And when it comes to liquid transfer, pipeline inefficiencies, cross-contamination, and product loss are daily hurdles that many manufacturers struggle to overcome. Traditional methods such as flushing, air purging, or chemical cleaning often fail to address these challenges effectively, leaving behind residues, wasting significant amounts of product and escalating operational costs.
HPS Advanced Liquid Product Recovery (Pigging) Technology offers a proven solution. By removing up to 99.5% of residual product from pipelines, HPS pigging systems help manufacturers tackle their biggest liquid processing challenges while achieving remarkable efficiency gains.
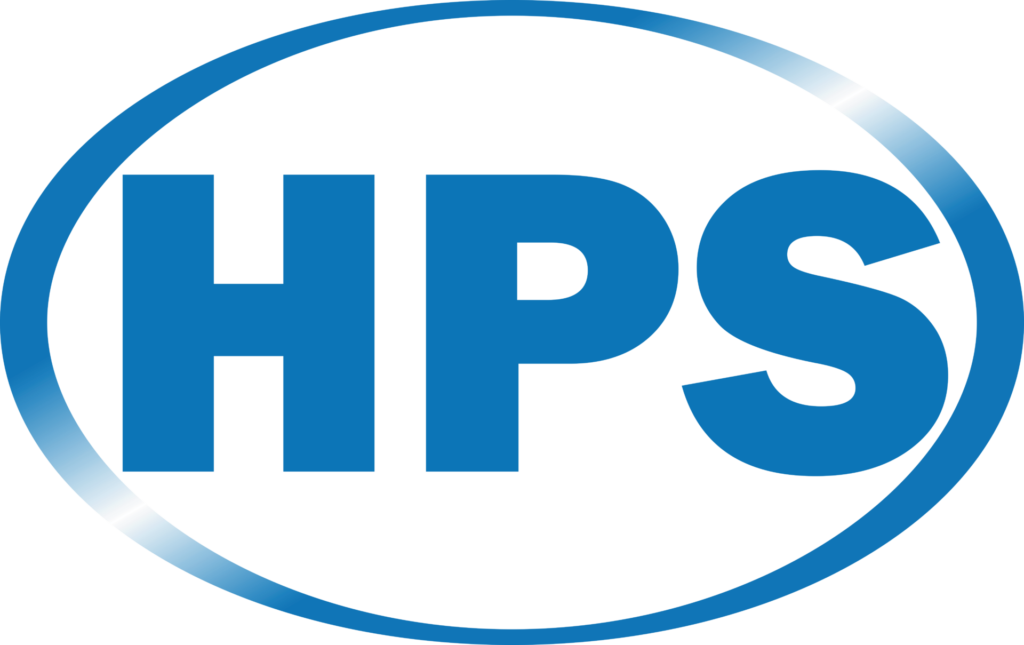
Why Chemical Manufacturers Are Turning to Advanced Pigging Technology
HPS pigging systems directly address the challenges chemical manufacturers face every day:
- Unnecessary Product Loss: Residual product left in pipelines represents wasted resources and lost revenue.
- Costly Waste Disposal: Inefficient cleaning methods increase the volume of wastewater and chemical effluents, driving up costs.
- Cross-Contamination Risks: Inadequate pipeline clearing compromises product quality and requires additional quality assurance measures.
- Lengthy Changeovers: Time-consuming cleaning extends downtime, reducing productivity.
By reclaiming otherwise wasted product, minimising contamination risks, and streamlining cleaning and changeovers, pigging delivers both immediate and long-term benefits.
What Can Pigging Do for You?
HPS pigging systems are tailored to the needs of chemical manufacturers, offering a range of tangible benefits:
- Recover Valuable Product: Reclaim residual liquid that would typically be discarded, significantly improving yield.
- Simplify and Accelerate Cleaning: Clean pipelines faster and with fewer resources, reducing labour and downtime.
- Lower Disposal Costs: Minimise the volume of waste, cutting expensive disposal fees.
- Prevent Contamination: Ensure the integrity of your product and reduce the risk of costly recalls or rework.
- Boost Productivity: Speed up changeovers, allowing for increased production capacity.
How Pigging Works for Chemical Pipelines
Pigging is a highly efficient process that uses a specialised device called a “pig”, along with other equipment, to recover residual product from pipelines. Propelled through the pipeline, the pig pushes product that would otherwise go to waste to its destination, ready for further processing, packaging, and sale.
Pigging saves companies that transfer liquids through pipelines tens, sometimes hundreds of thousands of dollars every year.
Product Recovery: Pigs recover nearly all residual product from pipelines, leaving minimal residue.
Adaptability: Will navigate bends and work with diverse chemical processing environments.
Safe Materials: Constructed from materials compatible with aggressive chemicals, ensuring longevity and safety.
