Design considerations for CIP
The main purpose of CIP is to remove physical dirt and residues, as well as bacteria. It is commonly used for equipment such as piping, tanks, and fillers, and CIP employs turbulent flow or spraying and can also be accomplished with filling, soaking and agitation.
As well as ensuring that production equipment is hygienically clean and suitable for use, CIP also plays a number of other important roles. CIP systems should ensure that no cleaning fluids or contaminants remain in the equipment – ensuring food safety, and by reducing the effort and downtime required for cleaning, they also ensure production cycles are efficient and cost-effective. Because of the automated or semi-automated nature of CIP systems, they provide improved control of the cleaning parameters to ensure consistent results, as well as automatic record keeping for traceability and due diligence purposes. Furthermore, being automatic reduces the need for human contact with potentially harmful cleaning agents or other chemicals.
However, if CIP is to be effective, not only does the CIP system itself need to be well designed, but the production equipment itself needs to be designed from the beginning with effective CIP in mind. Equipment and machinery must be hygienically designed and easy to manage, maintain and audit. Because of the specialised and custom nature of much food and drink processing machinery, some CIP systems will be designed specifically for a particular system or piece of equipment, although with careful design it is common to install a dedicated CIP system, such as those available from HRS.
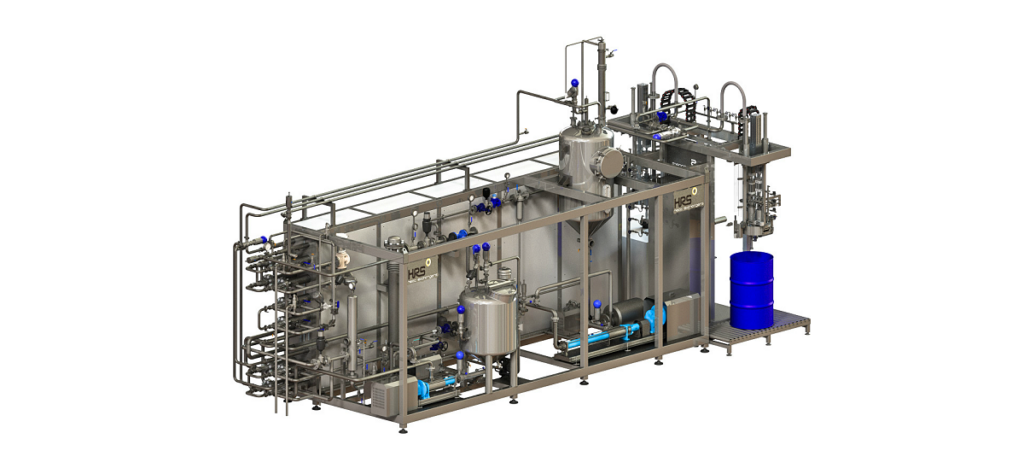
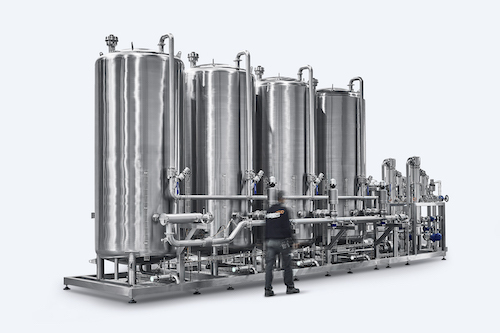
Typical CIP processes
Most CIP employs a similar set of operations, including:
- Pre-rinsing – to remove large debris and residues
- Detergent cleaning – to remove attached dirt and soiling using a caustic detergent
- Rinsing – to remove detergent and dirt
- Optional acid cleaning – if required to remove scaling or alkaline residues
- Rinsing – to remove the acidic cleaning agent
- Disinfection – heat or chemical treatment to disinfect the equipment
- Final rinse – to remove all traces of chemicals and prevent contamination
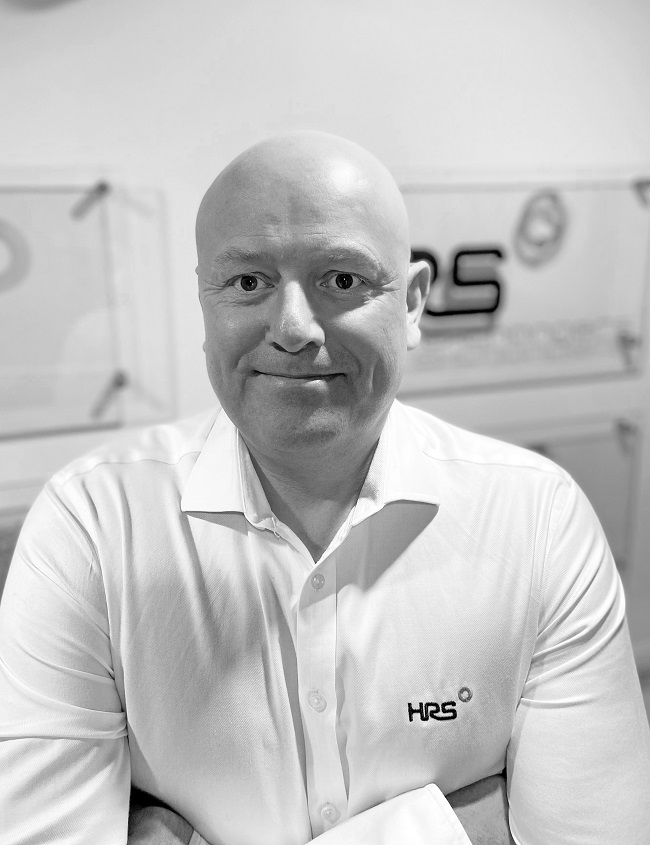
These steps may be combined or used in different ways. For example, using detergent at high temperatures may clean and disinfect equipment at the same time, or using steam may reduce the need for chemical detergents. Depending on the design of the system, and the risk of contamination, cleaning solutions may be reused multiple times or discarded immediately. There may also be differences between CIP and SIP (sterilise-in-place) systems.
While the actual cleaning regime used will depend on a number of factors, including the risk category of the food or drink product, the physical and chemical properties of the product, and the design of the machinery in question, in many situations it is preferable to rely on water alone (together with temperature, pressure and agitation) rather than additional cleaning chemicals which could present a contamination risk. In general, the higher temperatures and greater kinetic energy provide more efficient cleaning, but the duration of the CIP cycle will be optimised according to the properties mentioned above.
Where detergents are required, one of the most common is caustic soda (NaOH), although many other alkali- and acid-based chemicals are available depending on the nature of the product and residues which need to be cleaned. Alkali materials are generally more effective against proteins and fats, while acids perform better where salts need to be removed. For sugars, water remains one of the most effective cleaning mediums.