Understanding Thermal Mass Flow Meter Configurations
All thermal mass flow meters serve the same fundamental purpose—accurate gas mass flow measurement based on thermal dispersion principles. However, they come in different physical configurations to accommodate various installation requirements.
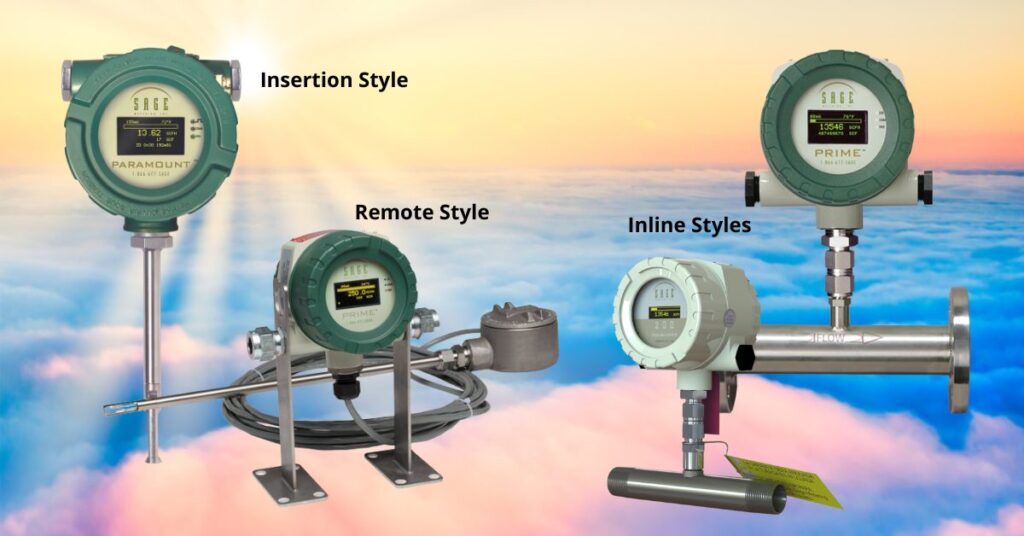
How Thermal Mass Flow Meters Work
Before discussing configuration differences, it’s important to understand that all Sage thermal mass flow meters:
- Measure gas mass flow based on the same thermal dispersion principle
- Provide direct mass flow measurement without requiring pressure or temperature compensation
- Deliver high accuracy, wide turndown ratios, and excellent repeatability
The primary difference between an inline meter and an insertion flow meter lies in how they’re installed.
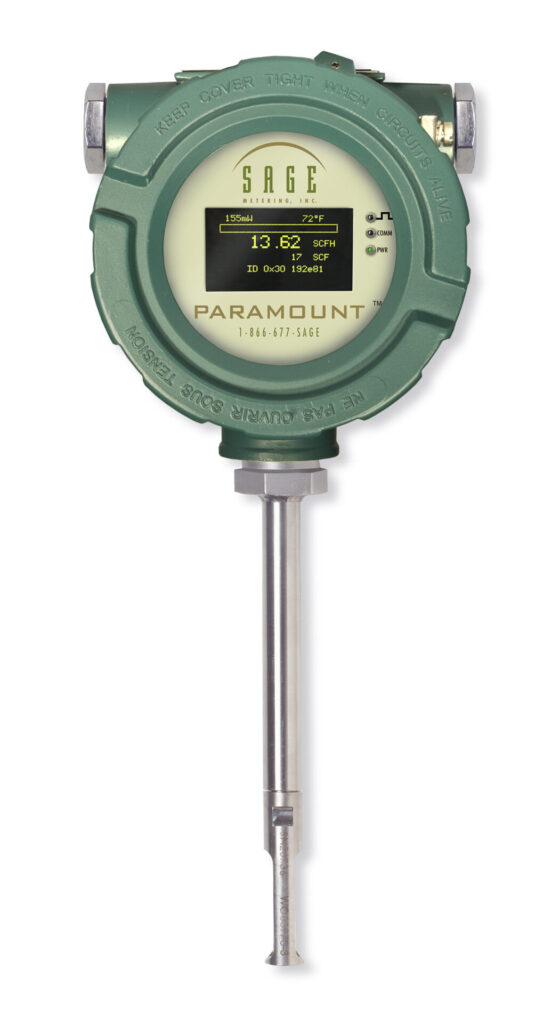
Insertion Style Flow Meters
What is an Insertion Flow Meter?