Advanced Detection: Fully detectable pigs allow for efficient and precise operation
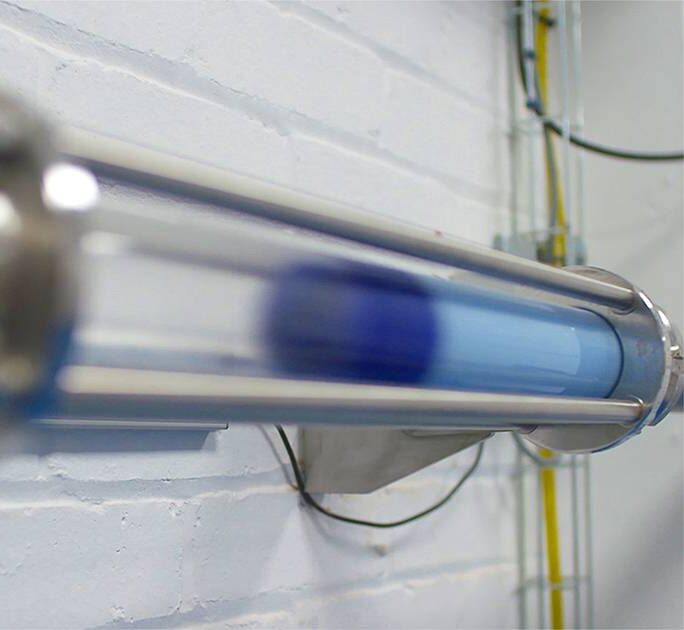
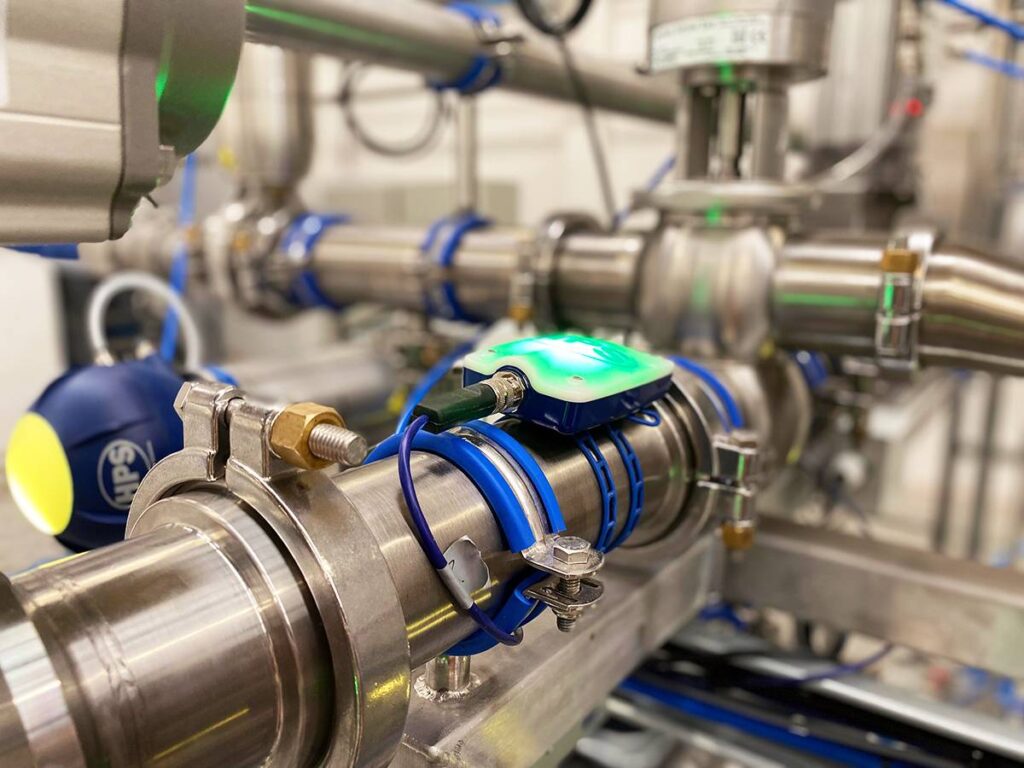
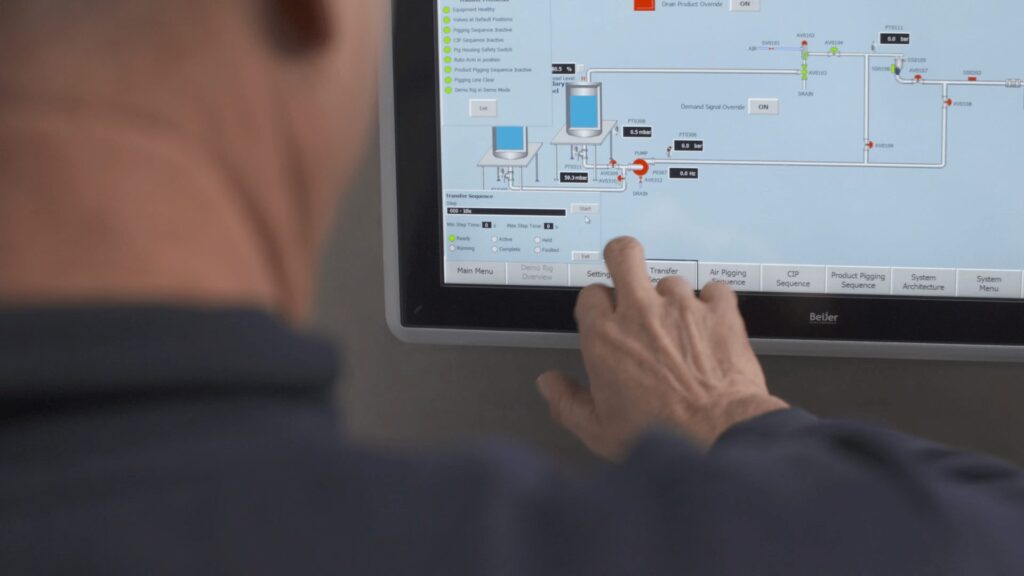
Real-World Success Stories
Case Study 1: Silicone Gel Manufacturer
A European chemical company producing silicone gel faced persistent challenges:
- Contamination: Thick gel residues mixed with other products during purging.
- High Product Loss: Valuable gel discarded during cleaning.
- Escalating Costs: Increased waste transportation and labour expenses.
HPS Solution: Two automated pigging systems for chemicals recovered nearly all residual product, drastically reduced contamination risks, and simplified cleaning. The manufacturer saw immediate savings in waste disposal and labour costs while improving product yield.
Case Study 2: U.S. Chemical Producer
A large U.S. chemical manufacturer grappled with:
- Massive Product Loss: 425 monthly changeovers wasted 60 gallons of product each, equating to $5 million annually.
- Extended Downtime: Labour-intensive cleaning slowed production.
- Escalating Disposal Costs: Higher waste volumes added further expenses.
HPS Solution: By implementing pigging technology, the company recovered lost product, reduced downtime through faster changeovers, and significantly lowered waste disposal costs.
