Introduction
Not many years ago, cryogenics – the production and behavior of materials at very low temperatures – was likely to be understood by a group of people with specialized knowledge in fields like aerospace.
Working with cryogenic applications means working with systems and components that have very special design and performance requirements. The costs associated with manufacturing and testing can be extreme. For these reasons, relatively few manufacturers have become adept at developing and commercializing cryogenic products that can meet the performance needs of the end user, at a price point that is practical.
What Makes Cryogenic Product Development Such a Challenge
By their very definition, cryogenic products need to perform in extreme low-temperature environments. For liquefied natural gas (LNG), the process of liquefying the gas reduces the volume by 600 times, making it far more economical to transport aboard LNG carrier ships to destinations around the world.
The temperature required to liquify natural gas is -260°F (-162°C), which means that most pipe, valves and fittings are specified to exceed that cryogenic temperature – typically in a range from -270°F to -325°F (-168°C to -198°C) (see Fig. 1).
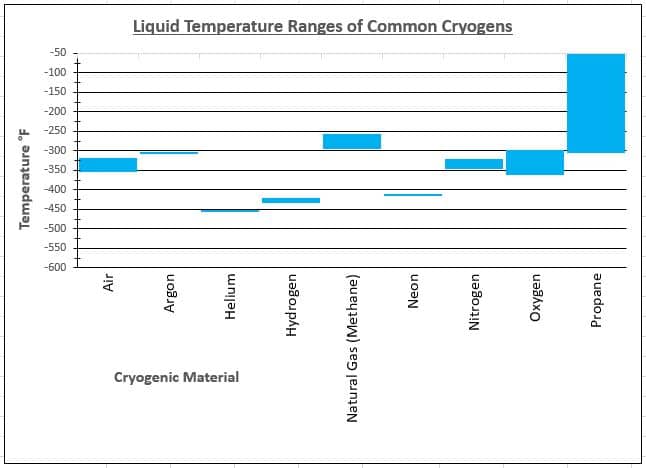
Fig.1: Liquid Temperature Range of Common Cryogens
Beyond low temperature requirements is the need for the materials to work well in ambient temperatures, too. Being able to withstand frequent temperature fluctuations along with durability is essential. This means that cryogenic products must be made of low- or no-shrink materials that maintain (or even increase) their strength in extreme low temperatures.
Sealing Methods and Materials
There are several different types of cryogenic seals including primary, backup, and weather seals. Common to all of them is the need to keep moisture out. Any amount of moisture will freeze at cryogenic temperatures, and any such freezing has a negative effect on bearings or any other components designed for movement.
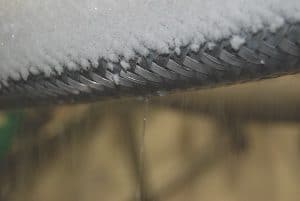
For this reason, the goal for cryogenic products is to avoid requiring lubricants to be part of the final design. Lubricants have the potential to freeze, and they can attract dust – two ‘evil things’ in a cryogenic application.
A fundamental consideration when designing products for cryogenic use is whether the required seal is static or dynamic. Is the product required to seal two surfaces that never move in relation to each other, or are the sealing surfaces going to be moving in relation to adjoining surfaces?
If it’s a dynamic seal that’s needed, the next consideration is the direction and the relative motion that will be happening – axial, radial, circumferential or something else.
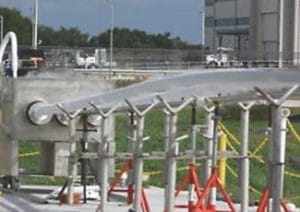
This image dramatically shows the impact on piping during a cryogenic cooldown period. Note the bowing of stainless steel pipe due to uneven thermal contraction. Designing products to operate properly in cryogenic conditions will reduce the risk of pipe failures due to stress.
This is where material selection becomes critical. The proper choice of materials is determined by those requirements and by temperature excursions (defined as outside a given range) – warmer to colder and back again. The incidence of thermal cycling is also important because products need to work hundreds or thousands of times, without the material taking on a different shape in the process.
The key is to have all the performance factors working together in an intricate manner – and all the permutations must be designed and carefully tested to achieve a design that works not only well, but well over time.
As for the materials usually specified for products and components designed for use in cryogenic environments, austenitic type 316 stainless steel is a frequent choice, along with UHMW (ultra-high molecular weight) polyethylene, Teflon™ as well as other fluoropolymer and fluorosilicone materials.
Stainless steel is a good material choice because of its strength. Its properties change very little with temperature excursion; indeed, stainless steel becomes stronger as it gets colder. Moreover, it is a non-corrosive metal.
