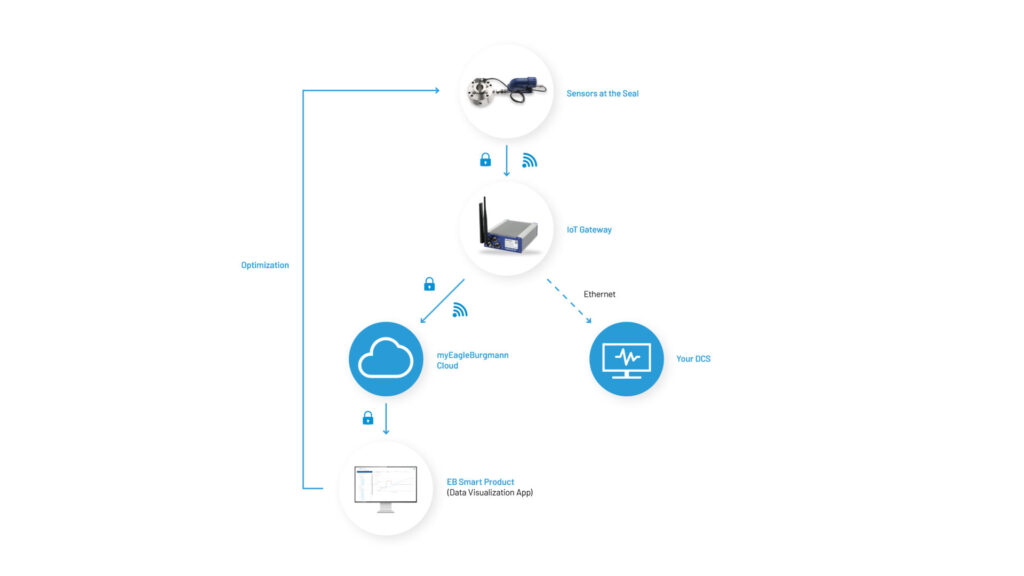
A unique additional offer is a mirrored application setup. Here, the same sealing solution is installed at EagleBurgmann as at the operator’s site with the calculated parameters. The mirrored setup makes it possible to identify and exclude the influence of the customer’s environmental conditions, such as installation location, process fluctuations and even weather influences.
Valuable knowledge when it comes to evaluating the possible causes and effects of measures and changes.
Good reasons for using remote condition monitoring with intelligent sliding directions
Most pump, agitator and compressor applications are designed based on calculated operating conditions. In practice, the number of different influencing factors and their interactions are so diverse that these calculations are often exceeded or undercut.
Condition monitoring with intelligent mechanical seals shows the actual operating reality and provides unprecedented insights into operating parameters, their interrelationships and interactions. This results in multiple benefits for the user, which quickly pay for themselves through an enormous increase in safety and process stability.
Condition monitoring does not necessarily have to be operated on a permanent basis but can also be used as a service tool to analyze and rectify bad actor applications, for example.
Another advantage of condition monitoring with intelligent mechanical seals is the accumulation of valuable knowledge for the implementation of practical predictive maintenance solutions.
