Hydrogen is developing into a key technology for the energy transition in industry. However, the atoms of the “green” energy carrier are the smallest and lightest of all elements. Their minuscule size enables them to penetrate into many materials, where they can cause structural changes. This places the highest demands on all plant and system components in process engineering and therefore also on the stop and control valves. Valves made of ferritic and martensitic steels are particularly prone to the so-called hydrogen embrittlement, which can lead to material failure.
Choice of material is decisive for safety
Schubert & Salzer solves this problem with sliding gate valves made of austenitic steels such as 1.4408 and 1.4404. These materials guarantee a very high resistance to hydrogen-induced cracking. The Ingolstadt-based manufacturer of control and stop valves also makes seat valves from stainless steel 1.4408 especially for hydrogen applications.
Also, classic sealing materials such as EPDM or fluorocarbon rubber cannot be used without restriction in the hydrogen environment. In order to prevent material failure caused by the penetration of hydrogen, Schubert & Salzer relies on special plastics or – in particular for high pressures – on metal seals in order to ensure integrity both permanently and in the case of sudden pressure drops.
Permanent tightness prevents risk of explosion
One of the biggest potential hazards involved in the use of hydrogen is its extremely high flammability. With 4 to 75 percent by volume in air, its explosion range is significantly wider than for other gaseous energy carriers. This greatly increases the risk of an ignitable atmosphere being created.
In order to reduce this risk, the sliding gate valves from Schubert & Salzer are technically and permanently leak-tight according to the Technical Rules for Hazardous Substances and meet the requirements of the Technical Instructions on Air Quality Control (TA-Luft 2021) according to EN ISO 15848-1. Special versions even achieve body leakage rates of less than 5 x 10⁻⁶ mbar l/s and are therefore suitable even for use in closed rooms.
The seat valves from Schubert & Salzer also stay tight in hydrogen applications. Selected variants conform to Category I of the Pressure Equipment Directive; with options such as metal bellows, welding ends or flange connections, they offer outstanding tightness. The types 7015 and 7025 in particular are ideally suited here with a certified leakage rate according to the Technical Instructions on Air Quality Control.
“In hydrogen applications – be it for production, storage or transport – every component must work absolutely reliably even under demanding conditions”, stresses Christoph Lukasik, Head of Design and Development at Schubert & Salzer. “The materials and design of our control and stop valves enable the long-term safe and cost-effective use of this key technology on an industrial scale.”
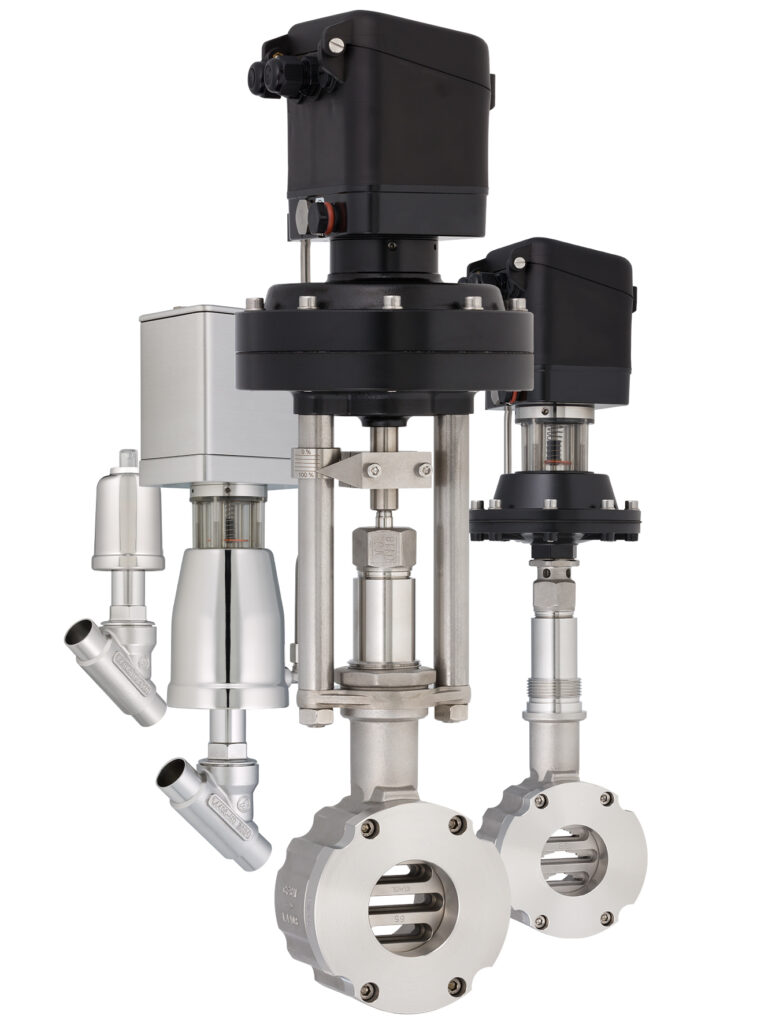