Brass can be an acceptable choice of material, too. It is often found in fittings on cryogenic products – particularly those providing static versus dynamic sealing service.
Teflon™ has the fortunate characteristics of gradually increasing tensile strength, and gradually increasing tensile and compression modulus as temperature decreases. In addition, Teflon™ exhibits low creep (when confined) and a low friction coefficient, and is also a good thermal insulator. Unlike straight silicones, fluorosilicone at low temperatures is low shrink, has a low compression set and resists swelling.
The choice of materials is also influenced by the pressures under which the components will be operating. When kept in storage, LNG is not a highly pressurized substance. But for LNG to be pumped or gasified, a cryogenic product will need to be able to withstand much higher pressures. The Compressed Gas Association has issued guidelines for CGA brass fittings that help end-users know if the products they are considering will provide the level of performance and safety they need.
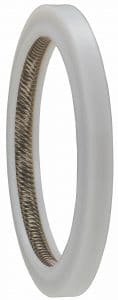
Small diameter gasket
Manufacturers have generally settled on brass, stainless, and PTFE materials for cryogenic applications. Initial testing with rubber compounds like Buna were not successful. The properties associated with nitrile materials cannot withstand the temperature requirements, and become brittle and crack. When modifications are made for the material to stay flexible, swell resistance to oils and fuels becomes compromised.
Many other sealing materials have proven to be substandard performers in cryogenic temperature environments. Silicones have low abrasion and tear resistance, and are low tensile strength – all of which represent inferior qualities for dynamic sealing applications. Fluoroelastomers like FKM (Viton®) can suffer from rapid decompression damage, high compression set and high glass transition temperature when compared to other elastomer materials.
Little Tolerance for Big Tolerances
When designing products for cryogenic service, engineering tolerances are a critical factor in determining performance levels. In the general industrial arena, it isn’t uncommon to find customers accommodating tolerances of 0.05 inches or even greater. That doesn’t cut it in the cryogenic world, where customers have tolerance requirements of 0.02 or even 0.01 inches along with correspondingly smooth surface finishes.
Considering that two components may need to be operating in concert, the negative impact of tolerances can be magnified if each component is at “opposite extremes” on the tolerance score.
Here again, a balancing act is required on the part of component makers in figuring out how to achieve extremely tight tolerances without manufacturing costs skyrocketing.
Surface Appeal
Surface finishes are another important consideration in the design of products for use in cryogenic environments. The smoother the surface finishes are, they allow mated components to work with less (or no) lubrication. The components won’t degrade as quickly, either.
Determining the best finish specs depends on each product’s intended function and what kind of environmental conditions it will experience. For example, a surface that is required to retain a cryogenic fluid under “dynamic” conditions – as the component moves or rotates or flexes in some way – will require a higher degree of surface smoothness or polish compared to a component that doesn’t require performance in such extreme temperatures, or that is merely performing the function of preventing dust or moisture ingress.
Typically, surface finishes required in the cryogenics range from 6 to 12 micro-inches, as compared to 32 micro-inches or greater in more typical industrial applications.
For product designers, practical considerations mean achieving the desired surface finishes right off the lathe, rather than having to undertake subsequent burnishing or polishing operations. In some cases, manufacturing considerations such as this might mean the difference between introducing the new product or not (see Fig. 2).
