Are You Losing Product and Profit Every Time You Flush Your Pipelines?
Many food and beverage manufacturers unknowingly waste thousands of gallons of valuable product every year.
Traditional flushing and rinsing methods – whether with water, chemicals, or even purging them with air – may seem like a simple solution for clearing pipelines.
But in reality, these methods lead to excessive product loss, high water usage, slow changeovers, and potential cross-contamination risks.
But there’s a better way to recover more product, reduce waste, and maximise efficiency – HPS Advanced Liquid Product Recovery (Pigging) Technology.
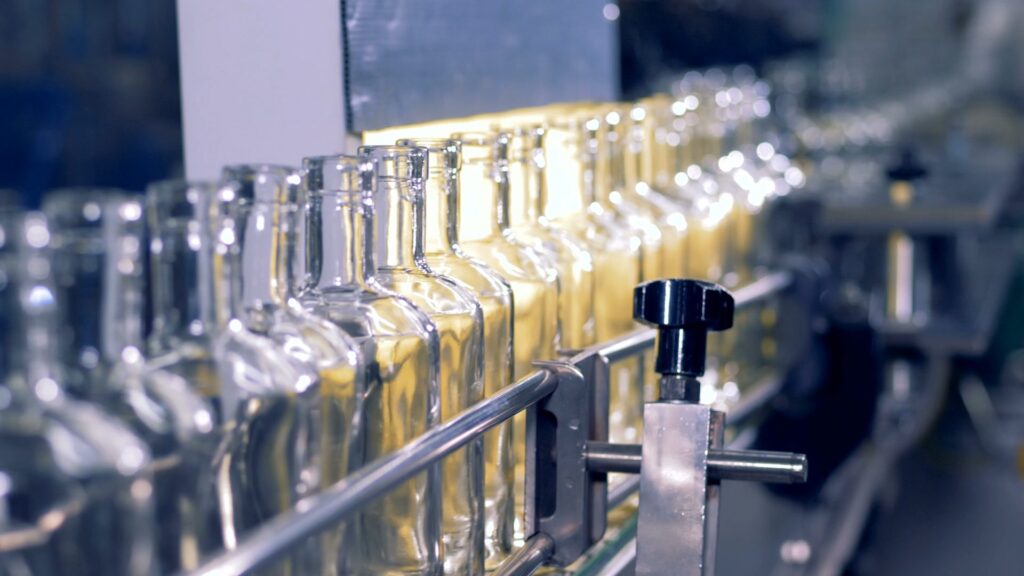
The Problem with Flushing
Flushing pipelines with water, cleaning agents, or air might seem like a simple fix, but it comes with major downsides:
Lost Product: Ingredients like syrups, dairy, juices, and sauces are flushed away, impacting profitability.High
Water & Chemical Use: Flushing requires excessive resources, increasing costs and hindering sustainability.
Expensive Waste Disposal: High amounts of effluent, along with contaminated wastewater and cleaning agents add to disposal costs.
Slow Changeovers: Long cleaning times mean more downtime and lower productivity.
Contamination Risks: Flushing isn’t always thorough, leading to potential cross-contamination issues.
Why Food And Beverage Manufacturers are “Pigging” Their Pipelines
HPS pigging technology helps food and beverage companies move away from outdated, inefficient flushing methods and enhance liquid transfer processes.
Here’s how:
- Recover More Product: Instead of flushing product down the drain, pigging pushes it through the pipeline to its intended destination—ready for processing, packaging, or sale.
- Use Less Water & Cleaning Agents: Pigging removes residual product, drastically reducing water, chemicals, and CIP (Clean-in-Place) processes.
- Cut Disposal Costs: Less waste means a lower environmental impact, reduced effluent generation, and lower wastewater treatment and disposal expenses.
- 20% Faster Changeovers (Often More!) : Pigging typically reduces flush times and changeover times by at least 20% (often more), boosting operational efficiency.
- Improve Product Quality and Safety: By eliminating cross-contamination risks, pigging helps maintain product integrity, ensuring food safety and consistency.
- Aeration, Foaming and Dissolved Oxygen (DO): For products sensitive to aeration, foaming, or dissolved oxygen, pigging reduces these issues, preserving the quality of your liquid products.
How Pigging Works
Pigging uses a specialist projectile (the “pig”) along with dedicated equipment to recover product from the pipeline—reducing waste and improving efficiency.
