Temperature transmitter vs RTD input modules:
Temperature measurement is a critical component in process automation, as temperature can affect many chemical, physical, and biological processes in industrial settings. Temperature measurement provides important data for process control, optimization, and safety. Accurate temperature measurement is necessary to achieve desired product quality, reduce energy consumption, and minimize product waste.
Whether your application is using an RTD or a thermocouple, the temperature sensor will need a connection to your control system – either via direct wiring to an input module in the DCS or PLC, or via connection to a separate temperature transmitter. At first glance, it may seem easier to skip a transmitter altogether and wire temperature sensors directly, but temperature transmitters provide substantial benefits.
You might use a temperature transmitter instead of an RTD/thermocouple input module for a few reasons:
- Remote sensing: If the temperature sensor is located far from the control room, a temperature transmitter can be used to convert the sensor output into a signal that can be transmitted over long distances without losing accuracy. In the case of thermocouples, using a temperature transmitter will reduce the cost of wiring, as you can use simple twisted-pair wiring instead of expensive thermocouple extension cable.
- Standardized output: Temperature transmitters provide a standardized output signal, such as 4-20 mA or HART protocol, which can be easily read by many types of control systems.
- Signal conditioning: A temperature transmitter provides signal conditioning that can improve the accuracy and reliability of the temperature measurement. The transmitter can provide linearization, cold junction compensation and other signal conditioning functions that are not available in a basic input module.
- Flexibility: Temperature transmitters can be used with a wide range of temperature sensors, including, RTDs, thermocouples, and thermistors, allowing for greater flexibility in system design and easier integration into existing systems.
- Maintenance and diagnostics: Temperature transmitters can be easier to maintain than an input module. The transmitter can be calibrated and configured remotely using digital communication protocols, reducing the need for on-site maintenance. Additionally, the digital communication capabilities of a temperature transmitter can improve system integration and provide advanced diagnostic and troubleshooting features.
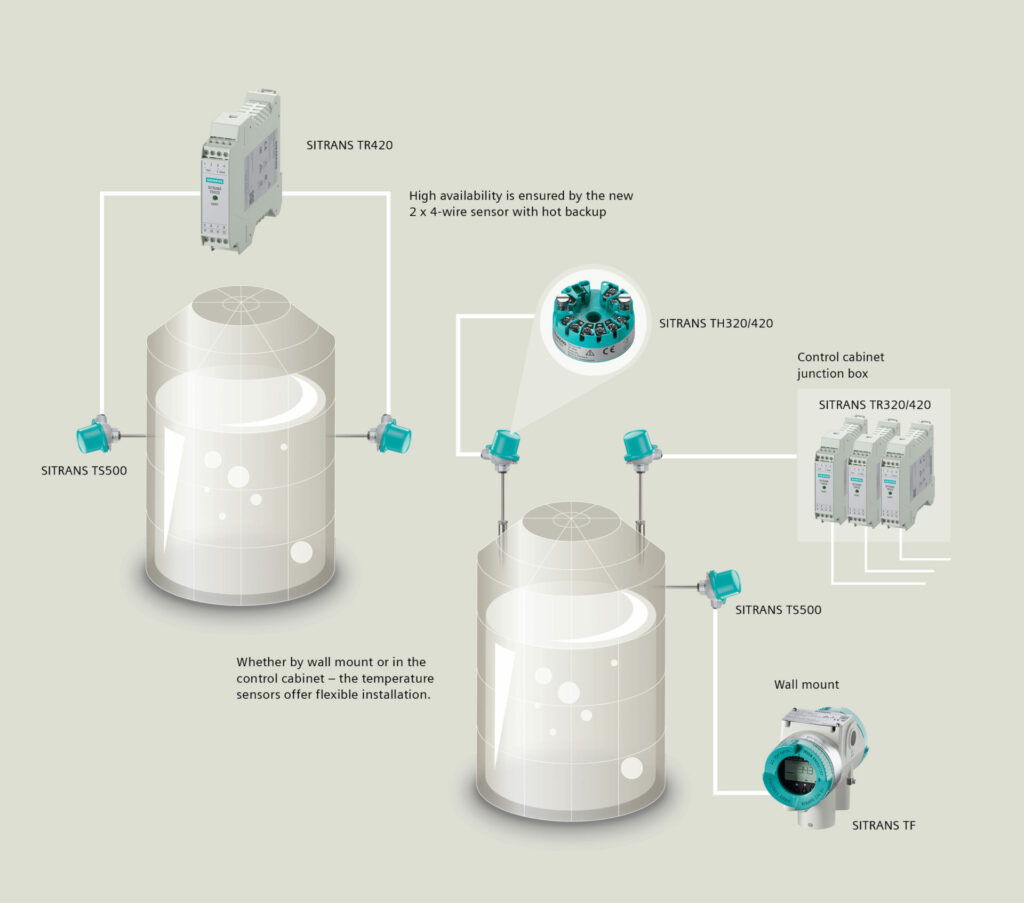
Dual sensor input – hot backup
Temperature transmitters with dual sensor inputs, like Siemens’ SITRANS TH420 and TF420, bring even further enhancements to a temperature control loop. They provide redundancy and increased reliability, particularly in hot backup applications via safe sensor switching capability.
