When there is higher demand, water is released back into the lower reservoir through a turbine. Pumped-storage schemes currently provide the most commercially important means of large-scale grid energy storage. Such systems greatly improve the daily capacity factor of power generating systems though out the world.
Situation
A large hydro-electric power plant in Germany serves over 125,000 households and companies. The pump reservoir power station provides electricity according to demand with the help of water which is pumped up from a storage lake to the water reservoir. The upper reservoir is located at an elevation of 1289 feet and holds almost 2 million cubic yards of water. The lower reservoir and turbines are located at an elevation of about 305 feet, resulting in a drop of 984 feet.
There are two pipes (¾ miles long, 11.3 feet in diameter, with a wall thickness of ½ inch) used to pump the water from the upper reservoir to the 4 turbines near the lower reservoir, and then back to the upper reservoir again. Each pipe serves two pumps/ turbines with a maximum flow rate of approximately 65 cubic yards per second.
The turbines produce a total of 220MW. The total amount of energy that can be stored is 940MWh. At night, the water is pumped back to the upper reservoir. Although more energy is needed to pump the water back up, it is still an economical electricity source because it occurs during low electrical power demand periods. Other types of power plants can be more expensive to run, especially at peak demand times.
Challenge
A few years ago, the plant experienced an accident when a pipe broke after it was sand dusted during maintenance. The pump location, including the turbines and control room, was completely flooded. As a consequence, the customer was looking for a cost-effective flow measurement solution to drive a safety (emergency) shut-down valve in case the pipe should break again, or in case the flow rate should exceed a certain value. The required system would need to measure bi-directional flow and also provide an indication in the case of an unexpected flow variance. In addition, the flow meter would monitor the pump output and compare the function of the 4 pumps. Deposits (e.g. mussel deposits) on the inside of the pipe were an additional measurement challenge.
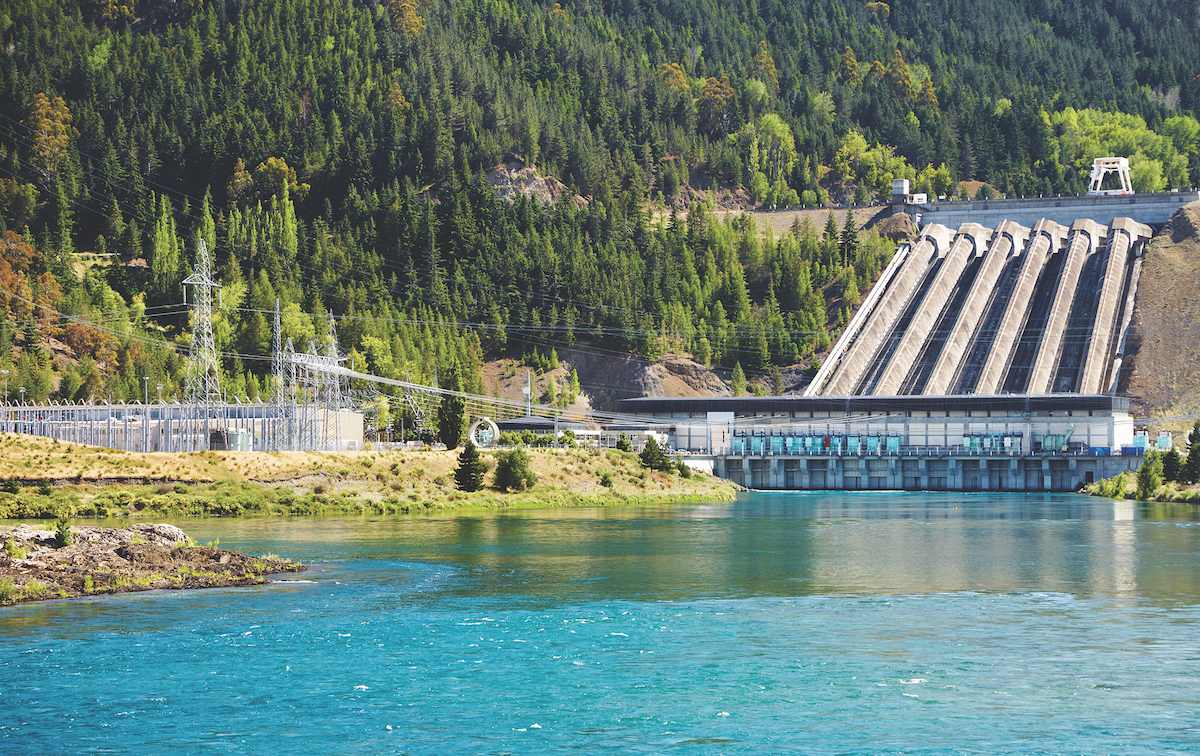
Solution
After consulting with a Siemens representative, the customer determined that the optimal solution for this difficult measurement was the Siemens clamp-on ultrasonic flow meter. With the ultrasonic clamp-on technology, there is no cutting into the pipe or interference with the actual flow. During the trial and simulation phase, with the SITRANS FS230 system was interfaced with the customers systems and was used for diagnoses. This modem allowed the user to record data or to make adjustments via a computer.
Two SITRANS FS230 flow meters with dual path measuring and high precision sensors were installed, one on each pipe. After several years, the customer is still very satisfied with the performance of the flow systems. Because of the safety benefits provided by the Siemens flow system, the customer is confident that, in case of an accident like the previous one, the cost savings would far outweigh the investment in flow meters by a thousand times or more.
Advantages
- Non-intrusive measurement – ideal and less expensive for larger and some smaller pipe sizes
- Little to no maintenance – no moving parts to break or wear out
- Maintains reliable performance
- Commissioning, programming, and adjusting can be done remotely via system interface
- Data logging
- Enhanced security – previous accident with the broken pipe resulted in a huge cost because the main hall with the turbines and control room was flooded
- Support – timely response time, good customer/vendor relationship, excellent service the world over
About the SITRANS FS230 flow meter
The SITRANS FS230 clamp-on ultrasonic flow meter has WideBeam® transit-time sensor technology to improve signal detection. It increases measurement accuracy by using the resonant frequency of the pipe to transmit ultrasonic waves through the flowing liquid, with the pipe wall acting as a waveguide. This makes it suitable for virtually any liquid. It offers numerous advantages that cannot be matched by any other single flow measurement technology, including zero pressure drop, insensitivity to outside noise and a high turndown ratio.
The SITRANS FS230 flow meter is available in single and dual path configurations. As with any clamp-on ultrasonic flow meter from Siemens, the sensors are installed on the outside of the pipe, making them the perfect choice for retrofit applications and applications where corrosive, toxic or high-pressure liquids and gases rule out the option of cutting the pipe. The non-intrusive sensors also minimize maintenance expenses and prevent deposits from forming.