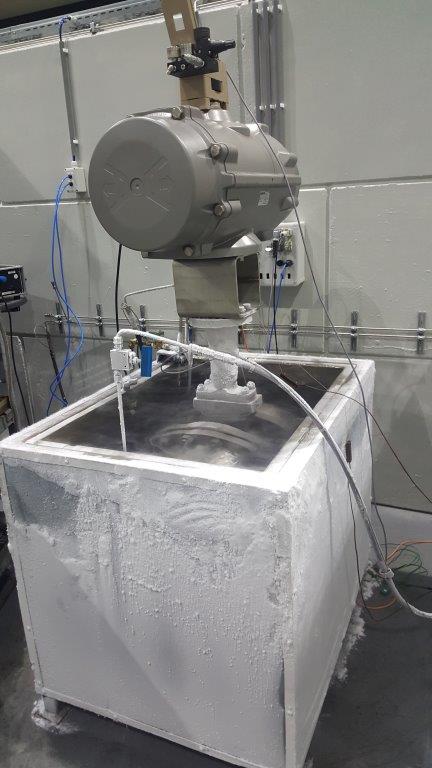
The increased demand for LNG in recent years is causing an exponential growth of valve testing at low temperatures for projects all around the world. Despite strict standards for design, engineering, manufacturing and testing, a wide range of products intended for use at low temperatures fail to pass the test of practicality. Timely cryogenic testing at temperatures as low as −253°C is the answer to this problem.
By Colin Zegers
LNG is a relatively new product and for most installation components – valves, for example – standards apply which indicate how to design, manufacture and test them. However, for a number of components, no standards regarding the use under low-temperature conditions are available or integrated. Building in components without any knowledge of their functioning could lead to failing equipment, resulting in extremely dangerous situations, due to the hazardous nature of LNG. Needless to say, reliable installations, installation components and further equipment are of paramount importance. This calls for meticulous and extensive cryogenic testing procedures concerning reliability, durability, functioning as well as safety, performed by specialists.
Hydrogen: the new LNG?
Can hydrogen, the smallest of molecules and a colorless, odorless gas whose vapors are lighter than air, become a major part of a future clean energy system? Many scientists and industries think so. It ignites easily and burns with an almost invisible flame. It is clean-burning, producing no CO2. When combined with oxygen in a fuel cell, hydrogen produces heat and electricity with only water vapor as a by-product. These characteristics predict a bright future for hydrogen. There is nevertheless concern about possible technical challenges with respect to reliability and emission of industrial components and their applications. Here, too, an important role is reserved for cryogenic testing.
Cryogenic fluids
Examples of cryogenic fluids applied by ITIS are LNG (Liquified Natural Gas, temperature approximately −162°C), liquid oxygen, (-183°C), and liquid argon (-186°C). On a regular basis the company, which is located in the south of the Netherlands, is also requested to test products suitable for liquid hydrogen (-253°C). To cool down objects, ITIS applies liquid nitrogen as well. However, this cooling fluid is not suitable for temperatures of -253°C. In situations like these, liquid helium can be used since it is applicable at temperatures as low as −269°C.
Shocking situation
Experience shows that performing cryogenic tests as described above is a bare necessity. Design Validation Testing of valves often reveals a large number of casting defects, gasket failures, broken parts, leakages etcetera. More than 60% of the valves do not pass the test whereas the valve data sheets claim all parts meet the PT (pressure/temperature) requirements. This, of course, is a shocking situation. It illustrates the importance of expert testing. Extensive cryogenic testing procedures were specifically designed to assess and prove the capability of valve manufacturers as well as demonstrate the functional performance of newly designed products and components. With regard to valves, cryogenic testing is employed to confirm the seat sealing, the fugitive emission rate, and the operational torque capabilities of the valves. Both during and after the testing procedures, the valves undergo a series of mechanical and thermal cycles. These include testing at RT (room temperature), upper design temperature, lower design temperature, followed by another RT test and, finally, a strip-down during which the valves are examined for any potential damage(s), as well as wear and tear.
Costly confusion
In my opinion cryogenic testing should be performed as early as possible, i.e. at the factory where the individual components are manufactured. Normally, individual components meant for industrial application are pressure tested to check them for leaks before they are shipped to the client. The testing types and methods applied are based on a multitude of different standards which frequently leads to confusing situations. As a result, the purpose, as well as the expected results of these tests, are often misunderstood and misapplied, causing unnecessary delays, unanticipated costs and, last not but not least, hazardous situations that could have been prevented, had the individual components been submitted to extensive cryogenic testing at an early stage.
Timely prevention
Cryogenic tests performed by ITIS reveal a relatively high failure percentage. Closer analysis often shows that the applied basic materials, individual components and/or products were never exposed to necessary testing or, for that matter, practical conditions. In one of the projects performed by ITIS, a certain type of valve had been used in a cryogenic installation. At room temperature, the performance of these valves was perfect. However, once tested under pressure at low temperatures, all valves failed. Due to increased brittleness and unacceptable tolerance changes they were impossible to operate in combination with the original actuators. This, of course, could have had some serious consequences. After the valves had been provided with different seats as well as larger actuators, the problems for operability were over. But expert cryogenic testing at an earlier stage under practical conditions would have prevented this situation altogether.