An insertion-style thermal flow meter features a probe that inserts directly into the process pipe through a valve assembly or compression fitting.
Key Features of Insertion Flow Meters:
Straight Run Requirements: Typically requires 15-25 pipe diameters of straight run upstream to achieve optimal accuracy when flow conditioning is not present
Installation Flexibility: Can be installed in existing pipes with minimal modification
Removal Without Process Shutdown: When installed with an isolation valve, the meter can be removed for cleaning or inspection without shutting down the process
Cost-Effective: Often more affordable, especially in larger pipe sizes
Adaptability: Can be relocated to different measurement points if needed
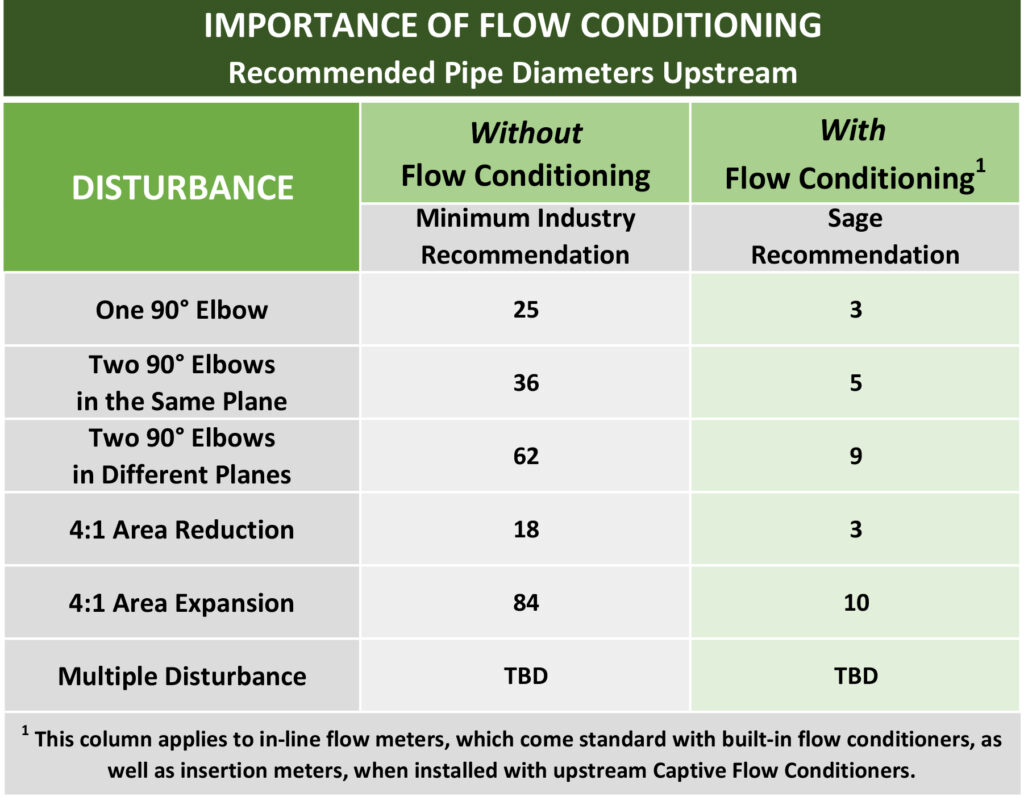
Obstructions such as valves, blowers, expanders, and PVC and HDPE pipes require additional straight run.
Optimizing Insertion Meter Performance with Captive Flow Conditioners
For applications where sufficient straight run isn’t available, Sage recommends using a Captive Flow Conditioner assembly with insertion-style meters.
