Conserve resources and save costs
There is potential for avoiding food waste in many different areas in production plants. In the various manufacturing processes, intelligent measurement technology can make a significant contribution to avoiding the loss of valuable resources like raw products or processed food. In the following, we illustrate examples of successful implementation based on specific real-life customer cases. By clicking on the links you can get more details on the case studies described or the applications presented.
Phase transition between two different media:
- Problem: Often a safety time buffer is applied for quality assurance reasons, resulting in high-value product being discharged into the wastewater.
- Solution: Inline analysis of the media for phase transition in real time, e.g., by a turbidimeter or a conductivity sensor.
- Example: The organic dairy Söbbeke carried out a comparative measurement before and after installation of one ITM-51 turbidimeter each in the inlet and outlet of their UHT plant. As a result, the discharge to the sewer per phase change was demonstrably reduced by 65 seconds. As a consequence, the ITM-51s save almost 120 liters of organic milk at each phase transition.
Leibinger Brewery uses ILM-4 conductivity meters to ensure that beer ends up in the bottle and rinse water in the sewer. With this automised control step in the filling facility the loss of product or also of clean water can be minimized.
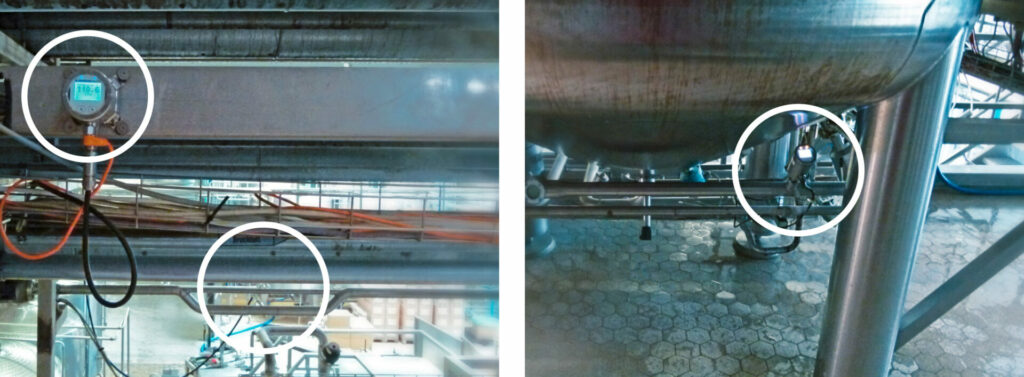
118 litres of milk saved per phase transition at the Söbbeke organic dairy: The turbidimeter ITM-51 is used as a “remote sensor” for the feed. The measuring unit with display is mounted separately for on-site control. At the outlet, the compact version of the ITM-51 is ideal.
Non-optimised production processes:
- Problem: The quality of the product sometimes does not meet the requirements and it has to be discarded or can only be used for lower-quality end products, such as cattle feed.
- Solution: Continuous control of process parameters through measurement technology with active alarming in case of deviation from the specifications.
- Example: In Friesland Campina’s production of rice pudding in a continuous process, foam formation in the feed tank repeatedly caused a process standstill and the loss of an entire production batch. The NSL-F potentiometric level probe reliably measures the level without the influence of foam, and there have been no production downtimes ever since.
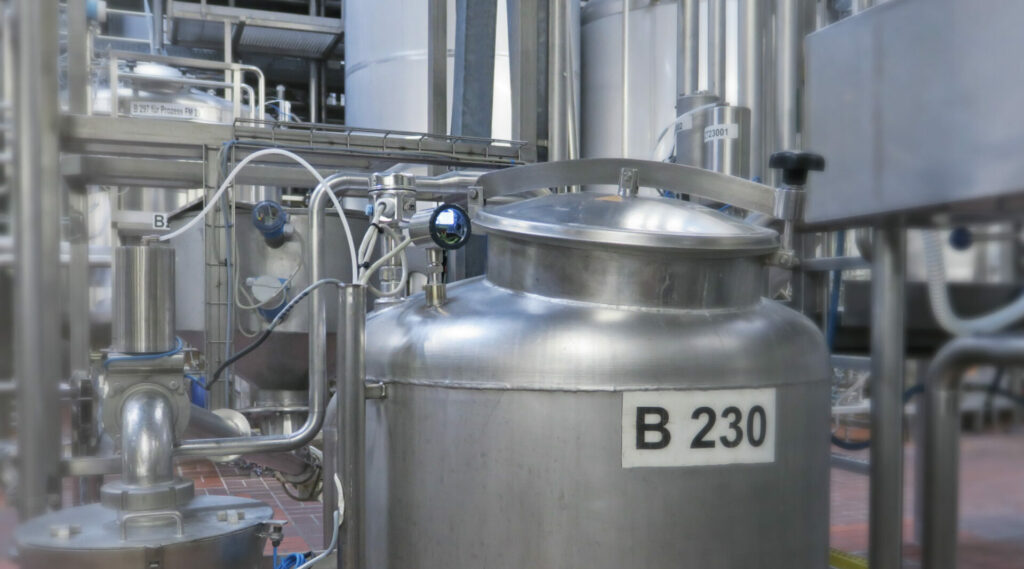
“We tried all kinds of things, but it was only with Anderson-Negele that we found a safe and reliable level measurement. It was so convincing for us that since then we have also been using the NSL-F in other applications, such as in the fruit feed vessel or for dessert creams.” G. Stiepan, Team Leader Maintenance at Friesland Campina
Inaccurate level control in process tanks:
- Problem: To avoid dry-running of pumps, feed vessel contents are often not used to the maximum. Residual product is then flushed out during cleaning.
- Solution: Accurate level control in the vessel
- Example: Level switches for point level detection such as the capacitive level sensors NCS or the conductive level sensors NVS provide a highly precise and immediate indication for any medium, so that the production processes can run optimally and with maximum product utilization.
Non-optimised CIP process:
- Problem: As a result, traces of acid or lye can contaminate product in the subsequent production process, which then has to be disposed of.
- Solution: A hygienic design of the entire production plant including process connections for the instrumentation that are free of dead legs.
- Example: Process adapters with clamp or screw connections without dead legs. The CPM fittings or the CLEANadapt process connection systems are designed in such a way that deposits of cleaning agents formed during cleaning are minimised, thus enabling better control of product quality.
Success can be calculated
Worldwide the amazing quantity of around 40% of food is lost. In the media, “Food Waste” is often presented with photos of waste containers with food. Yet the fight against waste already begins in the dairy, brewery or beverage production, in the raw material processing itself.
There are many approaches to reduce waste of raw materials, intermediate and end products to a minimum already during production. In many cases, an instrumentation system pays for itself within a few weeks or months by avoiding resource loss. Anderson-Negele’s application specialists can perform an ROI calculation with an online tool for interested companies.
Further details and application reports on the practical examples presented can be found on our homepage. We would be happy to help you find potential savings in your production as well. Just contact us, you will also find the contact details of our application specialists on our homepage.