Instruments and analyzers installed outdoors are customarily enclosed in insulated boxes to protect them from both physical damage and adverse weather. Many installations of these delicate equipment require a certain temperature be maintained inside the enclosure to prevent freezing, control viscosity, or maintain precise instrument calibration. Two commonly used heating systems to provide protection against cold weather are Electric Tracing and Steam Tracing.
Electrical Trace: Using an electrical heat tracing cable normally provides excellent temperature control with integral thermostatic control but is often quite costly to operate. In addition, electrical heating systems are not suitable for use in applications where hazardous or combustible material may be present, and traced equipment is subject to freeze damage should a power outage occur or in the event of a frayed or damaged wire that compromises everything down line from the break.
Steam or Hot Fluid Trace: Steam or hot fluid tracing is a particularly ideal solution for applications where there is an existing supply of heating media, or where there are potentially hazardous or combustible materials present. This tracing system typically maintains enclosure temperatures by dressing a copper or stainless-steel tube around the inside of an enclosure or by installing a coil or finned tube heating element inside an enclosure. Steam, heat transfer fluid, hot oil, water, and even hot condensate from a steam main is circulated through the loop or heater providing the source of heat to protect the instruments from adverse weather. This normally provides excellent freeze protection but when uncontrolled can result in overheating of the instrumentation.
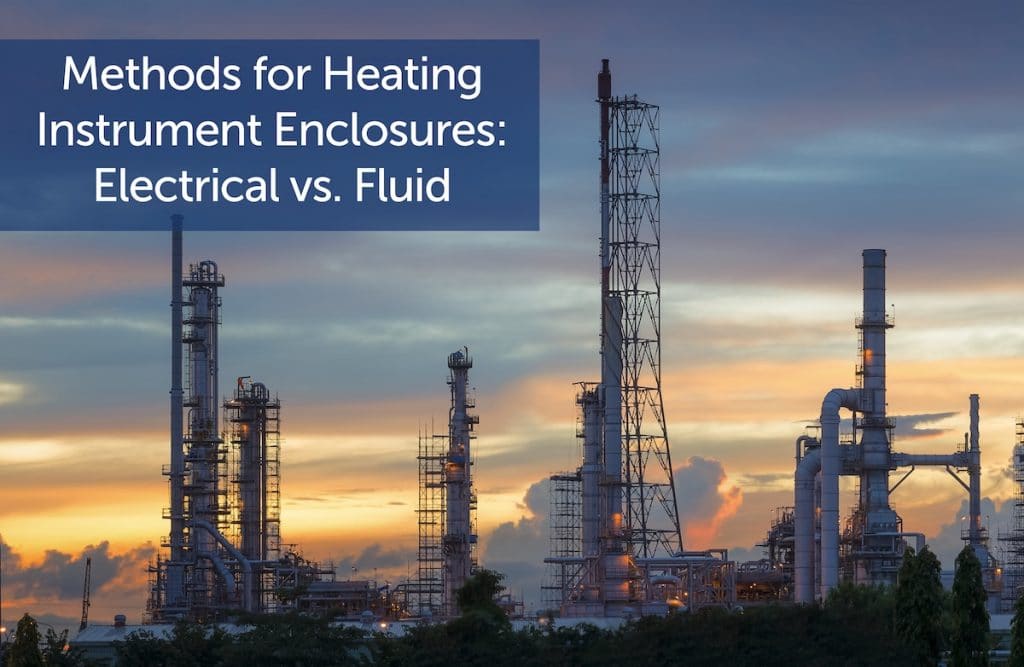
To facilitate the proper control of a steam or hot fluid tracing system, it is recommended that a thermostatic control valve be implemented. While its exact implementation may differ in terms of design, generally the thermostatic control valve will modify flow of the heating media to rectify temperature variations in the enclosure – allowing heating media to flow when the temperature is below a specific point, and curtailing flow when temperatures are above it. This allows for the instrument enclosure’s temperature to be maintained within a narrow and pre-determined temperature range, thus maintaining the integrity and continued operation of the instruments it contains.