As the second lightest gas next to hydrogen, it has many industrial uses and is of critical importance as a process gas. Gaseous helium requires robust and tight-sealing valves and fittings in order to properly contain and disperse it.
Helium is usually produced as a byproduct of natural gas processing in the course of removing nitrogen, water vapor, carbon dioxide, helium, and other non-combustible materials to improve the heat energy of the natural gas.1 Extraction of crude helium from natural gas typically requires three steps which include removal of impurities, extraction of high-molecular-weight hydrocarbons, and cryogenic processing, which removes most of any remaining methane gas. Further purification of helium via activated charcoal absorbers or pressure-swing adsorption (PSA) processes is required in order to yield helium purities of 99.99 percent or better.2
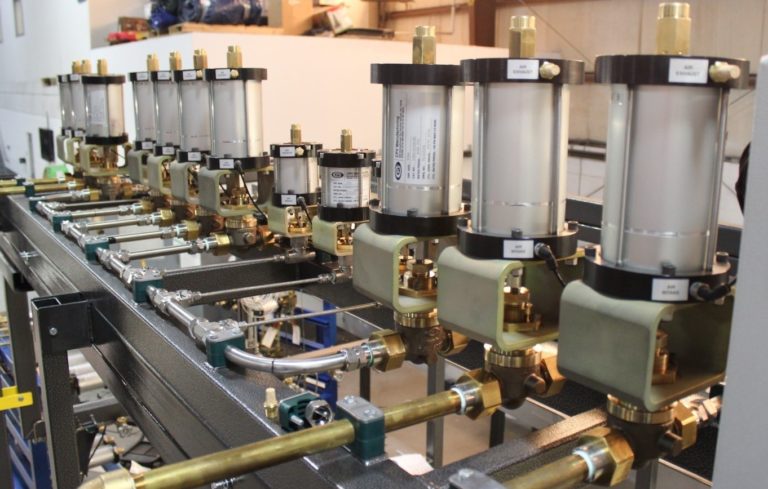
Gaseous helium is used in industry as an inert shielding gas in metal arc and laser welding; protective atmosphere in the production of reactive metals, such as titanium and zirconium; non-reactive atmosphere for growing silicon and germanium crystals used to make electronic semiconductor devices; a coolant during the drawing of optical fibers; and as a carrier gas for chromatography.3 Additionally, gaseous helium is used for leak detection equipment in piping systems and for filling party balloons. Liquid helium, on the other hand, is often used for MRI (magnetic resonance imaging) systems due to its unique cooling properties.
CPV Products in Gaseous Helium service – Design Considerations
There are inherent shortcomings in conventional metal-to-metal seated valves for high pressure service – especially in systems handling helium and other elusive gases. CPV engineers have taken the soft-seated approach to effectively managing high pressure, perfecting a full line of soft-seated valves and O-Ring Face-Seal (ORFS) separable unions designed to meet the rigorous demands of modern high pressure fluid systems.
CPV valves are unique, and superior to other products for high pressure service due to their complete, interchangeable cartridge design, including a removable, flat seat. A single valve cartridge – the entire operating portion of the valve – can be inserted into any CPV O-SEAL® body, direct weld body, or specialty manifold. This exclusive CPV valving concept gives piping system engineers unprecedented design flexibility – all the way from the drawing board up to and after installation.