The Captive Flow Conditioner assembly consists of:
- Two flow conditioner plates positioned between two flanges
- A mounting point for the insertion meter
- An engineered design that creates a uniform flow profile
Benefits of using a Captive Flow Conditioner:
- Reduces straight run requirements significantly
- Creates a consistent measurement profile even in non-ideal piping configurations
- Enables insertion meters to achieve accuracy comparable to inline meters
- Maintains measurement integrity in space-constrained installations

Inline Flow Meters
What is an Inline Flow Meter?
The inline (or in-line) flow meter includes a complete flow body that integrates into your process line as a spool piece.
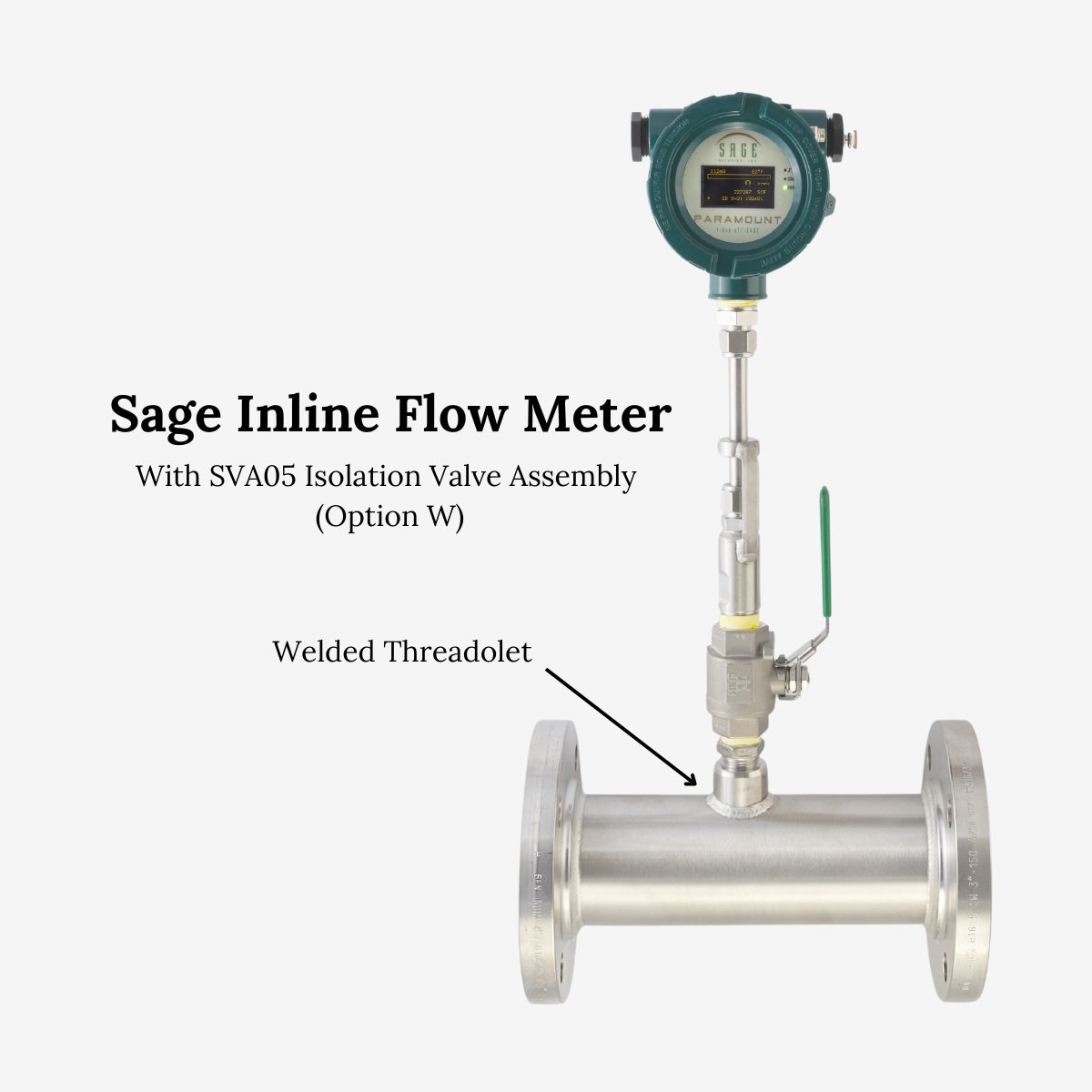
Key Features of Inline Flow Meters:
- Built-in Flow Conditioning: Integrated flow conditioning elements optimize gas flow profiles
- Reduced Straight Run Requirements: Significantly reduces requirements when compared to a meter without flow conditioning
- Optimized for Small Pipes: Particularly effective for pipe sizes under 2 inches in diameter
- Fixed Position: Permanently installed at a specific measurement point
- Precision Engineering: The flow body is designed specifically for the application’s flow range
Remote Configuration: Enhancing Access and Readability
Both inline and insertion meters are available in remote configurations, where the electronics and display are separated from the sensor.
