1 – Run the pump dry without limitations
Dry running an AODD will not have an immediate negative effect on your pump, but an AODD who runs dry will speed up. This will not only cause a bigger air consumption but the diaphragms will make a lot of strokes and will come to the end of their elasticity much quicker and will fail. To prevent this you can use a “Flow Stop Valve” in the air supply to your pump. This valve will detect the bigger air consumption and will close down the air supply to the pump.
2 – Run the pump with dirty and/or very humid air.
Air moisture and air quality are of utmost importance high moist or bad quality of the air can cause icing or clogging of the air valve or muffler; the moisture will condense in the air exhaust because of temperature drop from high to low pressure and will cause clogging the muffler. Also waste collected over time can cause clogging. Use clean, dry, filtered air to avoid clogging/icing of the muffler. Check the muffler on dirt on a regular basis and check the quality of the air you use to operate the pump. If the plant air is from low quality the use of an ”Anti-Ice Muffler” and Installing an air filter in the compressed air line before the pump will also help you to run the pump error free.
3 – Start-up of the pump at full pressure
It is always recommended to start up a diaphragm pump slowly.
If air pressure supplied to the pump is too high, while the pump is not filled with liquid, the pump will change over too quickly and the valve balls will not have enough time to close the valve seat to create vacuum to drawn the liquid into the pump.
On automatic on/off systems it is recommended to install a “Soft start valve” in the air supply to the pump.
4 – Use always the same diaphragms on different applications
An incorrect diaphragm selection can cause rupture of the diaphragm and many other problems to the pump. The lifetime of diaphragms depends strongly on the material the diaphragm is made of. Always check if the material of your diaphragm is resistant against the liquid you are pumping. PTFE diaphragms can be used on almost all chemical applications, but doesn’t have the best mechanical strength so will be prone to wear in abrasive applications. Diaphragms made of molded PTFE on a rubber layer will give a better result on this kind of applications. If not sure, ask a specialist which material to use as diaphragm will give you the best cost/lifetime combination for your application.
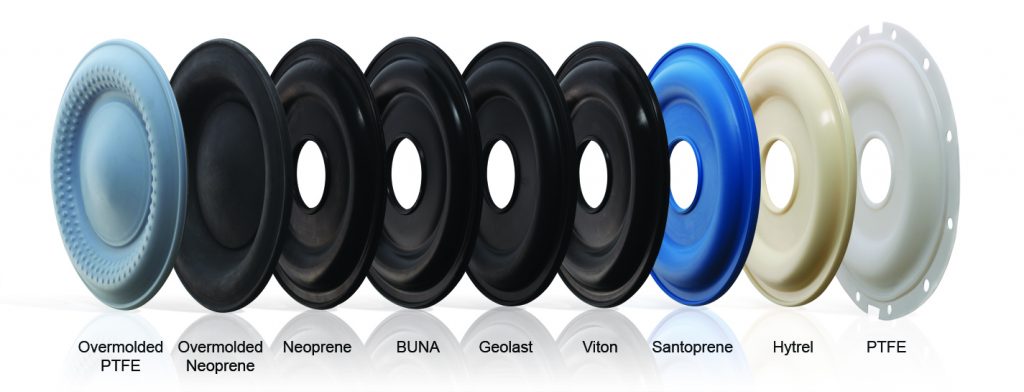
5 – Run the pump with high inlet pressure
An AODD making an irregular noise “like a machine gun” is a typical problem of an AODD running at too high inlet pressure. The valve balls on the suction side will be pushed from their seat by the liquid pressure and will start running around in their cage, generating this “machine gun noise”. Try to install an AODD always in such a way the pump has to create suction lift or only has a very limited positive inlet pressure. Using heavier valve balls (example rubber balls with a steel core) will also reduce this problem.
6 – Installing an air line withan inner diameter that is too small
Using an air-line that is too small, or air equipment in the air supply which are reducing the volume of air your pump needs to operate well, will starve the pump of the compressed air, making it operate slowly. Upgrading to a larger air-line and/or air equipment which can handle a bigger air flow is the solution. A rule of thumb is to use air equipment and hoses of the same internal diameter as the air connection of the pump. Check the operating manual of your pump for the correct size of air supply.
7 – Installing a fluid piping to the pump which is too small
A suction pipe which is too small can cause cavitation inside your pump and will reduce the life-time. A discharge line which is too small will create bigger pressure losses and will reduce the flow capacity of your AODD. If not sure, please contact your pump specialist with the necessary info of your application to select the best pipe-size for your installation.
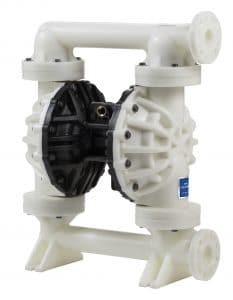
8 – Run your pump fast on abrasive applications
If you run an AODD fast on abrasive applications, the valve seats and balls will run out very quickly. Also the life-time of your diaphragms will be reduced. On those applications you will need to use a bigger pump running slower.
9 – Not taking suction lift and viscosity of your medium in account by selecting your diaphragm pump.
All AODD manufactures are publishing pump curves based on water and the pump running without suction lift. But due to the way of working, compressed air supplied to the pump is used at the same time for suction lift and to discharge your medium. When an AODD pump has to provide suction lift, the maximum flow rate of the pump will be reduced.
Pumping media with higher viscosity will create more pressure drop inside the pump. The pump will need to use more power to push the liquid out of the pump chamber through the ball/seat combination in the discharge line. By doing this the maximum capacity of the pump will be reduced.
Always check the flow reduction curves of suction lift and viscosity as well when selecting pump or check the selection with your local pump specialist.
10 – Not using the most efficient double diaphragm pump
Not efficient AODD pumps will have a bigger air consumption and will need more time to do the job. This will generate more maintenance not only at the
