Currently, the majority of the cooling systems are based on the use of steam compression cycles and fluid refrigerant phase changes.
The selection of refrigerant fluids is based on their heat-absorption property (calories) while they pass from their liquid phase to their gas phase.
So far, the majority of the refrigerants used were halogenated hydrocarbons because of their low toxicity and their good thermodynamic performance: CFC (chlorofl uorocarbons), HCFC (hydro chlorofl uorocarbons).
However, the Montreal Protocol dated 16th September 1987 (an international agreement intended to reduce and completely eliminate the substances that deplete the Ozone Layer and increase the greenhouse effect), which was reinforced by the Kyoto protocol dated March 2007, required the elimination of CFCs and HFCs including:
- a ban on their use as propellants;
- a requirement for enhanced sealing of the refrigeration circuits;
- a requirement for new measures to prevent bleeding and discharges into the atmosphere;
- a systematic recovery of the refrigerants.
This has promoted the use of natural fluids that are more delicate to handle but more effective from a thermodynamic point of view, such as ammonia (mainly for agricultural/food industries), carbon dioxide and hydrocarbons (propane and butane).
How do we produce cold?
Whether it’s a refrigerator or an air-conditioned car, the principle is the same : pumping the heat out of the place you want cool and evacuate it.
Heat transfer is possible thanks to the following gas properties:
- compressing a gas raises its temperature
- condensation of a gas releases heat
- the expansion of a gas lowers its temperature
- the evaporation of a liquid needs heat to be removed.
So, a compressor will compress a refrigerant fluid and therefore increase the gas temperature. The compressed refrigerant enters the condenser. The circulation of fluid in the gaseous state at high temperature in an environment with a lower temperature causes condensation of the latter. Afterwards, the operator will lower the pressure of the fluid, that will cause a temperature drop (down to -20°C). Cold fluid refrigerant is then sent into the evaporator.
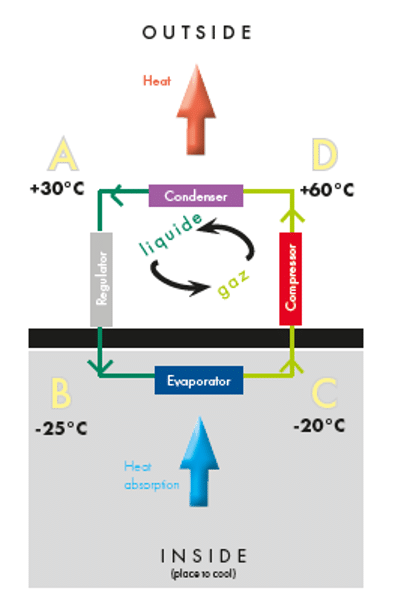
Installation
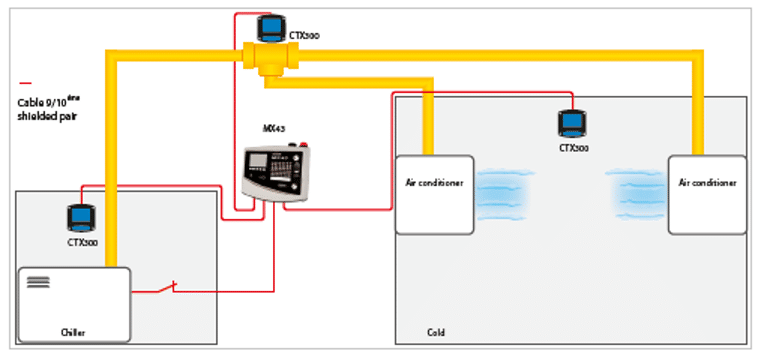
The installation rules depend on the configuration of your system, however, do not forget to take into account the density of the gases and the air flow when positioning your detectors.
The sensors must be placed at a high level, usually in the attic, in order to protect people (engine room, technical room).
Areas to be monitored: compressor zone (1 sensor per compressor), condenser zone (1 sensor per condenser), valves (if there is a risk of leakage).
Cell type: Electrochemical
Wire to be used: 1 pair 9/10th shielded (use a third if the sensor has a display).
Refrigerant gases detection installation
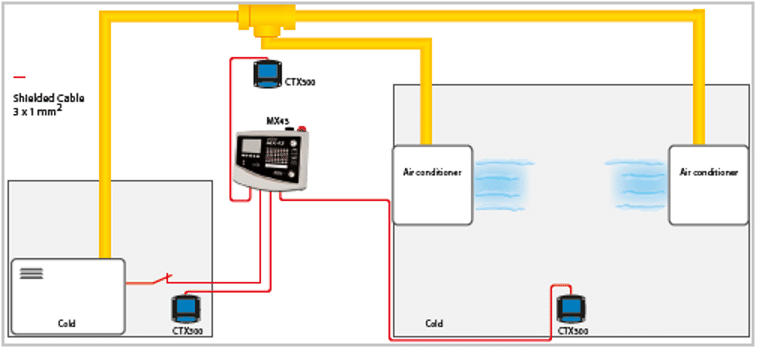
The sensors are placed near the ground level (because of the Freon density) usually in the engine room or technical room.
Areas to be monitored (where there is a risk of leakage): compressor, condenser, valves.
Cell type: Semi-Conductor
Wire to be used: 3 x 1 mm2 shielded wires.
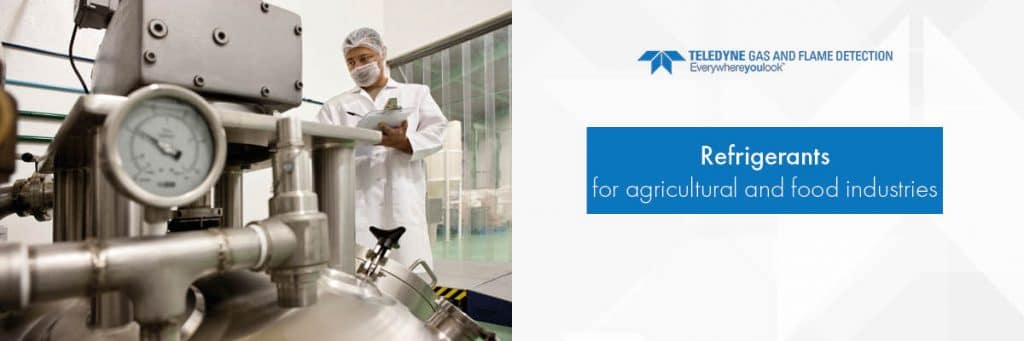