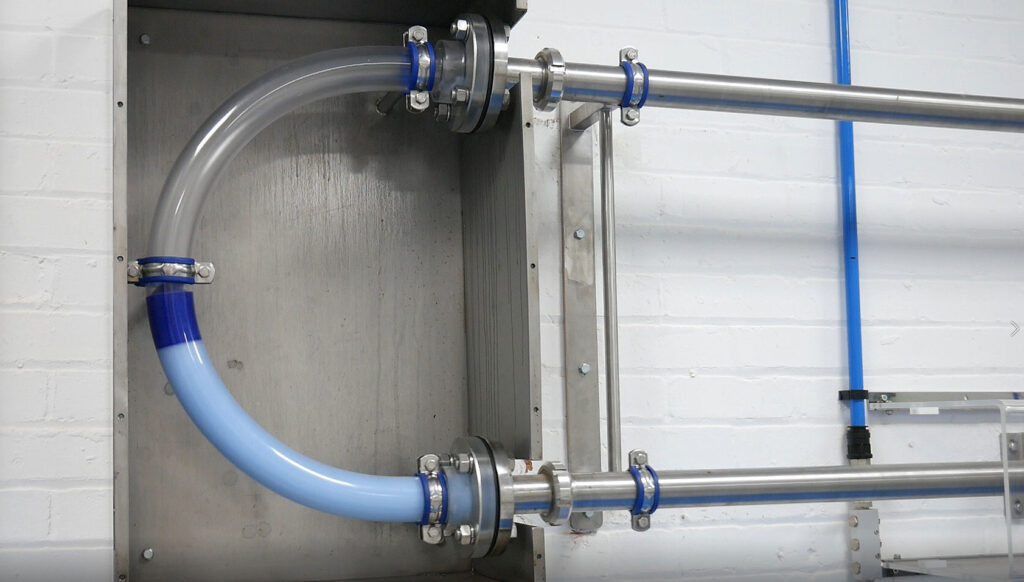
What About Air Purging?
Air purging is another technique sometimes used to clear pipelines before the next batch, but it only recovers around 50% of the product. With such low product recovery rates, long flush times still follow, leading to further loss and wasted resources.
In contrast, pigging recovers nearly all of the product, significantly reduces cleaning times, and boosts overall efficiency.
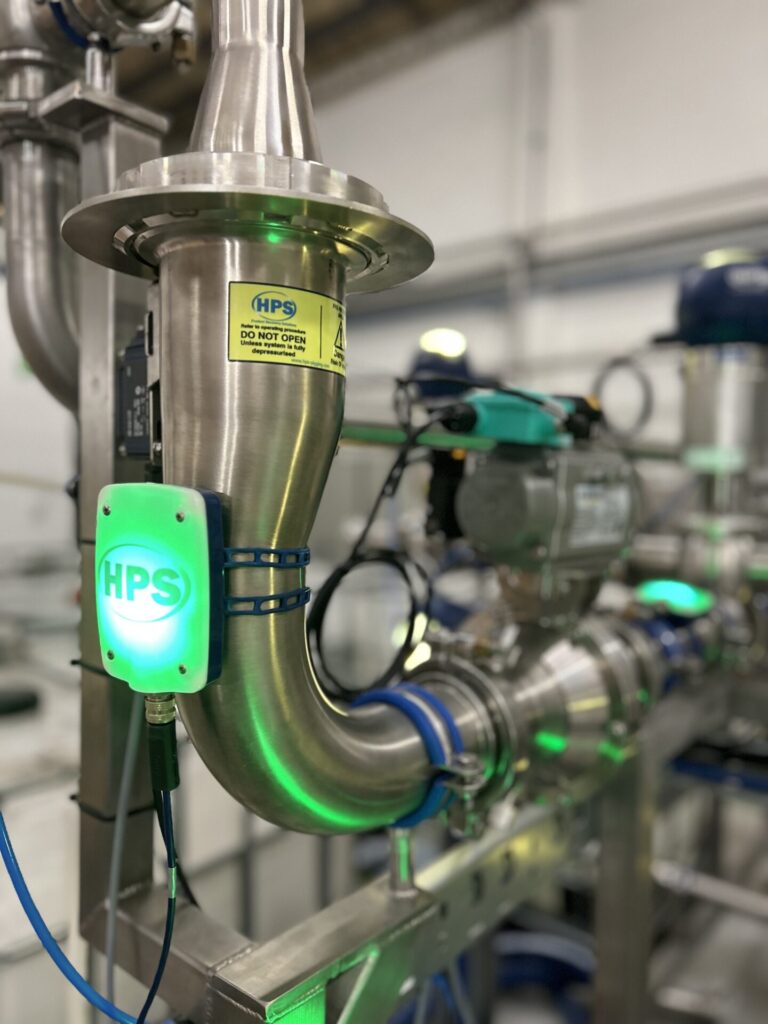
Proven Results with Pigging
Here are some real (and typical) results from HPS clients:
- Up to 99.5% product recovery from pipelines
- Prevention of 1,200 gallons of product loss per cycle
- 4% increase in yields—equating to 48,000 extra cans per week
- Sanitization times cut to 15 minutes instead of 2-3 hours
- Reducing product waste from 500-600 lbs per changeover to just a few pounds.
- Approximately 40 megalitres of water saved annually
- Lower carbon footprint—improving sustainability and reducing waste
Using HPS pigging technology improves yields, efficiency, capacity, sustainability, and bottom-line performance.
The Bigger Picture: Compliance, ROI & Sustainability
Switching to pigging isn’t just about cost savings—it’s also about long-term return on investment. Many food and beverage manufacturers face increasing pressure to:
- Achieve sustainability targets by reducing water, energy and chemical usage
- Improve operational efficiency while maintaining product quality
With HPS pigging technology, manufacturers can achieve all these goals while increasing profitability.
Start Pigging Your Pipelines Today!
Why waste valuable product, time, and resources on outdated flushing methods? HPS pigging technology provides a sustainable, cost-effective way to recover product, reduce waste, and boost efficiency.
Find out how manufacturers are reducing product loss by up to 99.5% with pigging—get the full guide here.