Case Study 3: Cutting Carbon Emissions
A Carbon-Zero report on water-based and solvent-based paint production revealed that pigging technology can save around 2.6 tonnes of carbon dioxide equivalent for every product changeover.
This highlights how pigging not only improves operational efficiency but also supports sustainability goals by significantly reducing carbon emissions.
Why Choose HPS?
With 30 years of experience and 2,000+ systems implemented globally, HPS is the leading provider of pigging solutions for chemical manufacturers. Our systems are:
- Custom-Designed: Tailored to meet your process requirements.
- Safe and Hygienic: Built with safety and compliance in mind.
- Efficient and Reliable: Proven to deliver immediate ROI through savings and productivity gains.
- Supported by Experts: Backed by ongoing technical support and a commitment to innovation.
Start Pigging Today
Don’t let inefficiencies hold your chemical operations back. HPS pigging technology offers a sustainable, cost-effective way to recover product, reduce waste, and maximise productivity.
Contact HPS today to learn how pigging can enhance your liquid processes and deliver measurable results.
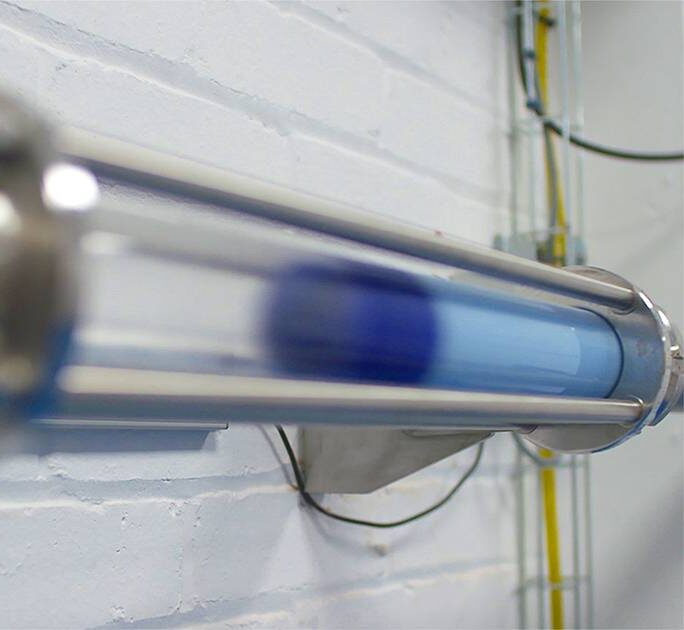