Clear picture
The importance of appropriate and perfectly customised materials and parts can hardly be overestimated. All it takes for the designer and the manufacturer is a clear picture of the purpose of the product or products they are planning to create, as well as the conditions under which they eventually have to perform. Many manufactures of PTFE, for example, claim a working temperature that extends down to -200°C (-328 °F), displaying little or no increased brittleness. They also claim the product maintains high strength, toughness and self-lubrication at temperatures down to -268°C (-450°F). However, tests performed at the ITIS testing facility showed that the strength and flexibility of the product could not be guaranteed at temperatures below -200°C. If used for the manufacturing of seats, for example, it could at some point prove to be unsuitable and thus lead to highly problematic situations. This, again, demonstrates that early cryogenic testing pays off.
Fugitive Emissions Tests
Fugitive emissions are emissions of gases or vapours from pressurized equipment due to leaks and other unintended or irregular releases of gases, mostly from industrial activities. As well as the economic cost of lost commodities, fugitive emissions contribute to air pollution and some vapours present potential hazard to human health and safety. Therefore, industrial components must comply with a number of international standards and directives for the emission of dangerous substances, such as ISO 15848-1 (International standard), TA-Luft (applicable in Germany) and API (USA). Compliance is achieved by performing leak tests, preferably at the earliest stage possible. Early-stage leak testing can even be performed on complete newly built installations before start-up, after overhaul or during shut down. For example, in the form of a Fugitive Emissions Test. FET-testing is a highly precise means of leak detection and is used to locate and quantify leaks in a wide variety of industries and applications. It focuses on valves, vessels, heat exchangers, seals, welds, flange connections, tubes, condensers, and many other components.
Some expert tips for preventing failures under cryogenic conditions
- Check if all the information about the materials you intend to use for your products is available. Sometimes seats and seals are selected on the basis of a PT (Pressure/Temperature) graphic provided by the manufacturer. However, the properties of the products could turn out differently when they are applied at lower temperatures or pressure rates.
- Make sure your products are free from any dust and/or oil, and completely dry before installation or testing. In many cases, liquids such as water with a corrosion inhibiter are used during hydrostatic testing. At lower temperatures, this could lead to failures.
- Use sealing and gaskets suitable for the fluids involved in combination with the specific temperature conditions under which the sealings and gaskets will be used.
Research frequently shows that products were never tested under or exposed to the conditions (minimum/maximum temperature) mentioned in the product data sheet.
- Acquire the necessary data about the integrity of the products you are going to use, as well as their application(s). Test the products, at the very least under practical conditions (temperature, pressure, operational cycles, etcetera).
- Some materials are preferably cooled down to a specific minimal temperature rate/duration in order to prevent failures. Excessive temperature changes could make the materials shrink or crack.
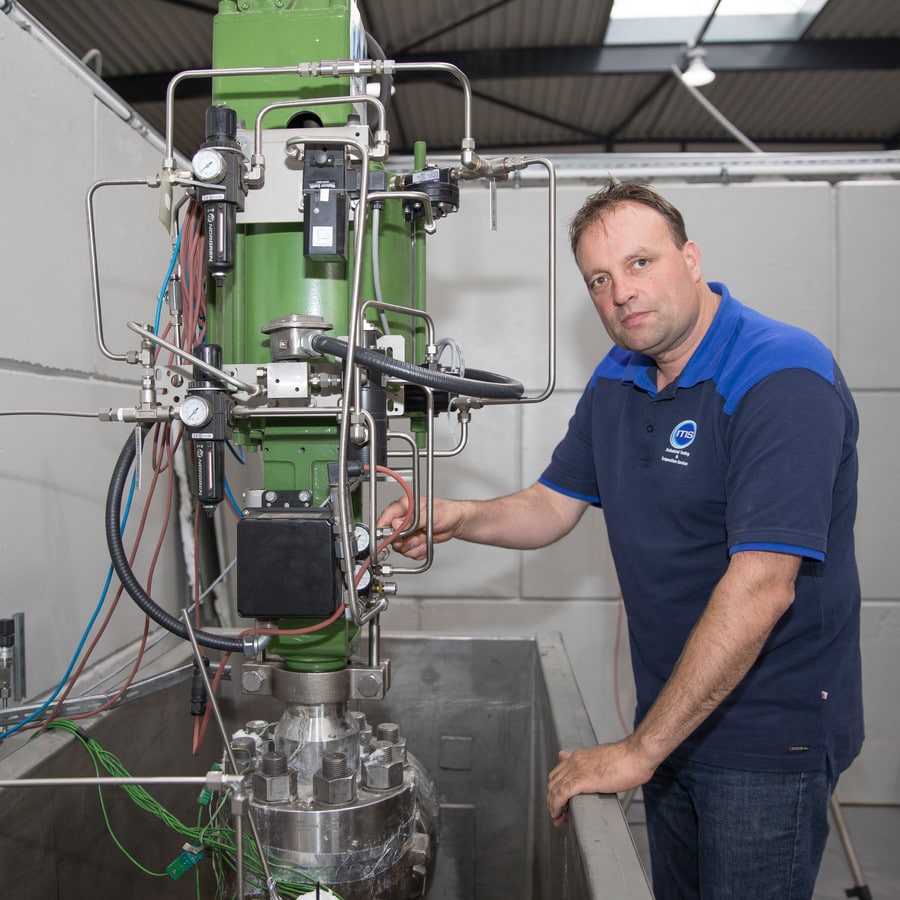
Colin Zegers is the owner of Industrial Testing & Inspection Services (ITIS B.V.), located in Goes, the Netherlands.