Yet, in municipalities approximately 6 billion gallons of water are lost to leaks every day, and inefficient energy practices result in excess energy costs of up to 30 percent.
The nation’s aging infrastructure includes over 2 million miles of water distribution pipes, most of which are past their life expectancy. These old water pipes remain largely untouched until a major burst draws attention. This means leaks can go unnoticed until a significant break occurs in the leaking section of pipe. Along with the estimated 240,000 water main breaks that occur each year, leaks and smaller breaks add up to a water loss between 14% and 18% of total distribution.
In addition to the significant amount of energy used to treat and distribute the water that is lost, inefficient energy practices have a huge impact on the bottom line. Utilities are often subject to peak pricing schedules of electricity suppliers. Unfortunately for municipalities, peak water demands coincide with peak electricity demands of consumers. This increased demand means higher energy costs for pumps and therefore higher overall costs to water and wastewater plants. It is estimated that electricity accounts for 80% of municipal water processing and distribution costs – and also estimated that utilities can reduce costs between 15% to 30% by incorporating energy efficient practices.
The Solution
There are major areas where efficiencies can be maximized to impact costs, efficiencies and reduce environmental impact. Leak detection technology allows municipalities to promptly and accurately locate leaks or breaks in their distribution systems. In addition, efficient pumping algorithms built into pump controllers allow implementation of economy pumping routines to best suit electricity peak pricing. Together, this two-pronged approach results in more cost-efficient plant operation.
Leak Detection
Leaking pipes often go years without being detected. By reducing lost water through leak detection technology, utilities can realize substantial cost savings in their systems. There are many methods of identifying leaks in water systems. Leak detection is often accomplished with manual equipment or a water auditing service. These methods limit leak detection to the duration of the survey and ignore any additional leaks or breaks that may occur between inspections.
Other options include costly permanent equipment spanning the entire length of the distribution network, such as a separate network of acoustic leak sensors, in addition to existing flow meters. However, there is a simpler solution that incorporates leak detection into the flow meters located in pipelines. This solution eliminates the need to install additional leak detection equipment or perform labor-intensive manual analysis. Furthermore, leaks can be monitored on a daily basis, allowing for prompt detection of leaks.
Flow meters, such as battery powered mag meters include integrated software optimized for leak detection applications in the water industry. Leak detection alarms are set by the user to warn of any significant deviation from normal flow. The user specifies the minimum and maximum flow rates that are expected under normal conditions. If flow rates are detected outside of the set parameters, the alarm is sounded, and the operator is promptly notified.
Rapid leak detection is central to minimizing water loss due to breaks or leaks in a system, and this automated approach to leak detection allows leaks to be resolved in a timely manner. Compared to other methods, integrated leak detection allows for rapid and cost-efficient operation in a single instrument. Incorporating leak detection into your system can help regain the 14-18% of potential revenue lost annually to leaks and breaks.
Economy Pumping with Ultrasonic Level Controllers
Water treatment plants are often the largest energy consumer for municipal governments. In these energy intense processes, pumping systems account for the majority of electricity used.
According to a Department of Energy study, optimizing pumping systems can reduce energy costs by 20% or more. The first step to implementing energy efficient practices in water or wastewater systems begins with the “energy hogs,” motors and pumps. Treated water and sewage processing demands surge during times of peak electricity use, which leads to peak pricing for the energy consumed by pumping systems. Some peak pricing rates can even be 80% more expensive per kWh than off-peak pricing! In order to realize significant savings in pumping systems, it is imperative to minimize pump operation during these peak times. But how can pump routines be scheduled for off-peak times?
Using a full featured ultrasonic level controller with integrated pump control algorithms the pump control parameters that can be set to minimize pumping activity during on-peak pricing. This is accomplished by setting the schedule for peak pricing, low-level set point and high-level set point of the well in the controller. The Ultrasonic level controller will then pump the well down to the low set point during off-peak pricing, allowing for the well to completely fill when energy is at a premium. During the peak pricing periods, the controller will maintain a high level in the well to be pumped out again once the offpeak period returns. This pumping strategy greatly reduces the energy demand during the elevated rates of peak pricing and greatly improves the bottom line.
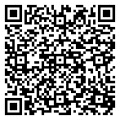
This smart approach to pumping only requires the economical investment in an ultrasonic level controller, which can control up to two motors. There are also available Cost of Water calculators, from which you will see just how much you can save by incorporating leak detection and economy pumping strategies into your plant.