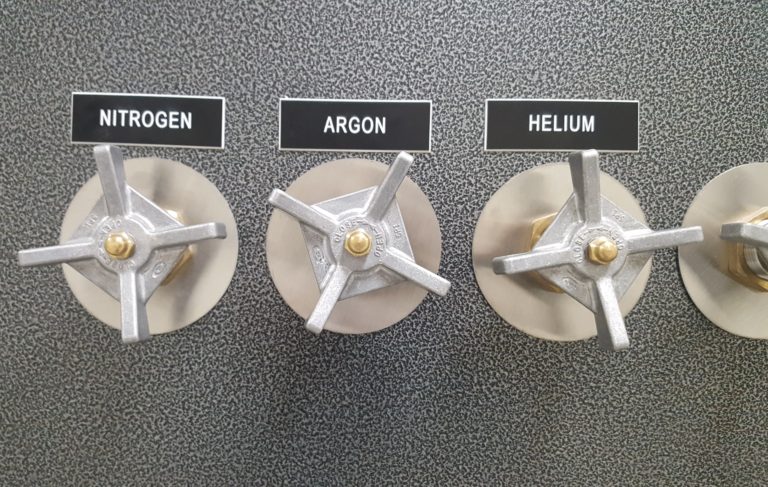
The O-SEAL® system actually uses line pressure to strengthen the seal; the higher the pressure, the tighter the seal. CPV fittings have break-remake flexibility to ensure leak-proof reliability. Connections can be broken and remade at will, with full assurance of positive sealing. Recessed in a close-tolerance groove in the body of the CPV fitting is a resilient O-Ring that is compressed against the flat metal face of the tailpiece by means of a union nut. The flat-faced design permits components to be slipped in and out easily, while the O-Ring seal assures that connections remain leak-tight at pressures ranging from vacuum to 6000 PSIG – regardless of how often they are broken and remade. Unlike compression fittings, which can require high torque for sealing, the CPV fittings require minimal torque to create a seal – in any size from 1/8 in to 2.50 in.
CPV valves and fittings have effectively eliminated helium leakage problems – particularly those exposed to extreme temperature changes during start-up, which can cause leakage due to expansion/contraction of metal-to-metal-sealed conventional fittings. CPV fittings also provide significant maintenance advantages. The resilient O-Ring effectively absorbs vibration shock to prevent gradual “backing off” of the threaded connection of the union nut, making periodic retightening unnecessary. Moreover, because of the flat-faced design of the fittings, components are more accessible to simplify routine maintenance. By simply backing off the union nuts, components can be slipped out without springing the line, and then slipped back in without affecting the sealing capability of the fittings.
CPV O-SEAL® and G-Series® product lines have been used at industrial gas fill plants for bottling high pressure pure helium gas, often needed by labs and welding operations. For high volume installations, helium from tube trailers is transferred, pressurized and controlled using CPV automated valves, hand valves and connecting fittings. CPV O-SEAL® valves with FloMaster® pneumatic actuators are used on fill islands inside plants, as well as outside on ground storage tanks, where they are often subjected to extreme winter weather conditions. CPV valves are the most reliable and robust valve in the industry, operating for every fill and every shutoff, requiring very little maintenance throughout their long service life.
CPV and the US Navy
Since the 1950’s the US Navy has specified CPV products because of their leak-proof connections, bubble-tight sealing, and shock & vibration resistance in critical systems on nuclear submarines, surface ships, and aircraft carriers. CPV valves and fittings are used on elevator systems for lifting aircraft to the flight deck, in the arresting gear that catches aircraft when they return, and in the lubrication systems on the catapults that launch the aircraft. CPV instrument valves are also preferred in refrigeration and air-conditioning systems and CPV relief valves are used in air and hydraulic systems owing to their reliability in high pressure air ram tensioner systems.
CPV O-SEAL® and Mark VIII® product lines are used in helium cryogenic refrigeration compressors as well as in saturation diving systems and hyperbaric chambers for the US Navy and NASA. CPV fittings are employed on gages, filters, relief valves and solenoid valves, wherever sealing is critical or periodic servicing of components is necessary. CPV valves are effective when precisely controlled helium-oxygen mixtures are required and are critical to breathability in underwater and space environments.
Why CPV?
Where bubble tight sealing and leak-proof integrity are the highest priority, CPV valves and fittings are the answer. The company’s innovative designs are well suited to standard applications, as well as one-of-a kind custom requirements. With CPV, reliability and dependability is our calling card. That’s why we are ‘American Engineering Trusted Worldwide®’.
Written by Joshua Raizman, Senior Applications Engineer at CPV Manufacturing
Sources: (1) How Products are Made. Volume 4: Helium. Retrieved 9 September 2019, from http://www.madehow.com/Volume-4/Helium.html – (2) The National Academies Press. The Impact of Selling the Federal Helium Reserve (2000): Chapter: 4 Helium Supply, Present and Future. Retrieved 9 September 2019, from https://www.nap.edu/read/9860/chapter/7 (3) Air Products: Safetygram 5: Gaseous Helium. Retrieved 9 September 2019, from http://www.airproducts.com/~/media/Files/PDF/company/safetygram-5.pdf