While polyethylene (PE) first entered the market in the 1950s, it was only in the 1990s that it was adopted as a material for piping systems and since then, polyethylene has become an industry standard for applications such as the transport of water and gas. There are several reasons for this development: On the one hand, its material properties make PE corrosion and maintenance-free, resulting in lower costs compared to metal. And, due to its lower weight, it is also easy to transport and install. At the same time, pipe connections are simplified thanks to jointing technologies such as butt-welding and electrofusion.
Speed, simplicity, and flexibility
Electrofusion, in particular, has proven to be a popular and efficient technology. Unlike butt fusion, which can require bulky machinery to execute, electrofusion is an effective alternative for pipe connections in trench environments or in tight spaces. In addition, electrofusion provides planners and installers more flexibility as this technique also allows for pipe connections with different material grades and wall thicknesses. It is possible, for example, to create a joint between PE80 and PE100 or a thickness of SDR 11 and SDR 17.
In order to achieve this, the ends of the two pipes are first pushed into an electrofusion fitting according to the specified insertion depth. The cable of an electrofusion machine is then attached to the pin connector on the electrofusion fitting and sends an electrical current to copper wires embedded within. The wire melts the material of the fitting and the pipe, while the resulting pressure buildup fuses them together and creates a weld after a predetermined cooling period. This process is further simplified by modern electrofusion machines that use a bar code scanner to input the correct welding parameters and alerts the operator with error messages should an issue arise. As a result, electrofusion minimizes risks and ensures a high quality thanks to repeatability. And, in addition to welds using couplers, electrofusion allows installers to attach saddles and fittings with the same technique.
The challenges of electrofusion
Like butt fusion, it requires a dedicated, yet simple, preparation phase that must be carried out correctly. In order to create perfect connections, installers should therefore avoid deviations from the recommended welding procedure. Problems may include misaligned pipes, contaminated surfaces prior to welding, or poor scraping. This is due to the fact that bad alignment can cause the pipe ends to move during fusion which leads to a short circuit of the copper wires and poor welding quality. Scraping issues are also common as removing too much material can lead to unwanted gaps between the pipe and fitting, while not removing enough material may lead to a residual layer of deteriorated PE. Finally, contaminated weld areas mean that foreign substances are embedded between the pipe and fitting, which can impact the integrity of the joint.
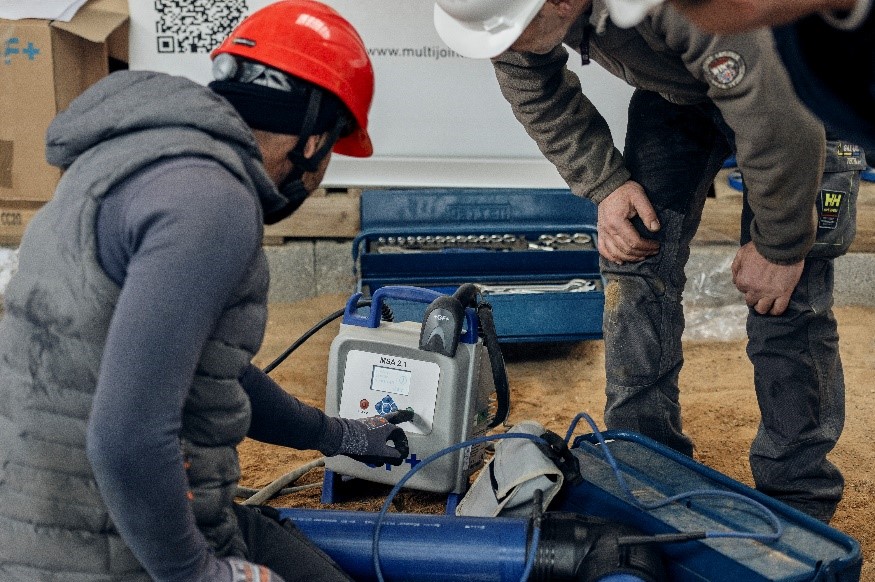
Precision leads to success
The good news is that electrofusion is a simple and intuitive process, and mistakes are easily avoidable. Following a thorough checklist allows any installer to unlock the benefits of using electrofusion to connect polyethylene pipes. These checklists may vary between manufacturers, just as countries might apply different standards on building sites. The following are some best practices based on the installation guide for the ELGEF Plus range by Swiss flow solutions provider GF Piping Systems:
- Manual
Due to differences between manufacturers, it is essential to observe the installation manual closely before beginning the electrofusion procedure. - Welding environment
To ensure the best possible results, installers must take their environment into account. Relevant factors are weather conditions such as rain and wind, or possible contaminants such as clay, dirt, and bentonite. In addition, pipes should be cleaned with clean water and rags. - Inspection