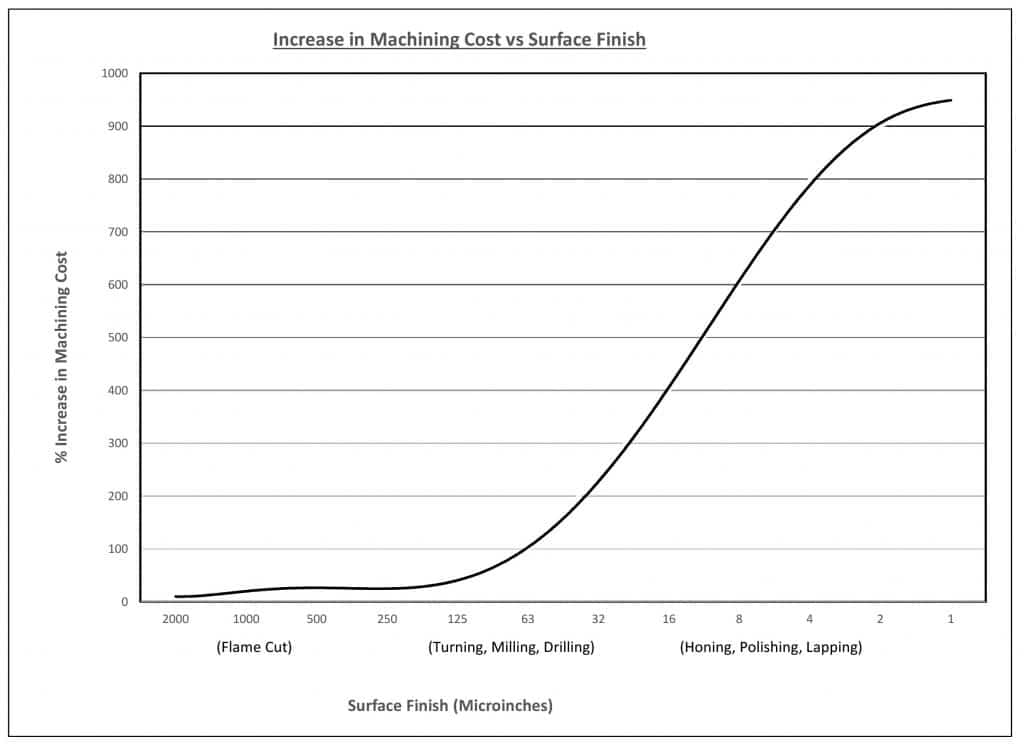
Fig.2: Increase in Machining Cost vs Surface Finish
Design is Only the Beginning
As with other industrial products and components, designing them is just the first step; following design engineering is prototyping, in-house testing and field testing. Beyond product testing in extreme temperature environments, rigorous cycle testing is important in the cryogenic world. Any new products must meet stringent cycle testing guidelines prior to bringing it to a customer location for “real world” testing in the field.
But even with those assurances, in the rapidly- evolving “new world” of cryogenic facility operations it’s only natural that some people will have trepidation about testing a new or improved way of operating. Demonstrating extraordinary knowledge, diligence and discipline in the product development process will go a long way towards convincing these early adopters – and others following them that the improved efficiencies of cryogenic operations far outweigh the risks of trying something new.
Dixon Innovation Center
The Dixon Innovation Center in Chestertown, MD is one of the few places in the world where research on products and systems for cryogenic service is happening. A specially designed cryogenic workstation at the Center allows for R&D testing and repair in environments that replicate those encountered “real-life” in the field. The workstation uses liquid nitrogen to test product designs – a substance that is even colder than liquified natural gas.
Engineers at the Center are committed to providing more than “standard” product solutions. It begins with carefully studying products already in use in the field – then using that knowledge to create new products that are practical in their application and that often possess unique performance characteristics.
Cryogenic product development can’t be rushed, as each aspect of materials selection, sealing functionality, surface finishes, cycle testing and other key performance factors are developed.
Working in concert with ISO specifications, ASTM specifications and other outside specs that pertain to cryogenics, Dixon’s own specs are developed – and these can be more stringent. It’s part of the commitment Dixon has made to perform and control all key steps in the development process for cryogenic products: designing, testing and fabricating.
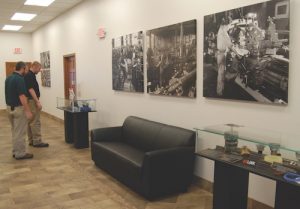
The Dixon Innovation Center also offers cryogenic design workshops and classes for engineers and operators, led by leading technical specialists. Customers, fellow manufacturers, and key end-user personnel from entities like shipping companies and port facilities are also welcomed to the Center to consult with Dixon engineers in evaluating and designing products and systems that will meet their specific requirements.
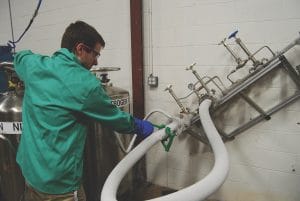
Dixon’s engineering expertise goes beyond developing products. The company is also being tapped by the American Society of Testing and Measurement (ASTM) in its endeavors to establish specifications for LNG bunkering systems. Those specifications are currently under development by the F25 Committee on Ships and Marine Technology’s LNG working group.
Dixon specialists serve on the U.S. Coast Guard’s Chemical Transportation Advisory Committee (CTAC) Sub- Committee on LNG, which is working in concert with the Coast Guard to identify gaps in existing policies and regulation that pertain to the design of LNG vessels, and to develop criteria to fill those gaps.
