Architectural glass with low emissivity (low-e) coatings have become one of the most popular and functional building materials. They play an important role in improving the energy efficiency and conservation of a structure by minimizing heat loss and internal condensation. The coating, or thin film, on the glass, controls the flow of visible light energy through the glass. This coating alters light transmission, reflection, and absorption characteristics at different portions of the electromagnetic spectrum, including infrared, visible, and ultraviolet light.
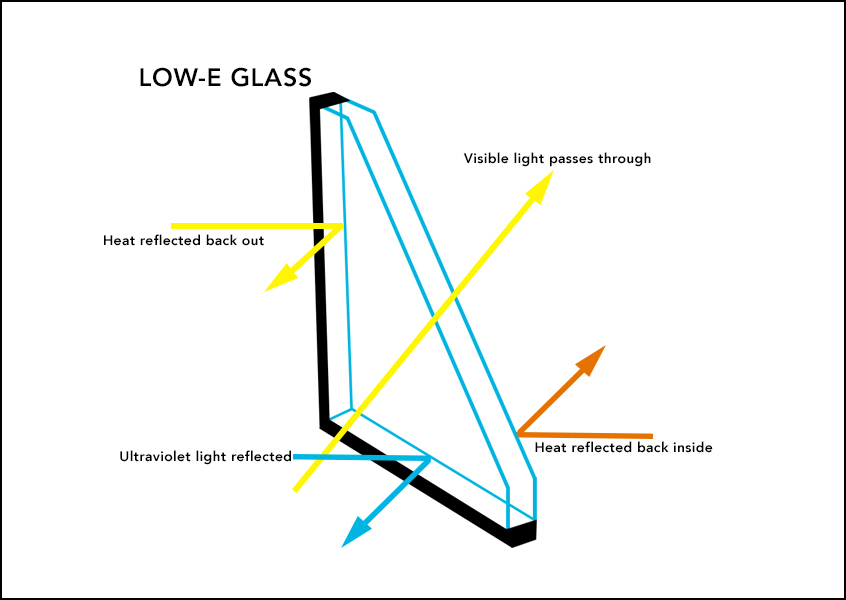
Low-e glass coatings require low emissivity, low absorptance, and high transparency. These specialty coatings consist of various microscopically thin chemical layers which are placed in a stack. There are two types of coating materials: Semiconductive and Metallic.
Glass coating manufacturers often use magnetron sputter vacuum deposition (MSVD). This method provides a cost-effective solution, excellent coating uniformity, improved emissivity (below 0.08), better heat radiation control and optical performance. Sputtering is used for the deposition of different types of materials including metal materials, oxides and dielectric materials.
It is important to note that the glass market is extremely competitive. As such, glass manufacturers are continuously pursuing approaches to minimize costs without sacrificing coating quality. These include in-house product/process development initiatives that aim to develop new, improved layer stacks. Manufacturers are also looking to increase productivity by reducing process time. They are achieving this by investing in “intelligent” and more dynamic systems to compensate in real-time for process conditions. Reducing operational costs through adaptive process technology to maximize yield and quality is significant. The entire manufacturing process, including quality control, takes about four weeks.
Application Requirements
Glass coating manufacturers run long production campaigns that require a consistent coating thickness and uniformity along with high yields and throughput.
A fully automated coating process, with stable process conditions can help to reduce operational costs. These conditions are made possible with premium instrumentation that provides:
- High accuracy, repeatability and reproducibility of reactive gases
- Superior, long-term gas control stability to maintain critical process parameters and less frequent instrument calibration between production campaigns
- Digital communications protocols, web interface and enhanced device profiles for easy setup and integration into DCS/PLC/IoT systems
Process Solution
A glass coating line consists of a glass washer and an entrance chamber passing through several sputter chambers to an exit chamber. The glass passes through a washer and a high-pressure air dryer to ensure a clean surface. The glass enters the coating line where it passes through a vacuum chamber where pressure is reduced from atmospheric to low pressure so plasma can form. The glass enters a process chamber with a magnetron where Brooks Instrument SLA Series mass flow controllers deliver a uniform and accurate amount of inert argon gas flow and in some applications, reactive gases such as oxygen or nitrogen. The ions from the plasma are attracted to the coating material, bombarding and dislodging atoms. Atoms are applied uniformly to the glass surface – producing a thin film.
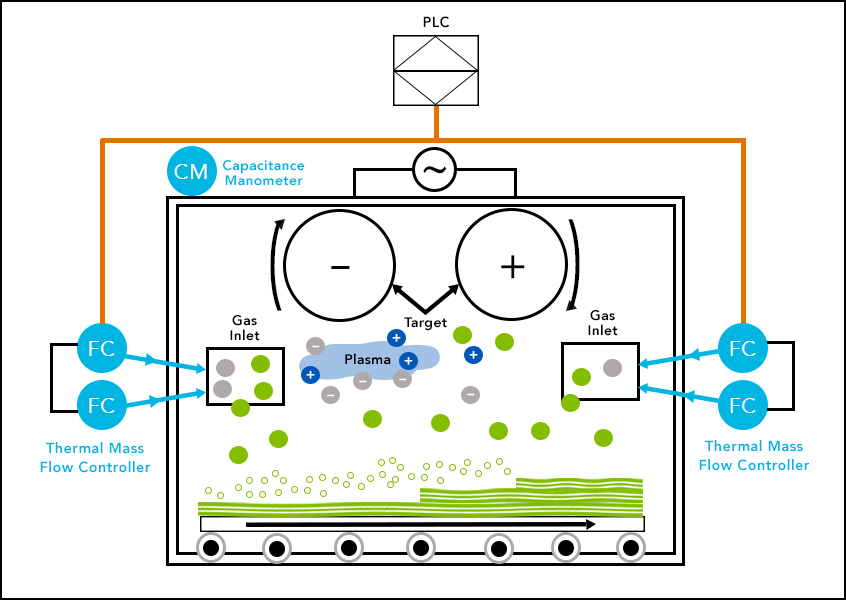
Gas flows must be sufficient for generating plasma and allowing the reactive sputtering process to maintain critical process parameters. Given the delicate balance of low-pressure control alongside adequate gas flows, highly precise and gas-independent vacuum capacitance manometers, like the Brooks Instrument XacTorr® Series, are used to control the base pressure.
As mentioned earlier, modern glass coating lines can be highly automated. The automation process monitors and controls key operational parameters such as gas flow, magnetic fields, and power supply. The system continuously collects performance and diagnostic data from various components and will correct any issues by compensating accordingly if any parameter is out of range. Communication protocols such as EtherNET/IP and PROFINET, available on Brooks Instrument SLA Series mass flow controllers, enables this automation by communicating data real-time between the mass flow controllers and PLC.
In Summary
By coupling highly automated control processes with stable, reliable flow and vacuum process control solutions, glass coating manufacturers are able to increase their productivity, reduce waste and operational costs, and deliver products with exceptional quality, reliability and uniformity.