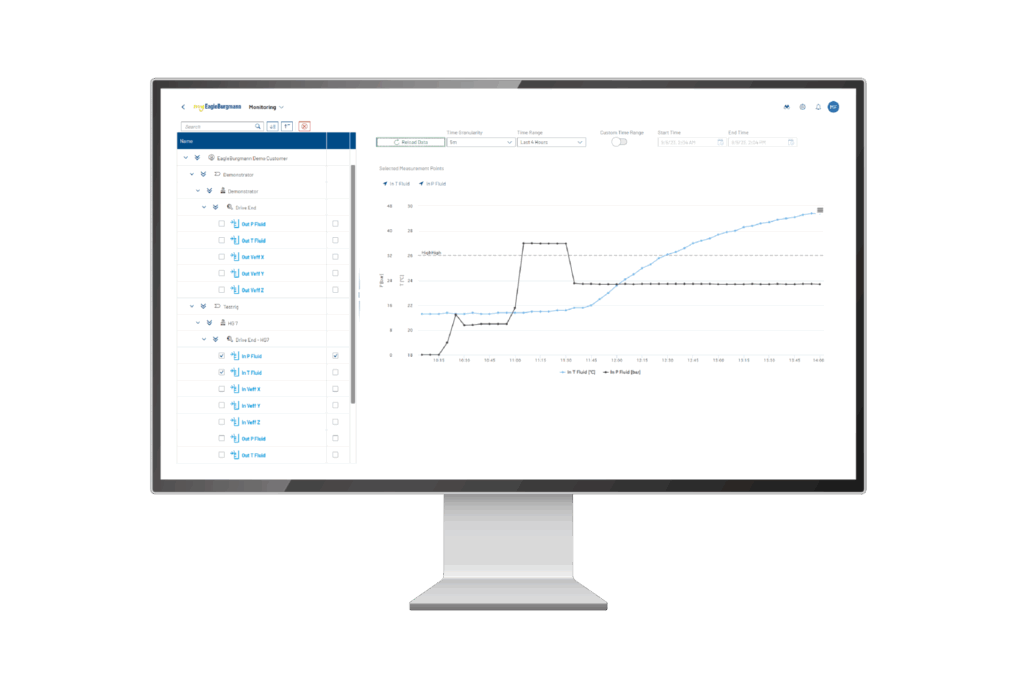
Conclusion
Condition monitoring in conjunction with intelligent mechanical seals enables previously unattainable process insights with fact-based data quality far beyond