Before beginning the welding process, it is important to inspect the pipes. This includes checking both the OD (outside diameter) and SDR (standard dimensional ratio), the pipe surface, pipe ovality, and reversion. Accordingly, pipes that are undersized, feature flat spots, exceed ovality, feature a tapered edge, or any type of damage, should be rejected or adapted, if possible. Similarly, the fitting must be also checked for compatibility, SDR, and resistance. - Cutting
When cutting the pipe, it is necessary to check the angle with a builder’s square to ensure 90°. After cutting, the pipe ends should be deburred to remove swarf and sharp edges. - Peeling
The correct peeling length is determined by measuring half the length of the fitting and adding 10mm. During the peeling process, installers must check that the peeling tool is sharp and measure the peel strip thickness to ensure that it is within the specified tolerances. Depending on the manufacturer, tools developed specifically for the electrofusion system may be available, and it is also best practice to make peeling records. For electrofusion, GF Piping Systems recommends a rotary peeler as well as a micrometer with 0.01mm accuracy. This ensures that installers achieve a constant wall thickness removal of <= 0.2mm. Additionally, an even chip formation and the required minimum pipe diameter need to be taken into consideration. - Cleaning
The freshly peeled surfaces must be treated with manufacturer-approved PE cleaning alcohol and lint-free wipes, without exceeding the peeled zone to prevent contamination. Installers should only wipe away from the pipe end and not back and forth. After this step is completed, the cleaner must completely evaporate before continuing. - Alignment
To assist the alignment process, it is recommended to measure half the length of the fitting and then to mark the pipe end four times around its circumference. It is recommended to only unpack the fitting directly prior to insertion and to avoid touching the welding zones. After insertion, the pipe is then held in place by alignment clamps, allowing the installer to make sure the gap is even and does not exceed a specific size. - Welding
After the welding machine has been connected and the fusion process has begun, it is important to focus on several parameters, such as the correct welding and cooling times as stipulated by the manufacturer, or error messages displayed on the machine. The alignment clamps should also stay in place until the cooling time has elapsed. - Final inspection
Following the welding process, a visual inspection allows installers to check for mistakes such as molten polymer that has extruded from the socket mouth or visible heating wires in the gap along the pipe’s circumference. Rising fusion indicators on the fitting confirm that sufficient energy has been applied.
Conclusion
For many applications, electrofusion is a fast, easy, and flexible solution. It can be used in tight spaces where butt fusion machines cannot be implemented, while modern welding machines reduce the workload for installers thanks to intuitive interfaces, data storage, and barcode scanning. At the same time, the success of electrofusion also depends on the preparation phase. Negligence can impact the quality of welds and lead to pipe failures in the short and long term. In order to prevent these costly and avoidable issues, it is therefore important to create awareness for best practices in the industry.
Outlook:
How can planners and installers further improve the quality of electrofusion welds? In part two of the electrofusion article series, experts from GF Piping Systems’ sales companies in Denmark and Australia will discuss their experiences assisting customers and the benefits of electrofusion training.