The separator performance is one of the most common causes of problems and capacity constraints. Foaming, flow surges, start-up, shutdown, and flow ramping are common causes of liquid and foam carryover. Undetected liquids cost the industry £millions every year in damage, lost revenue and labour costs.
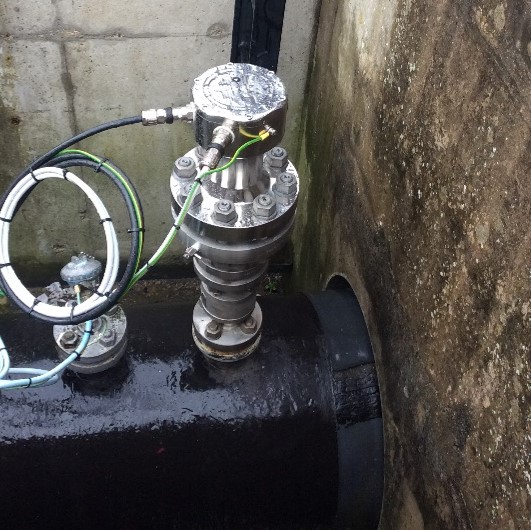
Separation systems in the natural gas industry will often have a specification for their effectiveness, but it is common that operational problems, fouling and sometimes design cause efficiency to drop significantly below the quoted specification, allowing liquids and solids to pass downstream. At the front end of gas processing, this can cause significant problems when it triggers foaming in the gas processing plant. The separation process at the back end of gas processing ensures that the processing liquids and Natural Gas Liquids (NGLs) are recovered and prevented from entering the gas export line. Therefore, the flow meters used at custody transfer points are dry gas flowmeters, and unexpected liquids and solids can cause an overread of around 5% when wet gas is present.
Using the LineVu system, a live video stream provides a view of pipeline activity at the custody transfer point. Image processing is used to provide an alarm if a mist flow, or liquids on the pipe floor, are detected. LineVu is providing a clearer picture of real-world problems when liquids and solids contaminate a gas flow. The life cycle of a contamination event has been observed on large diameter pipelines, and it does not always follow accepted thinking with fluid dynamics modelling.
When gas pipeline networks are pigged and the contents analysed, the products of glycol used in gas processing are often found. In fact, the vast majority of contamination found in gas networks has originated from gas processing systems. It follows then that the contamination has to move through the custody transfer point. Knowing when wet gas is present can give operators actionable insights to rectify the problem, and corrections can be made to flow measurements.
Recent observation has shown that solid matter and grease-like material is conveyed through the system combined with liquids moving as a slurry. This slow-moving contamination has gas rapidly moving above it and drawing off the lighter liquids leaving a dryer and slower-moving mass behind. The material becomes stationary, and further liquids are removed by the gas flow, making a stable dry mass on the pipe floor.
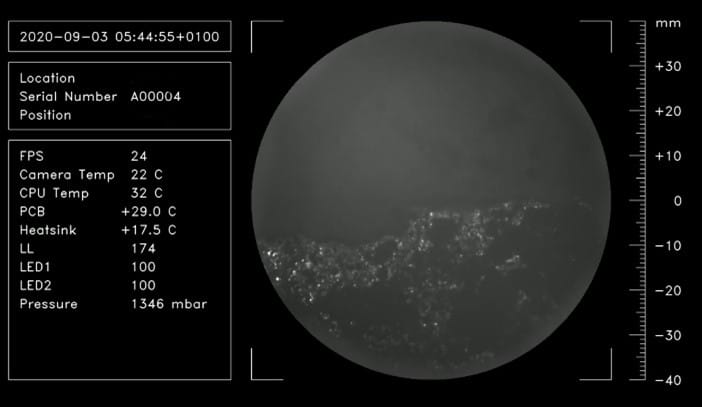
Observation show around a 3mm depth of stable contamination can be left as a permanent reminder of a contamination event. Calculations indicate that at an average-sized custody transfer point this amount of contamination would cause and an over-read of around 0.5% by the reduction in pipe diameter. This equates to around $500K per year at today’s prices.
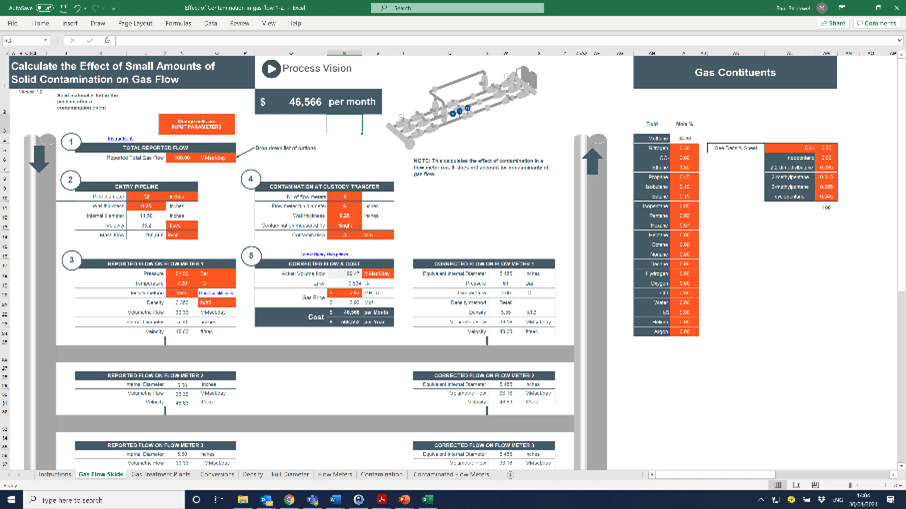