Emerson would like to share how the Roxar 2600 Multiphase Flow Meter offers increased sustainability over traditional separator solutions. The solution from Emerson supports oil and gas operators around the world reduce environmental impact, optimize production, save on energy costs and reduce waste.
Sustainable Design Built to Endure
The Roxar 2600 Multiphase Flow Meter is engineered to stand the test of time, with a lifespan of twenty-five years. This longevity significantly lowers waste in the form of meter replacements across the field. The modular design with an interchangeable venturi sleave, increases turndown ratios and enables adaptability for different flow rates as the production profile changes over time.
Consider for a moment a separator system – multiple instruments from multiple suppliers, all the moving parts, all the consumables. Then consider the Roxar 2600 Multiphase Flow Meter – one integrated solution, no moving parts, no direct consumables, no routine replacements and few spare parts needed throughout the lifetime of the instrument. Added services like Performance Monitoring, a remote service available, enable operators to perform more tasks without visiting the site and ensures data-driven actions over routine service work. Fewer trips into the field result in reduction of CO2 emissions from vehicles as well.
Using only 22 Watts, the meter itself also requires less power consumption, even compared to other multiphase meters available. The power can be suppled by renewable energy resources like solar panels, should this be appropriate for the installation location. This is particularly useful in remote and offshore locations where it is difficult to run power.
For applications where a radioactive source is recommended, our source has a half-life of 30.1 years – the best on the market today. From a sustainability perspective, this means you don’t have to worry about disposal or replacement for a much longer timespan. In addition, maximum 5mCi source strength is used, which is very low, limiting any safety concerns considerably.
Being built to endure, our meters are simply less wasteful than other flow metering solutions.
Reduced Environmental Impact
Consider again a separator system and its size and footprint, then consider a small, compact, inline Roxar 2600 Multiphase Flow Meter. This significant size and footprint difference reduces environmental impact in a few keyways. Establishing the well pad results in less ground disturbance. An operator typically needs to lay a pipeline to the central production facility for each separator system. Operators recognize that multiphase flow meters enable comingling of the flow after it has been measured. This results in only one pipeline being needed between the well pad area and the central production facility, cutting down on pipeline needs considerably. In addition to the immediate effect of less ground disturbance, the reduced need for steel piping and separator tanks, which requires a lot of energy to manufacture, greatly improves the CO2 footprint for the well pad development.
The compact mechanical design of the Roxar 2600 Multiphase Flow Meter means fewer potential leak points. Test separators have so much instrumentation – interface connections, gauges, valves, manifolds, etc. – resulting in many more potential leak points. Switching over from a separator system to a multiphase flow meter solution automatically reduces your chances of impacting the environment, and it makes monitoring your potential leak points much easier too.
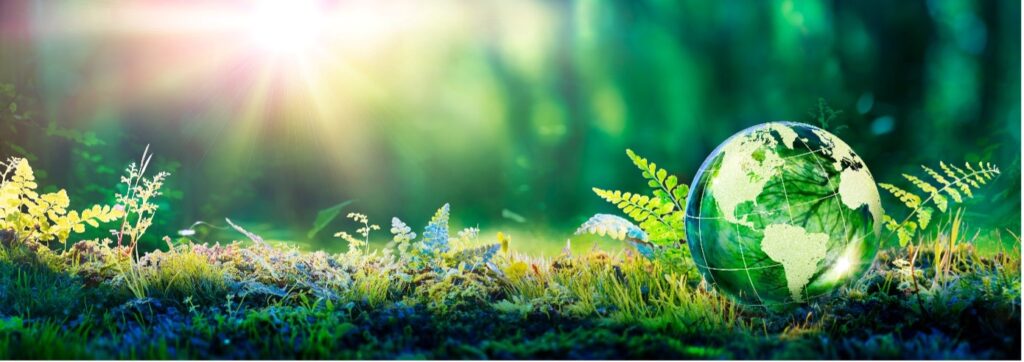
Optimizing Production to Improve Efficiency and Precision
High precision measurement performance capabilities like those in our embedded software, Roxar Rapid Adaptive Measurement, can not only be used to enhance oil recovery, reducing the need for additional drilling in the same reservoir, but also improve the sustainability of your operation. By utilizing 10 Hz data resolution, this valuable data helps users make adjustments to operations like gas lift injection rates so they can find optimum settings for producing the most amount of oil and least amount of water possible. Optimizing production results in less dirty water production and corresponding water cleaning plant needs, and it means less danger to the environment. It can also result in reduced gas production resulting in less gas flaring. The data can be used to optimize corrosion inhibitor injection, typically resulting in a reduction of chemical use. This enhanced insight empowers operators to be more efficient and less wasteful with resources overall.
Learn more about how we can provide you with the valuable data you need to support optimization of your oil & gas production, all while keeping your operations safe and sustainable. Visit the Multiphase section on Emerson.com for more information.