Bredel hose pumps are contributing to a sustainable solution for steam potato peeling provided by TOMRA Food which reduces water usage, water treatment and food waste.
The TOMRA Dry Peel Separator (DPS) uses Bredel as a dry-waste pump which enables food processors to reduce water usage and recover the potato skin and starch for use in animal feed or anaerobic digestion (biogas).
The steam peeled skin is separated using centrifugal force inside the TOMRA DPS and avoids the need for brush separators and water. From a drum that rotates at high speed, the peel waste flows to the Bredel hose pump, which transfers the material to the food processor’s storage location.
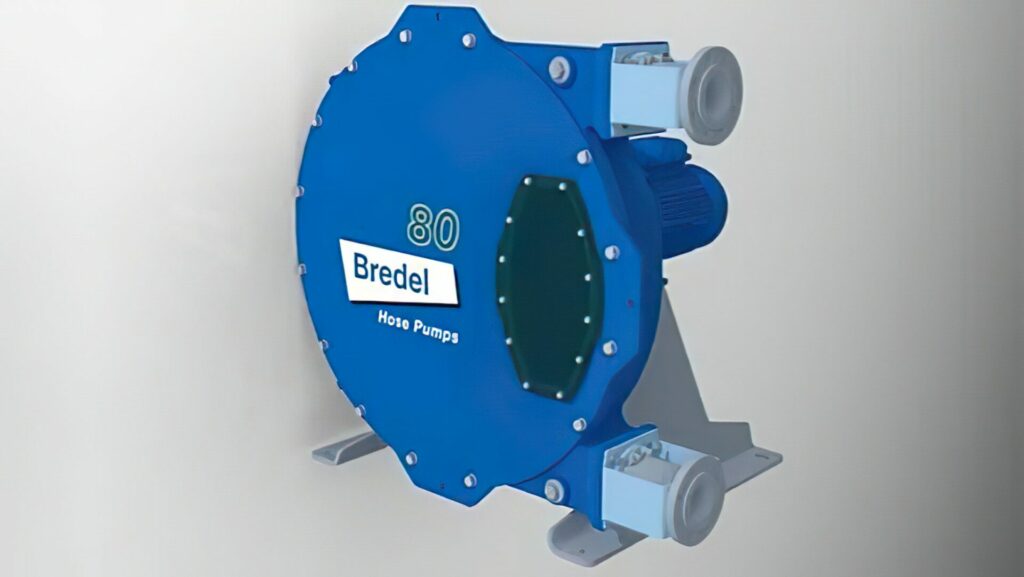
Bredel, crucially, minimises downtime and maintenance while handling steamed vegetable skin waste which contains high concentrations of solids, dirt, grit and sand. This makes the peel slurry not only viscous, but abrasive.
Eamonn Cullen, Market Manager Peeling at TOMRA Food, says Bredel plays a key role in TOMRA’s sustainable solution for an efficient, reliable and profitable potato peeling solution.
He said: “There are a number of advantages with using the Bredel hose pump. The ability to pump peel without the addition of water is one. The ability to pump hot, abrasive, steam peeled skin and starch is another.
“The main benefit that we experience is customer satisfaction. Today, food processors are processing higher volumes and they are faced with fewer opportunities to stop the line. Reduced maintenance and high reliability is vital and this a major reason why processors choose TOMRA. The Bredel hose pump is a part of the TOMRA solution and we see a very good fit with the TOMRA DPS solution and the Bredel pump solution.
“Pumping systems in food processing facilities are the unsung heroes of the process. They operate consistently and reliability day after day. If a blockage occurred or an unexpected breakdown occurred, the line would be forced to stop which would result in a huge cost to the food processor.
“If you also consider the factory workers, who would be tasked with removing this blockage and cleaning up, they would be required to stop the important work that they do to assist with the draining and cleaning of the pump and the associated pipework. You can imagine how difficult this task would be and how it would impact the day-to-day work inside the factory.”
Minimises waste and offers biogas opportunity
TOMRA’s unique Peeling line solution is capable of separating steam peeled skin from 50,000 kg/hr of steam peeled potatoes, with <5% peel loss, and 40,000 kg/hr of steam peeled carrots. This equates to capability of processing more than 2,000 kg/hour of peel.
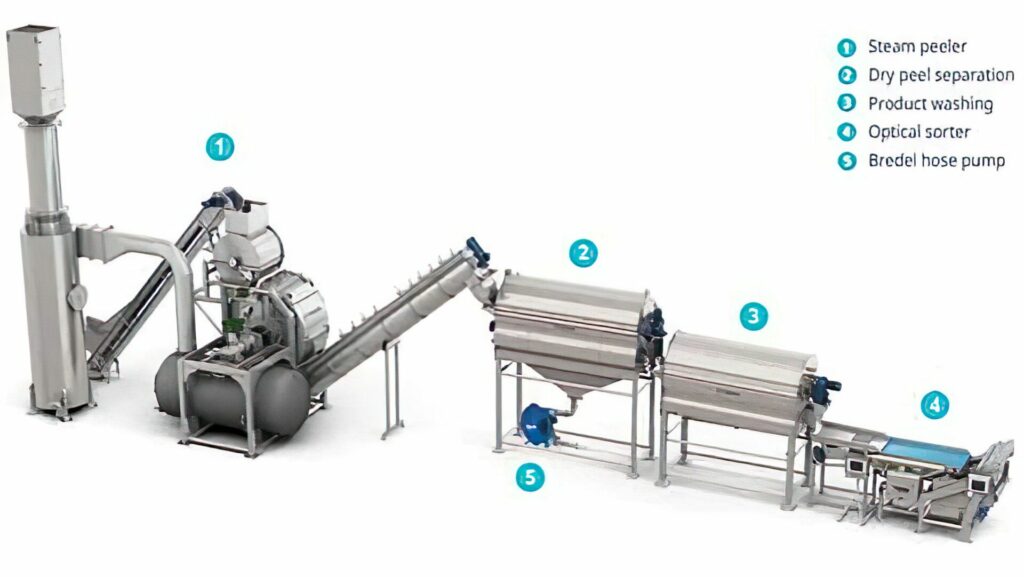
Today, 85% of the world’s French fries are processed by various TOMRA equipment, according to TOMRA, and its range of peeling solutions are used by the likes of Lamb Weston EMEA. Deploying a DPS makes a food processor’s operation more efficient and minimises food waste.
Eamonn Cullen, Market Manager Peeling at TOMRA Food, said: “TOMRA is continuously innovating and searching for new technologies to help businesses to reduce waste. The result of this in food, is that the use of every piece of food entering the supply chain is maximised to extract its full potential and to minimise waste. This is better for the environment, better for business and leads us to more sustainable business processes.
“The majority of potato processing facilities will collect all steam peeled skin in dry form. Some processors still need to use water in the peel separation brush machines, but this is reducing every year. It has become an important key performance indicator for the food industry to reduce water usage, to reduce food waste and to improve sustainability.
“Collecting the steam peeled skin and starch dry enables this material to be used in other parts of the value chain. It can be farmers feeding animals or anaerobic digesters changing biomass into biogas. These opportunities help maximise the utilisation of every part of the potato and make every potato count.”