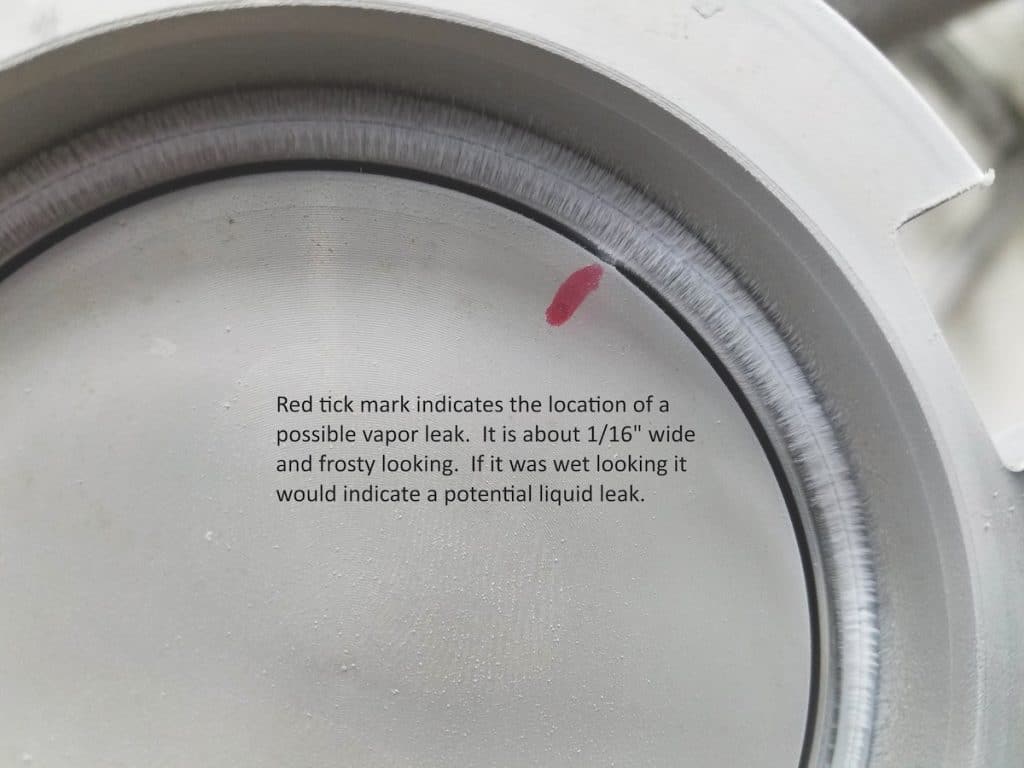
The cryogenic workstation at the Dixon Innovation Center enables design engineers to test and evaluate products, as in this example of checking a product prototype for a potential vapor leak.
Find Solutions at the Source
In the cryogenic environment, often it’s confronting challenges in the field – literally – that leads to new answers and new solutions.
As a recent example illustrates, one of Dixon’s customers was experiencing problems while using bunkering connections during the transfer of liquified natural gas. Technical specialists from Dixon were called to the scene to witness the next bunkering operation and assess the situation.
As a recent example illustrates, one of Dixon’s customers was experiencing problems while using bunkering connections during the transfer of liquified natural gas. Technical specialists from Dixon were called to the scene to witness the next bunkering operation and assess the situation.
During the pre-dawn bunkering procedure, the Dixon specialists noted intermittent performance problems with the coupling. Unfortunately, quick-fix attempts “on the scene” were unable to correct the issues. So, it was time to bring the coupler to the Dixon Innovation Center for more rigorous testing. That testing found that the high side loads on the coupling were causing performance issues at certain points of the LNG bunker cycle. Further evaluation determined that the addition of extra support bushings would greatly increase the side loads that could be applied to the coupling. As a result of that discovery, machining was done to the coupler along with the addition of the bushings. Next, in-field repair kits were prepared and shipped to all affected customer locations.
The entire process from original call to the delivery of repair kits happened within a matter of weeks. In addition to the quick turnaround Dixon was able to provide, this customer was able to solve a significant problem without having to make changes in the way it performs its bunkering operations – thereby maximizing work efficiencies and eliminating the need for employee retraining.
Dixon Experts
Sean Andersen is a product manager and LNG Specialist at Dixon. In addition to working closely with customers to evaluate, design and deliver custom LNG transport and bunkering systems, he is active in numerous industry organizations and societies. He is currently a member of the Chemical Transportation Advisory Committee (CTAC) Sub-Committee on LNG and the American Society of Testing and Measurement (ASTM) committee that is developing specifications and requirements for LNG fueling. Click here to contact Sean
Jim Shifrin is Manager of Engineering Innovation at Dixon. He oversees a staff of engineers and other specialists at the Dixon Innovation Center – a facility expressly built for the mission of commercializing “first-ever” products and bringing them to market. On average, the Dixon Innovation Center commercializes five new product introductions per year, along with harnessing new technologies such as 3D printing that bring added efficiencies and cost savings to the manufacturing process – and to customers. Click here to contact Jim