In hot backup applications, it is critical that the temperature sensor is always working and providing accurate readings. If the primary sensor fails or requires maintenance, a secondary backup sensor can be used to ensure that the temperature transmitter measurement is still available. The dual sensor inputs in the TH420 and TF420 transmitters allow for both the primary and secondary sensors to be connected to a single transmitter, providing a reliable and redundant system. The transmitter will alert if either of the sensors fails, making sure your backup is always ready.
With automatic, safe sensor switching, the output of the TH420 will not be interrupted upon failure of either the primary or secondary sensor. If the primary sensor fails the transmitter will automatically switch to the secondary sensor, ensuring that the process is not interrupted, and that accurate temperature measurement is still available. This hot backup capability can help prevent costly downtime and maintain process efficiency.
Upon switching sensors used for output, The TH420 transmitter will alert that maintenance is required. Once the primary sensor is replaced or repaired, the transmitter’s output will automatically switch back to the primary sensor with no reset or power-cycle required. If there is a situation where the secondary sensor fails before the primary sensor, the transmitter will still provide an alert, letting you know that maintenance is required to restore the measurement redundancy functionality.
It is common to use dual RTDs or thermocouples with single-input transmitters. However, upon failure of the primary sensor, the leads for the failed primary sensor must be manually disconnected and replaced with the leads from the backup sensor. There is no way to determine the integrity of this backup sensor until it is connected. In high-vibration or high-temperature environments, when one sensor has failed, it is very likely that the other is not far behind… if it hasn’t failed already. Monitoring both sensors independently with a dual-input transmitter increases the reliability of the measurement system.
Dual sensor input – sensor drift monitoring
In addition to safe-switching backup functionality, the dual-sensor TH420 temperature transmitter can be configured to monitor for drift between two sensors. RTDs are susceptible to changing resistance over time, which impacts the accuracy of the measurements.
One of the main causes of RTD drift is material degradation, which can occur due to exposure to high temperatures or chemical agents. As the RTD’s material degrades, its resistance can change, leading to drift. This degradation can occur at any point in the sensor circuit, as in the sensor itself, the lead wires, terminals, and extension wiring. Another cause of RTD drift is aging, which can occur due to the repeated cycling of the process temperature. As an RTD is repeatedly exposed to high temperatures and then allowed to cool, the repeated thermal expansion and contraction of the sensor can cause the material to fatigue, leading to changes in resistance over time.
With drift detection activated, The TH420 monitors both sensors under a defined drift threshold, for example +/- 5F. If the difference between the two sensors drifts outside of this configured differential, the transmitter will communicate that the system is starting to degrade. This alerts operators and technicians that recalibration or replacement may be necessary… before either sensor fails.
For additional dual-sensor functionality, the transmitter can also be configured to output the difference between two sensors (useful in applications like heat exchangers, reactors, and even HVAC) or the highest, lowest, or average value between the two sensors.
Mixed-type sensor inputs
Using both an RTD and a thermocouple as redundant sensors in process automation provides a backup measurement in case of a sensor failure or drift and helps improve the overall accuracy and reliability of the temperature measurement.
RTDs and thermocouples are two different types of sensors that work on two different principles. RTDs measure the change in resistance of a metal wire as the temperature changes, while thermocouples work by measuring the voltage generated between two dissimilar metals as the temperature changes. Both sensors have their own strengths and weaknesses, but by using both in tandem, you can mitigate the potential drawbacks of each type of sensor and improve the overall performance of the system.
For example, RTDs provide stable and accurate measurements over a wide range of temperatures but can be more susceptible to drift and require a longer stabilization time. In contrast, thermocouples are more robust and durable, and have a faster response time, but can be less accurate than RTDs.
By using both an RTD and a thermocouple in the same application, you can take advantage of the strengths and weaknesses of both sensors while minimizing the potential drawbacks. If one sensor fails or drifts out of calibration, the other sensor can provide a backup measurement and ensure that the temperature measurement remains accurate. Additionally, the combined measurement of both sensors can be used to improve the overall accuracy of the temperature measurement, as any discrepancies between the two readings can be used to adjust the measurement and account for any errors.
Conclusion
Temperature measurement and control is one of the most flexible and varied realms in the world of process automation. Between the breadth of available technologies, configurations, special features, and even suppliers, often there are no clear-cut lines defining what a temperature control loop must look like. Siemens SITRANS T family has the solution for any application, as well as the experts to help make sense of it all. From bare sensors and stand-alone transmitters to full temperature assemblies, complete with thermowell, sensor, and transmitter, we are here to help.