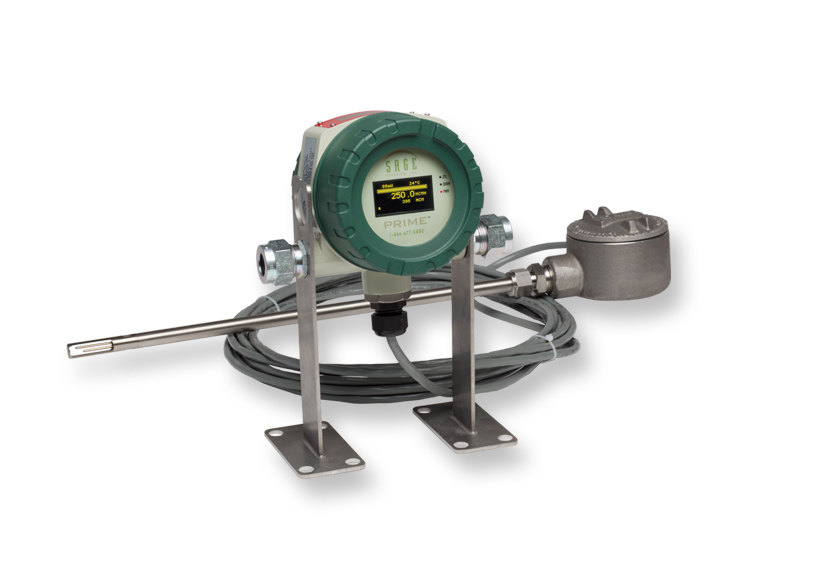
Benefits of Remote Configuration:
- Display can be mounted in an easy-to-access location
- Sensor can be installed in hard-to-reach or hazardous locations
- Available with up to 1000 feet of lead-length compensated cable
- Ideal for high-temperature applications or areas with excessive vibration
Selection Guide: Which Configuration Is Right for Your Application?
When selecting between inline and insertion configurations, consider:
- Pipe Size:
- Smaller pipes (under 2 inches): Inline typically preferred
- Larger pipes (2 inches and above): Insertion is often more economical
- Installation Constraints:
- Limited straight run: Inline or insertion with Captive Flow Conditioner
- Need for occasional removal: Insertion with isolation valve
- New installation vs. retrofit: Inline for new, insertion for retrofit
- Budget Considerations:
- Initial cost: Insertion is typically lower, especially in large pipes
- Installation cost: Insertion usually requires less modification
- Long-term maintenance: Both have excellent longevity with no moving parts
- Application Requirements:
- Highest precision needs: Either configuration when properly installed
- Temporary measurement: Insertion with compression fitting
- Permanent installation: Either configuration is suitable
Expert Support for Your Application
At Sage Metering, our representatives are extensively trained to help customers select the optimal configuration for their specific gas measurement applications.
To discuss your application and determine the best flow meter configuration submit your flow meter inquiry.
Related Resources
- Mass Flow Meter Installation Considerations
- This article was originally published by Sage Metering.