In the current situation, many manufacturing companies face additional special challenges. Changes in demand – both positive and negative – call for production to be adjusted.
What does that mean with regard to compressed air?
The consumption of electricity, gas and many other media that are required in production can usually be easily adapted. It’s not that easy with compressed air …
… rising demand pushes the capacity of compressed air generation to the limits of utilization ratio.
… decreasing demand, however, often leads to uneconomical operating conditions.
In both cases, locating and eliminating compressed air leaks can be a very useful, supportive measure.
Compressed air leaks don’t take a break
Leakage quantities in the compressed air network do not automatically change to the same extent when production parts are shut down. The result: the leakage rate of the compressed air consumed increases and worsens the specific efficiency of the compressed air generation.
Lower workload also creates good conditions for eliminating leaks. The maintenance staff has free capacities and plant parts are more accessible.
When increasing the production volume the capacity of compressed air generation sometimes reaches its limits. Eliminating leaks can help to use compressed air for production that would otherwise have been lost.
Modern devices for leak detection provide quick remedies in both cases, because they not only find the leaks during operation, but also provide direct information about the leakage volume and costs. This enables immediate prioritization of the measures and also enables sustainable reporting for energy management.
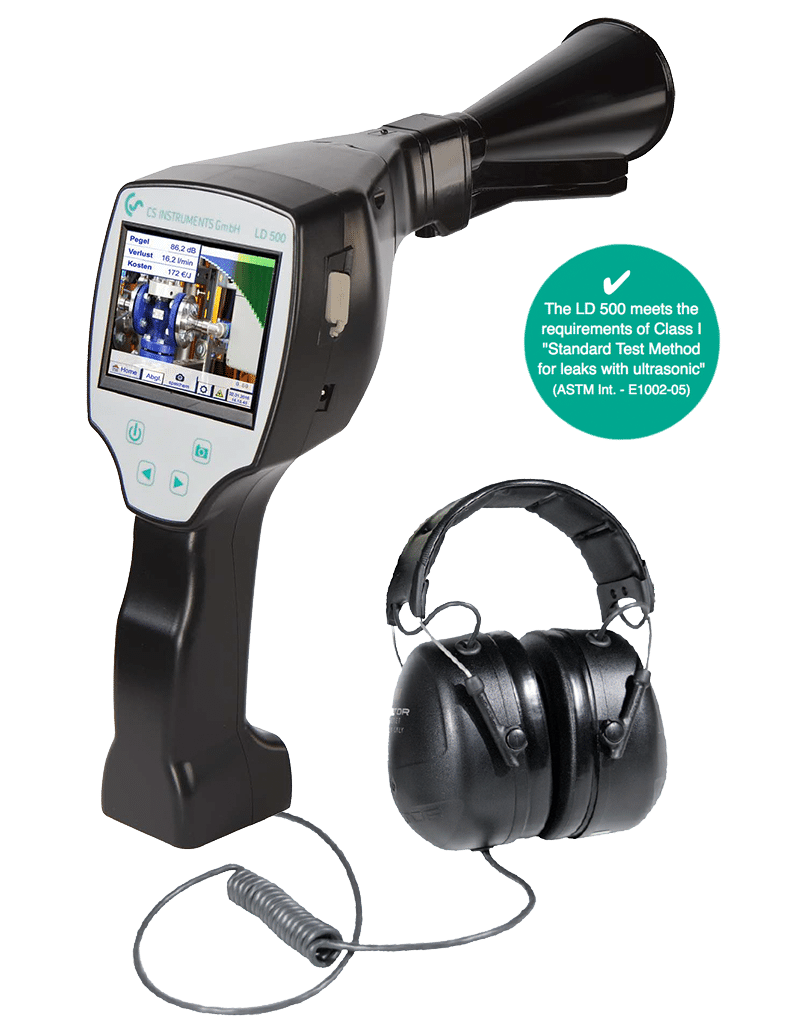
The leak detection device LD 500 from CS Instruments fulfills all requirements for an efficient detection of leaks, their prioritization and an intuitive reporting with the leak reporter software.