mechanical seal technology. The findings contribute directly to an improvement in application safety and reliability. The more comprehensive the knowledge of an application’s performance is, the more accurate forward-looking statements can be made. And thus, realize valuable efficiency gains.
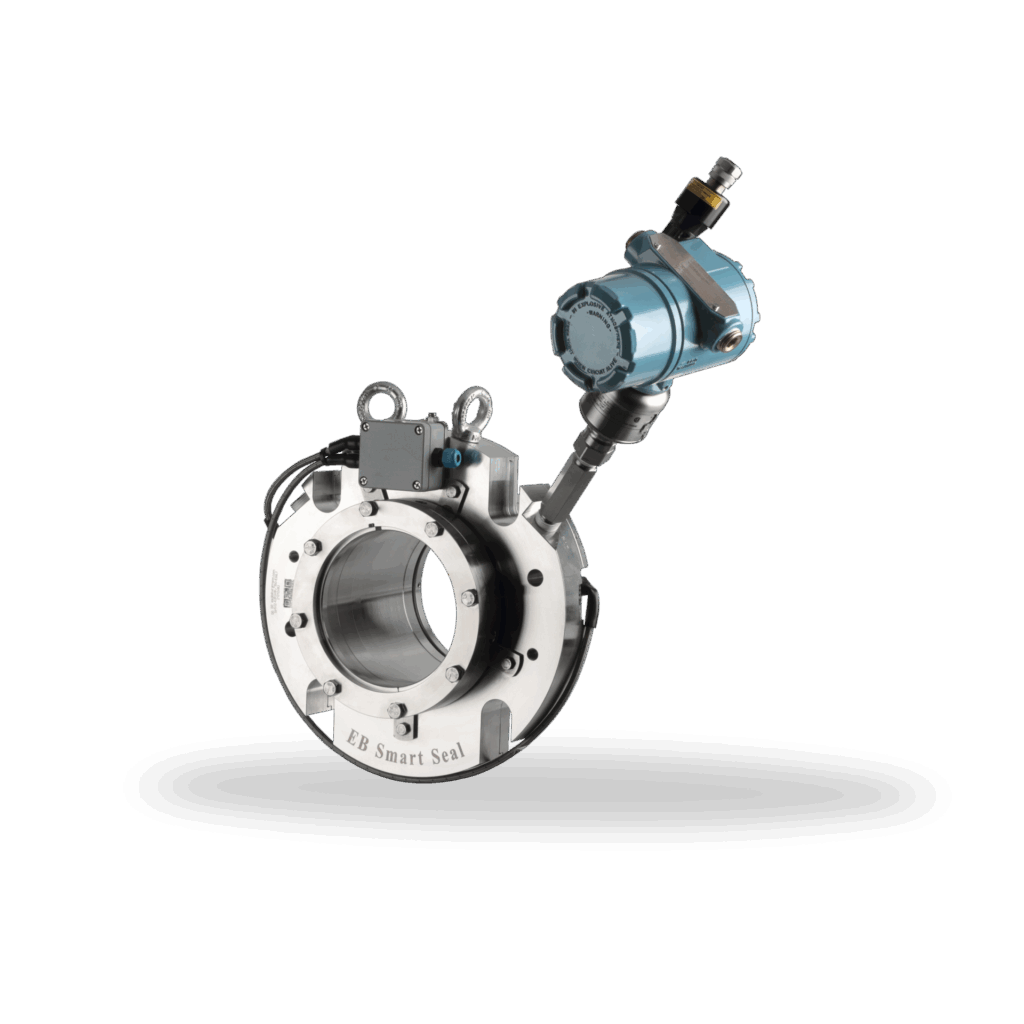
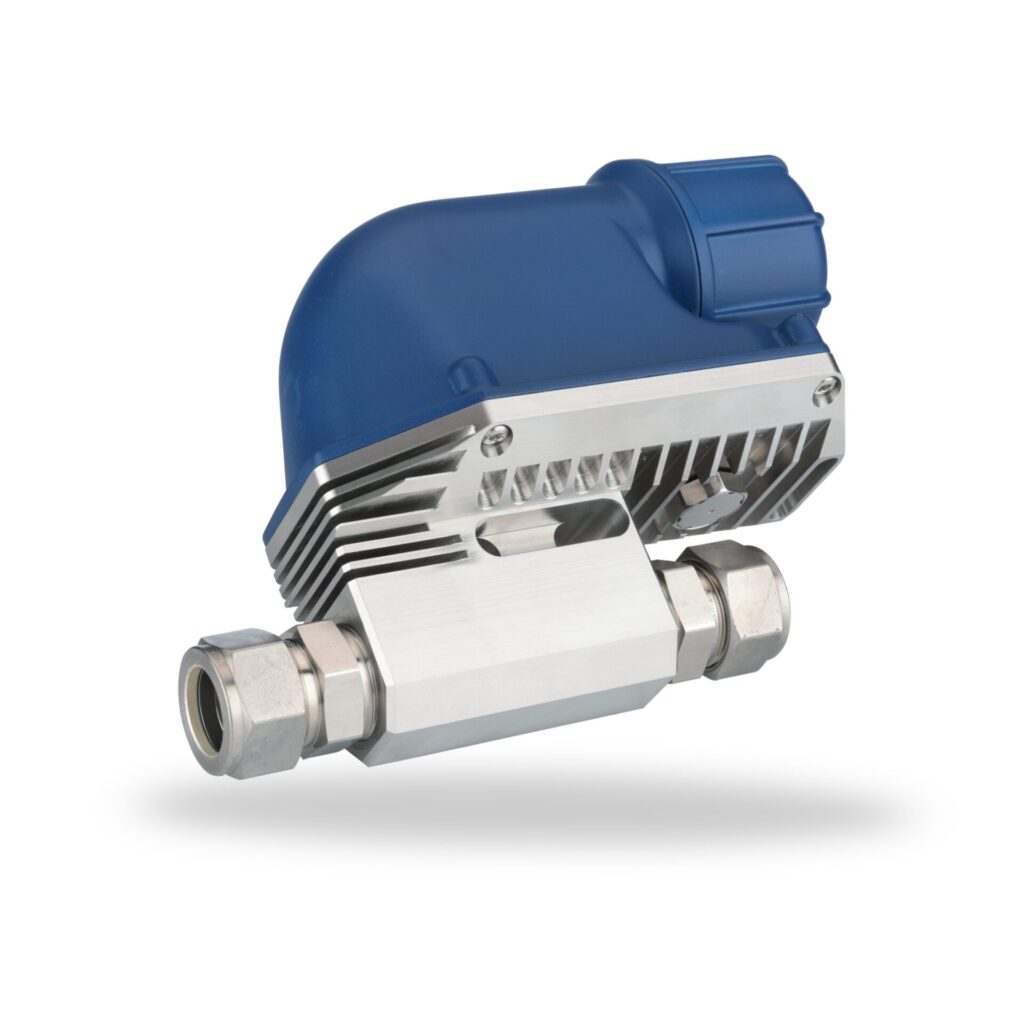
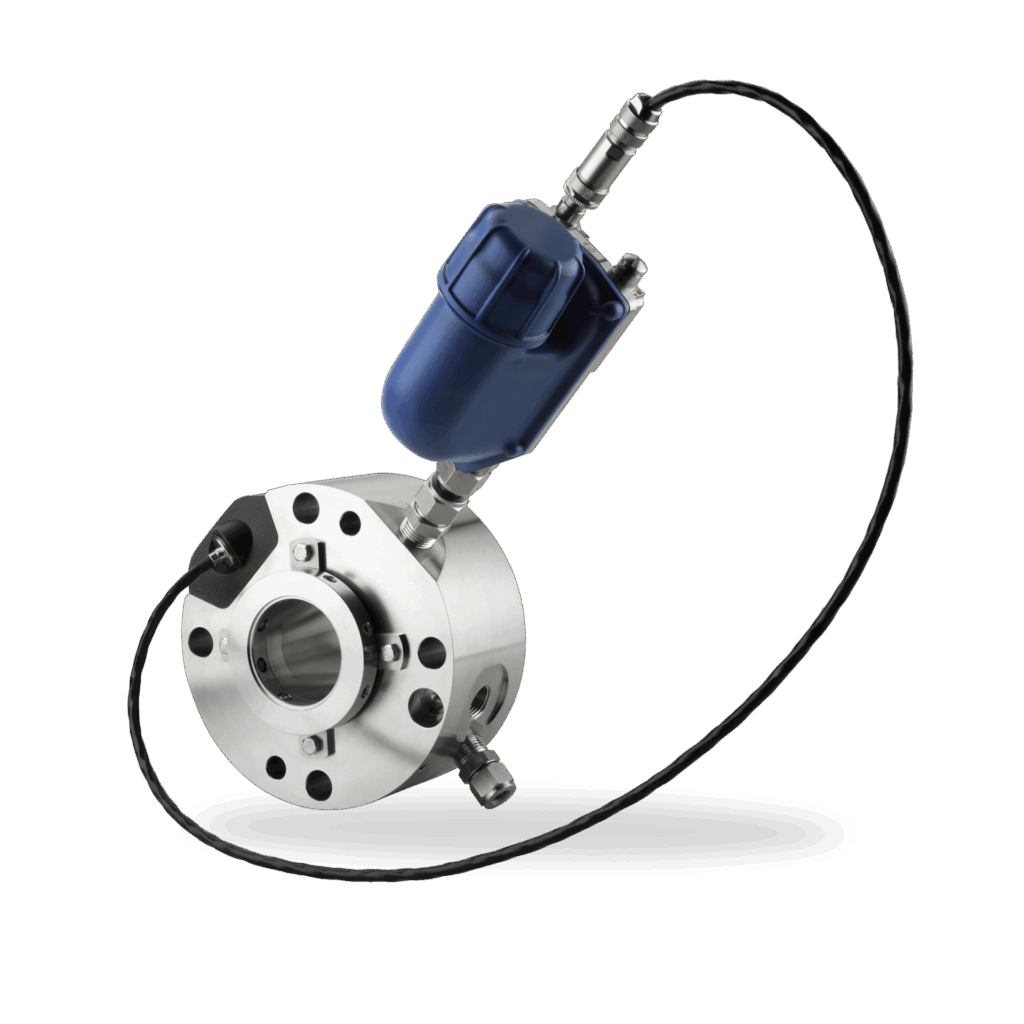